粉末焼結プロセスは、材料の融点に達することなく熱と圧力を加えることで、粉末状の材料を緻密な固形体に変化させる製造技術である。このプロセスは、粉末冶金、セラミック、プラスチックなどの産業で広く使用され、強度、耐久性、複雑な形状の部品を製造します。このプロセスには通常、粉末の準備、混合、成形、焼結、後処理など、いくつかの重要な工程が含まれる。焼結は、粒子境界を横切る原子の拡散を利用し、粒子を融合させて凝集塊にする。この方法は、タングステンやモリブデンなどの金属、セラミックやポリマーなど、融点の高い材料に特に有効です。
キーポイントの説明
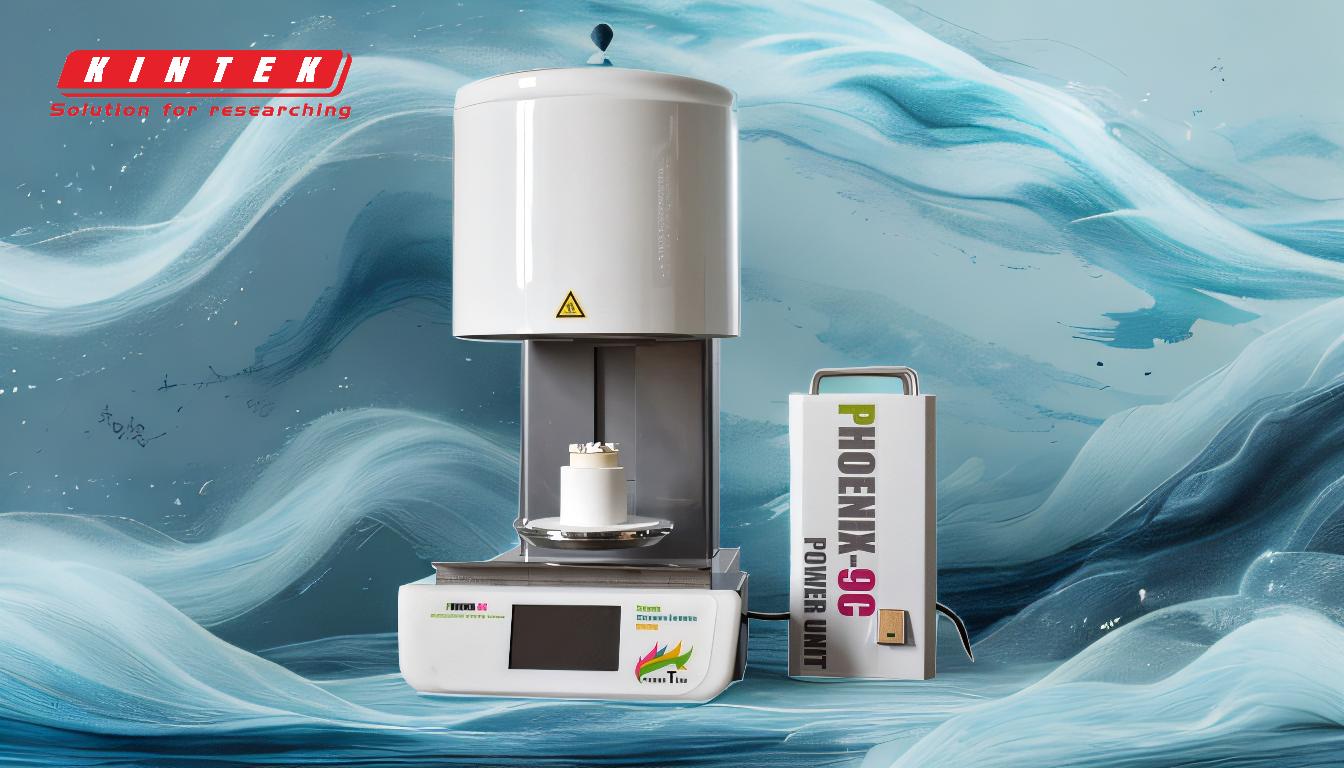
-
焼結の定義:
- 焼結とは、粉末状の材料に融点以下の熱と圧力を加えることで、緻密な固形体に変化させるプロセスである。
- 粉末冶金、セラミックス、プラスチックなど様々な産業で、耐久性のある複雑な形状の部品を作るために使用される。
-
焼結プロセスの主なステップ:
- 粉体製造:このプロセスは、金属、セラミック、プラスチックの微粉末の製造から始まる。これらの粉末は、霧化、化学的還元、機械的粉砕などの方法で製造されることが多い。
- 混合:パウダーは次に、流動性を改善し、粒子の均一な分布を確保するために、バインダーやその他の添加剤と混合される。
- 成形:混合された粉末は、型押し、静水圧プレス、射出成形などの技法を用いて所望の形状に成形される。この工程により、壊れやすい焼結前の形状である「圧粉体」ができあがります。
- 焼結:グリーンコンパクトは、制御された環境(炉など)の中で、材料の融点以下の温度で加熱される。この段階で原子の拡散が起こり、粒子が結合して固体の塊に緻密化する。
- 後処理:焼結後、機械加工、熱処理、表面仕上げなどの追加工程を経て、最終製品の所望の特性や寸法に仕上げることができる。
-
焼結のメカニズム:
- 焼結は、隣接する粒子の境界を横切る原子の拡散に依存している。温度が上昇すると、原子はエネルギーの高い領域から低い領域へと移動し、粒子同士が融合する。
- この原子の拡散により空隙が減少し、材料の密度が高まるため、最終製品はより強く耐久性のあるものになる。
-
焼結の応用:
- 粉末冶金:焼結は、ギア、ベアリング、フィルターなどの金属部品の製造に広く使用されています。高精度で無駄の少ない複雑な形状を作ることができる。
