スパークプラズマ焼結(SPS)は、パルス直流電流と一軸加圧を組み合わせた高度な焼結技術であり、材料の急速な緻密化を実現する。このプロセスでは、導電性グラファイトダイを通してパルス直流電流を流し、場合によっては材料自体にも流します。これにより、局所的な高温、プラズマ、ジュール加熱が発生し、粒子表面が活性化され、急速な結合と緻密化が促進される。SPSは、従来の焼結法に比べ、焼結温度の大幅な低下、加熱・冷却速度の高速化、保持時間の短縮を可能にします。その結果、特性が改善された高密度の材料が得られ、多くの場合、密度は99%を超えます。
キーポイントの説明
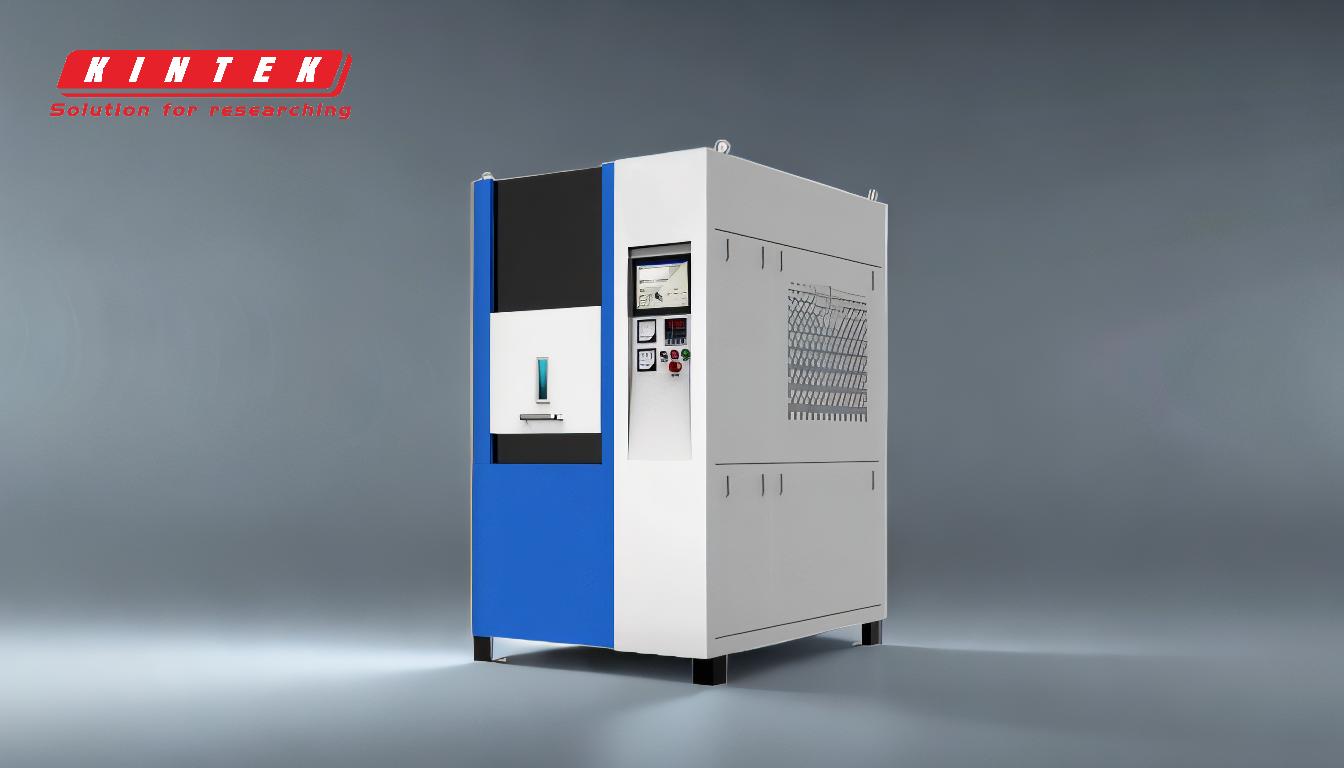
-
パルス直流電流の応用:
- SPSは、導電性グラファイトダイを通して、場合によっては焼結材料を通して直接印加されるパルス直流電流(DC)を利用します。
- 電流のパルス性(ON-OFFサイクル)により、粒子間に局所的な高温とプラズマが発生し、表面の活性化と結合が促進される。
-
プラズマと高温の発生:
- パルス電流は粒子間に火花プラズマを発生させ、超高温(最高10,000℃、18,032°F)に達する。
- この高温により、表面の汚染物質が酸化または蒸発すると同時に、粒子表面が溶けて融合し、最終的に緻密な構造になる「ネック」が形成されます。
-
ジュール加熱と均一な熱分布:
- 電流が材料を通過する際にジュール発熱が起こり、焼結体内で均一に発熱します。
- この均一な加熱により、焼結プロセスにとって重要な表面拡散と境界欠陥拡散が促進され、急速な緻密化が促進されます。
-
一軸加圧:
- 通電に加え、焼結過程で材料に一軸の圧力を加える。
- 圧力と電流の組み合わせにより、粒子の結合が強化され、気孔率が減少するため、材料の高密度化につながります。
-
迅速な高密度化と低い焼結温度:
- SPSは、従来の焼結方法と比較して、急速な加熱と冷却が可能で、保持時間も短い。
- このプロセスは、著しく低い温度(多くの場合、数百度低い温度)で緻密化を達成するため、材料の微細構造と特性を維持するのに役立ちます。
-
粒子結合のメカニズム:
- パルス電流により放電衝撃圧力と電界拡散を発生させ、粒子表面を活性化して結合を促進する。
- 粒子界面が溶融して結合し、空隙率の少ない緻密な構造が形成される。
-
別称と誤解:
