PVDコーティングプロセスの基本原理
蒸発
真空環境では、ターゲットと呼ばれる固体材料は、主に加熱を伴う様々な方法によって気体状態に変化します。蒸発として知られるこのプロセスは、物理蒸着(PVD)コーティングプロセスの基本です。この変換を達成するために、いくつかの技術が採用されています:
-
熱蒸発:この方法では、電気抵抗またはその他の加熱要素を使用して、ターゲット材料を蒸発温度まで加熱する。材料が気化点に達すると気体となり、基板上に拡散・凝縮して薄膜を形成する。
-
電子ビーム蒸着:高エネルギーの電子ビームをターゲット材料に向けて照射し、蒸発させる。この技術は、局所的な加熱効果により蒸発プロセスを正確に制御できるため、融点の高い材料に特に有効である。
-
レーザー蒸発:高エネルギーのレーザーパルスを利用して、ターゲット材料を蒸発させる方法。レーザー蒸発法は精度が高く、従来の方法では取り扱いが困難な材料の蒸発に使用できるため、複雑な薄膜材料の作製に有利である。
これらの方法にはそれぞれ独自の利点があり、使用する材料の種類や得られる膜の望ましい特性など、コーティング・プロセスの具体的な要件に基づいて選択される。
輸送
気体材料は、いったん蒸気の状態になると、真空チャンバー内で拡散を受ける。この拡散は、その後の成膜の均一性と品質に直接影響するため、PVDプロセスにおいて重要な段階です。この輸送段階には、いくつかの重要な要因が大きく影響します:
-
ガス圧力:真空チャンバー内の圧力は極めて重要な役割を果たします。圧力が低いほど拡散効率が高まり、ガス状物質が基板上に均一に広がります。逆に圧力が高いと、ガス分子間の衝突が起こり、全体的な拡散速度が低下し、膜の均一性に影響を与える可能性があります。
-
温度:真空環境内の温度も重要な変数である。温度が高いと拡散プロセスが促進されるが、基板への熱損傷や不均一な堆積物の形成を防ぐため、慎重に制御する必要がある。最適な拡散のためには、温度と他のプロセスパラメーターのバランスをとることが不可欠である。
-
基板の位置:ガス状物質の供給源に対する基板の空間的配置も重要である。適切な配置により、ガス状物質が基板の全領域に均等に到達し、局所的な過堆積や過少堆積を防ぐことができる。基板を回転させたり傾けたりする技術は、より均一な被覆を達成するのに役立つ。
まとめると、真空中でのガス状物質の輸送は、高品質の成膜を成功させるために、ガス圧、温度、基板の位置決めを綿密に制御する必要がある微妙なプロセスである。
蒸着
蒸着段階では、基板に運ばれた気体材料が冷却され凝縮し始めます。この冷却プロセスは、気体を固体薄膜に変化させ、基板表面に付着させるため、非常に重要です。成膜プロセスは単なる物理的変化ではなく、特定の用途に応じて基板の特性を大きく変化させる変革的なものでもある。
成膜時に使用されるガスの種類は、フィルムの最終的な構造と特性を決定する上で極めて重要な役割を果たす。例えば、アルゴンやヘリウムのような不活性ガスは、フィルムの純度を維持し、不要な化学反応が起こらないようにするために採用されることが多い。一方、酸素、窒素、フッ素などの反応性ガスは、酸化物、窒化物、フッ化物などの特定の化合物を生成するために導入され、特定の用途向けにフィルムの機能性を高める。
さらに、成膜チャンバー内のガスの圧力は、成膜速度と膜質の両方に影響する重要なパラメーターである。ガス圧力が低いと、一般的に緻密で均質な膜が得られ、多くの用途に望ましい。逆に、ガス圧を高くすると膜が粗くなり、密着性や反応性を高めるために表面積を増やす必要がある場合など、特定の状況では有益な場合がある。
まとめると、成膜プロセスは冷却、ガスの種類、圧力の高度な相互作用であり、各要因は所望の膜特性を達成するために細心の注意を払って制御される。この入念な調整により、出来上がった薄膜は、エレクトロニクスから光学まで、さまざまな産業で要求される厳しい基準を満たすことができるのです。
PVDプロセスの主な種類
蒸着
蒸着は、ターゲット材料を気化点まで加熱して薄膜を製造する高度な技術です。このプロセスは金属や特定の合金に特に効果的で、熱エネルギーによって固体状態から気体状態へと変化させます。気化した原子は基板上に凝縮し、均一で均一な薄膜を形成する。この方法は通常、高真空環境で行われ、衝突や汚染を最小限に抑え、蒸着膜の純度と完全性を保証する。