- セラミックス:焼結は、タイル、絶縁体、電子機器や航空宇宙分野で使用されるアドバンストセラミックスなどのセラミック材料の製造に不可欠である。
- プラスチック:焼結は、複雑な形状を持つプラスチック部品を作成するために付加製造(例えば、選択的レーザー焼結)で使用されます。
-
焼結の利点:
- 材料効率:焼結は、正確に成形・圧縮できる粉末を使用するため、材料の無駄を最小限に抑えます。
- 複雑な形状:従来の機械加工では困難または不可能な、複雑で入り組んだ形状の製造を可能にします。
- 高い強度と耐久性:焼結プロセスにより、高密度、高強度、耐摩耗性の材料が得られる。
-
課題と考察:
- 温度制御:反りや不完全焼結などの欠陥を避けるためには、温度と加熱速度を正確に制御することが重要です。
- 材料の選択:高温で酸化したり劣化するものもあるため、すべての材料が焼結に適しているわけではありません。
- 後処理:機械加工やコーティングなどの追加工程は、所望の表面仕上げや寸法精度を達成するために必要となる場合があります。
-
焼結材料の例:
- 金属:タングステン、モリブデン、鉄、ステンレス鋼は、高性能部品を製造するために一般的に焼結される。
- セラミックス:アルミナ、ジルコニア、炭化ケイ素は、高温および耐摩耗用途に使用するために焼結される。
- プラスチック:ポリアミド(ナイロン)をはじめとするポリマーは、積層造形プロセスで焼結され、軽量で耐久性のある部品を作ります。
粉末焼結プロセスを理解することで、メーカーはその利点を活用し、幅広い用途向けに特性を調整した高品質の部品を製造することができます。
要約表
主な側面 | 詳細 |
---|---|
定義 | 融点以下の熱と圧力を使って、粉体を緻密な固体に変える。 |
主な工程 | 粉末製造、混合、成形、焼結、後処理。 |
メカニズム | 原子拡散により粒子が融合し、空隙率が減少し、密度が増加する。 |
用途 | 粉末冶金、セラミック、プラスチック |
利点 | 材料効率、複雑な形状、高い強度と耐久性。 |
課題 | 温度管理、材料の選択、後処理。 |
加工例 | 金属(タングステン、モリブデン)、セラミック(アルミナ)、プラスチック(ナイロン)。 |
粉末焼結プロセスがお客様の製造能力をどのように向上させるかをご覧ください。 今すぐご連絡を !