レーザー焼結は積層造形(3Dプリンティング)技術の一種で、高出力レーザーを使用して粉末材料を固体構造に融合させる。航空宇宙、自動車、ヘルスケアなどの産業で、複雑で高精度の部品を作るために広く使用されている。このプロセスでは、粉末材料を積層し、レーザーで選択的に焼結することで、目的の物体を層ごとに作り上げる。この方法は、複雑な形状、高い強度、優れた表面仕上げを持つ部品の製造に特に有利である。また、材料の無駄を最小限に抑え、高融点材料を完全に溶かすことなく使用できるため、エネルギー効率とコスト効率にも優れている。
キーポイントの説明
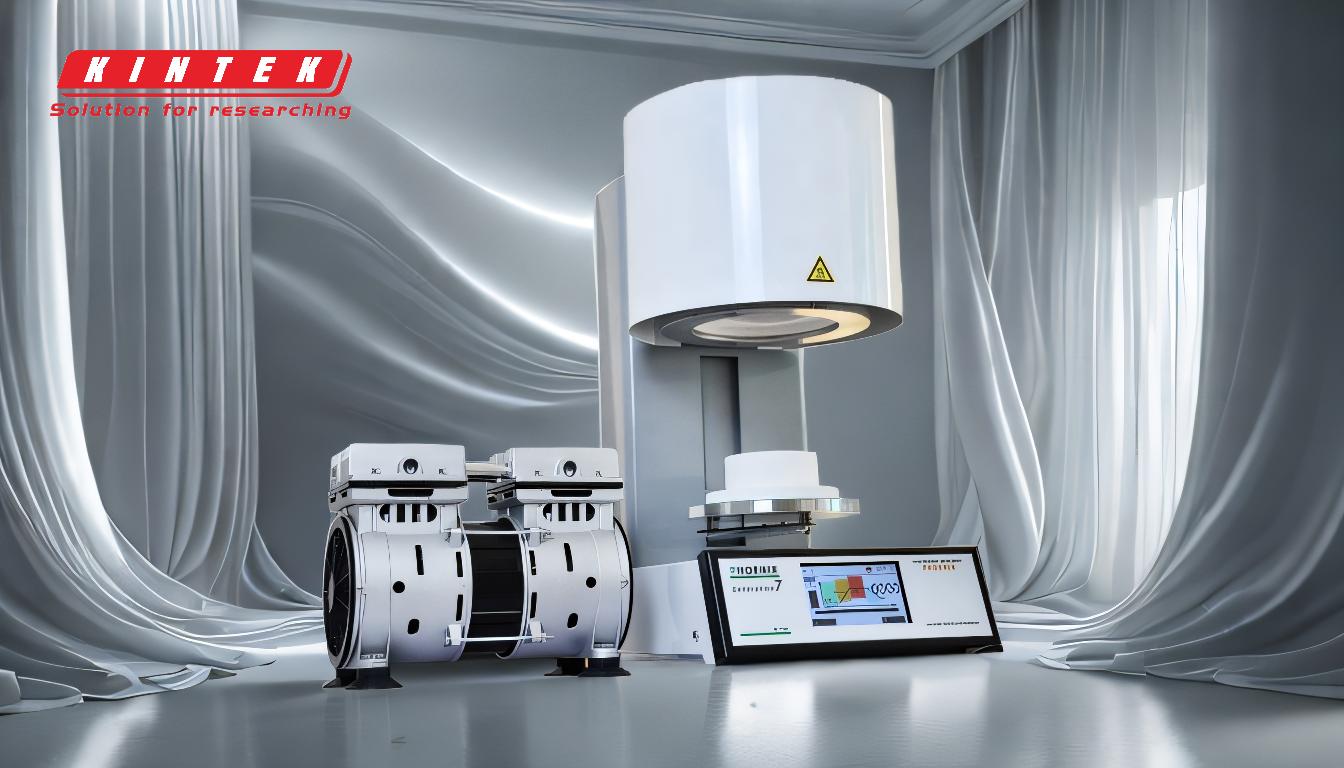
-
レーザー焼結の定義:
- レーザー焼結は、レーザーを使用して粉末材料を固体構造に融合させる積層造形プロセスである。
- 層ごとのプロセスで、粉末の各層が選択的に焼結され、最終的な3Dオブジェクトが作成されます。
-
レーザー焼結で使用される材料:
- 一般的な材料には、金属(チタン、アルミニウム、ステンレス鋼など)、ポリマー(ナイロン、ポリアミドなど)、セラミックなどがある。
- 材料の選択は、強度、耐久性、耐熱性など、最終部品の望ましい特性によって決まります。
-
プロセスの概要:
- ステップ1:準備:部品の3DモデルをCADソフトウェアで作成し、薄い層にスライスする。
- ステップ2:粉末析出:粉末材料の薄い層は、ビルドプラットフォーム上に均一に広げられます。
- ステップ3:レーザー焼結:高出力レーザーがパウダーベッドをスキャンし、3Dモデルのデザインに従ってパウダーを選択的に焼結します。
- ステップ4:レイヤーの追加:造形台が下がり、新しいパウダー層が前の層の上に広げられる。パーツが完成するまで、この工程を繰り返す。
- ステップ5:後処理:部品が製造された後、冷却、洗浄、表面仕上げなどの追加工程が行われます。
-
レーザー焼結の利点:
- 材料保全:レーザー焼結は、必要な粉末のみを焼結するため、材料の無駄を最小限に抑えます。
- エネルギー効率:材料全体を溶かす必要がないため、従来の製造方法と比べてエネルギーが少なくて済む。
- 費用対効果:材料廃棄とエネルギー消費の削減は、生産コストの削減につながります。
- 設計の柔軟性:レーザー焼結は、従来の方法では困難または不可能であった複雑な形状や複雑なデザインの作成を可能にします。
