適切な脱炭酸温度を選択することは、望ましい材料特性と性能を確保するための重要なステップである。脱炭酸温度は、分解、相転移、結晶化など、材料の化学的・物理的変換に直接影響する。適切な脱炭酸温度を決定するには、材料の熱安定性、所望の相または構造、および装置の能力を考慮する必要があります。以下に、脱炭酸温度を選択する際に考慮すべき主な要因について詳しく説明する。
キーポイントの説明
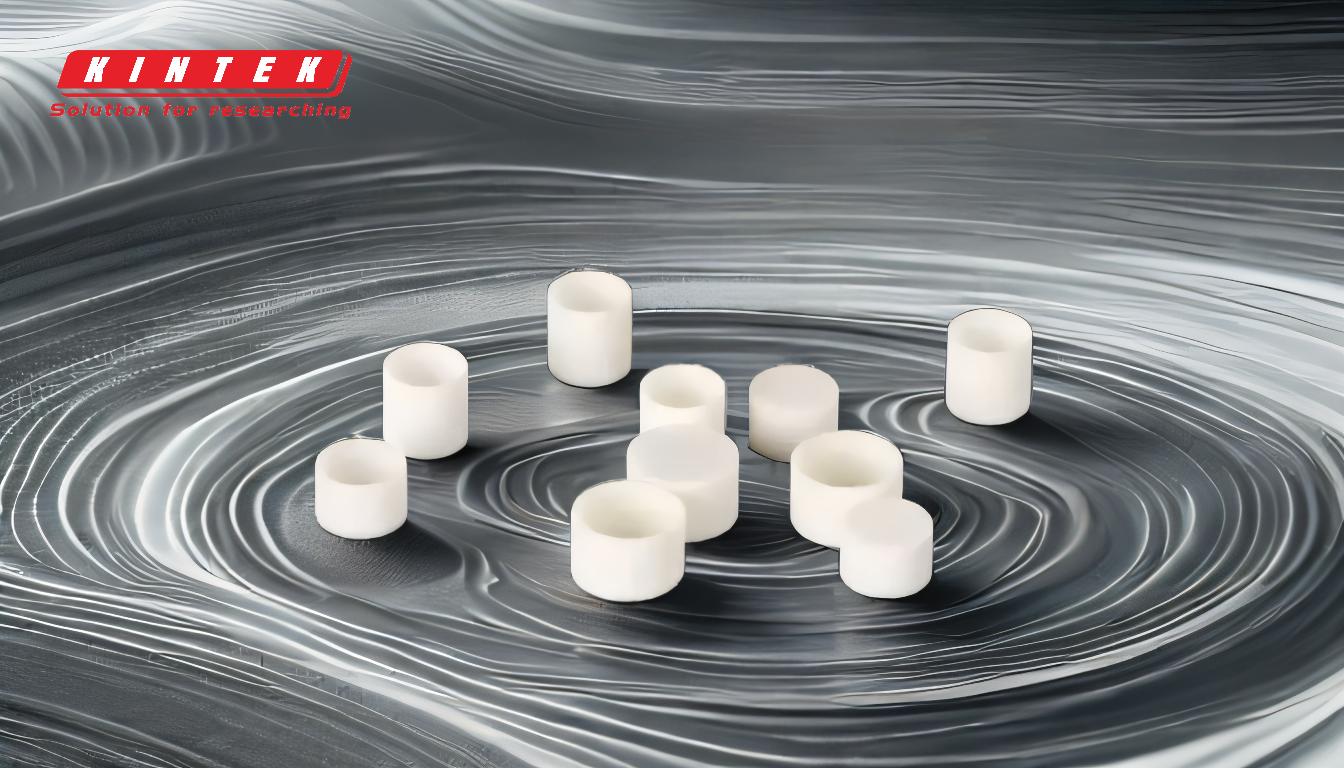
-
材料の熱挙動を理解する
- 熱分解温度:材料が分解や相変化を起こす温度を測定する。これは、熱重量分析(TGA)や示差走査熱量測定(DSC)などの技術によって特定できる。
- 相転移温度:材料が目的の結晶相または非晶質相に遷移する温度範囲を特定する。
- 熱安定性:選択した焼成温度で、材料が劣化したり、意図した特性を失ったりしないことを確認する。
-
望ましい結果を定義する
- 相純度:特定の結晶相を得ることを目的とする場合、焼成温度は相形成温度と一致させなければならない。
- 粒子径と形態:温度が高いと粒成長やシンタリングが起こる可能性があり、低いと反応が不完全になる可能性がある。
- 化学組成:焼成温度が、望ましくない反応や揮発性成分の損失を引き起こさないことを確認する。
-
機器の制限を考慮する
- 炉内温度範囲:炉の最高温度は、安定した性能を確保し、炉の上限温度での運転を避けるために、要求される脱炭酸温度を100~200℃上回る必要がある。
- 加熱速度と均一性:炉は、材料の特性に影響を及ぼす可能性のある熱勾配を避けるために、均一な加熱と精密な温度制御を提供する必要がある。
- 大気のコントロール:脱炭酸に特定の雰囲気(不活性、酸化性、還元性など)が必要な場合は、炉が要求される条件を維持できることを確認してください。
-
実験的トライアルによる最適化
- パイロット実験:小規模な実験を行い、さまざまな焼成温度と時間をテストする。得られた材料特性を分析し、最適な温度を特定する。
- 反復的改良:収率、相純度、粒子径などの要因を考慮し、実験結果に基づいて温度を調整する。
- 特性評価:X線回折(XRD)、走査型電子顕微鏡(SEM)、フーリエ変換赤外分光法(FTIR)などの技術を使用して、焼成後の材料を評価する。
-
現実的な制約を考慮する
- エネルギー効率:温度が高くなると、エネルギー消費と運転コストが増加する可能性がある。望ましい材料特性とエネルギー効率のバランスをとる。
- 安全への配慮:選択した温度が装置の安全な動作範囲内であり、過熱や材料の劣化などの危険性がないことを確認してください。
- スケーラビリティ:選択した温度が、大規模生産で一貫して達成できるかどうかを検討する。
-
参考業界標準と文献
- 研究発表:一般的に使用される焼成温度とその結果を特定するために、類似材料に関する研究をレビューする。
- メーカー推奨品:特定の材料に最適な使用温度については、装置メーカーにお問い合わせください。
- 過去のデータ:該当する場合は、過去の実験や生産から得たデータを用いて判断する。
これらの要因を注意深く考慮することで、効率的で安全な操業を確保しながら、望ましい材料特性を達成する脱炭酸温度を選択することができる。このプロセスには、脱炭酸条件を最適化するための理論的理解、実験的検証、および実際的考察の組み合わせが含まれる。
総括表:
キーファクター | 説明 |
---|---|
材料の熱挙動 | 分解温度、相転移温度、熱安定温度を特定する。 |
望ましい結果 | 相純度、粒子径、形態、化学組成の目標を定義する。 |
機器の制限 | 炉の温度範囲、加熱速度、均一性、雰囲気を考慮する。 |
実験的トライアル | パイロット実験を行い、温度を反復的に改良する。 |
現実的な制約 | エネルギー効率、安全性、拡張性のバランスをとる。 |
業界標準 | 参考調査、メーカーの推奨、過去のデータ。 |
最適な焼成温度の選択にお困りですか? 専門家にご相談ください オーダーメイドの指導のために!