化学溶液析出法(CSD)は、ゾル-ゲル法とも呼ばれ、精密な化学量論的制御で薄膜を作るために広く使われている技術である。このプロセスは、有機溶媒に溶解した金属有機物を含む液体前駆体溶液から始まる。この溶液は、通常スピンコーティングによって基板上に蒸着され、均一な層が形成される。その後、フィルムは乾燥と熱分解を経て溶媒を除去し、有機成分を分解して非晶質フィルムとなる。最後に、フィルムを熱処理して結晶化させ、目的の結晶相を得る。CSDは、その簡便さ、費用対効果、高品質の薄膜を製造する能力が評価されている。
キーポイントの説明
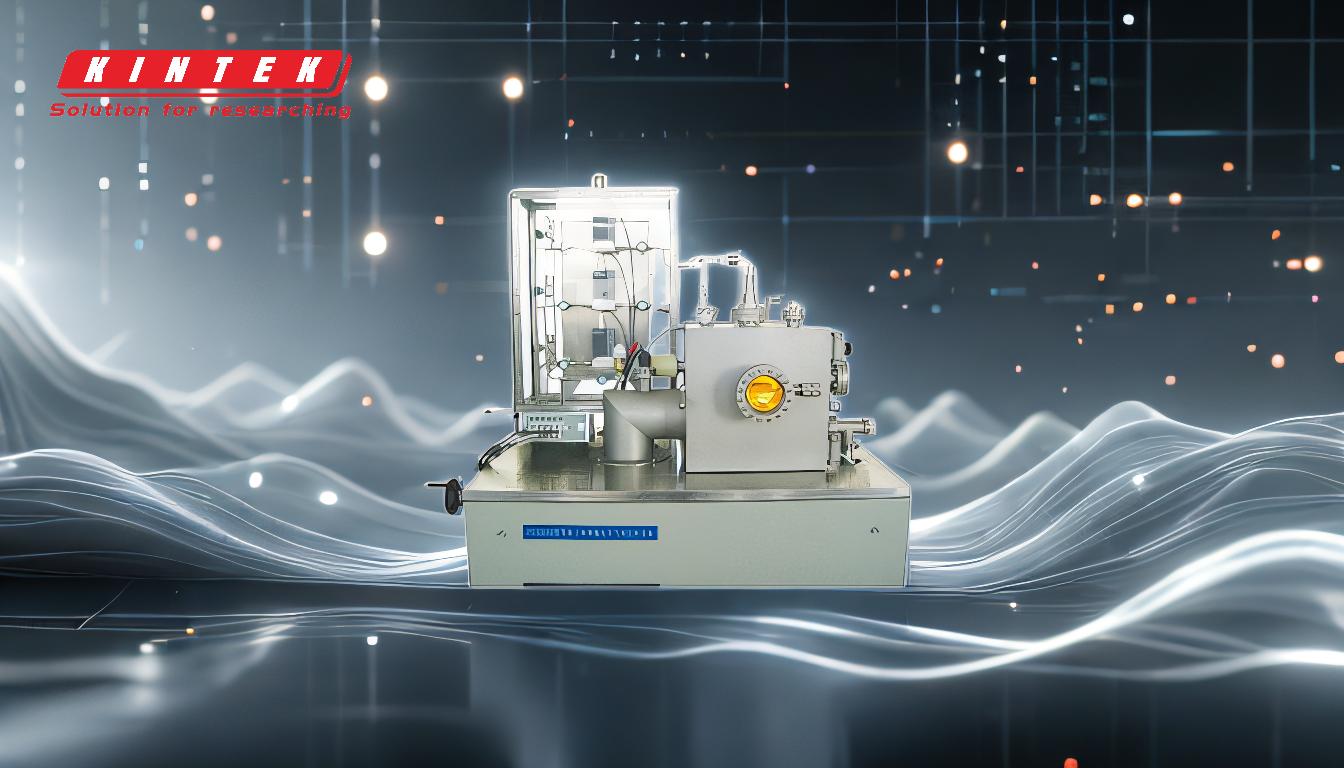
-
前駆体溶液の調製:
- 有機溶媒に有機金属化合物を溶解して前駆体溶液を調製する。これらの化合物は、所望の最終材料組成に基づいて選択される。
- 溶液は、均一な析出と最終膜の正確な化学量論を保証するために、均質で安定したものでなければならない。
-
スピンコートによる成膜:
- 前駆体溶液は、スピンコーティングを使って基板上に蒸着される。この技術では、基板を高速で回転させることにより、基板上に溶液を均一に広げる。
- スピンコートにより、厚みを制御した均一な薄膜を得ることができ、これは一貫した材料特性を得るために重要である。
-
乾燥と熱分解:
- 成膜後、溶媒を蒸発させる乾燥工程を経て、有機金属化合物の固体層が残る。
- 続いて熱分解が行われ、フィルム中の有機成分が熱分解される。このステップで残留有機物が除去され、フィルムはアモルファス状態に変換される。
-
結晶化:
- 非晶質フィルムに高温の熱処理を施し、結晶化を誘導する。
- このステップにより、フィルムは電気的、光学的、機械的特性など、所望の相と特性を持つ結晶構造に変化する。
-
CSDの利点:
- 費用対効果:CSDは、物理的気相成長法(PVD)や化学的気相成長法(CVD)のような他の薄膜形成技術に比べて比較的安価である。
- 化学量論的精度:この方法では、最終フィルムの化学組成を正確に制御することができ、正確な化学量論が保証される。
- 汎用性:CSDは、酸化物、窒化物、複雑な多成分系を含む幅広い材料の蒸着に使用できます。
-
用途:
- CSDは、電子デバイス、センサー、光学コーティングの製造に一般的に使用されている。
- 特に、強誘電体、圧電体、超伝導体などの特性を調整した薄膜の製造に有用である。
これらのステップを踏むことにより、化学溶液析出は、組成と構造を正確に制御した高品質の薄膜を製造するための、信頼性が高く効率的な方法を提供する。
要約表
ステップ | 説明 |
---|---|
前駆体溶液調製 | 有機金属化合物を溶媒に溶解し、均一で安定した溶液にする。 |
スピンコートによる成膜 | スピンコートで溶液を均一に広げ、均一な薄膜を成膜します。 |
乾燥と熱分解 | 溶媒を除去し、有機物を分解して非晶質膜を形成する。 |
結晶化 | 所望の結晶相を得るために熱処理を施す。 |
利点 | 費用対効果、化学量論的精度、多様な材料適合性。 |
用途 | エレクトロニクス、センサー、光学コーティングに使用され、材料特性を調整します。 |
CSDがお客様の薄膜製造プロセスをどのように強化できるかをご覧ください。 今すぐお問い合わせください !