蒸着法の主な利点のひとつは、均一性と均一性に優れた高品質の膜を形成できることです。この技術は汎用性が高く、金属、セラミックス、半導体など、さまざまな材料を蒸着することができる。しかし、このプロセスは高真空環境を必要とし、環境要因に非常に敏感であるため、特定のシナリオでは適用が制限されることがあります。
スパッタリング蒸着
スパッタリング蒸着は高度な物理的気相成長(PVD)技術で、ターゲット材料に高エネルギー粒子(通常はプラズマからのイオン)を浴びせる。この砲撃によってターゲット材料から原子や分子が放出され、真空中を移動して基板上に凝縮し、薄膜が形成される。このプロセスは汎用性が高く、金属、酸化物、窒化物など幅広い材料に適用できる。
スパッタリング蒸着では、ターゲット材料はアルゴンイオンと電子からなるプラズマにさらされる。これらの高エネルギー粒子はターゲットから原子を「叩き落とし」、ソース原子の雲を作る。このクラウドが基板上に凝縮し、薄膜を形成する。ターゲット材料の選択とプラズマの条件は、堆積膜の特性に大きく影響する。
スパッタリング成膜の特筆すべき点として、すでに成膜された材料が、その後のイオンまたは原子砲撃によって再放出されるリスパッタリング現象がある。これは膜の均一性と膜厚に影響を与える可能性があり、望ましい結果を得るためには蒸着パラメーターを注意深く制御する必要がある。
スパッタリング成膜は、基板との密着性に優れた高品質で緻密な膜を作ることができるため、さまざまな産業で広く利用されている。スパッタリング成膜は、さまざまな材料に適用できることから特に好まれており、エレクトロニクス、光学、機械部品用の高度な薄膜の製造において汎用性の高いツールとなっている。
パルスレーザー蒸着 (PLD)
パルスレーザー蒸着(PLD)は、高エネルギーレーザーパルスを使用して真空チャンバー内でターゲット材料を蒸発させる高度な蒸着プロセスです。この方法は、特に複雑な薄膜材料の作製に長けており、様々な科学的・工業的用途で好んで使用されています。
PLDプロセスは、レーザービームが材料をターゲットにして気化させ、プラズマのプルームを形成することから始まる。このプラズマは次に基板上に堆積し、そこで凝縮して薄膜を形成する。蒸発、アブレーション、プラズマ形成、剥離を含むこのプロセスは複雑であるため、慎重に最適化する必要がある。多くの変数を管理するために必要な時間と労力は増加するものの、PLDにはいくつかの利点がある。
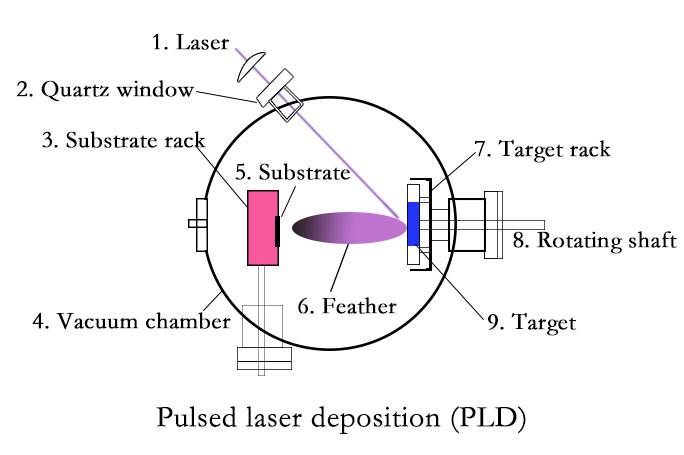
PLDの主な利点のひとつは、その高い蒸着速度であり、他の方法と比較してプロセスが大幅に合理化される。さらに、PLDではフィラメントが不要なため、メンテナンスが簡素化され、潜在的な汚染源も減少する。このためPLDは、エレクトロニクスや光学産業など、高い精度と純度が要求される用途に特に適している。
まとめると、PLDはその複雑さゆえに綿密な制御が要求されるが、高品質で複雑な薄膜を効率的に、しかも最小限のメンテナンスで製造できることから、PVDコーティング・プロセスの領域では貴重なツールとなっている。
化学気相成長法(CVD)
化学的気相成長法(CVD)は物理的気相成長法(PVD)とは基本的に異なりますが、この2つの技術を組み合わせて優れた膜特性を実現する例もあります。真空蒸着法であるCVDは、高品質・高性能の固体材料、特に半導体産業で使用される薄膜を製造することで有名です。このプロセスでは、ウェハー(基板)を1つ以上の揮発性前駆体にさらし、基板表面で反応・分解させて目的の堆積物を形成します。この方法は汎用性が高く、単結晶、多結晶、アモルファス、エピタキシャル構造など、さまざまな形態の材料を成膜できる。
