冷間加工は、金属を再結晶点以下の温度、一般的には室温で成形する金属加工プロセスである。冷間加工には、強度、表面仕上げ、寸法精度の向上など、いくつかの利点がある一方で、注目すべき欠点もある。これには、脆性につながる可能性のある材料硬度の上昇、成形性の制限、中間焼鈍工程の必要性などが含まれる。さらに、冷間加工は残留応力を引き起こし、延性を低下させ、より大きな力とエネルギーを必要とするため、特定の材料や用途には適さない。このような欠点を理解することは、特定の材料や望ましい結果に対して適切な製造工程を選択する上で極めて重要である。
キーポイントの説明
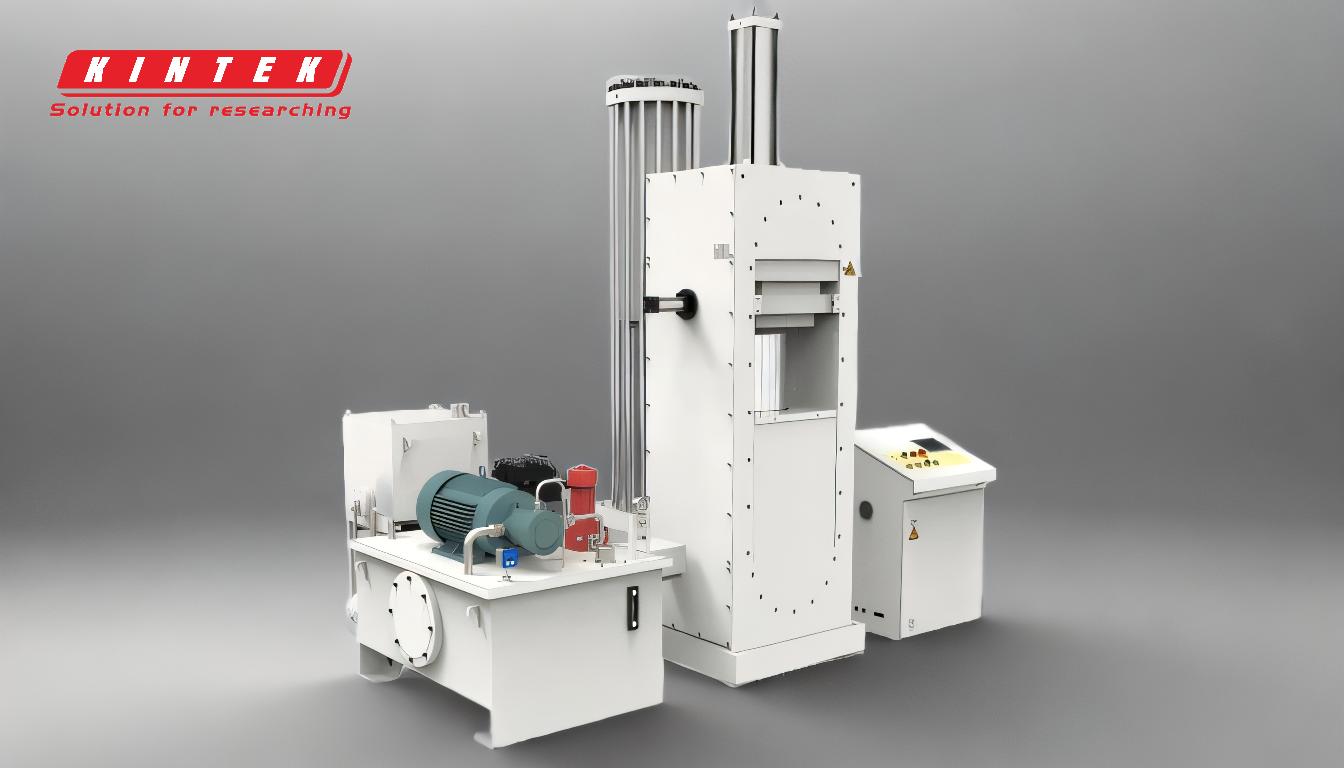
-
材料の硬度と脆さの増加
- 冷間加工は結晶構造に転位を導入することで金属を強化するが、同時に硬度を高め、延性を低下させる。
- 時間の経過とともに材料はもろくなりすぎ、応力下で割れや破損が生じやすくなる。
- この制限により、冷間加工は高い靭性や耐衝撃性を必要とする用途には不向きである。
-
成形性の制限
- 冷間加工を施すと、材料が割れずに変形を続ける 能力が低下する。
- 複雑な形状や深絞り加工では、多段階の冷間加工が必要となり、生産時間とコストが増加する。
- 高炭素鋼や特定の合金のように、延性が 低いために冷間加工が特に難しい素材もあ る。
-
残留応力
- 冷間加工は材料に内部応力を発生させ、時間の経過とともに歪みや反りを生じさせます。
- このような残留応力は、熱処理や応力除去焼鈍など、材料を安定させるための追加工程を必要とする場合があります。
- 適切な処理を行わないと、残留応力によって最終製品の構造的完全性が損なわれる可能性があります。
-
大きな力とエネルギーの必要性
- 冷間加工は、材料が低温で柔軟性を失うため、熱間加工に 比べてかなり大きな力を必要とする。
- これはエネルギー消費と工具の摩耗を増加させ、操業コストを上昇させる。
- 増大する力を処理するために特殊な装置や工具が必要になる場合もあり、さらに費用がかさむ。
-
延性の低下
- この工程では、破断せずに伸びたり変形したりする能力が低下するため、動的環境や高ストレス環境での用途が制限される可能性がある。
- 延性が低下した材料は、製造時の許容度が低くなり、欠陥やスクラップの可能性が高まります。
-
中間焼鈍の必要性
