薄膜蒸着入門
目的とプロセス
薄膜蒸着は、基板上にナノスケールの薄膜を蒸着させることを目的とした、半導体製造における重要なプロセスである。この最初のステップに続いて、エッチングや研磨を繰り返すなど、一連の入念な工程を経て、複数の積層層が形成される。これらの層は導電性または絶縁性のいずれかとなり、それぞれが緻密な回路設計を形成するように綿密にパターン化される。
薄膜堆積のプロセスは、半導体部品や回路を複雑なチップに統合するために不可欠である。成膜されパターン化された各層は、チップ全体の構造の中で特定の機能を果たし、チップの性能、信頼性、機能性に貢献します。薄膜蒸着プロセス特有の精度と制御は、これらの層が最新の半導体デバイスに要求される厳格な基準に確実に準拠するために不可欠です。
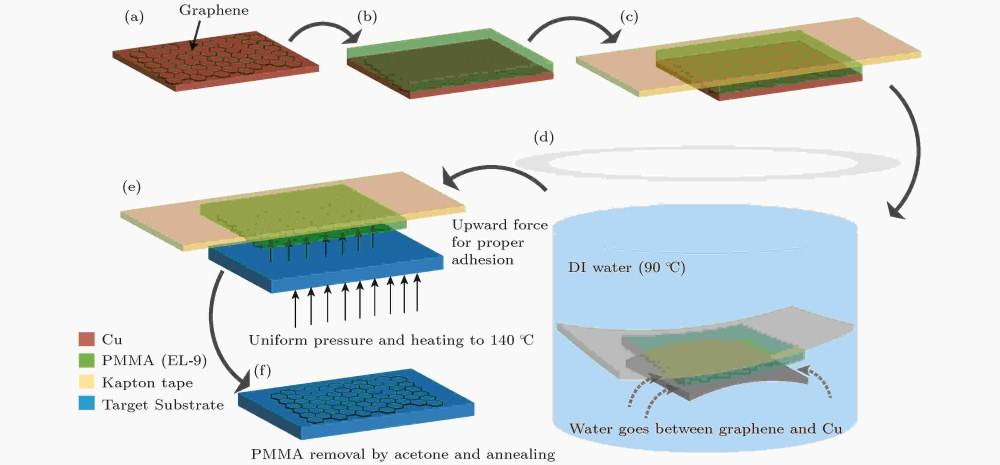
要するに、薄膜蒸着とは単に層を作ることではなく、半導体技術の基礎となる要素を層ごとに構築し、今日の電子機器を動かす高度で高性能なチップを実現することなのです。
化学気相成長法(CVD)
概要と特徴
化学気相成長法(CVD)は、ガス化合物の熱分解や反応によって薄膜を形成する高度な技術です。この方法にはさまざまな利点があり、半導体製造の要となっています。その主な強みのひとつは、堆積物の種類に多様性があることで、特定の特性を持つ多様な材料を作り出すことができる。この汎用性は、基板全体にわたって均一なコーティングを実現する能力によって補完され、最終製品の一貫した性能と信頼性を保証する。
高純度であることも、CVD成膜の重要な特徴である。CVDリアクター内の環境が制御されているため、汚染が最小限に抑えられ、不純物の少ない膜が得られる。この高純度は、微量の汚染物質でも機能に大きな影響を与える半導体デバイスの性能と寿命に不可欠です。
さらにCVDでは、成膜された膜の組成を正確に制御することができる。ガス化合物や反応条件を注意深く選択・調整することで、メーカーは特定の要件を満たすように膜の特性を調整することができる。このレベルの制御は、正確な材料特性が最適な性能に不可欠な先端半導体デバイスの製造において非常に貴重である。
しかし、CVDの顕著な限界の一つは、成膜プロセス中に高温が要求されることである。この高温により、使用できる基板の種類に制約が生じたり、冷却や熱管理のソリューションが必要になったりする可能性がある。この課題にもかかわらず、汎用性、均一性、純度、組成制御の面でCVDの利点があるため、半導体産業では欠かせない技術となっている。
CVDプロセスの段階
化学気相成長(CVD)プロセスは、気体状の前駆物質を基板上の固体膜に変化させる多段階の手順である。このプロセスは、半導体製造に不可欠な、組成と厚さを正確に制御した薄膜を作成するために非常に重要です。
-
基板へのガス拡散:初期段階では、反応性ガスが基板に向かって拡散する。この拡散は濃度勾配によって起こり、ガスは濃度の高い領域から低い領域へと移動する。この段階の効率は、温度、圧力、反応槽の設計などの要因に影響される。
-
基質表面への吸着:反応性ガスが基材に到達すると、基材表面に吸着する。吸着には、弱いファンデルワールス力が関与する物理的なものと、共有結合が形成される化学的なものがある。吸着の種類は、その後の化学反応や最終的なフィルムの品質に大きく影響する。