蒸発やスパッタリングのような物理的プロセスに依存するPVDとは対照的に、CVDは化学反応を利用して材料を堆積させる。この化学的アプローチにより、蒸着膜の組成や特性をより細かく制御することができる。しかし、特定の用途では、CVDとPVDを相補的に使用することで、密着性の向上、機械的特性の改善、より均一なコーティングなど、より優れた特性を持つ膜を得ることができる。例えば、予備的なPVD層を使用することで、後続のCVD層に対してより受容性の高い表面を形成し、全体的な膜質を最適化することができる。
CVDとPVDの統合は、複雑な微細加工プロセスにおいて特に有益であり、化学的成膜技術と物理的成膜技術を組み合わせることで、どちらの手法も単独では対応できなかった特定の課題に対処することができる。このハイブリッド・アプローチは、成膜可能な材料の幅を広げるだけでなく、最終製品の機能性と性能を向上させる。
PVDプロセスにおけるガスの応用
不活性ガス
アルゴン(Ar)やヘリウム(He)などの不活性ガスは、キャリアガスとしてスパッタ蒸着プロセスで重要な役割を果たします。これらのガスは、化学反応を起こすことなくターゲット材料のスパッタリング効率を向上させることができるため、好まれています。この非反応性により、高品質のコーティングを実現するために不可欠な成膜の純度が維持される。
不活性ガスの使用はスパッタ蒸着に限ったことではなく、試料を劣化させる望ましくない化学反応を防止するためにも使用される。一般的に、このような望ましくない反応には酸化や加水分解が含まれ、これらは通常、空気中の酸素や水分の存在によって開始される。これらの反応性元素を不活性ガスで置換することにより、試料の完全性が保たれます。
特にアルゴンは、天然に多く存在し、比較的安価であるため、様々な用途で最も一般的に使用されている不活性ガスである。アルゴンは地球大気の約1%を占め、工業的に利用しやすい。アルゴンが最も一般的ですが、ヘリウムやネオンなどの他の希ガスも、プロセスの特定の要件に応じて使用することができます。
不活性ガス」という用語が文脈に依存することは注目に値する。希ガスはしばしば不活性とみなされるが、特定の条件下では、低い確率ではあるが反応することがある。この特性は、これらのガスの完全な価電子殻によるところが大きく、一般的に非反応性である。しかし、希ガスであっても特定の条件下では化合物を形成することがあるため、これは絶対的なルールではない。
不活性ガスの純度を指定する場合、汚染レベルを100万分の1(ppm)で示すのが一般的です。例えば、汚染レベル100ppmとは、不活性ガスの分子100万個のうち、100個が異物分子であることを意味する。蒸着膜の純度を維持する不活性ガスの有効性を確保する上で、この指標は極めて重要である。
まとめると、アルゴンやヘリウムのような不活性ガスは、材料の純度と完全性を維持することが最も重要なスパッタ蒸着やその他のプロセスにおいて不可欠である。非反応性で入手しやすいため、幅広い産業用途に最適です。
反応性ガス
反応性ガスは、PVDプロセスにおける様々な薄膜の調製において重要な役割を果たします。酸素(O₂)、窒素(N₂)、フッ素(F₂)を含むこれらのガスは、それぞれ酸化膜、窒化膜、フッ化物膜を作成するために不可欠である。これらの反応性ガスの導入は、蒸着膜において所望の化学組成や特性を得るために必要なことが多い。
例えば、酸化アルミニウム(Al₂O₃)の薄膜を作製する場合、酸素を反応ガスとして導入するのが一般的である。これにより、気相中のアルミニウム原子が酸素と反応して、安定で均一なAl₂O₃膜が形成される。反応ガスの使用は酸化アルミニウムに限らず、窒化ケイ素(Si₃N₄)や二酸化チタン(TiO₂)など他の材料にも及び、それぞれ窒素と酸素が使用される。
反応性ガスの選択とその濃度は、膜の密度、硬度、化学的安定性などの特性に大きく影響する。例えば、酸素濃度が高いほど多孔質で緻密性の低い膜になり、低いほど酸化が不完全になり、膜全体の品質に影響を与える可能性がある。
まとめると、反応性ガスの適切な使用はPVDプロセスの重要な側面であり、様々な用途に合わせた特性を持つ高性能薄膜の作成を可能にする。
有機ガス
特殊な用途では、エチレンやプロピレンなどの有機ガスが、ポリマーフィルムやコンポジットの調製に重要な役割を果たします。これらのガスは、不活性ガスや反応性ガスだけでは達成できない特定のフィルム構造の形成を促進するために、PVDプロセスに導入されることが多い。
