コーティングチャンバー、特に真空蒸着プロセスで使用されるコーティングチャンバーは、様々な表面に薄く耐久性のある保護層を塗布するために設計された高度なシステムです。これらのチャンバーは真空条件下で作動し、固体の金属材料を気化させ、気化した原子が製品の表面に浸透して結合し、保護膜を形成します。このプロセスにはいくつかの重要なコンポーネントが関与しており、それぞれがコーティングプロセス全体の機能と効率に貢献している。これらのコンポーネントがどのように連動しているかを理解することで、真空コーティング技術の複雑かつ精密な性質を理解することができます。
キーポイントの説明
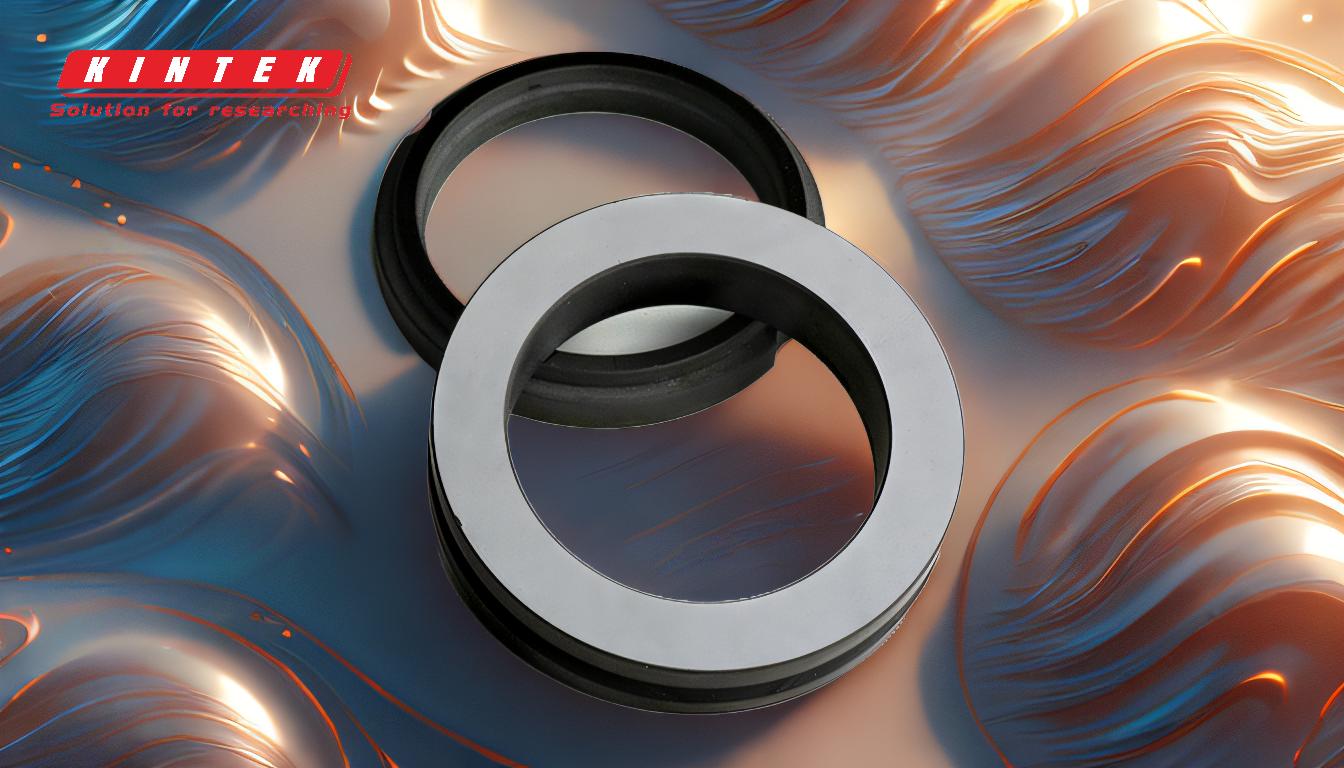
-
真空チャンバーとコーティング装置:
- 真空チャンバーは、コーティングプロセスが行われる核となる部品です。材料の気化と蒸着に不可欠な高真空環境を維持するように設計されています。
- チャンバーは通常、高温・高圧に耐える素材でできており、コーティングプロセスの安定した環境を確保します。
- チャンバー内にはコーティングされる製品が置かれ、気化した材料がその製品に向けられ、保護層が形成される。
-
真空取得部:
- チャンバー内の真空を作り出し、維持する役割を担う。チャンバーから空気やその他のガスを除去するポンプやバルブが含まれる。
- 真空は、汚染を防ぎ、気化した材料が製品表面まで妨げられることなく移動できるようにするため、非常に重要です。
-
真空測定部:
- 真空レベルの正確な測定は、コーティングプロセスの制御に不可欠です。この部分には、チャンバー内の圧力をモニターするゲージやセンサーが含まれます。
- 適切な真空レベルを維持することで、コーティングの品質と一貫性を保証します。
-
電源部:
- 電源は、固体金属材料を蒸発させるのに必要なエネルギーを供給する。これには、スパッタリングや蒸着源用の高電圧電源が含まれる。
- コーティング材料の正確な成膜を保証するために、電源は安定していて制御可能でなければなりません。
-
プロセスガス入力システム:
- 一部のコーティングプロセスでは、成膜プロセスを向上させたり、コーティングの特性を変更したりするために、特定のガスをチャンバー内に導入します。
- ガス導入システムは、これらのガスの流量と組成を制御し、コーティングの密着性、密度、その他の特性に影響を与えます。
-
機械的伝達部:
- チャンバー内で製品を移動・位置決めするための機構。製品が均一にコーティングされ、気化した材料が均一に分散されるようにします。
