物理的気相成長法(PVD)は、真空を利用したコーティングプロセスで、基板上に薄膜を形成するのに用いられる。このプロセスでは、熱蒸発、スパッタリング、イオン砲撃などの方法で固体材料を蒸気相に変換し、基板上に蒸気を凝縮させて薄く均一な層を形成します。PVDは、エレクトロニクス、光学、工具製造など、耐久性のある高性能コーティングを必要とする産業で広く使用されている。このプロセスは、優れた密着性、高純度、精密な膜厚制御を特徴とし、耐食性、耐摩耗性、熱安定性を必要とする用途に適しています。
キーポイントの説明
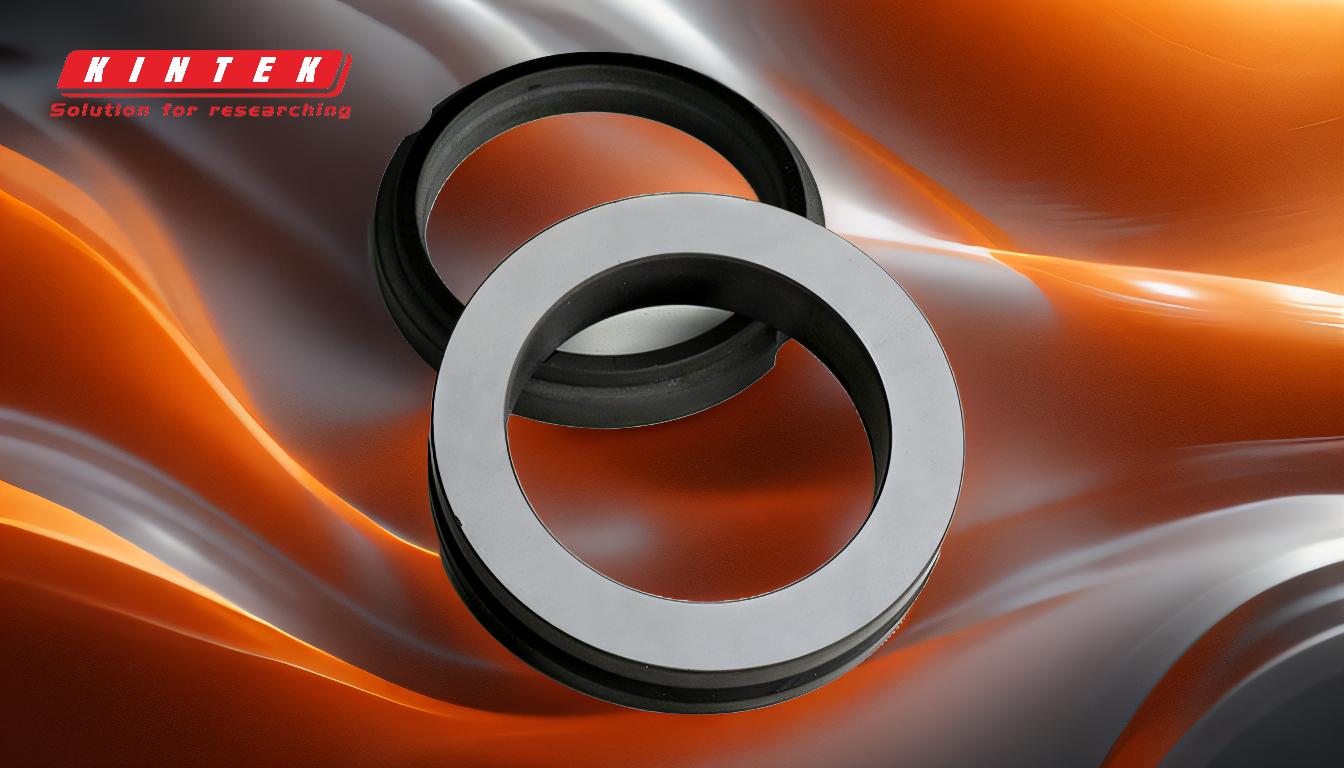
-
真空環境:
- PVDは真空チャンバー内で行われ、バックグラウンドガスによる汚染を最小限に抑え、クリーンな成膜プロセスを保証します。
- チャンバー内の圧力を下げると、バックグラウンドガスと蒸着材料との化学反応の可能性が低くなり、コーティングの品質が損なわれる可能性があります。
-
ソース材料の気化:
-
固体の前駆体材料(ターゲット)は、いくつかの方法のいずれかを用いて蒸気相に変換される:
- 熱蒸発:ターゲット材料は蒸発するまで加熱される。これは、抵抗加熱または電子ビーム加熱によって達成することができる。
- スパッタリング:高エネルギーのイオンがターゲット材料に衝突し、原子を表面から気相に叩き落とす。
- イオンプレーティング:スパッタリングと蒸発を組み合わせたもので、蒸着前にターゲット材料を気化・イオン化する。
-
固体の前駆体材料(ターゲット)は、いくつかの方法のいずれかを用いて蒸気相に変換される:
-
気化した材料の輸送:
- 気化した原子や分子は、真空チャンバー内を基板に向かって移動する。
- 真空環境は、気化した粒子が一直線に移動することを保証し、蒸着プロセスを正確に制御することを可能にする。
-
基板上の凝縮:
- 気化した物質が基材上に凝縮し、薄く均一な膜を形成する。
- フィルムと基材との密着性は一般的に強く、耐久性のあるコーティングが得られる。
-
膜厚と速度のコントロール:
- 水晶振動子式レートモニターは、成膜速度と膜厚の測定と制御によく使用される。
- これにより、コーティングが用途に応じた仕様に適合することが保証される。