-
固体堆積物を形成する化学反応:第3段階は最も重要で、吸着されたガスを固体膜に変える一連の化学反応を伴う。この反応には、ガスが固体生成物と気体生成物に分解する熱分解と、2つ以上のガスが反応して固体生成物を形成する化学合成がある。形成される固体堆積物は通常、薄く、均一で、半導体製造の厳しい要件を満たす高純度である。
これらの各段階は、高品質な薄膜の成膜を確実にするため、綿密に制御されている。ガス拡散、吸着、化学反応の相互作用が、膜厚、均一性、組成など、成膜された薄膜の最終的な特性を決定する。
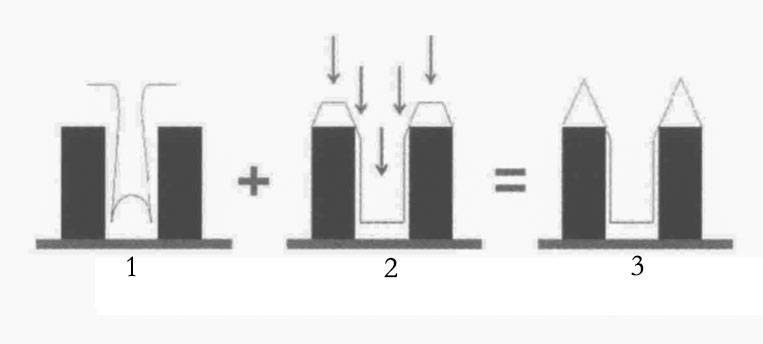
一般的なCVD反応
化学気相成長(CVD)の領域では、いくつかの基本的な反応がさまざまな薄膜の形成に極めて重要である。これらの反応は、熱分解、化学合成、化学移動の3種類に大別されます。これらの反応はそれぞれ成膜プロセスにおいて重要な役割を果たし、特定の特性を持つ多様な材料の創出を可能にする。
熱分解 熱によって化合物が分解され、固体膜が形成される。例えば、ポリシリコンの成膜は、高温でのシラン(SiH₄)の熱分解に依存することが多い。このプロセスは次のように表すことができる:
[このプロセスは次のように表すことができる。
化学合成 は、2つ以上の反応物が結合して新しい化合物を形成し、それが固体膜として析出するときに起こる。この例は、シランと酸素の反応による二酸化ケイ素(SiO₂)の形成である:
[例えば、シランと酸素の反応による二酸化ケイ素(SiO₂)の形成である。
化学移動 化学移動とは、ある相から別の相への化学種の移動のことで、典型的には気体前駆体から固体膜への移動である。顕著な例として、窒化ケイ素(Si₃N_2084)の成膜があり、これはシランとアンモニアの反応によって達成できる:
これらの反応は、CVDの多用途性を示すだけでなく、組成を制御した高純度で均一な膜を製造する能力を強調するものでもある。反応の種類と前駆体材料の選択は、堆積膜の特性を調整する上で重要であり、CVDを半導体製造における適応性の高い技術にしている。
CVD装置の種類
薄膜の成膜を促進するために、さまざまな化学気相成長(CVD)リアクターが採用されており、それぞれが特定のプロセスパラメーターと材料特性を最適化するように設計されている。リアクターは、その動作条件と利用するメカニズムに基づいて分類することができる。
-
大気圧CVD(APCVD): このタイプのCVDは大気圧で作動するため、シンプルで効率的な大規模生産に適している。しかし、圧力が高いため、膜厚や品質が不均一になる可能性がある。
-
低圧CVD(LPCVD): 圧力を下げることで、LPCVDは蒸着膜の均一性と品質を向上させる。この方法は、半導体製造における二酸化シリコンや窒化シリコンの成膜によく用いられる。
-
超高真空CVD(UHVCVD): 超低圧下で作動するUHVCVDは、蒸着膜の最高純度と均一性を保証します。この方法は、精度が重要な研究開発用途に特に有効です。
-
レーザーCVD: この技術は、レーザーを使用して基板を局所的に加熱するため、成膜プロセスを正確に制御することができる。レーザーCVDは、熱によるダメージを与えることなく、繊細な基板上に高品質の膜を形成するのに有利です。
