焼結プロセスは、材料科学と製造における重要な手法であり、材料の融点に達することなく粉末材料を固体の凝集構造へと変化させるために用いられる。このプロセスには、粉末の準備、圧縮、制御された加熱、冷却など、いくつかの段階が含まれる。焼結は、高精度、高硬度、高靭性を持つ部品の製造に広く利用されており、従来の製造方法では困難な複雑な形状や形状の製造に最適です。また、このプロセスはコスト効率が高く、精度と再現性を維持しながら迅速な大量生産が可能です。以下では、焼結の主な段階と利点を説明します。
主なポイントの説明
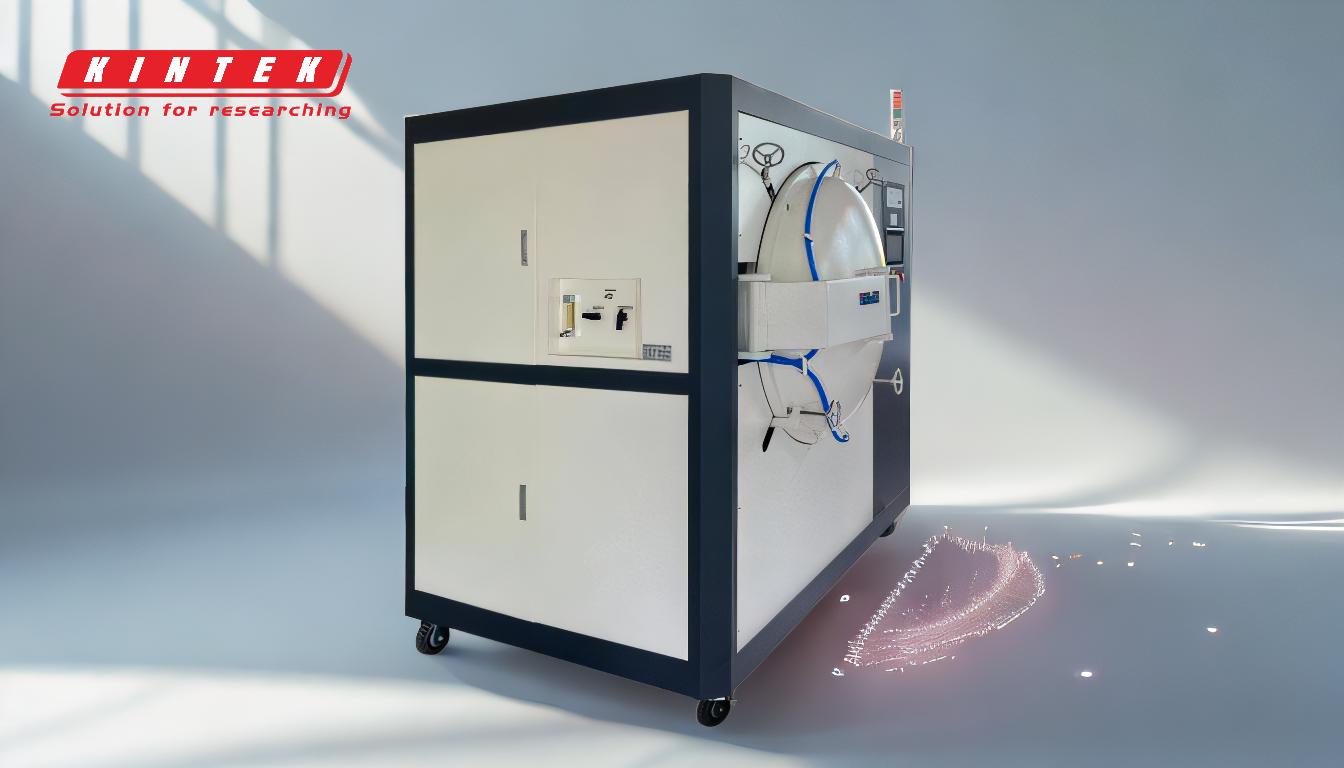
-
パウダー・コンパクトの準備
- この工程は、通常粉末状の原材料の準備から始まる。粉末は、水、ワックス、ポリマーなどの結合剤と混合され、くっつきやすくなる。
- その後、冷間溶接、プレスツール、3Dプリントレーザーなどの方法で粉末を圧縮し、「グリーン部品」を形成します。このステップにより、均一性が確保され、材料の空洞がなくなります。
-
加熱と圧密
- 圧縮された粉末は焼結炉に入れられ、融点ぎりぎりの温度まで加熱される。この制御された加熱により、粒子間の拡散プロセスが活性化され、ネック形成と緻密化が起こる。
- この段階で結合剤は蒸発または燃焼し、一次粒子はその表面で融合し始める。場合によっては、ブロンズのような中間結合剤が溶けて粒子間で結合し、一次材料はそのまま残る。
-
粒子の結合と高密度化
- 温度が上昇すると、粒子は拡散を受け、合体して緻密化する。この段階は、液相を形成して粒子の結合を強化する液相焼結(LPS)のような技術を用いて加速することができる。
- 材料は多孔質構造から緻密な固体の塊へと変化し、気孔率が減少して機械的特性が向上する。
-
冷却と凝固
- 加熱段階の後、材料は徐々に冷却される。この冷却プロセスにより、焼結製品は剛性の高い凝集構造に固化する。
- 最終製品は所望の形状を保持し、硬度、靭性、耐摩耗性などの特性が向上します。
-
焼結の利点
- 複雑な形状:焼結により、従来の製造方法では困難であった複雑な形状や形状の製造が可能になります。
- 材料特性:複数の素材の組み合わせが可能で、靭性や耐摩耗性などの特性を併せ持つ。
- 費用対効果:焼結により、金型コストを削減し、精度と再現性を維持しながら、迅速な大量生産を可能にします。
- 高融点材料:このプロセスは、タングステンやモリブデンのように融点が非常に高く、従来の溶融法が実用的でない材料に特に有効です。
-
焼結の応用
- 焼結は、ギア、ベアリング、フィルター、構造部品などの部品を製造するために、自動車、航空宇宙、エレクトロニクスなどの産業で広く使用されている。
- また、セラミック、金属、複合材料の製造にも使用され、汎用性の高い製造技術となっています。
焼結プロセスを理解することで、メーカーはその利点を活用し、高品質で耐久性のある部品を効率的かつコスト効率よく製造することができます。複雑な形状を作り出し、材料特性を組み合わせる能力により、焼結は現代の製造業に欠かせない技術となっている。
総括表
ステージ | ステージ |
---|---|
パウダーの調製 | 原料は粉末状に調製され、結合剤と混合される。 |
圧縮 | パウダーを圧縮して「グリーンパート」を形成し、均一性を確保して空隙をなくします。 |
加熱と圧密 | 圧縮されたパウダーは融点以下に加熱され、拡散と結合が活性化されます。 |
粒子の融合 | 粒子が合体して緻密化し、多孔質から緻密な固体構造へと移行する。 |
冷却と凝固 | 徐々に冷却することで、材料を固化させ、硬く凝集性のある最終製品に仕上げます。 |
利点 | - 複雑な形状 |
- 材料特性の向上
- 費用対効果の高い大量生産
- 高融点材料に最適 | 用途
| 自動車、航空宇宙、エレクトロニクス、セラミックス、金属、複合材料など。| 焼結が製造工程にどのような革命をもたらすかをご覧ください。 今すぐ専門家にお問い合わせください