- 加工硬化の影響に対抗するため、延性を回復させ、さらなる変形を可能にする中間焼鈍が必要となることが多い。
- この追加工程は、生産時間、エネルギー使用量、コストを増加させる。
- アニーリングは、材料の特性が意図せず変化しないよう、注意深く制御されなければならない。
-
表面の欠陥
- 冷間加工は多くの場合、表面仕上げを向上させるが、傷、ひび割れ、不均一なテクスチャーなどの表面欠陥を引き起こす可能性もある。
- これらの欠陥は、二次的な仕上げ工程を必要とし、全体的なコストと複雑さを増すことがある。
-
材料の制限
- すべての材料が冷間加工に適しているわけではありません。例えば、鋳鉄やある種のセラミックのような脆性材料は、亀裂が入らずに大きな冷間変形を受けることができません。
- アルミニウムや銅のような延性材料であっても、合金組成や初期状態によっては限界があります。
-
環境と安全への懸念
- 冷間加工で必要とされる大きな力とエネルギーは、二酸化炭素排出量と環境への影響を増加させる。
- また、高い圧力と力がかかるため、作業者は安全上のリスクに直面する可能性があり、厳格な安全プロトコルと設備が必要となる。
これらのデメリットを理解することで、メーカーは、冷間加工を使用する場合や、熱間加工や鋳造などの代替工程がより適切な場合について、十分な情報を得た上で決定することができる。
総括表
デメリット | 特徴 |
---|---|
硬度と脆性の向上 | 金属を強化するが、延性が低下するため、亀裂や破損の可能性がある。 |
成形性の制限 | 割れずに変形する能力が低下し、製造時間とコストが増加する。 |
残留応力 | 内部応力の原因となり、材料を安定させるための熱処理が必要となる。 |
大きな力とエネルギー | より大きな力とエネルギーを必要とし、作業コストと工具の摩耗を増加させる。 |
延性の低下 | 材料の伸びや変形が制限され、欠陥リスクが高まる。 |
中間アニールが必要 | 延性は回復するが、時間、エネルギー、コストがかかる。 |
表面の欠陥 | 傷、ひび割れ、不均一なテクスチャーが生じることがあり、二次的な仕上げが必要。 |
材料の制限 | 鋳鉄や特定のセラミックのような脆性材料には適さない。 |
環境と安全に関する懸念 | エネルギー使用量の増加による排出量の増加。 |
適切な金属加工プロセスの選択にお困りですか? 当社の専門家に今すぐご連絡ください オーダーメイドのソリューションを