粉末冶金は、エネルギー効率、費用対効果、複雑で高精度の部品を最小限の廃棄物で製造する能力など、多くの利点を提供する汎用性の高い製造プロセスです。卓越した公差を持つ均質で均一な部品を作ることができるため、自動車や航空宇宙などの産業にとって特に有益である。しかし、サイズの制限、非常に複雑な形状の製造における課題、従来の鋳造や鍛造の方法に比べて低い強度や延性などの限界もあります。このような欠点があるにもかかわらず、粉末冶金は現代の製造業に不可欠で環境に優しい技術であり続けている。
キーポイントの説明
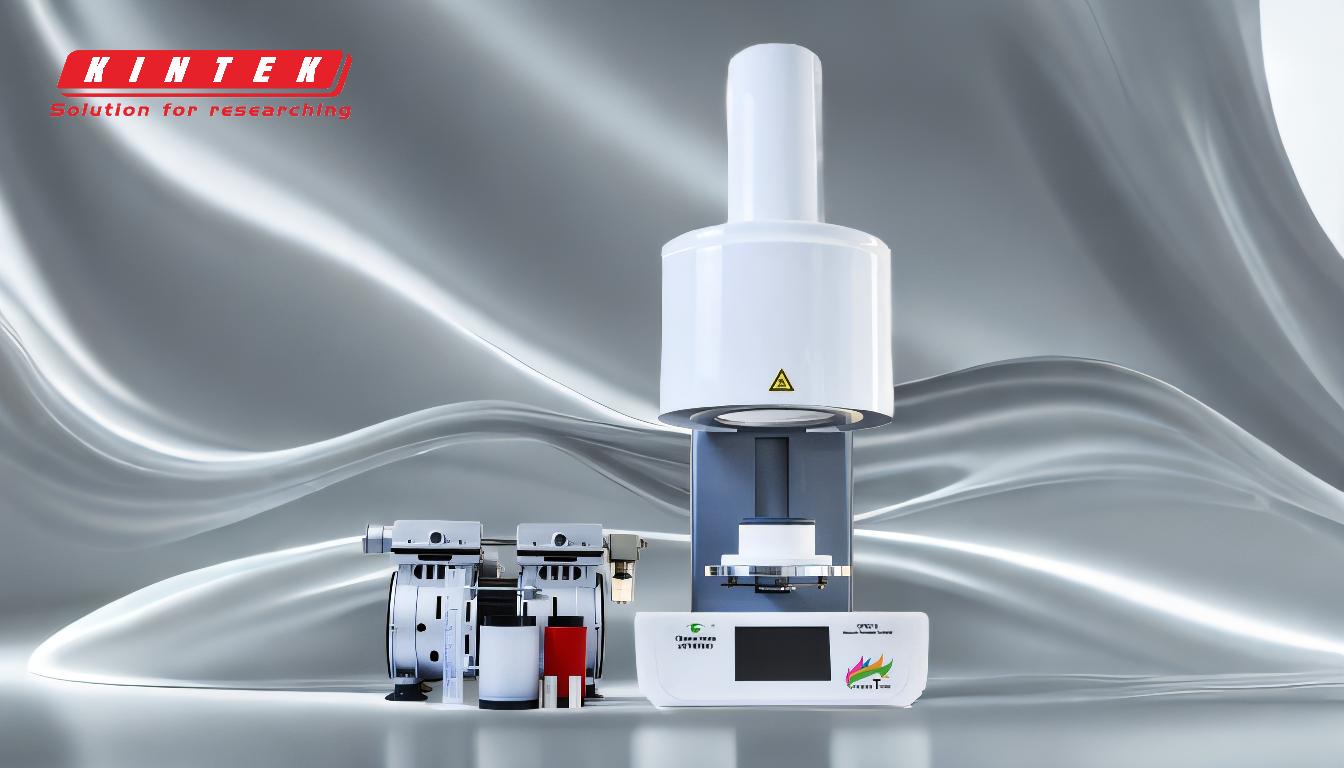
-
粉末冶金の利点:
- エネルギー効率と費用対効果:粉末冶金は、エネルギー消費と材料の無駄を削減する、短時間で効率的なプロセスです。使用された材料の約97%が最終製品の一部となり、スクラップを最小限に抑え、コストを削減します。
- 精度と均一性:このプロセスでは、非常に優れた公差を持つ均質で均一な部品を作成することができ、高精度のアプリケーションに最適です。
- 材料の柔軟性:粉末冶金は、特性を正確に制御するための材料構造の組み立てを可能にするため、高付加価値材料、特に高融点または鋳造性の悪い合金の製造に適しています。
- 環境に優しい製造:廃棄物やスクラップを最小限に抑える粉末冶金は、持続可能な生産方式に沿ったグリーン製造技術と考えられています。
-
主要産業への応用:
- 自動車と航空宇宙:軽量で耐久性があり、高精度の部品を製造できる粉末冶金は、これらの産業にとって不可欠なプロセスである。
- ハンドツール:粉末冶金で作られた工具は、耐摩耗性、靭性、硬度保持に優れ、他の方法で作られた工具の5倍も長持ちします。
-
粉末冶金の欠点:
- サイズ制限:業界最大のプレス機は約1,500トンで、実用的な部品サイズは平面面積で約40~50平方インチに制限される。
- 複雑な形状:熟練した製造業者であれば克服できる課題もあるが、非常に複雑な形状の部品を製造することは依然として難しい。
- 強度と延性:粉末冶金部品は一般に、鋳造や鍛造で製造される部品ほど強度が高くなく、延性もないため、高い機械的性能を必要とする用途では使用が制限される可能性がある。
-
将来の展望:
- 粉末冶金の精度と効率は、特に産業界が持続可能性と高性能材料を優先し続ける中で、将来の製造業にとって有望な技術となっている。近い将来、手工具製造を含め、より多くの産業がこの方法を採用することになるだろう。
要約すると、粉末冶金は効率、精度、持続可能性の点で大きな利点を提供するが、部品サイズ、複雑さ、機械的特性の点で限界もある。これらのトレードオフを理解することは、製造業者や購入者が特定の用途にこの技術を検討する際に極めて重要である。
総括表
側面 | メリット | デメリット |
---|---|---|
エネルギー効率 | エネルギー消費と材料廃棄を削減(材料利用率97%)。 | プレスサイズによる制限(最大1,500トン)。 |
精度と均一性 | 卓越した公差を持つ均質で高精度な部品を生産。 | 非常に複雑な形状の製造に挑戦。 |
材料の柔軟性 | 材料特性のコントロールが可能で、高付加価値合金に最適。 | 鋳造や鍛造に比べて強度や延性が低い。 |
環境に優しい | 廃棄物を最小限に抑え、スクラップを出さない。 | 部品サイズは~40~50平方インチに制限。 |
粉末冶金がお客様の製造工程にどのように役立つかをご覧ください。 今すぐ専門家にお問い合わせください !