熱蒸着は、基板上に薄膜を形成するために広く使われている物理蒸着(PVD)技術である。高真空チャンバー内で固体材料を蒸発するまで加熱し、真空を通過して基板上に堆積する蒸気流を形成して薄膜を形成する。この方法は、融点が比較的低い材料に特に有効で、OLEDや薄膜トランジスタなどの用途によく用いられる。このプロセスは、抵抗加熱または電子ビーム加熱に依存してターゲット材料を蒸発させ、高純度の成膜を保証する。以下では、熱蒸発の主要な側面について詳しく説明する。
キーポイントの説明
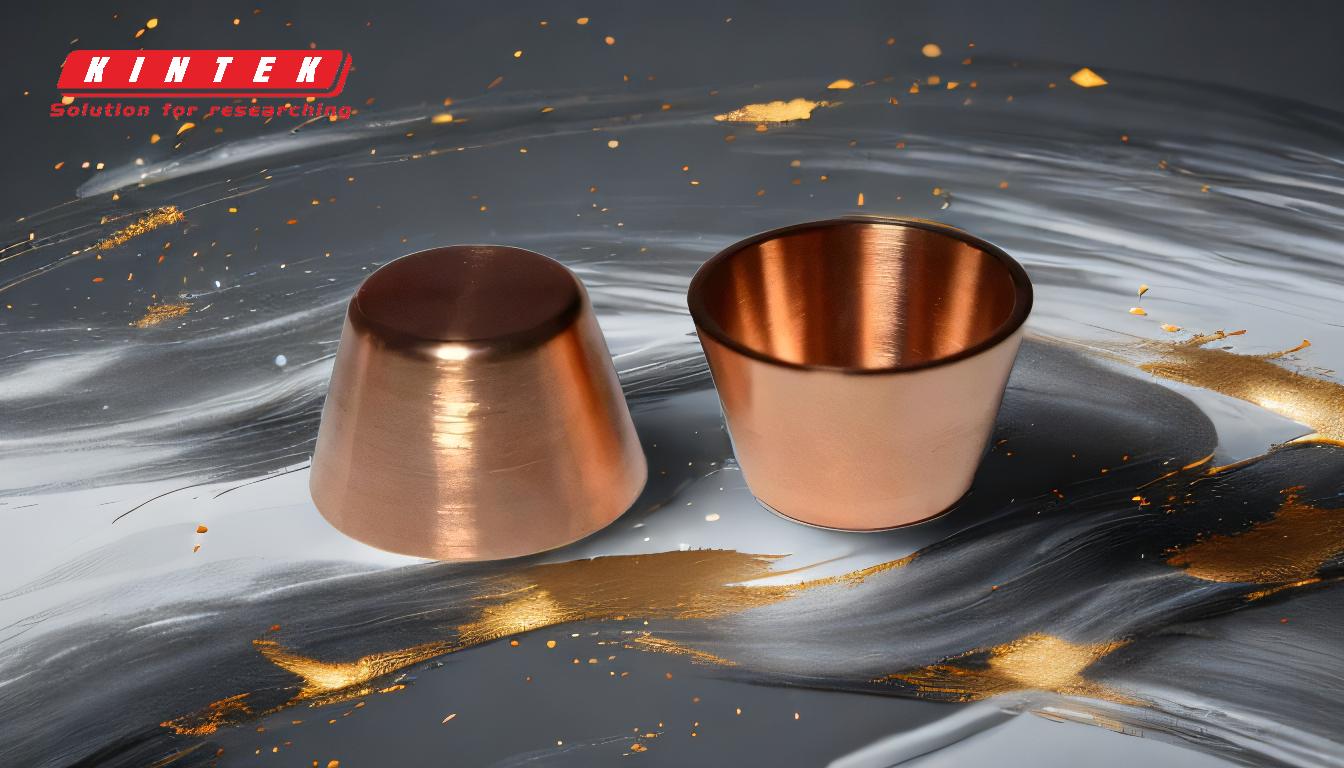
-
熱蒸発の基本原理:
- 熱蒸発は、高真空環境下で固体材料が気化するまで加熱する原理で行われる。気化した材料は雲を形成し、真空チャンバーを横切って基板上に堆積し、薄膜を形成する。
- 真空環境は、気化した材料が他の原子と反応したり散乱したりするのを防ぎ、クリーンで均一な成膜を保証するため、非常に重要である。
-
加熱メカニズム:
- 抵抗加熱:タングステンフィラメントまたはボートを使用して対象材料を加熱する一般的な方法。材料は発熱体の中または近くに置かれ、発熱体が抵抗加熱されて高温になり、材料が蒸発する。
- 電子ビーム加熱:電子ビームをターゲット材料に集束させ、局所的に加熱する方法。融点の高い材料や抵抗発熱体と反応する可能性のある材料に特に有効。
-
真空環境:
- このプロセスは、通常10^-5~10^-7Torrの高真空チャンバー内で行われる。この低圧環境はコンタミネーションを最小限に抑え、気化した材料が干渉を受けずに直接基板に移動することを保証する。
- 真空はまた、酸化やその他の化学反応のリスクを低減し、蒸着膜の純度を維持するために重要です。
-
材料に関する考察:
- 熱蒸発法は、金属(アルミニウム、金、銀など)や一部の有機化合物など、比較的低温で気化する材料に適している。
- 融点の高い材料や高温で分解する材料は、電子ビーム蒸着やスパッタリングなどの別の蒸着法が必要になる場合があります。
-
熱蒸発の応用:
- OLED(有機発光ダイオード):熱蒸着は、均一で純度の高い膜を作ることができるため、OLEDディスプレイの有機層の蒸着に広く使用されている。
- 薄膜トランジスタ:この方法は、膜厚と均一性の精密な制御が不可欠な薄膜トランジスタの製造にも採用されている。
- 光学コーティング:熱蒸着は、反射防止コーティング、ミラー、その他の光学部品の製造に使用されます。