- 高精度と一貫性:このプロセスでは、焼結プロセスの優れた制御が可能であるため、高い寸法精度と一貫した品質を持つ部品が得られます。
- 強化された材料特性:焼結部品は、制御された焼結プロセスにより、強度や硬度などの機械的特性が向上することがよくあります。
-
レーザー焼結の用途:
- 航空宇宙:タービンブレードや構造部品など、軽量で強度の高い部品の製造に使用される。
- 自動車:カスタム部品、プロトタイプ、エンジン部品やブラケットなどの複雑な部品の製造に適用。
- ヘルスケア:患者固有のインプラント、補綴物、手術器具を高精度で製作するために使用される。
- 消費財:カスタム・ジュエリー、眼鏡、その他複雑なデザインの消費者向け製品の製造に使用される。
-
課題と考察:
- 材料の制限:すべての材料がレーザー焼結に適しているわけではなく、特殊な粉末や後処理が必要な場合もあります。
- 表面仕上げ:レーザー焼結では良好な表面仕上げの部品が得られるが、超平滑な表面を必要とする用途では追加の後処理が必要となる場合がある。
- 設備コスト:レーザー焼結装置の初期投資は高額になる可能性があり、小規模メーカーにとっては障壁となる。
- プロセス制御:一貫した結果を得るには、レーザー出力、スキャン速度、粉末層の厚さなどのパラメーターを正確に制御する必要がある。
要約すると、レーザー焼結は、材料の節約、エネルギー効率、複雑で高精度の部品を製造する能力など、多くの利点を提供する汎用的で効率的な付加製造方法である。いくつかの課題はあるものの、廃棄物を最小限に抑えながら耐久性のある高品質の部品を製造できることから、さまざまな産業で広く利用されている。
総括表
アスペクト | 詳細 |
---|---|
定義 | レーザーを使用して粉末材料を層ごとに融合させる積層造形。 |
材料 | 金属(チタン、アルミニウム)、ポリマー(ナイロン)、セラミック |
工程 | 準備、粉末堆積、レーザー焼結、層追加、後処理。 |
利点 | 省資源、エネルギー効率、費用対効果、設計の柔軟性、高精度 |
用途 | 航空宇宙、自動車、ヘルスケア、消費財 |
課題 | 材料の制限、表面仕上げ、設備コスト、工程管理。 |
レーザー焼結がお客様の生産工程をどのように強化できるか、検討する準備はできていますか? 今すぐご連絡ください までご連絡ください!