溶接における析出速度は、溶接プロセスの種類、装置設定、材料特性、および操作パラメーターなど、いくつかの要因に影響される。例えば、レーザークラッディングでは、溶着率はレーザーの出力、送り速度、トラバース速度に依存する。スパッタリングでは、ターゲット材料の特性、電流、ビーム・エネルギーなどの要素が役割を果たす。ワイヤー電極溶接の場合、ワイヤーサイズ、アンペア数、溶接位置などの変数が溶着率に大きく影響する。これらの要素を理解することで、効率と品質のために溶接工程を最適化することができます。
キーポイントの説明
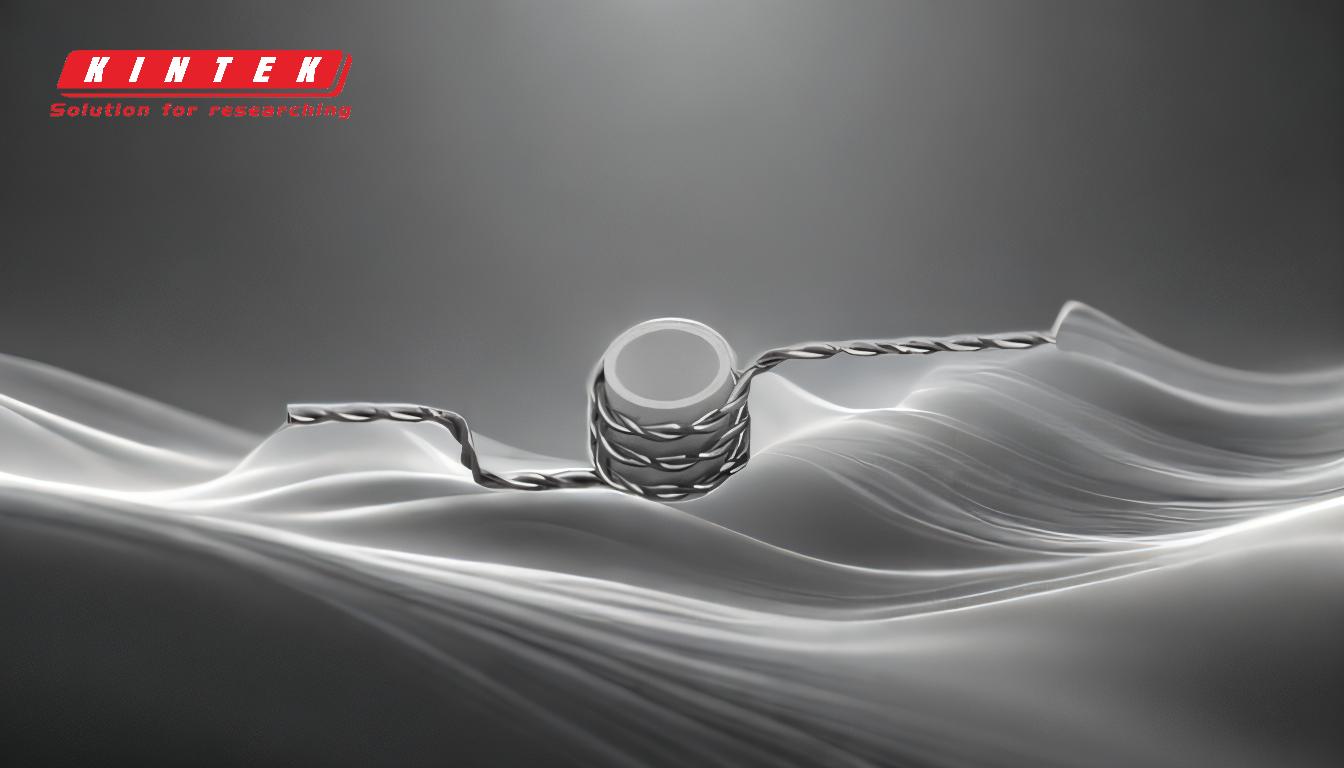
-
レーザクラッディングにおけるレーザ出力:
- レーザー出力は、材料へのエネルギー入力に直接影響し、溶融速度と蒸着効率に影響を与えます。
- レーザー出力が高いほど一般的に析出速度は向上しますが、過熱や反りなどの欠陥を避けるためにバランスをとる必要があります。
-
レーザークラッディングにおける送り速度:
- 材料(粉末またはワイヤーなど)を溶接ゾーンに供給する速度は、溶着率に影響する。
- 最適な供給速度は、欠陥の原因となる供給不足や供給過多を起こすことなく、一貫した材料添加を保証する。
-
レーザークラッディングにおけるトラバース速度:
- トラバース速度は、レーザーがワークピースを横切る速さを決定する。
- トラバース速度が速いと成膜速度は低下するが生産性は向上し、遅いと成膜速度は向上するが過度の熱入力につながる可能性がある。
-
プラズマ蒸着におけるプラズマ特性:
- プラズマの温度、組成、密度は成膜速度と品質に影響します。
- これらのパラメーターを監視することで、望ましい材料特性を確保し、汚染を最小限に抑えることができます。
-
スパッタリングにおけるターゲット材料特性:
- 密度や融点などのターゲット材料の物理的特性は、スパッタリングや成膜のしやすさに影響する。
- 融点が低く、スパッタリング収率が高い材料は、一般に成膜速度が速い。
-
スパッタリングにおける電流とビームエネルギー:
- 電流とビームエネルギーが高いほどスパッタリング速度が向上し、成膜速度の向上につながる。
- しかし、過剰なエネルギーはターゲットや基板を損傷させる可能性があるため、最適化が重要である。
-
溶接におけるワイヤ電極サイズ:
- より大きなワイヤー電極は、単位時間当たりにより多くの材料を析出させることができ、析出速度を増加させます。
