押出成形は、ダイに材料を押し込むことによって、一定の断面形状を持つ成形品を作る製造工程である。プラスチック製造、食品加工、金属加工などの産業で広く使われている。このプロセスにはいくつかの重要なステップがあり、まず原料(プラスチックペレットなど)をホッパーに投入し、加熱室で溶かした後、ダイに通して最終製品を成形します。以下では、押出成形がどのように行われるのか、ステップごとに詳しく説明します。
主なポイントを説明します:
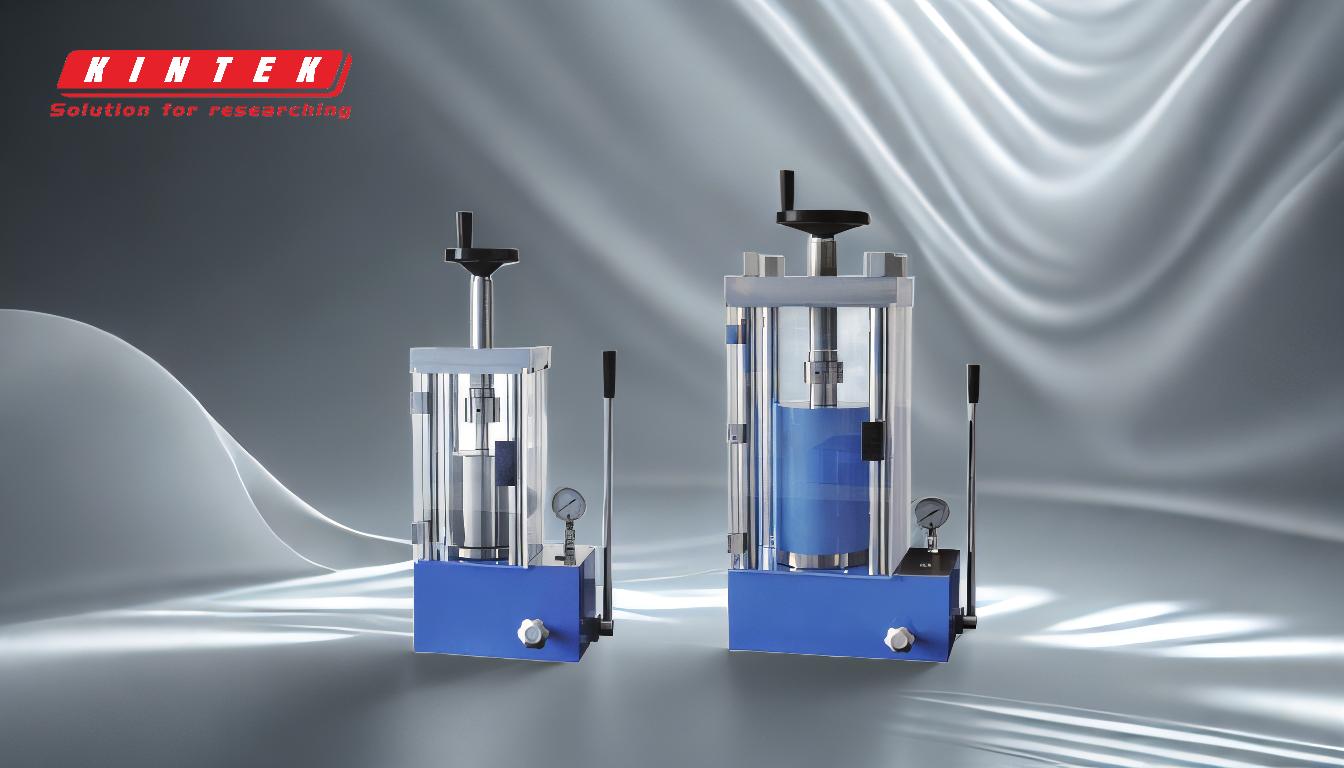
-
ホッパーへの原料投入
- プロセスは、通常ペレット、顆粒、または粉末状の原料をホッパーに供給することから始まります。
- ホッパーは貯留槽の役割を果たし、押出成形システムへの原料の安定供給を保証します。
- このステップは、均一な製品を製造するために不可欠な、安定した材料の流れを維持するために重要です。
-
加熱室への材料搬送
- ホッパーから材料は、スクリュー機構またはコンベアシステムを使って加熱チャンバーに運ばれます。
- スクリュー機構は、しばしば押出スクリューと呼ばれ、回転して材料を前方に押し出すと同時に、均一性を確保するために材料を混合します。
- このステップにより、材料が均一に分散され、溶融プロセスに備えることができます。
-
加熱室で材料を溶かす
- 材料が加熱チャンバーに到達すると、高温にさらされ、溶けて溶融状態になる。
- 加熱室には 加熱サーキュレーター エレメントと温度制御により、正確な溶解条件を維持します。
- 溶融材料がダイの中をスムーズに流れるためには、特定の粘度に達する必要があります。
-
溶融材料をダイに通す
- ダイは、溶融材料を所望の断面形状に成形する専用工具です。
- ダイは、パイプ、シート、プロファイルなどの押出製品の最終的な形状と寸法を決定します。
- 押出機のスクリューが加える圧力によって、材料がダイの中を均一に流れるようにします。
-
押出製品の冷却と固化
- 材料がダイを出ると、冷却と固化が始まり、ダイによって付与された形状が保持されます。
- 冷却は空冷で行うことができます、 冷却サーキュレーター バスなど、材料や製品の要件に応じた方法があります。
- 適切な冷却は、変形を防ぎ、製品の構造的完全性を維持するために不可欠である。
-
最終製品の切断または仕上げ
- 押し出された製品が冷えて固まったら、希望の長さに切断するか、追加の仕上げ加工を施します。
- 仕上げ加工には、用途に応じて、表面処理、印刷、組み立てなどが含まれる。
- この工程により、最終製品が要求される仕様を満たし、使用やさらなる加工が可能な状態になります。
これらのステップを踏むことで、押出成形は、安定した品質と精度で幅広い製品を効率的に生産することができます。このプロセスは適応性が高く、さまざまな素材や用途に適している。
総括表
ステップ | 内容 |
---|---|
原料の供給 | 原料(ペレット、顆粒、粉末)をホッパーに投入し、安定供給します。 |
原料の搬送 | 材料は均一性を保つため、スクリュー機構により加熱室に移動される。 |
材料の溶融 | 材料を加熱室で溶かし、適切な粘度にする。 |
ダイを通して押し出す | 溶融した材料を金型を通して押し出し、最終製品を成形する。 |
冷却と固化 | 押し出された製品は、その形状と構造的完全性を保持するために冷却されます。 |
切断または仕上げ | 最終製品は仕様に合わせて切断または仕上げされます。 |
押出成形がお客様の製造工程をどのように変えるかをご覧ください。 今すぐ専門家にお問い合わせください !