- スパーク・プラズマ焼結」という名称にもかかわらず、プラズマが常にプロセスに存在するわけではないことが研究によって示されている。
- この技術の別名には、電界焼結法(FAST)、電界焼結法(EFAS)、直流焼結法(DCS)などがあり、プロセスにおける電界の主な役割を反映している。
-
SPSの利点:
- 高密度:SPSは99%を超える材料密度を達成できるため、高性能セラミックスや金属の製造に最適。
- 効率:急速な加熱・冷却速度と低い焼結温度により、エネルギー消費量と処理時間を削減します。
- 微細構造制御:低温で処理時間が短いため、従来の焼結では失われがちな微細構造を維持できる。
-
SPSの応用:
- SPSは先端セラミックス、金属、複合材料の製造に広く使用されている。
- SPSは、切削工具、航空宇宙部品、生物医学インプラントなど、高密度、微細粒度、強化された機械的特性を必要とする材料に特に有用である。
-
限界と考慮点:
- このプロセスには、導電性グラファイト・ダイやパルス直流電流を生成できる電力制御装置など、特殊な装置が必要である。
- SPS装置の初期コストが高いため、産業によっては採用が制限されることもあるが、高性能のアプリケーションでは、そのメリットがコストを上回ることも多い。
要約すると、スパークプラズマ焼結は、パルス直流電流、プラズマ生成、および一軸加圧を活用して、低温で材料の迅速な緻密化を実現する、非常に効率的かつ効果的な焼結技術である。微細構造を持つ高密度で高性能な材料を製造できるため、先進的な製造や材料科学において貴重なツールとなっている。
総括表
主な側面 | 概要 |
---|---|
パルス直流電流 | 局所的な高温とプラズマを発生させ、粒子結合を強化します。 |
プラズマと高温 | 最高10,000℃まで到達し、粒子表面を溶融・融合して緻密化。 |
ジュール加熱 | 均一な熱分布を確保し、迅速な高密度化を実現します。 |
一軸圧力 | 粒子結合を強化し、気孔率を低減します。 |
利点 | 高密度(99%以上)、高効率、微細構造制御。 |
用途 | 先端セラミック、金属、複合材料、航空宇宙、生体インプラント。 |
制限事項 | 特殊な装置を必要とし、初期コストが高い。 |
スパークプラズマ焼結がお客様の材料生産にどのような革命をもたらすかをご覧ください。 今すぐお問い合わせください !