PVDプロセスにおける有機ガスの使用は、特定の化学的官能基を必要とするポリマーフィルムの形成に特に有効である。例えば、エチレンは、優れた機械的特性と耐薬品性で知られるポリエチレンフィルムの形成に使用できる。同様にプロピレンは、耐熱性と耐薬品性に優れたポリプロピレン・フィルムの製造に利用できる。
さらに、有機ガスを他のガスと組み合わせて、有機成分と無機成分の両方の特性をブレンドした複合フィルムを作ることもできる。このハイブリッド・アプローチにより、フィルムの特性をカスタマイズすることが可能になり、エレクトロニクス、光学、機械工学などの産業における特定の用途に合わせたフィルムを作ることができる。
まとめると、PVDプロセスに有機ガスを取り入れることで、高度なポリマーフィルムや複合材料の創製に新たな可能性が開かれ、ユニークで優れた特性を持つ材料の開発が可能になる。
ガス圧力の調整
PVDプロセスにおけるガスの圧力は、成膜速度と膜質の両方を決定する極めて重要な役割を果たします。このパラメータは、ターゲットから基板に移動する際のガス状物質の挙動に直接影響します。
ガス圧が低いと、ガス状物質はより均一に拡散する傾向があり、膜の緻密化と均質性が向上する。これは、圧力が下がることでガス分子間の衝突が最小限に抑えられ、より整然とした成膜プロセスが可能になるためです。その結果、得られる膜は欠陥が少なく、より一貫した構造となる。
逆にガス圧が高いと、膜の粗さが大きくなる。このような条件下では、ガス状物質がより頻繁に衝突するため、秩序だった蒸着プロセスが乱れる可能性がある。その結果、膜の均一性が低下し、表面粗さが大きくなる可能性がある。しかし、より高い圧力は、膜質を犠牲にするものの、蒸着速度を向上させることができることは注目に値する。
ガス圧力 | 膜質 | 蒸着速度 |
---|---|---|
より低い | 緻密化と均質性の向上 | 遅い |
高い | 粗さの増加 | より速い |
最適なガス圧力は、多くの場合、アプリケーションの特定の要件によって決定され、効率的な蒸着速度に対する高品質フィルムの必要性のバランスをとります。この微妙なバランスが、最終製品で望ましい特性を達成するために重要です。
PVDコーティングプロセスの応用分野
エレクトロニクス産業
半導体デバイス、集積回路、ディスプレイの分野では、物理的気相成長(PVD)プロセスがさまざまな膜の製造において極めて重要な役割を果たしています。具体的には、PVDは導電膜、絶縁膜、光学膜の3つの主要なタイプの膜を作製するために採用されています。
導電性フィルム
導電性フィルムは、電子機器内の電流の流れを確保するために不可欠です。これらの膜は通常、アルミニウム、銅、金などの金属から作られ、熱蒸着やスパッタリングなどの技術を用いて成膜されます。金属と成膜方法の選択は、フィルムの導電性、接着性、および全体的な性能に大きく影響します。
絶縁膜
一方、絶縁膜は電気的な短絡を防ぎ、繊細な部品を保護するために極めて重要です。二酸化ケイ素(SiO₂)や窒化ケイ素(Si₃N₄)のような材料は、これらの膜を作成するために一般的に使用されます。PVDプロセスでは、膜厚と均一性を正確に制御することができ、デバイスの完全性と信頼性を維持するために不可欠です。
光学フィルム
光学フィルムは、デバイスの表面と光の相互作用を管理し、ディスプレイの鮮明度を高め、グレアを低減するように設計されています。これらのフィルムには、反射防止コーティングや透過率向上層が含まれることがよくあります。PVDプロセスでは、屈折率や透過率といった特定の光学特性を持つこれらの膜を、デバイスの要件に合わせて作成することができる。
まとめると、PVDプロセスはエレクトロニクス産業において不可欠であり、現代の電子デバイスの基本である導電膜、絶縁膜、光学膜を製造するための汎用的で精密な方法を提供している。
光学デバイス
PVD(Physical Vapor Deposition)プロセスは、様々な光学機器の性能向上に不可欠な光学コーティングの製造において重要な役割を果たしています。これらのコーティングには、反射防止コーティング、透過率向上フィルム、保護層などがあり、これらはすべて、デバイス表面と光の相互作用を最適化するように設計されています。
