PVD(Physical Vapor Deposition)とCVD(Chemical Vapor Deposition)は、基板上に薄膜を蒸着するために広く使われている2つの技術だが、そのメカニズム、プロセス、用途は大きく異なる。PVDは、蒸発やスパッタリングなどによる材料の物理的気化と、それに続く基板上への凝縮を伴う。これに対してCVDは、気体状の前駆物質と基板との化学反応によって固体皮膜を形成する。PVDとCVDのどちらを選択するかは、希望する皮膜特性、基材の材質、アプリケーションの要件などの要因によって決まる。一方、CVDはより緻密で均一な皮膜を作ることができますが、高温と長い処理時間を必要とします。
キーポイントの説明
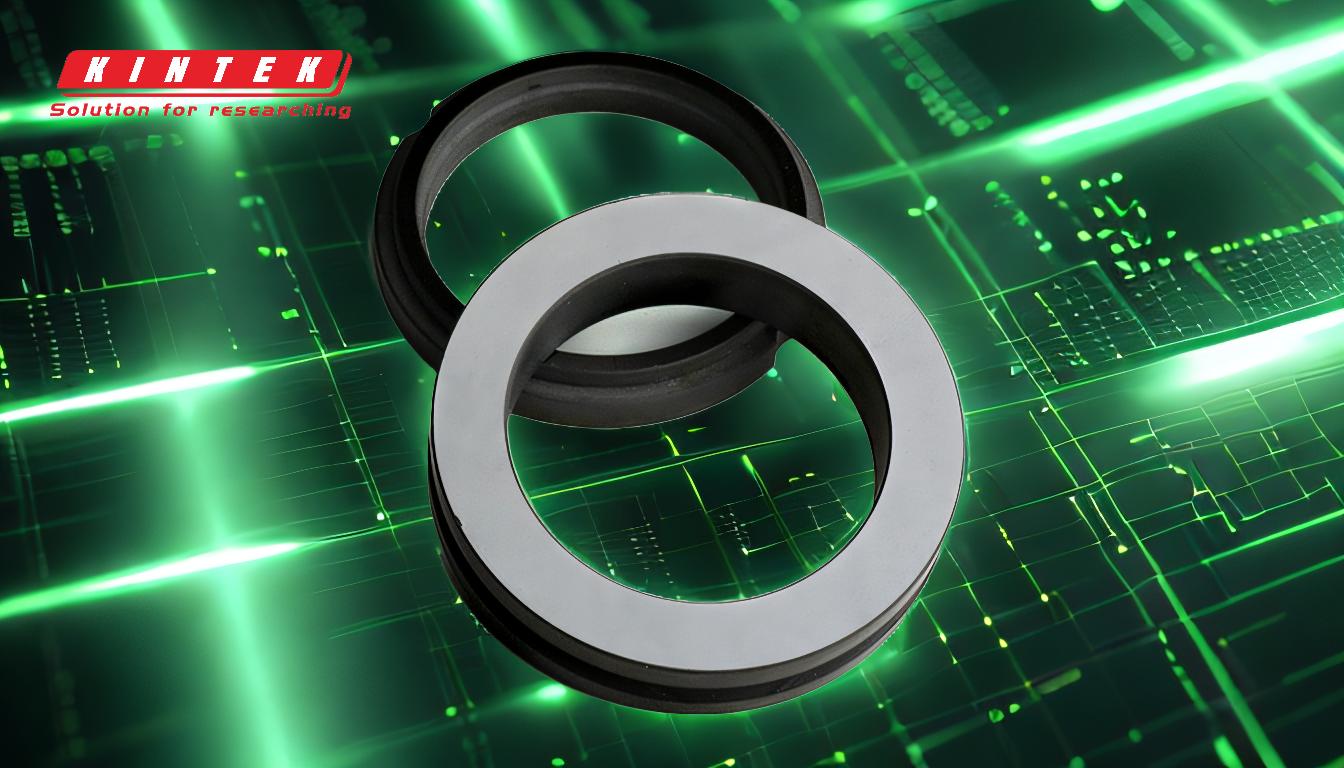
-
成膜メカニズム:
- PVD:蒸発、スパッタリング、イオン砲撃などの物理的プロセスにより、固体のターゲット材料を蒸発させ、基板上に凝縮させる。これはライン・オブ・サイトプロセスであり、化学的相互作用なしに材料が基板上に直接蒸着されることを意味する。
- CVD:ガス状前駆体と基材表面の化学反応に依存する。気体分子は反応または分解して固体コーティングを形成し、基材上で層ごとに成長する。これは多方向プロセスであり、複雑な形状をよりよくカバーすることができます。
-
使用温度:
- PVD:比較的低い温度、通常250℃~500℃で作動するため、熱に敏感な基板に適している。
- CVD:成膜に必要な化学反応を促進するため、通常450℃から1050℃の高温を必要とする。このため、温度に敏感な素材での使用が制限されることがある。
-
コーティングの性質:
- PVD:固体ターゲットを用いて、金属、合金、セラミックスなど幅広い材料を成膜できる。
- CVD:化学反応にガス状前駆体を使用するため、主にセラミックやポリマーを成膜する。
-
コーティング範囲と均一性:
- PVD:ライン・オブ・サイトであるため、緻密で均一なコーティングはできない。しかし、表面の平滑性と密着性は向上する。
- CVD:多方向蒸着プロセスにより、複雑な形状でもより緻密で均一なコーティングを実現。
-
膜厚と蒸着速度:
- PVD:通常、より薄い膜(3~5μm)をより速い蒸着速度で形成するため、大量生産に適している。
- CVD:より厚い膜(10~20μm)が得られるが、成膜速度が遅いため、大規模用途では効率が悪くなる可能性がある。
-
応力とクラック形成:
- PVD:冷却時に圧縮応力を形成し、コーティングの機械的特性を向上させる。
- CVD:加工温度が高いと、塗膜に引張応力や微細なクラックが発生し、耐久性に影響を及ぼす可能性がある。
-
用途:
- PVD:光学コーティング、装飾仕上げ、耐摩耗性コーティングなど、高い表面平滑性が要求される用途によく使用される。
- CVD:半導体製造、耐食コーティング、高温用途など、緻密で均一なコーティングを必要とする用途に適している。
-
材料適合性:
- PVD:金属や合金を含む幅広い材料を成膜できるため、材料適合性の面でより汎用性が高い。
- CVD:セラミックやポリマーなど、化学反応によって成膜できる材料に限定される。
まとめると、PVDとCVDのどちらを選択するかは、希望する膜特性、基板材料、処理条件など、用途の具体的な要件によって決まる。PVDは一般に高速で、低温で処理できるため、熱に敏感な基材に適している一方、CVDはより緻密で均一な皮膜が得られるが、高温と長い処理時間を必要とする。
総括表
側面 | PVD | CVD |
---|---|---|
成膜メカニズム | 蒸発やスパッタリングなどの物理的プロセス | ガス状前駆体と基板間の化学反応 |
使用温度 | 250°C ~ 500°C | 450°C~1050°C |
コーティング物質 | 金属、合金、セラミックス | 主にセラミックスとポリマー |
コーティングの均一性 | 密度が低く、均一性が低い | より緻密で均一 |
膜厚 | 3~5μm | 10~20μm |
蒸着速度 | 速い | 遅い |
用途 | 光学コーティング、装飾仕上げ、耐摩耗コーティング | 半導体製造、耐食コーティング |
PVDとCVDの選択でお困りですか? 今すぐ当社の専門家にお問い合わせください!