物理蒸着 (PVD) プロセス、特に酸化インジウムスズ (ITO) は、基板上に薄く導電性の透明なコーティングを蒸着するために使用される高度な方法です。このプロセスは、タッチスクリーン、ソーラーパネル、フラットパネルディスプレイなどのアプリケーションで広く使用されています。 ITO PVD プロセスには、準備、蒸発、輸送、反応、堆積などのいくつかの重要なステップが含まれており、すべて高真空環境で実行されます。このプロセスは環境に優しく、優れた材料特性を提供し、特定の用途要件を満たすように調整できます。
重要なポイントの説明:
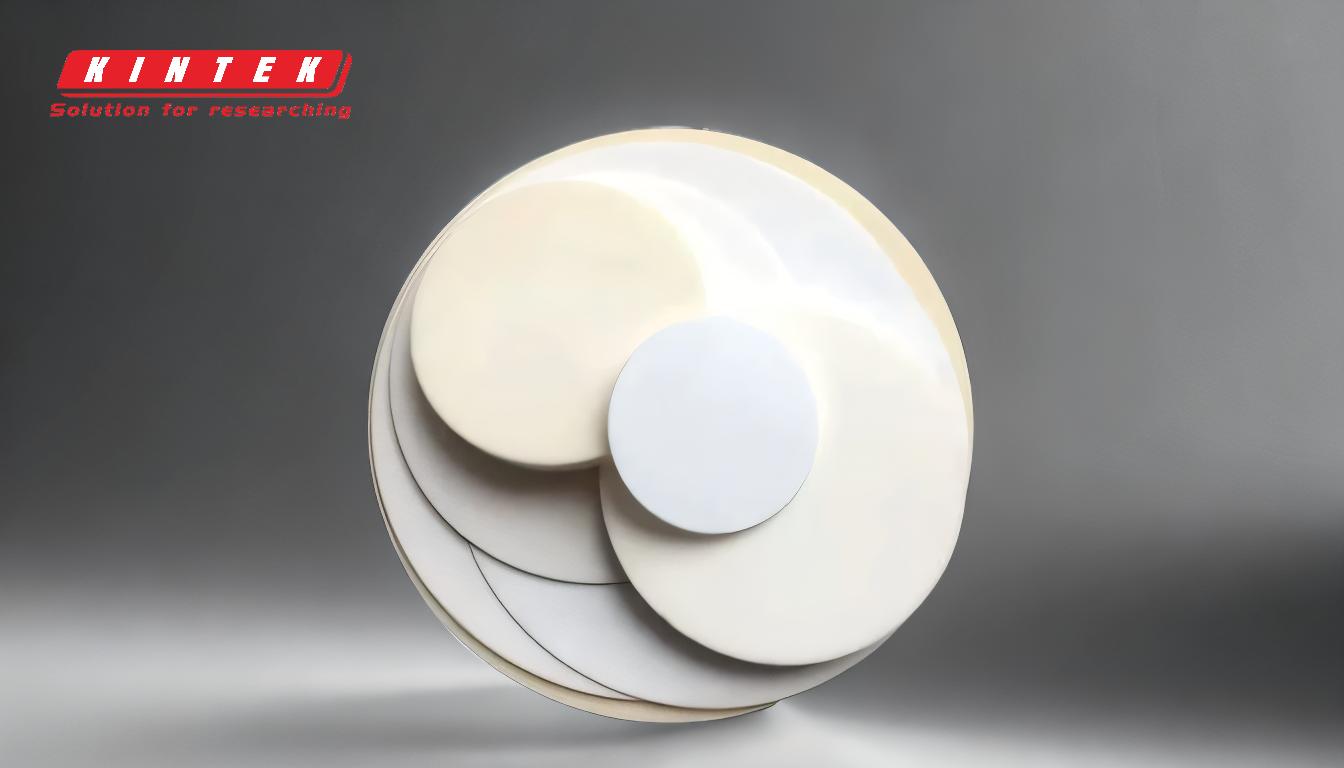
-
基板の準備:
- PVD プロセスを開始する前に、ITO コーティングの最適な密着性を確保するために基板を徹底的に洗浄および前処理する必要があります。これには、既存のコーティングを剥離し、基板を洗浄し、乾燥させることが含まれる場合があります。
- 真空チャンバーに入る前に基板が適切に位置合わせされ、欠陥がないことを確認するには、固定と目視検査も重要です。
-
ターゲット物質の蒸発:
- ITO ターゲット材料は通常、酸化インジウムと酸化スズの組み合わせであり、スパッタリングやアーク放電などの高エネルギー源を使用して蒸発させます。このプロセスでは、ターゲット材料から原子が除去され、蒸気が生成されます。
- 蒸発は高真空チャンバー内で行われ、汚染を防ぎ、クリーンな蒸着環境を確保します。
-
気化した原子の輸送:
- 気化した原子はターゲット材料から基板に輸送されます。このステップは、原子が均一に移動し、基板上に均一に堆積することを保証するため、重要です。
- 真空環境により輸送プロセスが促進され、他の粒子との衝突が最小限に抑えられ、基板への直接経路が確保されます。
-
反応性ガスとの反応:
- 輸送段階では、蒸発した原子が酸素や窒素などの反応性ガスと反応する可能性があります。この反応により蒸発した材料の組成が変化し、最終コーティングの特性が向上します。
- ITO コーティングの場合、酸素との反応は、望ましい導電性と透明性を実現するために特に重要です。
-
基板への蒸着:
