セラミックの焼結には、熱と場合によっては圧力を加えることで、粉末材料を高密度の固体構造に変える一連の技術と工程が含まれます。このプロセスには通常、粉末の準備、成形、粒子を融合させるための加熱が含まれます。技法は、使用する材料、最終製品に求められる特性、利用可能な装置によって異なる。一般的な方法には、コンベンショナル焼結、スパークプラズマ焼結(SPS)、マイクロ波焼結、熱間加圧焼結などがある。それぞれの方法には独自の利点があり、温度制御、速度、圧力印加の必要性など、特定の要件に基づいて選択されます。
キーポイントの説明
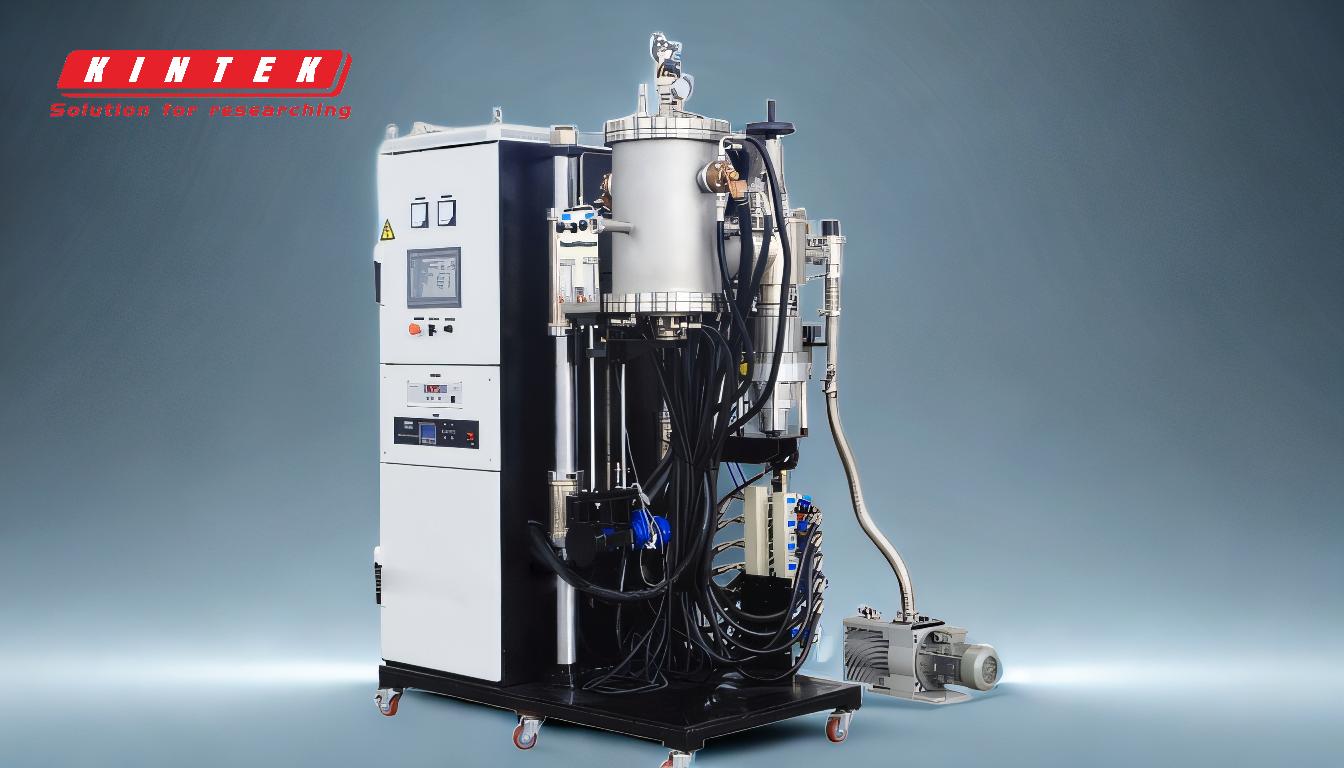
-
粉末の調製:
- 混合:この工程は、セラミック粉末を結合剤、凝集除去剤、場合によっては水と混合し、スラリーを形成することから始まります。この混合により、粒子の均一な分布が保証され、成形工程を助けます。
- スプレー乾燥:スラリーを噴霧乾燥して流動性のある粉末にします。
- プレス:乾燥した粉末を金型に押し込んで「グリーン・ボディ」を形成する。このプリフォームは所望の形状を持つが、最終製品の強度と密度には欠ける。
-
加熱と圧密:
- バインダーのバーンオフ:グリーンボディを低温で加熱し、バインダーを除去する。この工程は、最終製品の欠陥を防ぐために非常に重要である。
- 焼結:一次焼結工程では、セラミックを融点ぎりぎりの温度まで加熱します。これにより、粒子が緻密化して融合し、気孔率が低下して強度が高まります。正確な温度と時間は、セラミック材料と希望する特性によって異なります。
-
高度な焼結技術:
- 従来の焼結:これは最も一般的な方法で、セラミックを炉で加熱します。さまざまな材料に適していますが、時間がかかります。
- スパークプラズマ焼結 (SPS):この技法は、電流を利用して粉末成形体内で直接熱を発生させるため、急速な加熱と冷却が可能です。高密度で微細な構造を必要とする材料に特に有効です。
- マイクロ波焼結:この方法では、マイクロ波エネルギーを使用してセラミックを加熱します。均一な加熱が可能で、従来の方法に比べて焼結時間を大幅に短縮できます。
- 熱間加圧焼結:この方法では、加熱プロセス中に圧力を加えて緻密化を促進します。従来の方法では焼結が困難な材料に最適です。
-
焼結に影響を与える要因:
- 材料特性:セラミックの種類、粒子径、純度は、焼結プロセスに大きく影響します。一般に、粒子径が小さく純度の高い材料ほど焼結しやすい。
- 温度と時間:所望の密度と微細構造を得るには、温度と焼結時間を正確に制御することが重要です。
- 雰囲気:焼結環境(空気、真空、不活性ガスなど)は、セラミックの最終的な特性に影響を及ぼします。例えば、真空中での焼結は酸化を防ぎ、緻密化を向上させます。
-
焼結後のプロセス:
- 冷却:焼結後、セラミックはクラックを防ぎ、微細構造を安定させるために徐冷する必要があります。
- 仕上げ:最終的な寸法と表面品質を達成するために、機械加工、研磨、コーティングなどの追加工程が必要になる場合があります。
これらの重要なポイントを理解することで、購入者は、特定のニーズに適した焼結技術と材料について、十分な情報を得た上で決定を下すことができ、最適な性能とコスト効率を確保することができます。
総括表
焼結技術 | 主な特徴 | 最適 |
---|---|---|
従来の焼結 | 時間がかかるが、幅広い材料に適する | 時間的制約のない汎用セラミックス |
スパークプラズマ焼結 (SPS) | 急速加熱/冷却、高密度材料、微細構造 | 高密度、高精度が要求される材料 |
マイクロ波焼結 | 均一加熱、焼結時間の短縮 | 迅速な処理と均一な熱分布 |
熱間加圧焼結 | 圧力アシストによる高密度化、難焼結材料に最適 | 高密度化と強度が必要な材料 |
セラミック焼結プロセスを最適化する準備はできていますか? 当社の専門家に今すぐお問い合わせください にお問い合わせください!