光学コーティングの種類
-
反射防止コーティング:光の反射を最小限に抑え、光学表面を通過する光の量を増やすように設計されたコーティングです。カメラレンズ、眼鏡、ソーラーパネルなどの用途で特に重要です。
-
透過率向上フィルム:特定の波長の光の透過率を高めるように設計されたフィルムで、光学フィルターやセンサーなどのデバイスで重要な役割を果たします。
-
保護膜:湿気、ほこり、機械的損傷などの環境要因から下地材料を保護し、光学デバイスの寿命と性能を保証します。
光学コーティングにおけるPVDの利点
- 高精度:PVDプロセスは、膜厚の精密な制御を可能にし、これは所望の光学特性を達成するために非常に重要です。
- 耐久性:PVDコーティングされた光学デバイスは、他の方法でコーティングされたものと比較して優れた耐久性を示し、様々な環境下での長期使用に最適です。
- 汎用性:PVDコーティングは、様々な光学用途のニーズに対応し、幅広いコーティングが可能です。
光学デバイスへの応用
デバイスタイプ | コーティングの目的 |
---|---|
カメラレンズ | より良いイメージングのための反射防止コーティング |
眼鏡 | 反射防止層と傷防止層 |
ソーラーパネル | 反射防止コーティングでエネルギーを最大限に取り込む |
光学フィルター | 特定の波長に対する透過率の向上 |
センサー | 安定した性能を保証する保護層 |
PVDプロセスは、これらのデバイスの機能性を向上させるだけでなく、動作寿命を延ばし、光学産業において不可欠な技術となっています。
機械部品
機械部品の表面処理の領域では、PVD(Physical Vapor Deposition)プロセスが、動作寿命と性能を向上させる上で極めて重要な役割を果たしています。PVD技術は、これらの部品の耐摩耗性、耐腐食性、耐酸化性を向上させるために採用されています。その結果、耐用年数が大幅に延長され、厳しい産業環境での信頼性と耐久性が向上します。
機械部品へのPVDの応用は、単に保護層を追加することではなく、過酷な条件に耐える表面を作り出すために、高度な材料科学を統合することです。例えば、自動車エンジン、航空宇宙タービン、産業機械などの部品は、急速な劣化につながる厳しい条件にさらされることがよくあります。PVDコーティングを施すことで、これらの部品は摩擦や化学反応、高温への暴露による摩耗や損傷から強化されます。
さらに、PVDコーティングは、さまざまな機械部品の特定の要件に合わせて調整することができます。製造部門の高精度工具であれ、医療機器の重要部品であれ、コーティングをカスタマイズできることで、それぞれの部品が固有の条件下で最適に機能することが保証されます。このレベルのカスタマイズは、ターゲット材料の種類、ガス圧、温度などの成膜パラメーターを変化させ、得られる皮膜の特性を微調整することで達成される。
まとめると、機械部品の表面処理にPVDプロセスを使用することは、その耐久性と性能を高めるための戦略的投資であり、最終的にはさまざまな産業用途の効率と信頼性に貢献する。
装飾用コーティング
PVDプロセスは、さまざまな製品の美的魅力を高める装飾膜の作成に役立っています。金属光沢と鮮やかな色彩を特徴とするこれらのフィルムは、宝飾品、時計、家庭用品などの分野で広く採用されている。このプロセスでは、フィルムの厚さと均一性を正確にコントロールすることができるため、最終製品がこれらの業界で要求される視覚的な魅力と耐久性の高い基準を満たすことができる。
宝飾品の分野では、PVDコーティングは、貴金属の外観を模倣できる洗練された仕上げを、わずかなコストで提供します。これは、豪華な外観を維持することが重要な大量生産には特に有利です。一方、時計はPVDコーティングの恩恵を受けており、見た目の美しさを高めるだけでなく、傷や腐食に強く、時計の寿命を延ばすことができます。
キッチン用品や装飾品などの家庭用品も、PVDコーティングによってモダンで洗練された外観を実現しています。コーティングにさまざまな色やパターンを取り入れることができるため、デザインの可能性が広がり、PVDは消費財製造における汎用性の高いツールとなっている。
