製造、特に半導体製造における蒸着は、基板上に材料の薄膜を塗布する重要なプロセスである。このプロセスは、電子デバイスの骨格となる複雑な層を形成するために不可欠である。このプロセスでは通常、材料ソースを選択し、それを基板に運び、蒸着して薄膜を形成し、場合によっては膜を処理して特性を向上させる。高密度プラズマ化学気相成長法(HDP-CVD)、プラズマエンハンストCVD、CVDタングステンなどの技術が業界で一般的に使用されている。このプロセスは、所望のフィルム特性を達成するために、分析と修正を通じて微調整される。
キーポイントの説明
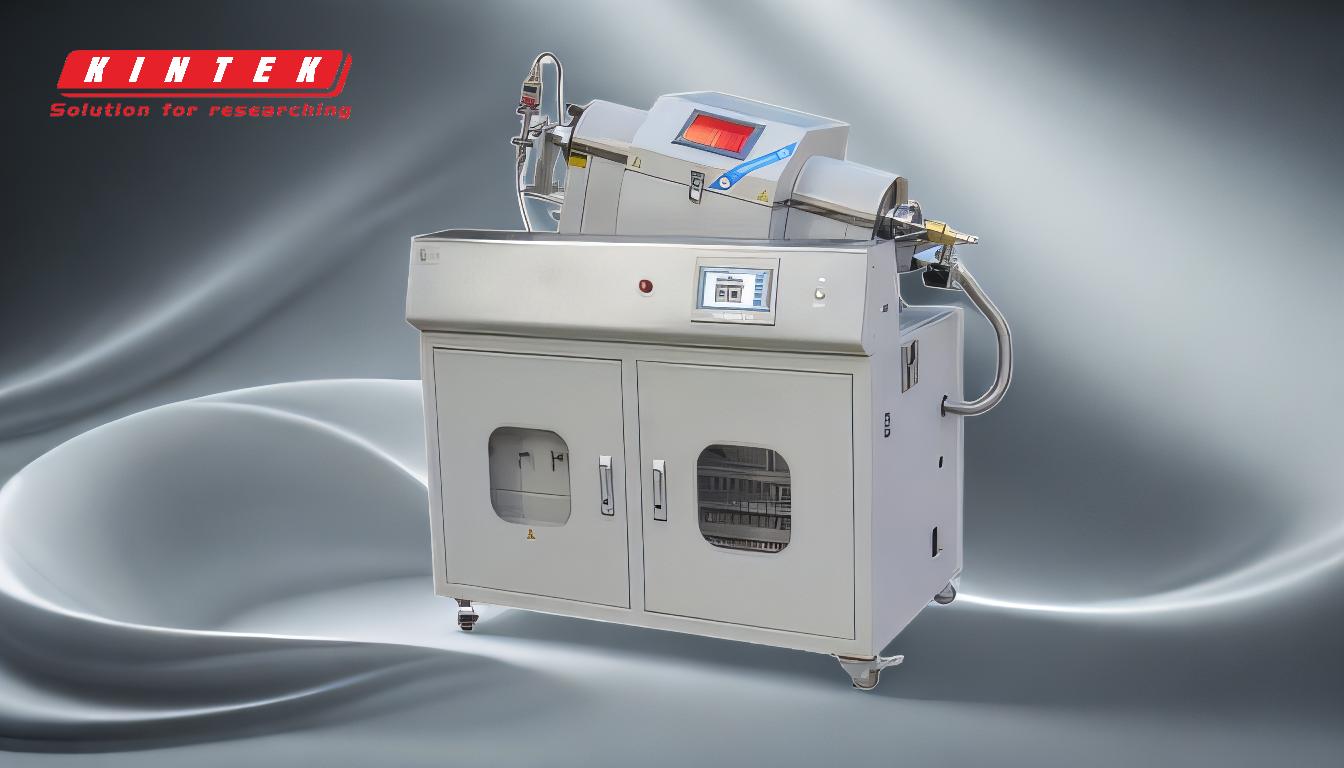
-
材料源(ターゲット)の選択:
- このプロセスは、ターゲットと呼ばれる純粋な材料源を選択することから始まる。この材料は、導電性、熱安定性、光学特性など、最終的な薄膜に求められる特性に基づいて選択される。
- 蒸着膜の品質と一貫性を確保するため、ターゲット材料は高純度でなければならない。
-
ターゲットの基板への搬送:
- ターゲット材料は次に基板に輸送される。この輸送は、使用される特定の蒸着技術によって、流体や真空などの媒体を介して行われる。
- 化学気相成長(CVD)のような技術では、ターゲット材料は多くの場合ガス状で、キャリアガスを通して基板に運ばれる。
-
基板への蒸着
- ターゲット材料が基板に到達したら、それを蒸着して薄膜を形成する。この蒸着は、物理的気相成長法(PVD)、化学的気相成長法(CVD)、原子層蒸着法(ALD)など、さまざまな方法で行うことができる。
- 成膜方法の選択は、材料特性、希望する膜厚、特定のアプリケーション要件などの要因によって決まります。
-
オプションのアニールまたは熱処理:
- 蒸着後、薄膜はアニールまたは熱処理を受けることがある。この工程は任意であり、結晶性、基板との密着性、電気的性能など、薄膜の特性を向上させるために行われる。
- アニーリングは、膜内の応力を緩和するのにも役立ち、これはデバイスの長期安定性にとって極めて重要です。
-
分析と修正:
- 最終段階では、蒸着膜の特性を分析する。この分析には、膜厚、均一性、導電率、その他の関連特性の測定が含まれる。
- 分析結果に基づいて成膜プロセスを修正し、所望の膜特性を達成することができる。この反復プロセスにより、最終製品が半導体製造の厳しい要件を満たすことが保証される。
-
一般的な成膜技術
- 高密度プラズマ化学気相成長法(HDP-CVD): 高密度プラズマを使用して成膜速度を向上させ、膜質を改善する技術。特に誘電体材料の成膜に有効である。
- プラズマエンハンストCVD(PECVD): PECVDは、プラズマを使用して成膜に必要な温度を下げるため、温度に敏感な基板に適しています。
- CVDタングステン: この技術は、半導体デバイスの相互接続に不可欠なタングステン膜の成膜に特に使用される。
まとめると、製造における成膜プロセスは、材料の選択から最終的な分析まで、複数のステップを含む複雑だが不可欠な手順である。各工程は、現代の電子デバイスの厳しい要求を満たす高品質の薄膜を確実に製造するために、注意深く制御されている。
総括表
ステップ | 説明 |
---|---|
1.材料の選択 | 希望するフィルム特性に基づいて、高純度のターゲット材料を選択する。 |
2.輸送 | 流体、真空、またはキャリアガスで材料を基板に輸送する。 |
3.蒸着 | PVD、CVD、ALDなどの方法を用いて基板に材料を塗布する。 |
4.オプションのアニーリング | フィルムを熱処理して、結晶性や接着性などの特性を向上させる。 |
5.分析と改良 | フィルムの特性を分析し、特定の要件を満たすようにプロセスを改良する。 |
6.一般的な技術 | HDP-CVD、PECVD、CVDタングステンは、半導体製造に広く使用されています。 |
成膜プロセスに関する専門家の指導が必要ですか? 今すぐご連絡ください 製造ワークフローの最適化のために