スパークプラズマ焼結(SPS) は、パルス直流電流(DC)を利用して粉末材料を急速に緻密化する高度な焼結技術です。従来の焼結法とは異なり、SPSは粉末成形体に一軸の機械的圧力とパルス電流を加え、局所的な高温(最高10,000℃)と粒子間のプラズマを発生させます。このプロセスにより、従来の焼結に比べ、急速な加熱速度(最高1000℃/分)、短い焼結時間、低温での緻密化が可能になります。機械的圧力、電場、熱場の組み合わせにより、粒子の結合が強化され、ナノ粉末の固有の特性を維持しながら、高密度材料(場合によっては99%以上)が得られます。SPSはエネルギー効率が高く、環境にやさしく、幅広い材料に適しています。
主なポイントを説明します:
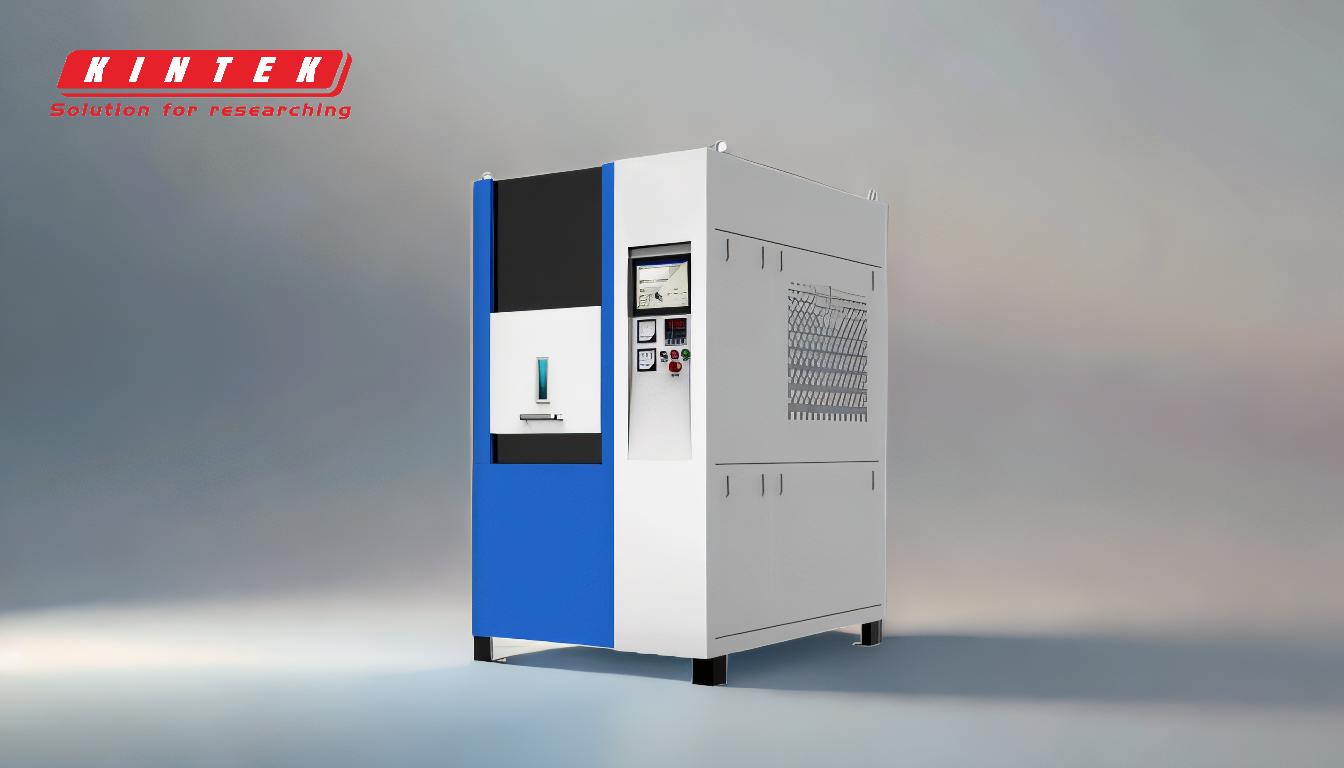
-
SPSの原則:
- SPSは電気火花放電の原理で作動し、高エネルギーのパルス電流が粉末粒子間に火花プラズマを発生させる。
- このプラズマは局所的な高温(最高10,000℃)を発生させ、粒子表面を溶融・融合させる。
-
コンポーネントとセットアップ:
- SPSはホットプレスに似たパンチ/ダイシステムを使用し、粉末をダイに入れ、一軸の機械的負荷をかけて圧縮する。
- パルス直流電流が粉末成形体に直接印加され、ジュール加熱とプラズマ活性化が発生する。
-
主なメカニズム:
- プラズマ活性化:パルス電流により粒子間にプラズマを発生させ、粒子間隙を減少させ、表面拡散を促進する。
- ジュール加熱:通電により粉末成形体を直接加熱し、急速加熱(最高1000℃/分)を実現。
- 吐出衝撃圧力:高エネルギーパルスが衝撃圧を発生させ、高密度化をさらに促進する。
-
SPSの利点:
- 急速な高密度化:SPSは数分で完全な緻密化を達成し、従来の焼結よりも大幅に速い。
- より低い焼結温度:SPSは従来の方法より200~500℃低い温度で材料を緻密化できる。
- エネルギー効率:直接加熱と短時間処理により、エネルギー消費量を削減。
- 素材保存:高い加熱・冷却速度は、最終製品のナノ粉末の特性を維持するのに役立ちます。
-
用途:
- SPSは、先端セラミックス、金属、複合材料、ナノ材料の焼結に広く使用されています。
- 特に、高密度で微細な組織制御が必要な材料に有益です。
-
環境および経済的利点:
- エネルギー使用量の削減と処理時間の短縮により、環境に優しいプロセスです。
- より低い焼結温度とより速い処理により、全体的な生産コストを削減します。
-
従来の焼結との比較:
- 輻射加熱に頼るホットプレスとは異なり、SPSは直接ジュール加熱とプラズマ活性化を使用します。
- SPSは、従来の方法に比べてわずかな時間で、より高い密度と優れた材料特性を実現します。
-
課題と限界:
- SPS装置の高コストと専門的なトレーニングの必要性が、採用の障壁となりうる。
- このプロセスは、特に急速加熱や高電界に敏感な材料など、すべての材料に適しているとは限りません。
機械的圧力、電場、熱場を組み合わせることで、SPSは材料の高密度化にユニークで効率的なアプローチを提供し、先端製造と材料科学における貴重な技術となっている。
要約表
アスペクト | 詳細 |
---|---|
原理 | パルスDCを使用して火花プラズマを発生させ、局所的な高温(最高10,000℃)を作り出す。 |
主なメカニズム | プラズマの活性化、ジュール加熱、放電衝撃圧力。 |
利点 | 迅速な高密度化、低い焼結温度、エネルギー効率、材料保存。 |
用途 | アドバンストセラミックス、金属、複合材料、ナノ材料 |
環境へのメリット | エネルギー使用量の削減と処理時間の短縮 |
課題 | 高い設備コストと専門的なトレーニングの必要性。 |
スパークプラズマ焼結がお客様の材料加工をどのように変えることができるか、検討する準備はできていますか? 今すぐお問い合わせください までご連絡ください!