粉末冶金(PM)は、鋳造、鍛造、機械加工といった従来の金属加工法とは一線を画す独自の製造プロセスです。これらのプロセスとは異なり、粉末冶金は金属粉末を所望の形状に圧縮し、高温で焼結して固体で高密度の部品を作ります。この方法は、部品間の均一性、材料の柔軟性、コスト効率など、比類のない利点を提供する。特に、材料の無駄を最小限に抑えながら、複雑で高精度な部品を製造するのに適しています。以下では、他の製造プロセスと比較した粉末冶金の主な違いと利点を探ります。
キーポイントの説明
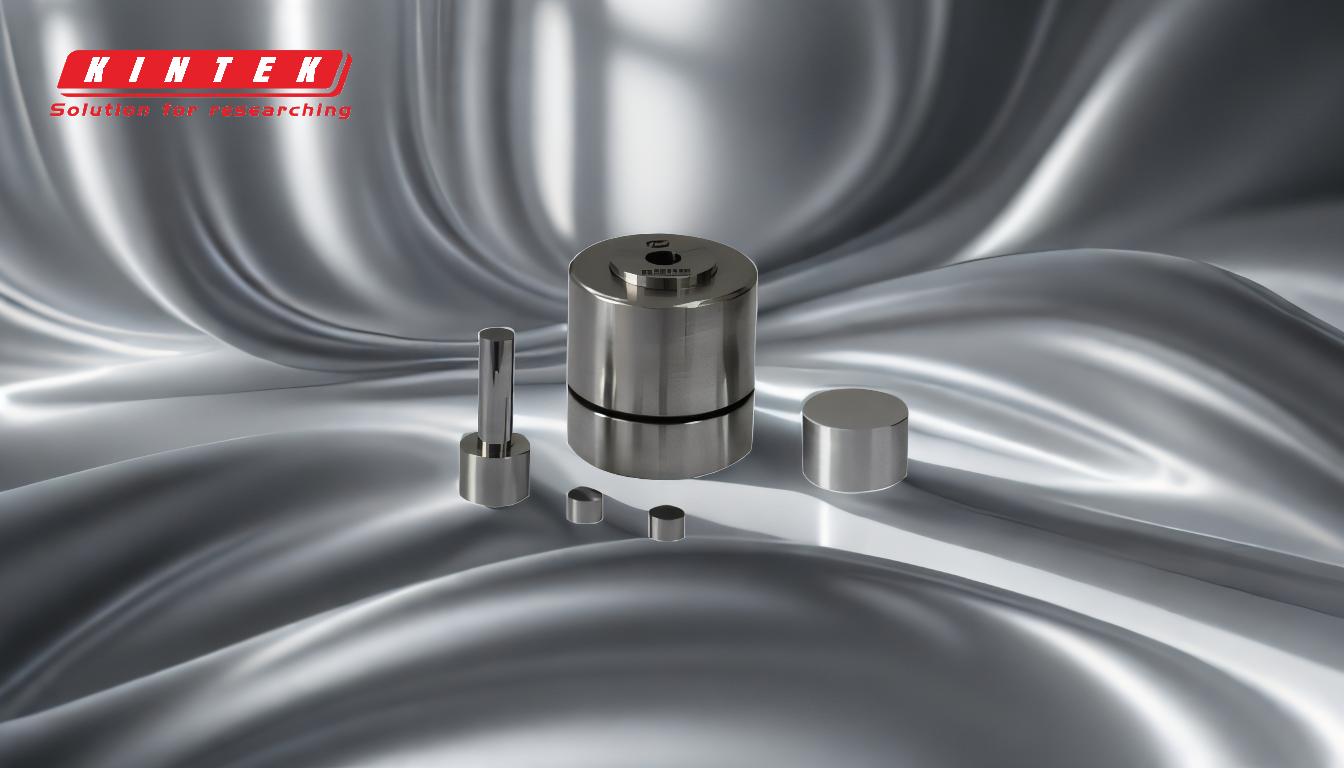
-
部品間の均一性と精度
- 粉末冶金では、粉末の圧縮と焼結プロセスが制御されているため、部品の寸法と特性が一定に保たれます。
- 鋳造や鍛造では、冷却速度や材料の流れに起因するばらつきに悩まされることがありますが、粉末冶金では、公差が厳しくばらつきの少ない部品を製造することができます。
- この均一性は、自動車や航空宇宙産業など、精度と信頼性が最も重要な産業にとって非常に重要です。
-
材料の柔軟性
- PMでは、金属、合金、複合材料を含む幅広い材料を使用することができ、特定の用途に合わせて調整することができます。
- 特定の合金や組み合わせを苦手とする従来のプロセスとは異なり、PMではタングステン、チタン、あるいはセラミックと金属の複合材料などの材料を組み込むことができる。
- この柔軟性により、高強度、耐摩耗性、熱伝導性などのユニークな特性を持つ部品の製造が可能になります。
-
複雑な形状と設計の自由度
- 粉末冶金は、機械加工、鋳造、鍛造では困難または不可能な複雑形状の製造に優れています。
- このプロセスでは、アンダーカット、薄肉、内部溝などの複雑な形状を、二次加工なしで作り出すことができます。
- この設計の自由度により、組み立ての必要性が減り、製造工程が簡素化されます。
-
材料の無駄を最小限に
- PMはニアネットシェイププロセスであり、最終的な部品は希望寸法に非常に近く、追加の機械加工はほとんど必要ありません。
- 機械加工のような伝統的な工程では、スクラップが大量に発生することが多いが、PMではほぼすべての原材料を使用するため、持続可能でコスト効率に優れている。
- この効率性は、高価な素材や希少な素材を扱う場合に特に有益です。
-
費用対効果
- 複雑な部品を単一工程で製造できるため、機械加工や鍛造のような多工程に比べ、人件費や金型費が削減されます。
