スパークプラズマ焼結(SPS)は、電流と急速な加熱速度を利用して高密度の材料圧密を実現する高度な焼結技術である。この方法は、セラミック、金属、複合材料を含む幅広い材料を、従来の焼結法に比べて低温・短時間で焼結するのに特に効果的である。このプロセスでは、材料とダイを通過するパルス直流電流を印加することで、内部加熱と外部加熱の両方を可能にする。この結果、表面酸化物の除去、エレクトロマイグレーション、電気塑性などの高密度化メカニズムが強化される。SPSはまた、優れた機械的および光学的特性を持つ材料を製造することが可能であり、先端材料製造のための貴重な技術となっている。
ポイントを解説
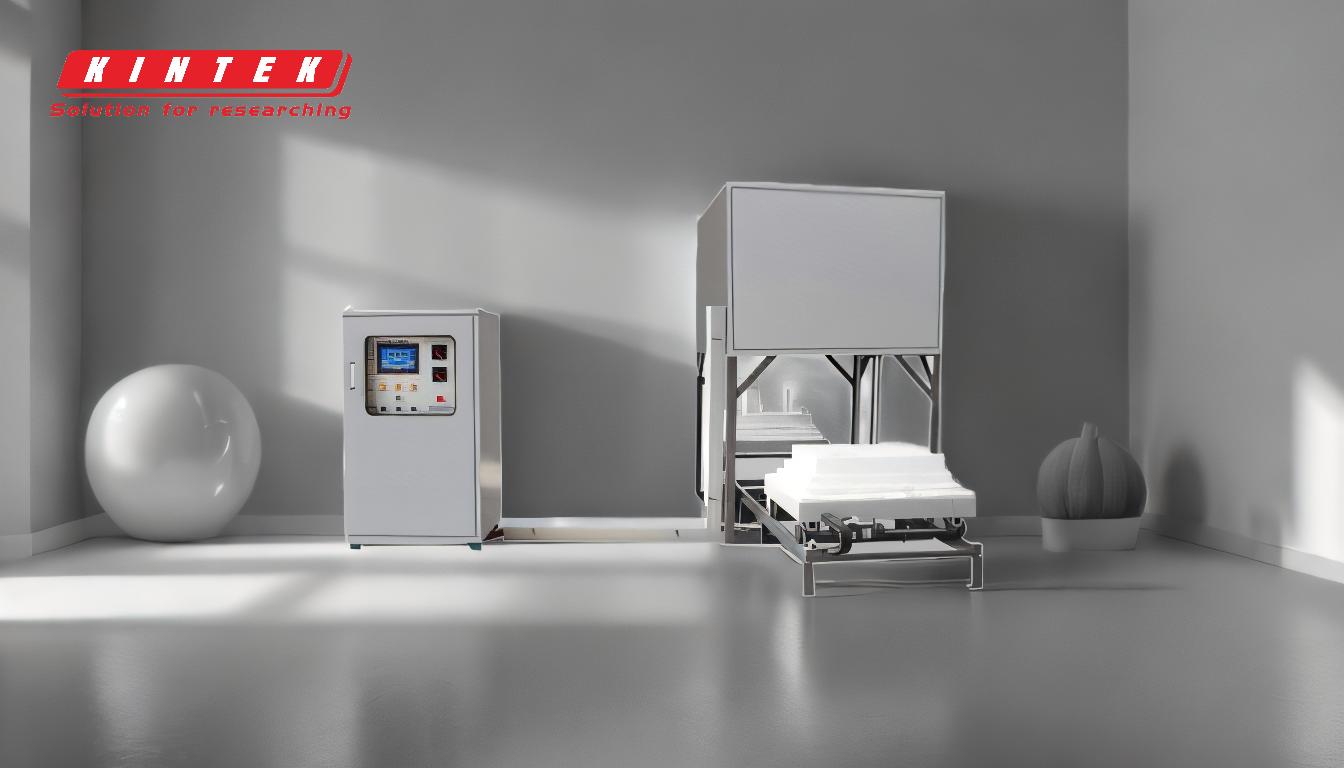
-
電流の応用:
- SPSでは、パルス状の直流電流が印加され、この電流は導電性の加圧ダイ(通常はグラファイト製)を通過し、材料が導電性であれば材料そのものを通過する。この二重の加熱メカニズム(内部および外部)は、表面酸化物の除去、エレクトロマイグレーション、電気塑性などの様々なメカニズムを活性化することにより、焼結プロセスを著しく向上させます。これらのメカニズムは、材料の急速な緻密化に寄与します。
-
高い加熱速度:
- SPSの際立った特徴のひとつは、最高1000℃/分という極めて高い加熱速度を達成できることである。この急速加熱により、従来の焼結法に比べて低温・短時間での材料の圧密化が可能になる。高い加熱速度は、特に極低温粉砕のような技術で加工された材料の微細構造を維持するのに有益である。
-
焼結プロセスのステップ:
- 構成:工程は、主原料とカップリング剤の添加と混合から始まる。この工程により、パウダーは後続の工程に向けて十分に準備される。
- 圧縮:混合された粉末は、金型を使って必要な形状にプレスされる。この工程は、所望の形状と材料の初期密度を達成するために非常に重要です。
- 熱:成形されたパウダーは高温にさらされ、カップリング剤が除去され、主原料が低孔率で融合される。SPSでは加熱速度が速いため、この工程が効率的に完了し、緻密でよく固まった材料が得られる。
-
熱源としての金型:
