粉末冶金における気孔率は、最終製品の機械的特性と性能に影響する重要な要因である。気孔率の低減は、製造工程におけるいくつかの重要なパラメータを最適化することで達成できる。これには、成形圧力、焼結温度、焼結時間を高めることが含まれ、これらはまとめて見かけの気孔率を低下させ、かさ密度を高めるのに役立つ。さらに、粒径が大きいと気孔率が増加する傾向があるため、粒径を制御することも極めて重要です。これらの要因を注意深く管理することで、メーカーは機械的特性を改善した高密度で低気孔率の部品を製造することができます。
キーポイントの説明
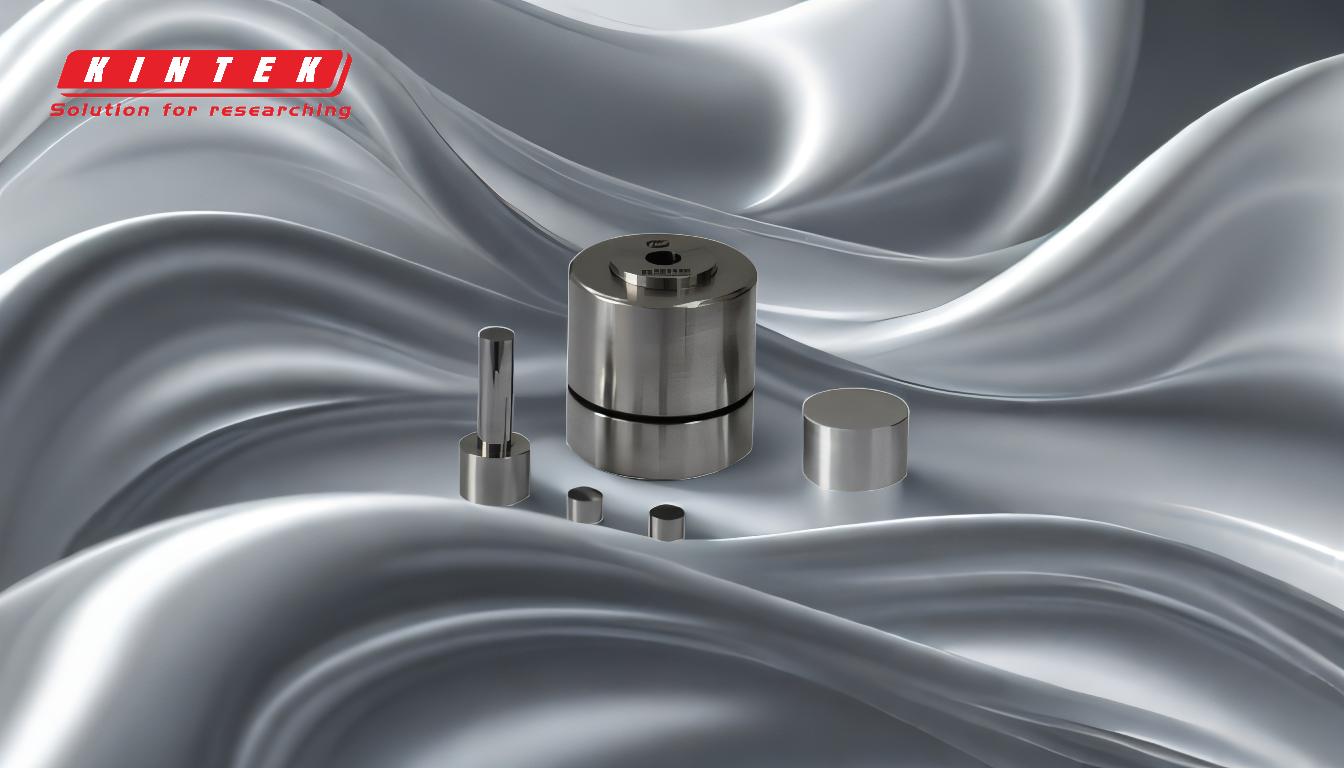
-
コンパクション圧の増加:
- インパクト:成形圧力が高いほど、粉末粒子間の隙間が減少し、気孔率の低い緻密な成形体が得られる。
- 成形メカニズム:締固め段階で圧力がかかると、粒子同士が強制的に密着し、空隙が最小限に抑えられ、圧粉体の嵩密度が高くなる。
- 実用上の考慮:より高い圧力は有益ですが、金型を損傷したり、部品に不均一な密度分布を引き起こしたりするリスクとのバランスを取る必要があります。
-
焼結温度と時間の最適化:
- インパクト:焼結温度が高く、焼結時間が長いほど、粒子の結合と拡散が促進され、気孔率が減少し、密度が向上する。
- メカニズム:焼結は、圧縮された粉末を融点以下に加熱することで、原子が粒子境界を越えて拡散し、気孔が閉じて材料が強化される。
- 実用的考察:過度の温度や時間は粒成長や歪みの原因となるため、慎重な最適化が必要である。
-
粒子径の制御:
- インパクト:一般的に粒子径が小さいほど、空隙が少なく効率的に充填されるため、空隙率が低くなる。
- メカニズム:細かい粒子は表面積と体積の比率が高く、焼結と結合を促進する。一方、粒子が大きいと隙間が多くなり、気孔率が高くなる。
- 実用的考察:粒子は小さい方が望ましいが、凝集のリスクも高まるため、加工時に管理する必要がある。
-
粉体製造方法:
- インパクト:金属粉末の製造方法は、そのサイズ、形状、分布に影響し、ひいては気孔率に影響する。
- メカニズム:霧化のような技術は、制御された粒径範囲を持つ粉末を生成し、空隙率を最小化するように調整することができる。破砕や粉砕では、不規則な形状の粒子が生成され、充填効率が低下する可能性がある。
