セラミック材料の焼結は、粉末セラミックを融点以下の熱処理によって緻密な固体構造に変える重要なプロセスです。このプロセスには、粉末成形体の準備、結合剤を除去するための加熱、粒子を融合させるための高温焼結など、いくつかの段階が含まれます。焼結に影響する主な変数には、温度、雰囲気、圧力、粒子径があり、これらは総体として強度、気孔率、密度などの最終的な材料特性を決定する。焼結プロセスは、これらのパラメータを制御することで最適化され、最終的なセラミック製品に望ましい特性を持たせることができます。
要点の説明
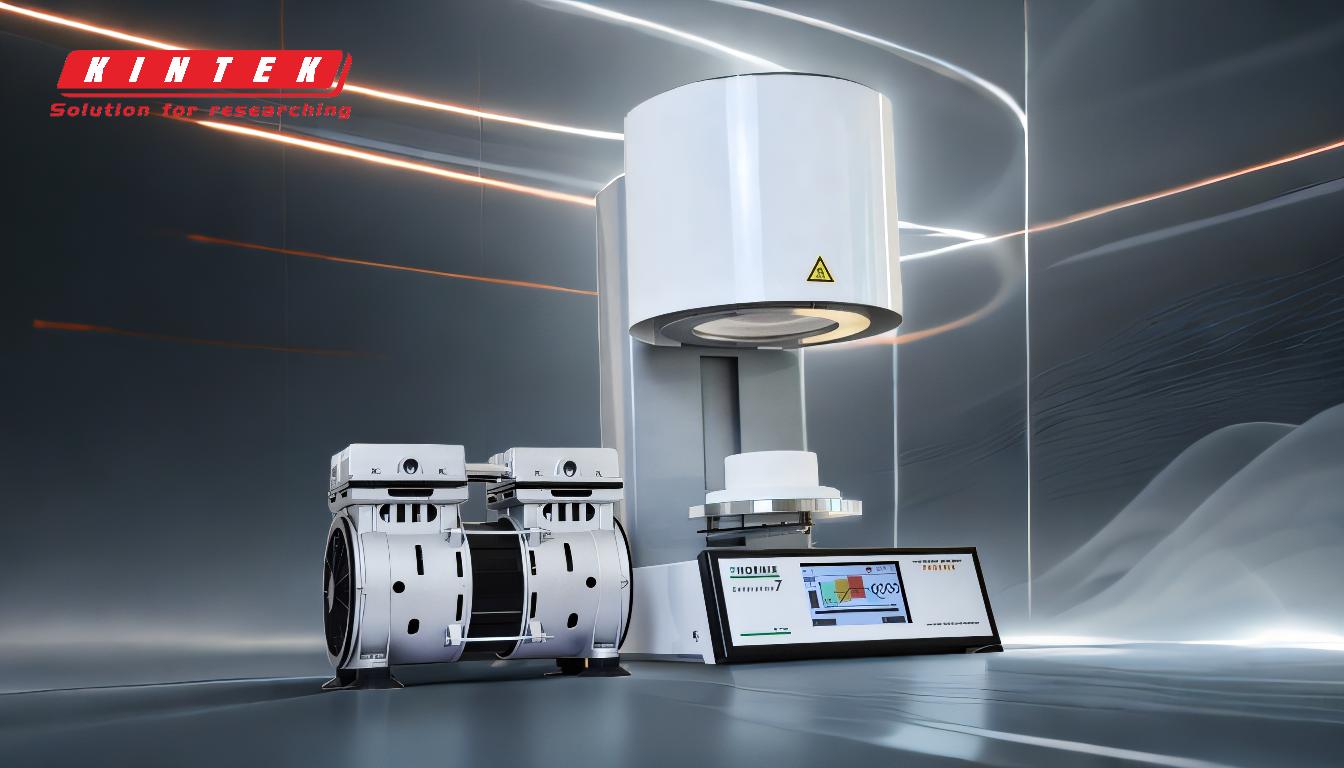
-
パウダーコンパクトの準備:
- 混合とスラリー形成: プロセスは、未焼成のセラミック粉末を水、結合剤、凝集除去剤と混合してスラリーを形成することから始まる。このスラリーを噴霧乾燥し、流動性のある粉末にします。
- グリーンボディにプレスする: 噴霧乾燥された粉末を型に押し込んで、成形された未焼成のセラミック部品である「グリーン体」を形成します。この工程は、所望の形状と初期密度を達成するために非常に重要です。
-
バインダー除去:
- 低温加熱: グリーンボディを低温で加熱し、バインダーを燃焼させる。残留バインダーは高温焼結中に気孔やクラックの原因となるため、この工程は最終製品の欠陥を防ぐために不可欠である。
-
高温焼結:
- 融点直下まで加熱: 次に、グリーン体をセラミック材料の融点ぎりぎりの高温まで加熱します。このステップにより、粒子が拡散して結合し、気孔率が減少して密度が高まります。
- 粒子の結合と高密度化: 焼結中、粒子は緻密化し合体するが、これは液相焼結(LPS)のような技術を使って加速することができる。このプロセスは、粒子表面から粒子間の接触点への材料の拡散を伴い、ネック形成と最終的な融合をもたらす。
-
冷却と凝固:
- 制御された冷却: 焼結後、材料は制御された方法で冷却され、一体化した塊に固化します。冷却速度は、セラミックの最終的な微細構造や特性に影響を与える。
-
焼結に影響を与える要因:
- 温度: 一般に温度が高いほど焼結速度が増し、引張強さや衝撃エネルギーなどの材料特性が向上する。しかし、過度の温度は望ましくない結晶粒の成長につながる。
