物理的気相成長(PVD)プロセスは、基板上に材料の薄膜を蒸着するために使用される真空ベースのコーティング技術である。高温真空やプラズマなどの物理的手段によって固体材料を蒸気の状態に変え、蒸気を基材に運び、凝縮させて薄く均一な層を形成する。PVDは、摩擦の低減、耐酸化性の向上、硬度の向上などに応用され、耐久性のある高性能コーティングを形成できることから広く利用されている。このプロセスは低圧条件下で行われ、スパッタリング、蒸発、熱処理などの工程を経るのが一般的です。
要点の説明
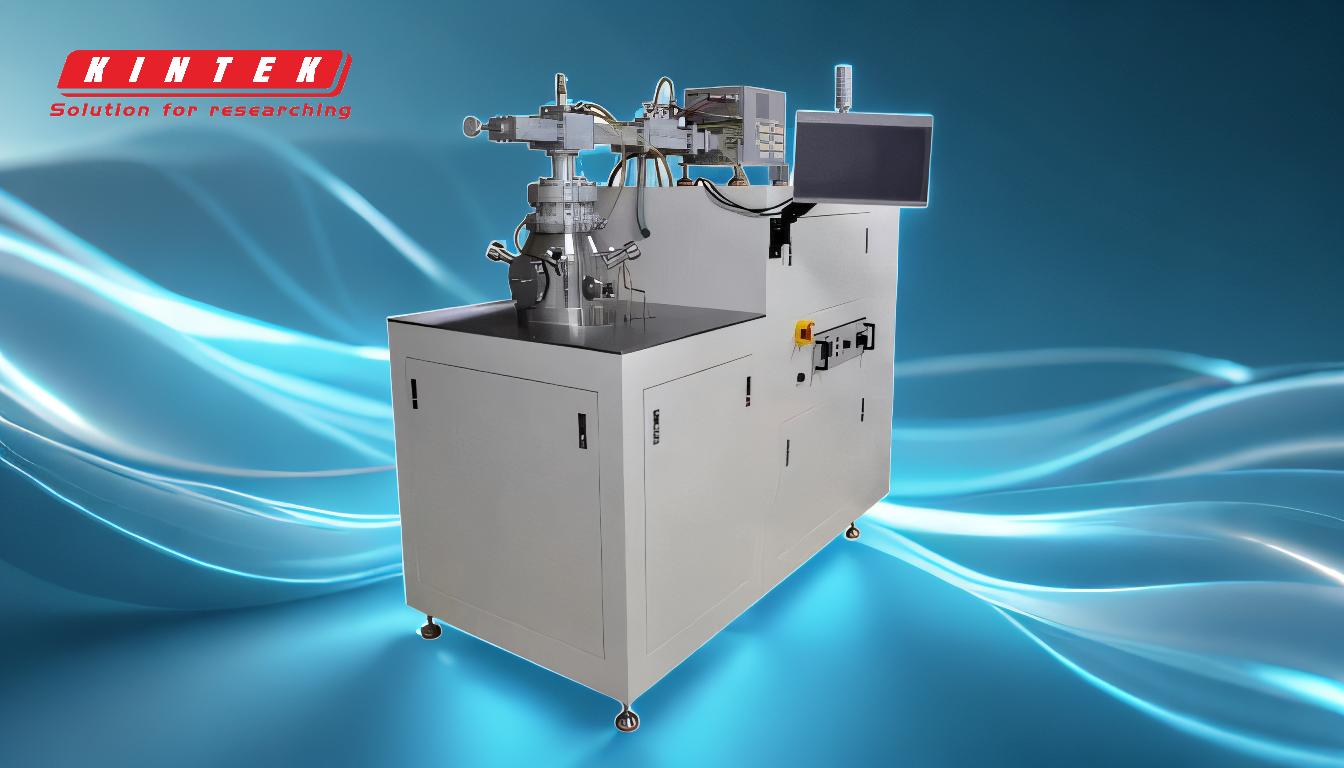
-
原料の気化:
- PVDプロセスは、固体の前駆物質を蒸気に変えることから始まる。これは、高温真空、電子ビーム砲撃、プラズマ放電などの物理的方法によって達成される。
- 例えば、固体の金属ターゲットに高エネルギーの電子またはイオンを照射し、スパッタリングとして知られるプロセスで表面から原子を放出させる。
- 気化した原子はその後、低圧環境を通して基板に輸送される。
-
基板への蒸気輸送:
- 気化された材料は、真空チャンバー内でソースから基板に運ばれる。このステップにより、気化された原子は、バックグラウンドガスの干渉を受けることなく、一直線に移動する(視線蒸着)。
- 真空環境は汚染を最小限に抑え、クリーンな蒸着プロセスを保証する。
- 場合によっては、化合物コーティング(窒化物や酸化物など)を形成するために、反応性ガスをチャンバー内に導入することもあります。
-
凝縮と皮膜形成:
- 気化した原子は基板に到達すると凝縮し、薄く均一な膜を形成する。膜の厚さはナノメートルからマイクロメートルまで、用途によって異なる。
- 凝縮プロセスは、基板温度、蒸着速度、反応性ガスの存在などの要因に影響される。
- 出来上がった膜は基材に強く密着し、硬度、耐摩耗性、耐食性などの特性が向上する。
-
PVD技術の種類:
- スパッタリング:ターゲット材料に高エネルギーのイオンを照射し、原子を放出させて基板上に堆積させる。この技術は、金属、合金、化合物の蒸着に広く使われている。
- 蒸発:原料を蒸発点まで加熱し、気化した原子を基板上に蒸着させる。この方法は、金属や半導体の薄膜の蒸着によく使われる。
- アーク蒸着:電気アークを使って原料を蒸発させ、それを基板に蒸着させる。この技術は、窒化チタン(TiN)のような硬質コーティングによく使用される。
