真空蒸着は、制御された環境、通常は高真空条件下で、表面に材料の薄層を蒸着するために使用されるプロセスである。その原理は、原料の蒸発または昇華を中心に展開し、それが基板上に凝縮して薄膜を形成する。このプロセスにより、コンタミネーションを最小限に抑え、蒸着層の厚さと特性を正確に制御することができる。重要なステップには、不純物を除去するために真空を作り、蒸発を誘発するために原料を加熱し、気化した原料を基板上に凝縮させることが含まれる。物理的気相成長法(PVD)や化学的気相成長法(CVD)といった技術が一般的に使用されており、それぞれに特有の用途と利点がある。
キーポイントの説明
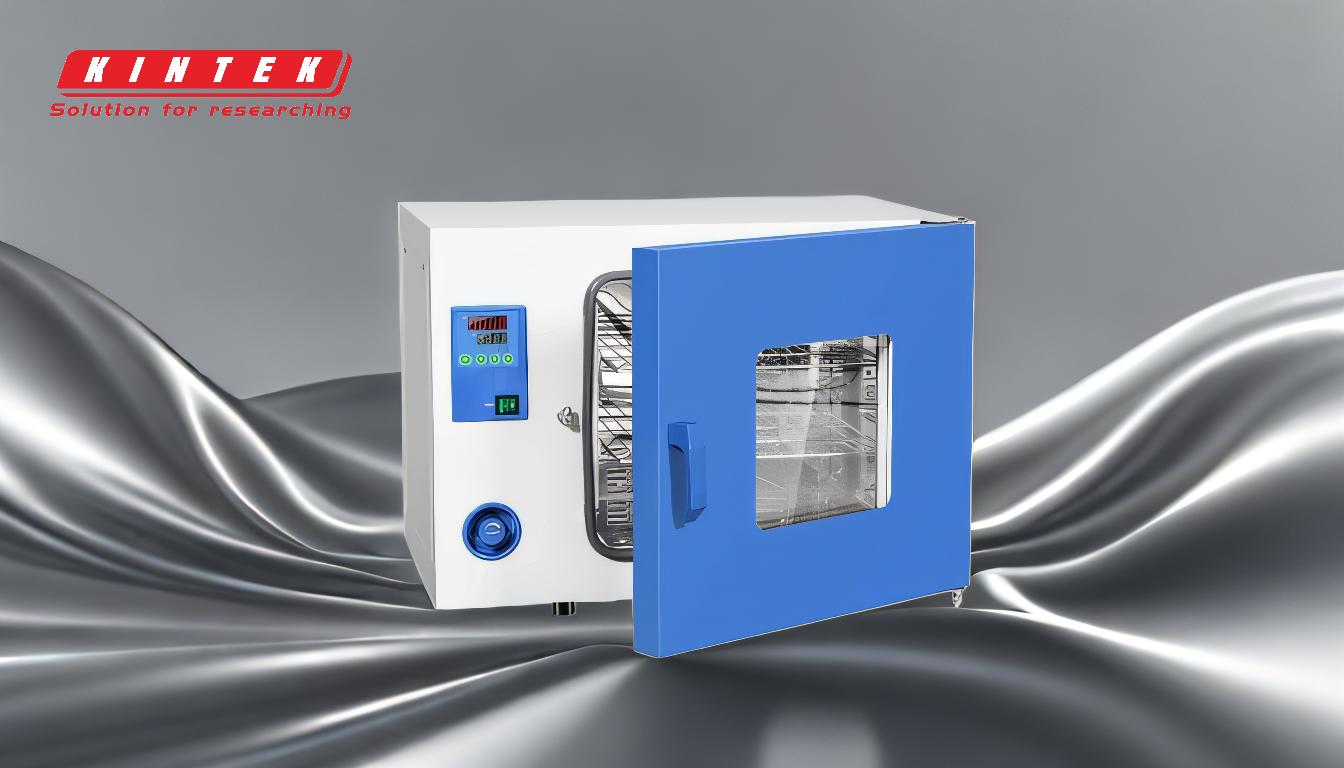
-
真空蒸着の定義と目的:
- 真空蒸着は、真空環境で基板上に材料の薄層を蒸着させるために使用される技術である。
- 主な目的は、金属などの表面に保護層や機能層を作り、その特性(耐食性、導電性、光学特性など)を向上させることである。
-
プロセスにおける真空の役割:
- 真空環境は、蒸着プロセスを汚染する可能性のある空気やその他のガスを排除するために不可欠である。
- 気体分子が存在しないため、蒸発した材料は基板まで妨げられることなく移動し、均一で高品質な膜が得られる。
-
蒸発と凝縮:
- 原料は、蒸発または昇華して蒸気になるところまで加熱される。
- この蒸気は真空を通り、冷却基板上に凝縮して薄膜を形成する。
- フィルムの厚さは、用途によって1原子層から数マイクロメートルに及ぶ。
-
熱源と蒸発:
- 電子ビームや抵抗加熱などの熱源は、原料が蒸発するのに必要なエネルギーを供給するために使用される。
- 熱源の選択は、成膜される材料と膜の望ましい特性によって決まる。
-
真空蒸着プロセスの種類:
- 物理的気相成長(PVD):ソースから基板への材料の物理的移動を伴う。一般的なPVD法には、スパッタリングや熱蒸着がある。
- 化学気相成長法(CVD):薄膜を成膜するための化学反応。このプロセスは通常低圧で行われ、反応性ガスを使用して基板上に目的の材料を形成することもある。