- 焼結は通常、鋳造で金属を溶かすよりも低い温度を必要とするため、PMはエネルギー消費も最小限に抑えます。
- 大量生産の場合、PMはその拡張性と効率性により、大幅なコスト削減を実現します。
-
用途の多様性
- 粉末冶金は、自動車(ギア、ベアリングなど)から医療(インプラントなど)、エレクトロニクス(ヒートシンクなど)まで、幅広い産業で使用されています。
- このプロセスは、自己潤滑性ベアリング用の気孔率や構造部品用の高密度など、特定の特性を持つ部品を製造することができる。
- この多用途性により、PMはカスタマイズされた材料性能を必要とする用途に適した選択肢となっています。
-
環境面での利点
- PMの材料廃棄量とエネルギー消費量の削減は、従来の製造方法と比較して環境フットプリントの低減に貢献する。
- 金属粉末をリサイクルできることは、プロセスの持続可能性をさらに高める。
- これらの利点は、環境に優しい製造ソリューションに対する需要の高まりと一致している。
要約すると、粉末冶金は非常に効率的で汎用性が高く、精密な製造プロセスとして際立っている。複雑で高品質な部品を最小限の無駄とコストで製造できることから、多くの用途で優れた選択肢となっています。鋳造や機械加工のような伝統的な方法にもそれなりの場所はあるが、PMは現代の製造業でますます評価されている独自の利点を提供する。
総括表
側面 | 粉末冶金(PM) | 従来の方法(鋳造、鍛造、機械加工) |
---|---|---|
部品の均一性 | 高精度、一貫した寸法、最小限のばらつき。 | 冷却速度や材料の流れによってばらつきが生じやすい。 |
材料の柔軟性 | 金属、合金、複合材料を含む幅広い材料。 | 材料適合性と加工上の課題による制限。 |
複雑な形状 | 最小限の二次加工で複雑な形状を加工。 | 工具の制約と加工の複雑さによって制限される。 |
材料の無駄 | ニアネットシェイプ・プロセス、廃棄物を最小限に抑え、持続可能。 | スクラップが多い。 |
コスト効率 | 人件費、金型費、エネルギーコストを削減。 | 多段階プロセスやエネルギー集約的なオペレーションにより、コストが高くなる。 |
用途 | 産業(自動車、医療、エレクトロニクス)を問わず、カスタマイズされた特性で多用途。 | 材料と設計の制約による制限。 |
環境への影響 | 廃棄物の削減、エネルギー効率、リサイクル可能性。 | 廃棄物とエネルギー消費による環境フットプリントの増加。 |
次のプロジェクトで粉末冶金の利点を活用する準備はできていますか? 今すぐご連絡ください までご連絡ください!