- 実用上の考慮:適切な粉末製造方法を選択することは、望ましい粒子特性を達成し、気孔率を最小限に抑えるために不可欠です。
-
材料の選択:
- インパクト:基材の選択(銅基材、鉄基材など)は、粒子の形状、大きさ、焼結挙動の違いにより、気孔率に影響を与える可能性がある。
- メカニズム:ある材料は他の材料よりも焼結しやすく、緻密化と気孔率の低下をもたらす。
- 実用的考察:材料の選択は、意図された用途と望まれる機械的特性に沿うものでなければなりません。
これらの重要な要因に対処することで、メーカーは粉末冶金における気孔率を効果的に低減し、強度、耐久性、および性能を向上させた部品を製造することができます。
要約表
キーファクター | インパクト | メカニズム | 実用的な考察 |
---|---|---|---|
成形圧力を高める | 粒子間の隙間を減らし、空隙率の低い高密度の圧縮体を作ります。 | 圧力により粒子を近づけ、空隙を最小限に抑え、嵩密度を高めます。 | ダイの損傷や不均一な密度分布を避けるため、圧力のバランスをとる。 |
焼結温度と時間の最適化 | 粒子の結合を促進し、気孔を減らし、密度を高める。 | 融点以下で加熱すると原子が拡散し、気孔が閉じて材料が強化される。 | 粒成長や歪みを防ぐため、過度の温度や時間は避ける。 |
粒度のコントロール | 小さな粒子は効率的に充填し、気孔率を低減します。 | 微粒子は表面積対体積比が高く、焼結と結合を促進します。 | より小さな粒子で凝集リスクを管理します。 |
粉体製造方法 | 粒子径、形状、分布に影響を与え、気孔率に影響を与える。 | 粉砕/粉砕は不規則な粒子を生成することがある。 | 希望する粒子特性を得るために、適切な方法を選択する。 |
材料の選択 | 基材は、焼結挙動の違いにより気孔率に影響する。 | 材料によっては焼結しやすく、緻密化しやすく、気孔率が低くなるものもあります。 | 用途と必要な機械的特性に合わせて材料を選択してください。 |
粉末冶金プロセスを最適化する準備はできていますか? 当社の専門家に今すぐご連絡ください オーダーメイドのソリューションを