- 例えば、250アンペアの1.4mmワイヤー電極は、平坦または水平位置で3.5kg/時間の析出速度を有する。
-
溶接におけるアンペア数:
- アンペア数が高いほど、入熱量と溶融速度が増加し、溶着率が高くなります。
- 適切なアンペア数を選択することで、溶接品質を損なうことなく、効率的な溶着を実現する。
-
溶接位置:
- 位置(平坦、水平、垂直、頭上など)は、溶融池に対する重力の影響に影響し、析出速度に影響を与える。
- フラットおよび水平位置は、通常、垂直または頭上位置と比較して、より高い析出速度を可能にする。
-
材料組成と汚染:
- 溶接工程における正しい元素組成の確保は、望 ましい材料特性を達成するために極めて重要であ る。
- 汚染は溶着率を低下させ、溶接の完全性を損な う可能性があるため、監視が不可欠である。
これらの要因を理解し、最適化することで、溶接工 やエンジニアは、溶接の品質と効率を維持しながら、 より高い溶着率を達成することができる。
要約表:
要因 | 蒸着速度への影響 |
---|---|
レーザーパワー(レーザークラッディング) | 出力が高いほど成膜速度は向上しますが、過熱や反りのリスクがあります。 |
送り速度(レーザークラッディング) | 最適な送り速度により、欠陥のない安定した材料添加を実現します。 |
トラバース速度(レーザークラッディング) | 速度を上げると成膜速度は低下するが、生産性は向上する。 |
プラズマ特性 | 温度、組成、密度は成膜品質に影響します。 |
ターゲット材料の特性 | 融点が低く、スパッタリング収率が高いため、成膜速度が向上します。 |
電流とビームエネルギー | エネルギーが高いほどスパッタリングレートは向上しますが、ダメージを避けるために最適化する必要があります。 |
ワイヤー電極サイズ | より大きなワイヤーは、単位時間当たりにより多くの材料を堆積させ、堆積速度を増加させる。 |
アンペア数 | アンペア数が高いほど、入熱量と溶融速度が増加し、析出速度が向上する。 |
溶接位置 | フラットおよび水平位置は、垂直またはオーバーヘッドよりも高い溶着率を可能にする。 |
材料組成 | 正しい組成は望ましい特性を保証し、汚染は成膜速度を低下させます。 |
溶接プロセスを最適化する準備はできていますか? 当社の専門家に今すぐご連絡ください オーダーメイドのソリューションを