薄膜製造にはさまざまな方法があり、物理的成膜プロセスと化学的成膜プロセスに大別される。物理蒸着法には、真空蒸着、レーザーアブレーション、分子線エピタキシー(MBE)、スパッタリングなどがある。化学蒸着法には、化学気相成長法(CVD)、原子層エピタキシー法、スプレー熱分解法、ゾルゲル法、スピンコーティング法、ディップコーティング法などがある。これらの方法は、望ましい膜特性、基板材料、アプリケーションの要件に基づいて選択される。成膜プロセスには通常、吸着、表面拡散、核形成といった複数の段階があり、これらは材料や基板の特性に影響される。PVDやCVDのような一般的な技術は、厚さと特性を正確に制御した薄膜を製造するために、産業界で広く使用されています。
キーポイントの説明
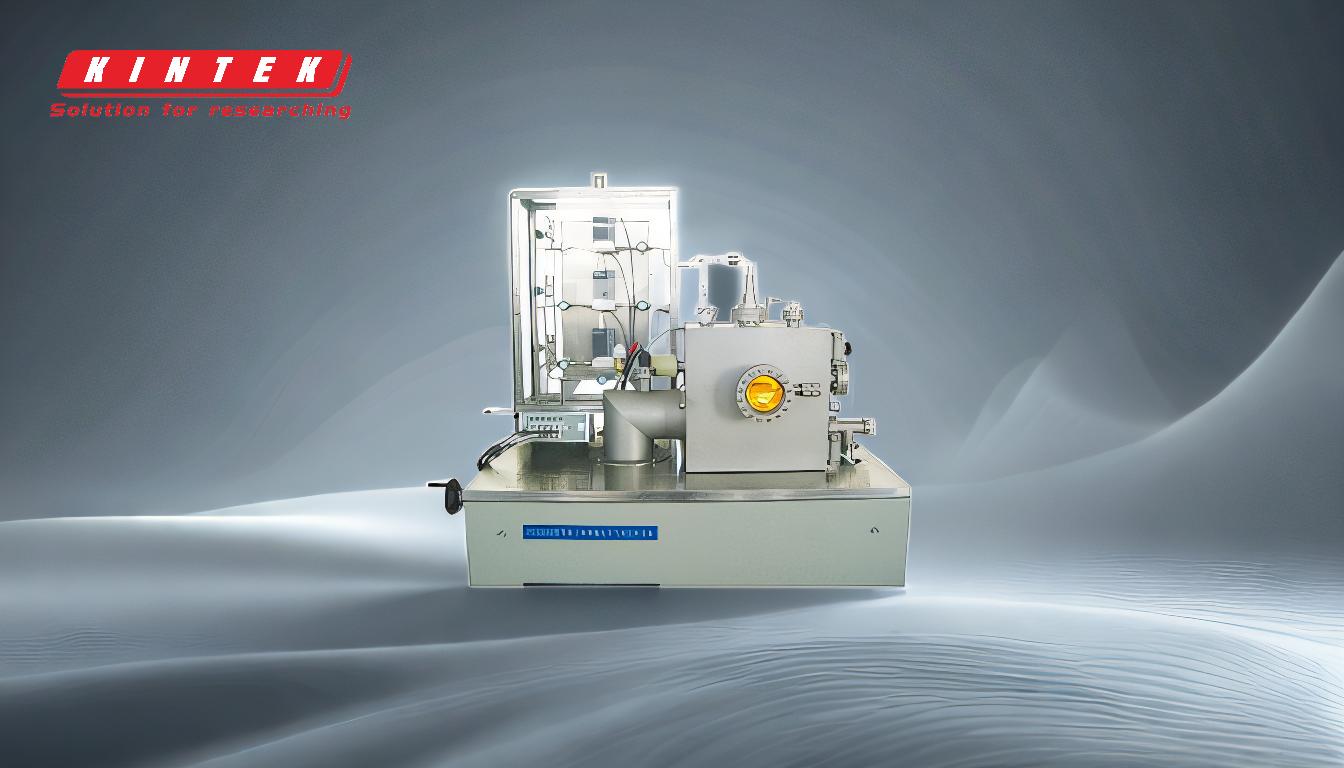
-
物理蒸着法:
- 真空蒸発:真空中で材料を蒸発するまで加熱し、基板上で凝縮させて薄膜を形成する手法。この方法は蒸気圧の高い材料に適している。
- レーザーアブレーション:高出力レーザーを用いてターゲットから材料を蒸発させ、基板上に堆積させる。この方法は、複雑な材料や多層構造に有効である。
- 分子線エピタキシー(MBE):高度に制御されたプロセスで、原子や分子のビームを基板上に照射し、薄膜を一層ずつ成長させる。MBEは高品質な結晶膜の製造に適している。
- スパッタリング:高エネルギーイオンの衝突により、固体のターゲット材料から原子が放出され、この原子が基板上に堆積するプロセス。スパッタリングは汎用性が高く、さまざまな材料に使用できる。
-
化学蒸着法:
- 化学気相成長法 (CVD):ガス状の前駆体を基板表面で反応させ、固体薄膜を形成する。CVDは、高品質で均一な薄膜の成膜に広く用いられ、さまざまな材料に適している。
- 原子層エピタキシー(ALE):CVDの一種で、薄膜を1原子層ずつ堆積させるため、膜厚や組成を精密に制御できる。
- スプレー熱分解:目的の材料を含む溶液を加熱した基板にスプレーし、溶媒を蒸発させて材料を分解させ、薄膜を形成する技術。
- ゾル-ゲル:溶液(ゾル)をゲル状に変化させ、これを乾燥・熱処理して薄膜を形成する。この方法は酸化膜やコーティングの製造に有用である。
- スピンコート:液体の前駆体を基板に塗布し、高速で回転させて液体を薄く均一な層に広げるプロセス。スピンコーティングは、半導体産業で一般的に使用されている。
- ディップコーティング:液体前駆体に基板を浸し、制御された速度で引き抜いて薄膜を形成する。この方法は簡単で、大面積のコーティングに費用対効果が高い。
-
成膜プロセスフェーズ:
- 吸着:蒸着源からの原子または分子が基板表面に付着する初期段階。