-
有機金属CVD(MOCVD): MOCVDは、光電子デバイスで使用されるような複雑な膜を成膜するために、有機金属前駆体を使用します。この方法は汎用性が高く、複雑な組成の膜を作ることができる。
-
プラズマエンハンストCVD(PECVD): プラズマをプロセスに組み込むことで、PECVDは必要な成膜温度を下げ、温度に敏感な材料に適している。この方法は、半導体デバイスの誘電体膜の成膜に広く使用されている。
各タイプのCVDリアクターには独自の利点があり、材料とアプリケーションの特定の要件に基づいて選択されます。
物理的気相成長法(PVD)
概要と原理
物理的気相成長(PVD)は、綿密に制御された真空条件下で材料を気化させる高度なプロセスです。この技術は、特定の機能を持つ薄膜を蒸着するのに役立ち、様々なハイテク産業の要となっています。PVDプロセスでは、真空環境を利用して汚染物質を除去するため、出来上がった薄膜の品質が非常に高くなります。
PVDの多用途性は、さまざまな材料やフィルムタイプに対応できることにあります。金属であれ、セラミックスであれ、複合材料であれ、PVDは正確に成膜することができます。この適応性は、高性能で信頼性が高く、均一な薄膜が求められる半導体製造において極めて重要です。このプロセスは、優れた膜質を保証するだけでなく、導電性、反射率、硬度などの特性を調整した膜を作成することも可能です。
要するに、PVDは、汎用性があるだけでなく、優れた品質の薄膜を製造する能力によって際立っており、現代の半導体製造の武器として不可欠なツールとなっている。
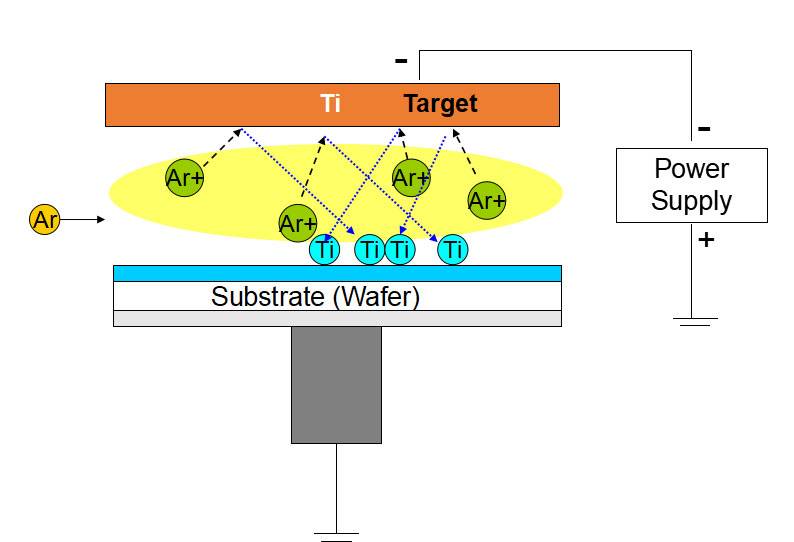
プロセスステップ
物理的気相成長(PVD)プロセスは、基板上に薄膜を正確に蒸着させるために設計された、綿密な一連のステップです。このプロセスは、真空条件下で材料を沸点まで加熱する重要なステップであるメッキ材料の気化から始まります。この加熱により、材料は固体または液体状態から気体状態に移行し、構成要素である原子、分子、またはイオンに分解される。
気化した原子、分子、イオンは、制御された移動段階を経る。この移動は真空環境によって促進され、衝突が最小限に抑えられ、粒子が基板に向かってまっすぐな経路を進むことができる。真空条件はまた、粒子が高いエネルギー・レベルを維持することを保証し、これは効果的な蒸着に不可欠である。
最後に、粒子は基板に到達し、堆積を開始し、薄膜を形成する。この蒸着プロセスは、粒子のエネルギーや入射角、基板の表面特性、真空圧など、いくつかの要因に影響される。その結果、均一で緻密な膜が基板に強固に密着し、所望の機能性と特性が得られる。
ステップ | 工程 |
---|---|
気化 | 真空下でメッキ材料を沸点まで加熱し、気体にすること。 |
移動 | 真空中で、原子/分子/イオンを基板に向けて制御しながら移動させる。 |
蒸着 | 高エネルギー粒子が基板表面に付着することにより、基板上に薄膜を形成する。 |
これらの各ステップは、PVDを半導体製造にうまく応用するために非常に重要であり、薄膜形成のための多用途で高品質な方法を提供します。
アプリケーションと利点