さらに、PVDプロセスは真空条件下で行われるため環境に優しく、廃棄物を最小限に抑え、従来のコーティング方法に伴う環境への影響を軽減することができる。この持続可能性という側面は、美観と環境への責任の両方が最重要視される産業において、その魅力をさらに確固たるものにしている。
PVDプロセスの利点と課題
利点
PVDコーティングプロセスには、様々な産業で好まれるいくつかの魅力的な利点があります。最も大きな利点のひとつは高品質フィルム.これらのフィルムは密着性,均一性そして構造的完全性これらは、コーティングされた材料の性能を高めるために極めて重要である。例えば、エレクトロニクス産業では、PVDコーティングされた導電性フィルムが優れた導電性と最小限の信号損失を保証し、光学機器では、コーティングがデバイスの性能を高める正確な光学特性を提供する。
もうひとつの特筆すべき利点は環境への配慮 です。他のコーティング方法とは異なり、PVDは真空条件下で行われるため、環境への有害物質の放出を最小限に抑えることができる。このため、特に環境規制が厳しい業界では、PVDは持続可能な選択肢となります。さらに、アルゴンやヘリウムのような不活性ガスを使用することで、環境に悪影響を与える反応性の副生成物を導入することなく、膜の純度を維持することができます。
また汎用性 もPVDプロセスの重要な強みである。PVDは、金属、セラミック、ポリマーなど幅広い材料に適用できるため、多様な用途に適しています。半導体用薄膜の作成、機械部品の耐久性向上、消費者向け製品の装飾コーティングなど、PVDは特定のニーズに合わせた柔軟なソリューションを提供します。例えば、酸素や窒素のような反応性ガスを使用することで、複雑な酸化膜や窒化膜を作成することができ、可能な応用範囲がさらに広がります。
まとめると、高品質な膜の製造、環境の持続可能性、幅広い応用可能性という組み合わせにより、PVDコーティングプロセスは、さまざまな分野で非常に有利な技術となっている。
課題
PVD(Physical Vapor Deposition:物理的気相成長)プロセスに関連する主な課題のひとつは、次のような大きなものである。装置コスト.電子ビーム蒸着やパルスレーザー蒸着のような高度なPVDシステムには、高度な機械と精密な制御システムが必要であり、小規模な事業には法外なコストがかかる。さらに、これらのシステムのメンテナンスと較正には専門的な知識が必要で、全体的なコストをさらに押し上げる要因となっている。
もうひとつの重要な課題は蒸着速度.最適な蒸着速度を達成することは、効率的な生産にとって極めて重要だが、ガス圧、基板温度、使用するターゲット材料の種類など、無数の要因によって左右される可能性がある。蒸着速度が遅いと、処理時間が長くなり、運用コストが増加し、蒸着膜の品質に影響を与える可能性がある。逆に蒸着速度が速いと、密度の低下や粗さの増加など、最適とは言えない特性を持つ膜ができる可能性があります。
膜厚制御 もまた、PVDプロセスにおける重要なハードルである。基板全体で均一な膜厚を確保することは、最終製品の性能と信頼性に不可欠です。しかし、特に複雑な形状や大面積の基板を扱う場合、膜厚を正確に制御し続けることは困難です。膜厚にばらつきがあると、光学的、機械的、電気的特性など、フィルムの特性にばらつきが生じ、意図した用途に悪影響を及ぼす可能性がある。
これらの課題に対処するため、現在進行中の研究と技術的進歩は、より費用対効果の高い装置の開発、蒸着パラメーターの最適化、膜厚の制御メカニズムの改善に重点を置いている。これらの努力は、PVDプロセスの効率と信頼性を向上させ、さまざまな産業でより利用しやすく効果的なものにすることを目的としている。
無料相談はお問い合わせください
KINTEK LAB SOLUTION の製品とサービスは、世界中のお客様に認められています。弊社スタッフがどんなご質問にも喜んで対応させていただきます。無料相談にお問い合わせいただき、製品スペシャリストにご相談いただき、アプリケーションのニーズに最適なソリューションを見つけてください。