-
熱蒸発の利点:
- シンプルさ:プロセスは単純で、他のPVD技術に比べて複雑な装置を必要としない。
- 高純度:真空環境と直接加熱機構により、コンタミネーションを最小限に抑えます。
- 均一な蒸着:膜厚と均一性を精密にコントロールできるため、高品質なコーティングを必要とする用途に最適。
-
熱蒸発法の限界:
- 資料制限:すべての材料が熱蒸着に適しているわけではなく、特に融点が高い材料や熱安定性の低い材料が適している。
- 視線蒸着:このプロセスはライン・オブ・サイトであるため、蒸気の流れに直接さらされる表面のみがコーティングされる。このため、複雑な形状や陰になる部分への使用が制限されることがある。
- スケーラビリティ:小規模な用途には効果的だが、大面積コーティングのための熱蒸発のスケールアップは困難である。
-
他の蒸着法との比較:
- スパッタリング:熱蒸着とは異なり、スパッタリングは高エネルギーのイオンを使ってターゲット材料から原子を引き離すため、高融点を含む幅広い材料に適している。
- 化学気相成長法(CVD):CVDは化学反応を利用して薄膜を成膜するため、ステップカバレッジと均一性に優れるが、高温と複雑な装置を必要とすることが多い。
まとめると、熱蒸発法は、特に融点の低い材料や、高い純度と均一性が要求される用途において、薄膜を成膜するための多用途で効果的な方法である。いくつかの制限はあるものの、その簡便さと信頼性から、エレクトロニクスから光学まで幅広い産業でよく使われる方法である。
総括表:
アスペクト | 詳細 |
---|---|
原理 | 真空中で固体材料を加熱して気化させ、基板上に堆積させる。 |
加熱メカニズム | 抵抗加熱(タングステンフィラメント/ボート)または電子ビーム加熱。 |
真空環境 | コンタミネーションと酸化を最小限に抑えるため、10^-5~10^-7 Torrで動作。 |
適した材料 | 金属(アルミニウム、金など)、低融点有機化合物 |
用途 | OLED、薄膜トランジスタ、光学コーティング(ミラー、反射防止)。 |
利点 | シンプル、高純度、均一な蒸着 |
制限事項 | 材料の制限、視線方向の蒸着、スケーラビリティの課題。 |
比較 | スパッタリング:材料範囲が広い;CVD:適合性は良いが複雑。 |
サーマルエバポレーションがどのように薄膜アプリケーションを強化できるかをご覧ください。 今すぐ専門家にお問い合わせください !