物理的気相成長法(PVD)は、主にその環境に優しい性質と生成される薄膜の優れた品質により、多くの産業で幅広い用途が見出されています。有害な化学物質や高エネルギーのプロセスを伴う他の蒸着技術とは異なり、PVDは真空条件下で作動するため、蒸着プロセスには汚染物質が含まれません。このため、環境コンプライアンスが重要な要素となる産業にとって理想的な選択肢となります。
PVDの際立った特徴のひとつは、成膜の均一性と密度です。このプロセスでは、厚みと構造が非常に均一な膜が得られるため、材料特性の精密な制御が必要な用途には極めて重要です。この均一性は、材料の気化と蒸着が制御されることで達成され、フィルムが所望の仕様に忠実であることを保証します。
さらに、PVDフィルムは被着体と強固に接着します。この強固な接着は、気化した材料が凝縮して基材表面と化学的に結合する直接蒸着プロセスの結果です。この強固な結合は、フィルムの耐久性を高めるだけでなく、さまざまな使用条件下でも無傷であることを保証するため、PVDフィルムは長期的な安定性と信頼性が求められる用途に適しています。
利点 | 特徴 |
---|---|
無公害性 | 真空条件下で動作するため、プロセス中に有害な排出物が発生しません。 |
均一で高密度なフィルム | 正確な厚みと構造を持つ、安定性の高いフィルムが得られます。 |
基材との強固な接着性 | 強固な接着力を確保し、耐久性と長期安定性を高めます。 |
まとめると、これらの利点の組み合わせにより、PVDは、薄膜の品質と信頼性が最重要視されるエレクトロニクスや光学から航空宇宙や自動車に至るまで、幅広い産業で好ましい選択肢となっています。
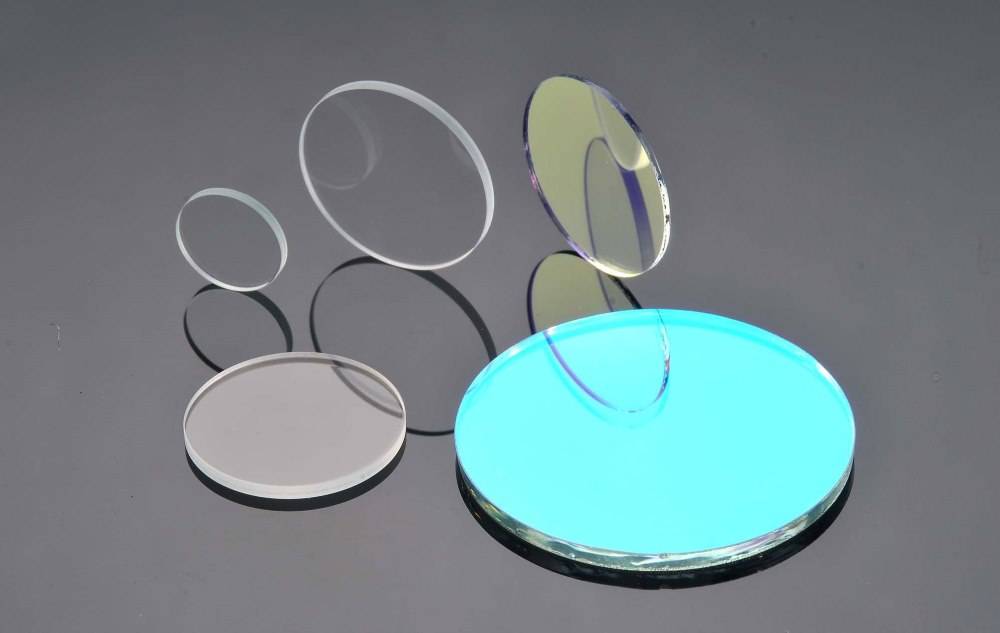
PVDの方法
PVD(Physical Vapor Deposition:物理的気相成長)は、真空条件下で精密な機能を持つ薄膜を成膜するために設計された、いくつかの高度な技術を包含しています。これらの方法は、高品質で均一、かつ高密度に接合された薄膜を製造できるため、さまざまな産業用途で極めて重要な役割を果たしています。
主なPVD法には以下のものがある:
-
真空薄膜コーティング:この方法では、真空チャンバー内で材料を気化させ、その蒸気を基板上に凝縮させます。コンタミネーションを最小限に抑え、膜厚と均一性のコントロールに優れています。
-
スパッタリングPVD:スパッタリングでは、ターゲット材料に高エネルギーの粒子(イオン)を衝突させて原子を移動させ、基板上に堆積させます。この方法は、金属、合金、化合物など、さまざまな材料の成膜に特に効果的です。
-
イオンコーティング:この技術では、イオンを基板に向かって加速し、蒸着膜の密着性と密度を高める。イオンコーティングは、密着性と耐久性の高い皮膜を形成できることで知られており、強固な保護が必要な用途に最適です。
これらの方法にはそれぞれ独自の利点があり、半導体製造やそれ以外のさまざまな用途に適しています。
無料相談はお問い合わせください
KINTEK LAB SOLUTION の製品とサービスは、世界中のお客様に認められています。弊社スタッフがどんなご質問にも喜んで対応させていただきます。無料相談にお問い合わせいただき、製品スペシャリストにご相談いただき、アプリケーションのニーズに最適なソリューションを見つけてください。