- 安定した膜厚と品質を得るためには、正確な動作が不可欠です。
-
加熱・温度測定装置:
- コーティングプロセスにおいて、温度制御は極めて重要です。ヒーターと温度センサーにより、チャンバーと製品が蒸着に最適な温度に保たれます。
- 適切な温度管理は、気化速度とコーティングの品質に影響します。
-
イオン蒸発とスパッタリングソース:
- これらのソースは、固体材料を蒸発させるために使用される。イオン蒸発法では材料が気化するまで加熱し、スパッタリング法では高エネルギーイオンを使用してターゲット材料から原子を叩き落とす。
- どちらのイオン源を使用するかは、使用する材料とコーティングに求められる特性によって決まります。
-
水冷システム:
- コーティング工程では大きな熱が発生します。機器の損傷を防ぎ、安定したプロセス条件を確保するためには、この熱を管理する必要があります。
- 水冷システムは、チャンバーやその他のコンポーネントに水を循環させて熱を放散し、安定した動作温度を維持します。
まとめると、コーティングチャンバーは、精密で高品質なコーティングを実現するために、さまざまなコンポーネントを統合した複雑なシステムです。各コンポーネントは、真空環境を作り出し、コーティング材を気化させ、製品表面への均一な成膜を実現するために特定の役割を果たします。これらのコンポーネントとその機能を理解することは、コーティングプロセスを最適化し、コーティングの望ましい保護特性と機能特性を達成するために不可欠です。
総括表
コンポーネント | 機能 |
---|---|
真空チャンバーとコーティング装置 | 材料の気化と成膜のために高真空環境を維持します。 |
真空取得部 | コンタミネーションを防ぐために真空状態を作り、維持する。 |
真空測定部 | 真空度を監視・制御し、安定した塗装品質を実現します。 |
電源部 | 固体原料を気化させるためのエネルギーを供給します。 |
プロセスガス入力システム | 成膜を促進したり、コーティング特性を変更するためのガスを導入します。 |
機械的伝達部 | 製品を正確に位置決めすることで、均一なコーティングを実現します。 |
加熱と温度測定 | 気化とコーティングの品質に最適な温度を維持します。 |
イオン蒸発&スパッタリングソース | 熱または高エネルギーイオンを使用して、蒸着用の材料を蒸発させます。 |
水冷システム | 安定した運転条件を維持するために熱を放散します。 |
先進の真空蒸着システムでコーティングプロセスを最適化します。 今すぐ専門家にお問い合わせください !