-
PVDのサブメソッド:
- 熱蒸発:融点の低い材料に適している。ターゲット材料は蒸発するまで加熱され、蒸気は基板上で凝縮する。
- スパッタリング:融点の高い材料に最適。高エネルギーイオンがターゲットに照射され、原子が放出され、基板上に析出する。
- イオンプレーティング:蒸発とイオン化を組み合わせ、密着性と膜密度を向上。
-
用途と利点:
- PVDコーティングは、エレクトロニクス(半導体デバイス用)、光学(反射防止コーティング用)、製造(耐摩耗工具用)など、幅広い産業で使用されている。
- このプロセスでは、優れた密着性、高純度、精密な膜厚制御が可能で、耐久性、耐食性、熱安定性が求められる用途に適しています。
-
PVDの利点:
- 高い接着性:コーティングは基材に強力に密着し、長期間の性能を保証します。
- 高純度:真空環境はコンタミネーションを最小限に抑え、高純度のコーティングを実現します。
- 精度:このプロセスでは、膜厚と組成を正確に制御することができます。
- 汎用性:PVDは、金属、セラミック、複合材料など、さまざまな材料に使用できます。
-
課題と考察:
- コスト:PVD装置とプロセスは、特に大規模なアプリケーションでは高価になる可能性がある。
- 複雑さ:このプロセスでは、最適な結果を得るために専門的な設備と専門知識が必要である。
- 材料の制限:材料によっては、その物理的性質(融点、蒸気圧など)により、PVD法に適さないものもあります。
要約すると、PVDは優れた特性を持つ薄膜を成膜するための汎用性が高く精密な方法である。制御された環境で高品質のコーティングを製造できることから、幅広い産業用途で利用価値の高いプロセスとなっている。
総括表
アスペクト | 詳細 |
---|---|
プロセス | 固体材料を蒸気に変換し、基板上に凝縮させて薄膜を形成する。 |
主な方法 | 熱蒸着、スパッタリング、イオンプレーティング |
応用分野 | エレクトロニクス、光学、工具製造 |
利点 | 高粘着性、高純度、精密な厚み制御、汎用性 |
課題 | 高コスト、複雑さ、材料の制限 |
PVDがお客様の産業アプリケーションをどのように強化できるかをご覧ください。 今すぐご連絡ください までご連絡ください!