- SPSでは、金型は材料を成形するための型としてだけでなく、熱源としても機能する。電流はグラファイト・ダイを通過し、材料が導電性であれば材料自体も通過する。その結果、均一な加熱と迅速な焼結が実現し、これがSPS法の主な利点となる。
-
SPS法の利点:
- 簡単操作:SPSの操作は比較的簡単で、従来の焼結方法に比べて複雑な設備は必要ない。
- 低い技術要件:このプロセスは高度な専門技術を必要としないため、幅広い用途に利用できる。
- 高速焼結:急速な加熱と冷却速度により、焼結時間全体が大幅に短縮され、生産性と効率が向上します。
-
アモルファス材料の調製:
- SPSは、ガラスのような非晶質材料の作製に特に有効である。この技術は、ガラスの融点よりもはるかに低い温度で秩序-無秩序転移を達成し、従来の溶融-冷却プロセスで製造された材料よりも高い硬度、破壊靭性、優れた光学特性(近赤外および紫外線透過率)を持つ材料をもたらす。
-
均一加熱と高い焼結温度:
- SPS法は、材料全体の均一な加熱を保証し、安定した材料特性を達成するために極めて重要である。SPSの高い焼結温度能力は、高密度の焼結体の迅速な焼結を可能にし、幅広い先端材料用途に適しています。
要約すると、スパークプラズマ焼結は、電流と急速加熱を利用して高密度の材料圧密を達成する、多用途で効率的な技術である。低温・短時間での操業が可能で、優れた特性を持つ材料を製造できることから、先端材料製造の分野では貴重なツールとなっている。
総括表
主な側面 | 内容 |
---|---|
電流 | パルス状の直流電流が金型と材料を通過し、二重加熱を可能にします。 |
高い加熱速度 | 最高1000℃/分、より低い温度と短い焼結時間を可能にします。 |
焼結ステップ | 迅速な高密度化のための組成、圧縮、熱処理。 |
熱源としての金型 | 黒鉛ダイスは電流を通し、均一な加熱と迅速な焼結を保証します。 |
利点 | 操作が簡単、技術要件が低い、焼結速度が速い。 |
アモルファス材料 | 優れた硬度、靭性、光学特性を持つ材料を製造。 |
均一加熱 | 安定した材料特性と高い焼結温度を保証します。 |
スパークプラズマ焼結で先端材料の可能性を引き出します。 お問い合わせ までご連絡ください!