- 表面拡散:吸着した原子や分子が基材表面を移動することで、膜の均一性や構造に影響を与える。
- 核生成:基材表面に小さなクラスターや核が形成され、それが成長して合体し、連続した薄膜を形成すること。
-
一般的な技術:
- 物理蒸着(PVD):真空蒸着、スパッタリング、MBEなどの方法を含む。PVDは金属、合金、セラミックの蒸着に広く使われている。
- 化学気相成長法(CVD):CVD、ALE、噴霧熱分解などの技術が含まれる。CVDは、半導体や酸化物などの高品質で均一な膜を成膜するのに適している。
-
応用例:
- 半導体:薄膜は半導体デバイスの製造において非常に重要であり、膜厚や特性の精密な制御が不可欠である。
- フレキシブル・エレクトロニクス:スピンコーティングやディップコーティングなどの技術は、フレキシブル太陽電池や有機発光ダイオード(OLED)用の薄膜を製造するために使用される。
- 光学コーティング:薄膜は反射防止コーティング、ミラー、フィルターに使用され、光学特性の精密な制御が要求されます。
-
プロセス制御と最適化:
- 素材の選択:適切なターゲット材料とプリカーサーを選択することは、所望のフィルム特性を達成するために非常に重要です。
- 蒸着パラメータ:温度、圧力、蒸着速度などの要素は、均一で高品質な膜を確保するために注意深く制御されなければならない。
- 蒸着後の処理:アニールや熱処理は、結晶性や密着性など、薄膜の特性を向上させることができる。
まとめると、薄膜製造には幅広い物理的・化学的成膜法があり、それぞれに利点と用途がある。どの方法を選択するかは、薄膜と基板の特定の要件に依存し、PVDやCVDのようなプロセスは様々な産業で広く使用されている。成膜段階を理解し、プロセスパラメーターを最適化することは、所望の特性を持つ高品質の薄膜を製造するために不可欠である。
総括表
カテゴリー | 方法 | アプリケーション |
---|---|---|
物理蒸着 | 真空蒸着, レーザーアブレーション, MBE, スパッタリング | 金属, 合金, セラミックス, 多層構造 |
化学蒸着 | CVD, 原子層エピタキシー, スプレー熱分解, ゾル-ゲル, スピンコーティング, ディップコーティング | 半導体, フレキシブルエレクトロニクス, 光学コーティング |
成膜相 | 吸着、表面拡散、核生成 | フィルムの均一性、構造、品質に影響 |
一般的な技術 | PVD (物理蒸着), CVD (化学蒸着) | 高品質で均一な薄膜を得るために産業界で広く使用されています。 |
お客様のニーズに最適な薄膜製造方法を見つけてください。 今すぐ専門家にご相談ください !