- 低圧プラズマ溶射(LPPS):真空条件下で行うプラズマ溶射のバリエーションで、酸化を最小限に抑えた高品質の皮膜を成膜できる。
-
真空蒸着の応用:
- 保護コーティング:金属部品の摩耗、腐食、酸化に対する耐久性と耐性を高めるために使用される。
- 光学コーティング:反射率や反射防止性を向上させるためにレンズやミラーに適用される。
- 半導体製造:集積回路やその他の電子部品の製造における薄膜の成膜に不可欠。
- 装飾用コーティング:金やクロムのような金属を薄く塗布し、美観を保つために使用される。
-
真空蒸着の利点:
- 高純度:真空環境のためコンタミネーションが少なく、高純度なフィルムが得られる。
- 精密制御:このプロセスでは、膜厚と組成を正確にコントロールできる。
- 汎用性:金属、セラミック、ポリマーなど、さまざまな材料の蒸着が可能。
-
課題と考察:
- 設備費:真空蒸着システムは、高真空チャンバーと特殊な加熱源が必要なため、高価になることがある。
- 複雑さ:このプロセスでは、所望の膜特性を得るために、温度、圧力、蒸着速度などのパラメーターを注意深く制御する必要がある。
- スケーラビリティ:小規模な用途には効果的だが、大規模生産のためにプロセスをスケールアップするのは難しい。
これらの重要なポイントを理解することで、真空蒸着が複雑でありながら非常に効果的であり、さまざまな産業における基盤技術となっていることが理解できるだろう。
総括表:
アスペクト | 詳細 |
---|---|
定義 | 真空下で基板上に薄い材料層を蒸着するプロセス。 |
目的 | 耐食性や導電性などの表面特性を向上させる。 |
主要テクニック | 物理的気相成長法(PVD)、化学的気相成長法(CVD)、LPPS。 |
アプリケーション | 保護膜、光学コーティング、半導体製造など |
メリット | 高純度、精密制御、材料蒸着における多用途性。 |
課題 | 高い設備コスト、プロセスの複雑さ、拡張性の問題。 |
真空蒸着がお客様のプロジェクトをどのように向上させるかをご覧ください。 エキスパートへのお問い合わせ !