- 最終ステップでは、蒸発した原子を基板上に凝縮させて、薄く均一な ITO 層を形成します。この層の厚さは通常、わずか数ナノメートルですが、優れた導電性と透明性を備えています。
- 堆積プロセスは、コーティングが特定の厚さと均一性の要件を確実に満たすように注意深く制御されます。
-
後処理と品質管理:
- 堆積後、コーティングされた基板は、コーティングの特性を改善するためにアニーリングなどの後処理プロセスを受ける場合があります。
- コーティングが希望の仕様を満たしていることを確認するために、厚さ測定や目視検査などの品質管理措置が実行されます。
-
ITO PVDの利点:
- ITO PVD プロセスには、基板と比較して特性が向上した材料を堆積できるなど、いくつかの利点があります。
- 有害な化学物質を含まず、大量の廃棄物も発生しないため、環境に優しいプロセスです。
- このプロセスは幅広い材料を堆積するように調整できるため、さまざまな用途に多用途に使用できます。
要約すると、ITO PVD プロセスは、基板上に薄く導電性の透明なコーティングを堆積するための、正確かつ制御された方法です。これには、基板の準備から後処理に至るまで、いくつかの重要なステップが含まれており、最適な結果を保証するためにすべて高真空環境で実行されます。このプロセスは環境に優しく、優れた材料特性を提供し、特定の用途のニーズに合わせてカスタマイズできます。
概要表:
ステップ | 説明 |
---|---|
1. 基板の準備 | 最適な接着力を得るために、基材を洗浄して前処理します。 |
2. 蒸発 | スパッタリングなどの高エネルギー源を使用して ITO ターゲット材料を蒸発させます。 |
3. 交通手段 | 高真空環境で蒸発した原子を基板に輸送します。 |
4. 反応 | 蒸発した原子を酸素などのガスと反応させてコーティングの特性を高めます。 |
5. 堆積 | 基板上に原子を凝縮させて、薄く均一な ITO 層を形成します。 |
6. 治療後 | 品質と性能を保証するために、コーティングを焼きなまして検査します。 |
7. 利点 | 環境に優しく、カスタマイズ可能で、材料特性を向上させます。 |
ITO PVD コーティングでアプリケーションを強化する準備はできていますか? 今すぐお問い合わせください もっと学ぶために!