- 雰囲気: 焼結雰囲気(空気、真空、アルゴンや窒素のような不活性ガスなど)は、セラミックの酸化状態や粒子の拡散速度に影響を与える可能性があります。
- 圧力: 焼結中に圧力を加えることで、粒子の再配列が促進され、気孔率が減少し、最終製品の密度が高くなります。
- 粒子サイズと組成: 粒子が小さく、組成が均一であれば、緻密化が促進され、焼結がより均一になる。焼結プロセスとパラメータの選択は、最終的なセラミック製品の望ましい特性によって決まります。
-
焼結プロセスの最適化
- パラメータの制御: 焼結温度、印加圧力、ガス雰囲気などのパラメーターを注意深く制御することで、焼結プロセスを最適化することができる。より微細な粉末とより高い温度は、成形性を高めることができるが、欠陥を避けるために液相の量を注意深く管理する必要がある。
- 最終気孔率: 焼結セラミックの最終的な気孔率は、グリーン成形体の初期気孔率、および焼結プロセスの温度と時間に依存します。例えば、純酸化物セラミックは、固体拡散のため、より長い焼結時間と高温を必要とします。
これらの重要な側面を理解し制御することで、メーカーは様々な用途に合わせた特性を持つ高品質のセラミック材料を製造することができます。
総括表
ステージ | 主なプロセス | 目的 |
---|---|---|
粉末の調製 | セラミック粉末をバインダー、水、凝集除去剤と混合し、スラリーを形成する。 | シェイピング用の流動性のあるパウダーを作る。 |
グリーンボディの形成 | 粉末を型に押し込み、未焼成のセラミック部品を形成する。 | 所望の形状と初期密度を得る。 |
バインダー除去 | 低温加熱でバインダーを燃焼除去。 | 焼結時のポロシティやクラックなどの欠陥を防ぐ。 |
高温焼結 | 融点直下で加熱して粒子を融合させる。 | 粒子の拡散により気孔率を下げ、密度を高める。 |
冷却 | 材料を凝固させるための制御された冷却。 | 最終的な微細構造と特性に影響を与える。 |
主な変数 | 温度、雰囲気、圧力、粒子径。 | 強度や気孔率などの最終的な材料特性を決定します。 |
セラミック焼結プロセスを最適化することで、優れた結果が得られます。 今すぐ専門家にご相談ください !