熱蒸着、特に熱蒸着は、薄膜コーティングプロセスで広く使われている技術である。高真空環境で固体材料を気化するまで加熱し、蒸気流を発生させて薄膜として基板上に堆積させる。この方法は、単原子層から厚膜まで、精密で均一なコーティングを作るのに非常に効果的である。このプロセスは、気化した材料が基板まで妨げられることなく移動し、そこで凝縮して固体膜を形成するように、高真空を維持することに依存している。熱蒸着は汎用性が高く、自立した構造や複雑な多層設計を可能にするため、エレクトロニクス、光学、材料科学などの産業で不可欠な技術となっている。
キーポイントの説明
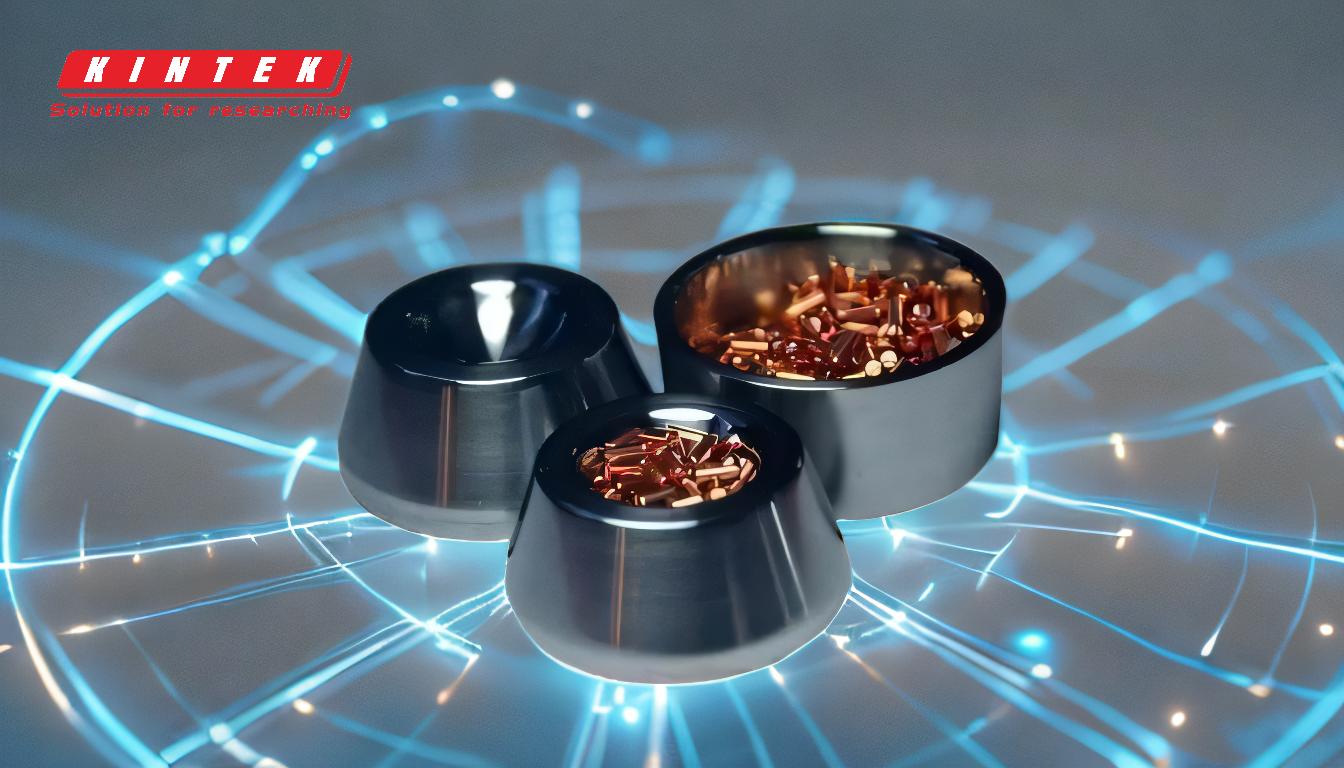
-
プロセス概要:
- 熱蒸着は真空を利用したコーティング技術で、固体材料を蒸発点まで加熱し、蒸気の流れを発生させる。
- 気化した材料は真空チャンバー内を移動し、基板上に堆積して薄膜を形成する。
-
加熱メカニズム:
- タングステンフィラメント、ボート、バスケット、または電子ビームを使用してターゲット材料を加熱する。
- 加熱プロセスにより、材料は融点または沸点まで上昇し、蒸発に十分な蒸気圧が発生する。
-
真空環境:
- このプロセスは、通常真空ポンプによって維持される高真空チャンバー内で行われる。
- 真空により、他のガスからの干渉が最小限に抑えられ、蒸気の流れが自由に移動し、基板上に均一に蒸着することができる。
-
気化と蒸着:
- 材料は熱エネルギーによって固体から蒸気の状態へと変化する。
- 蒸気の流れは基板上で凝縮し、正確な厚みと均一性を持つ固体膜を形成します。
-
応用例:
- エレクトロニクス(例:半導体、太陽電池)、光学(例:反射防止コーティング)、材料科学(例:自立構造)の薄膜作成に使用。
- 多層で複雑なデザインの成膜が可能。
-
利点:
- 高精度で膜厚制御が可能。
- 金属、合金、一部の有機化合物など、幅広い材料に対応。
- 高真空環境のため、コンタミネーションが少ない。
-
制限事項:
- 蒸発温度が比較的低い材料に限定される。
- 高融点材料には追加技術(電子ビーム蒸着など)が必要な場合がある。
- 複雑な基板や非平面基板上で均一なコーティングを実現する上での課題。
-
キーコンポーネント:
- 真空チャンバー:プロセスに制御された環境を提供する。
- 加熱源:蒸発に必要な熱エネルギーを発生させる。
- 基板ホルダー:均一な成膜のために基板を位置決めする。
- 真空ポンプ:プロセスに必要な高真空条件を維持します。
-
材料への配慮:
- ターゲット材料は、達成可能な温度での蒸発に適した蒸気圧を持っていなければならない。
- 蒸着を成功させるには、加熱源と基板との適合性が重要である。
-
今後の展開:
- 加熱源と真空技術の進歩により、成膜速度と材料適合性が向上している。
- 他の蒸着技術(例えばスパッタリング)との統合により、応用範囲が拡大している。
熱蒸着法は薄膜製造の基礎となる技術であり、精度、汎用性、拡張性を備えている。高品質のコーティングを作り出すその能力は、現代の製造と研究に不可欠なものとなっている。
総括表
アスペクト | 詳細 |
---|---|
プロセスの概要 | 真空中で固体材料を加熱し、蒸着用の蒸気流を作る。 |
加熱メカニズム | タングステンフィラメント、ボート、バスケット、電子ビーム |
真空環境 | 高真空チャンバーにより、ガス干渉を最小限に抑えます。 |
用途 | エレクトロニクス、光学、材料科学(太陽電池、コーティングなど)。 |
利点 | 高精度、最小限のコンタミネーション、多様な材料適合性。 |
制限事項 | 蒸発温度の低い材料に限定。 |
主要コンポーネント | 真空チャンバー、加熱源、基板ホルダー、真空ポンプ |
将来の開発 | 改良された加熱源、真空技術、他の方法との統合。 |
熱蒸着がお客様のプロジェクトをどのように強化できるかをご覧ください。 今すぐご連絡ください までご連絡ください!