スパークプラズマ焼結(SPS) は、一軸加圧とパルス直流(DC)を組み合わせた最新の焼結技術であり、粉末を急速に緻密で均質な材料に凝集させる。このプロセスは、従来の焼結法と比較して、そのスピード、効率、および低温で高密度化を達成する能力が特徴です。SPSの主な段階には、ガス除去、真空生成、圧力印加、抵抗加熱、冷却が含まれる。各段階は、粉末粒子の緻密化と結合を成功させるために重要な役割を果たします。このプロセスでは、プラズマ放電、ジュール加熱、塑性変形を利用して、急速加熱、粒子結合、材料圧密を実現します。
キーポイントの説明
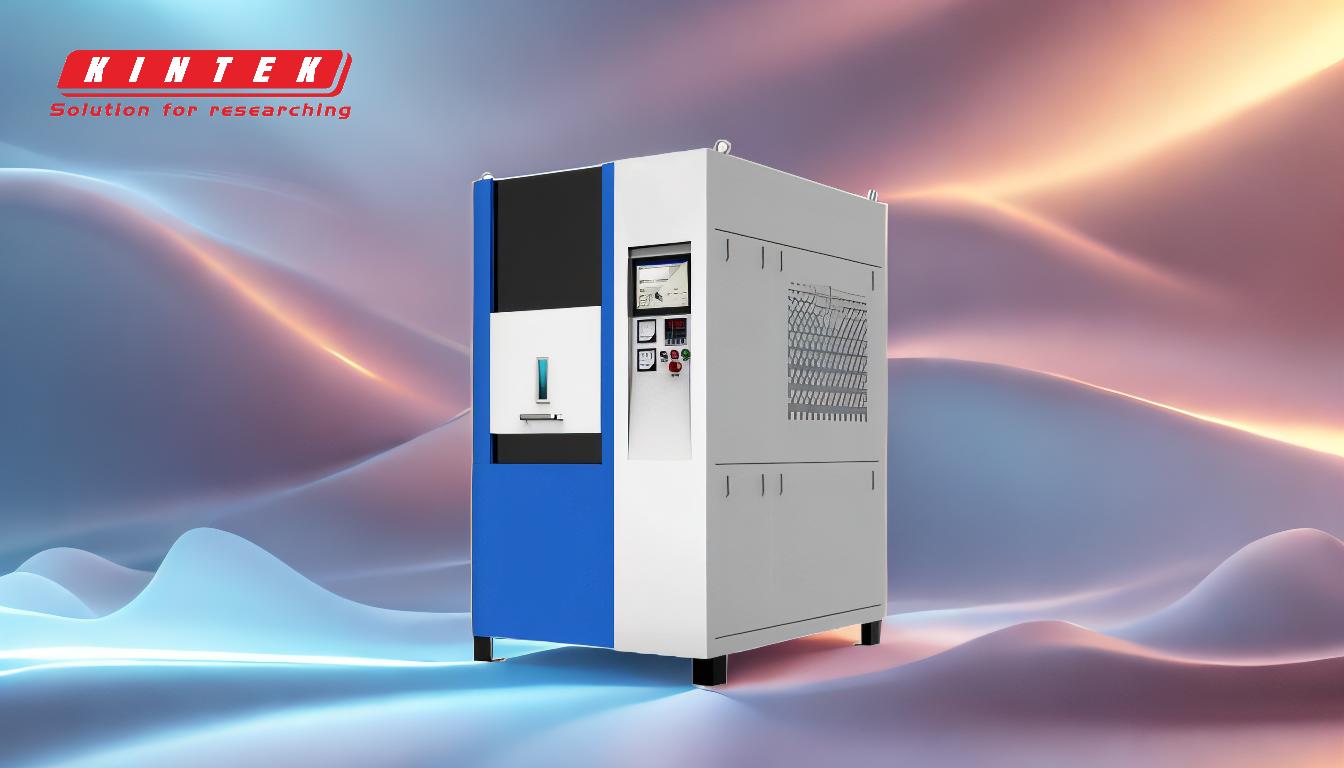
-
ガス除去と真空形成
- SPSの最初のステップは、焼結チャンバーからガスを除去し、真空または制御された雰囲気を作り出すことです。
- これは、粉末材料の酸化や汚染を防ぎ、最終製品の純度と品質を確保するために非常に重要です。
- A 真空環境 はまた、その後の段階での熱伝達とプラズマ発生を促進します。
-
圧力の適用
- 一軸圧力は、一般的に黒鉛で作られた金型内で粉末材料に加えられる。 グラファイト .
- この圧力は、粉末粒子を圧縮し、粒子間の隙間を減らし、焼結のための接触を促進するのに役立ちます。
- 加圧はまた、粒子の塑性変形を助け、高密度化を達成するために不可欠です。
-
抵抗加熱
- パルス状の直流電流をグラファイトダイに流し、導電性の場合は粉末材料自体にも流します。
- これにより、粒子間に局所的な高温とプラズマ放電が発生し、急速な加熱が起こります。
-
このプロセスには3つの加熱メカニズムがあります:
- プラズマ加熱:粒子間の放電によりプラズマが発生し、表面拡散と結合が促進される。
- ジュール加熱:材料内部の電気抵抗により発熱し、焼結を促進する。
- 塑性変形:熱と圧力の組み合わせにより粒子が変形し、界面で結合する。
- これらのメカニズムにより、従来の方法よりもはるかに低温・短時間での焼結が可能になる。
-
冷却段階
- 焼結工程の後、材料は室温まで急速に冷却されます。
- 急速冷却は、焼結材料の微細構造と特性を維持するのに役立ちます。
- 冷却速度は、最終製品の熱応力やクラックを防ぐために制御されます。
-
SPSの利点
- スピード:SPSは、従来の方法に比べて数分の一の時間で焼結プロセスを完了します。
- 低温:SPSは、従来の焼結よりも数百度低い温度で緻密化を実現します。
- 材料特性の向上:急速な加熱・冷却速度により、微細構造が得られ、機械的特性が向上します。
- 汎用性:SPSは、セラミック、金属、複合材料を含む幅広い材料に使用できます。
-
SPSの応用
- SPSは、ナノ構造セラミックス、機能性傾斜材料、複合材料などの先端材料の製造に広く使用されています。
- SPSは、航空宇宙、自動車、エレクトロニクスなど、微細構造と特性を精密に制御した高性能材料を必要とする産業で特に重宝されています。
以下の手順で スパークプラズマ焼結 は、優れた特性を持つ高品質で高密度の材料の製造を可能にし、先端材料製造のための好ましい選択肢となっている。
総括表
段階 | 主な内容 |
---|---|
ガス除去および真空 | ガスを除去し、酸化を防ぎ、制御された雰囲気を確保します。 |
圧力の適用 | 粉末粒子を圧縮し、隙間を減らし、塑性変形を助けます。 |
抵抗加熱 | プラズマ放電、ジュール加熱、迅速な粒子結合のためにパルスDCを使用します。 |
冷却段階 | 急速冷却により、微細構造を維持し、熱応力を防止します。 |
利点 | 速度、低温、特性の向上、材料の多様性。 |
用途 | 航空宇宙、自動車、エレクトロニクス、先端材料加工。 |
スパークプラズマ焼結がお客様の材料製造プロセスにどのような革命をもたらすかをご覧ください。 今すぐお問い合わせください !