-
PVDの利点:
- 高品質コーティング:PVDは、密着性と耐久性に優れた、緻密で均一なコーティングを実現します。
- 汎用性:金属、セラミックス、一部の有機化合物など、幅広い材料を蒸着できる。
- 環境に優しい:PVDは、有害な化学物質を使用せず、有害な副産物を生成しないクリーンなプロセスです。
- 高精度:このプロセスは膜厚と組成を正確に制御できるため、マイクロエレクトロニクス、光学、工具コーティングなどの用途に適している。
-
PVDの用途:
- 金型コーティング:PVDは、窒化チタン(TiN)やダイヤモンドライクカーボン(DLC)のような硬くて耐摩耗性のある材料で切削工具、金型、ダイをコーティングするために使用されます。
- 装飾コーティング:PVDは、時計、宝飾品、家電製品に耐久性があり、傷がつきにくいコーティングを施すために使用される。
- 半導体製造:PVDは、集積回路やマイクロエレクトロニクスデバイスの製造において、金属や誘電体の薄膜を成膜するために使用される。
- 光学コーティング:PVDは、レンズ、ミラー、その他の光学部品に反射防止膜、反射膜、保護膜を形成するために使用されます。
-
プロセス制御とモニタリング:
- PVDプロセスは、安定した膜質を確保するために注意深く制御されています。チャンバー圧力、基板温度、蒸着速度などのパラメーターはモニターされ、必要に応じて調整されます。
- 蒸着膜の膜厚をリアルタイムで測定するために、水晶振動子レートモニターがしばしば使用され、コーティングプロセスの正確な制御が保証されます。
まとめると、PVDプロセスは、幅広い用途の薄膜を成膜するための、多用途で精密な方法である。固体材料を蒸気に変え、基板上に凝縮させることで、PVDは様々な製品の性能や耐久性を向上させるコーティングを作り出す。
総括表
アスペクト | 詳細 |
---|---|
プロセスの概要 | 固体物質を蒸気に変え、輸送し、凝縮して薄膜にする。 |
主な技術 | スパッタリング、蒸着、アーク蒸着 |
利点 | 高品質、耐久性、汎用性、環境に優しい、精密制御 |
用途 | 工具コーティング、装飾コーティング、半導体、光学コーティング |
プロセス制御 | 監視パラメータ:圧力、温度、蒸着速度 |
PVDコーティングがお客様の製品をどのように向上させるかをご覧ください。 当社の専門家に今すぐご連絡ください オーダーメイドのソリューションを提供します!