スパークプラズマ焼結炉(SPS)のご紹介
スパークプラズマ焼結炉(SPS) は、材料科学の分野における最先端技術であり、プラズマ生成にオン・オフの直流パルス電流を使用することにより、焼結へのユニークなアプローチを提供します。この包括的なガイドは、SPS技術の複雑さを掘り下げ、軸流加圧装置、水冷パンチ電極、真空チャンバーなどのコンポーネントを探求しています。SPSの主な特徴と多彩なアプリケーションを理解することで、この技術が金属やセラミックスからナノ材料や複合材料まで、さまざまな材料の迅速、効率的、高品質な焼結にどのような革命をもたらすかを理解することができます。
スパークプラズマ焼結炉の主な特徴
スパークプラズマ焼結(SPS)炉は、そのユニークな機能と迅速な処理時間により、材料科学の分野に革命をもたらしました。この炉はパルス状の直流高電流を利用して粉末成形体を加熱・焼結するもので、従来の焼結法に比べていくつかの明確な利点があります。ここでは、急速焼結、純化・活性化焼結、微粒化焼結、広範囲温度焼結、密度制御焼結、温度勾配焼結など、SPS炉の主な特徴を掘り下げる。
急速焼結
SPS炉の最も重要な利点の一つは急速焼結が可能なことです。加熱速度は500℃/分を超えることもあり、ホットプレス、熱間等方圧加圧(HIP)、無加圧焼結などの従来の方法よりも大幅に高速です。この急速な加熱速度により、焼結時間を大幅に短縮することができ、多くの場合、工程を数時間からわずか数分に短縮することができる。また、加熱・冷却速度が速いため、粗大化プロセスが最小限に抑えられ、完全緻密化後も材料固有のナノ構造を維持することができます。
精製と活性化焼結
SPS 炉は独自の純化・活性化焼結プロセスを提供します。高パルス直流電流は粒子表面の浄化効果を誘発し、吸着ガスや酸化膜を除去します。この浄化プロセスと粒子表面の活性化効果を組み合わせることで、従来は焼結が困難であった材料の焼結が可能になります。この機能は、高純度要求の材料や表面汚染に敏感な材料に特に有益です。
微粒子焼結
SPS 炉の急速な温度上昇により結晶粒成長が抑制されるため、微細構造の調整と細粒焼結体の作製が可能です。この特徴により、SPSはナノ結晶材料の調製に優れた方法となる。焼結パラメータを制御することで、研究者は所望の粒径と微細構造を達成することができ、これは材料の機械的、電気的、熱的特性を最適化するために極めて重要である。
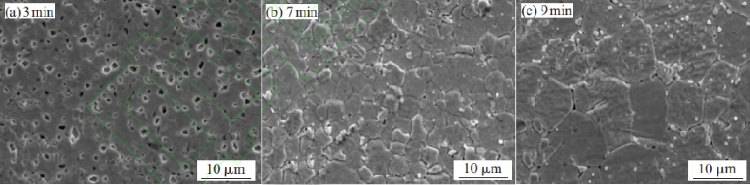
広い温度範囲での焼結
SPS炉は低温から2300℃の高温まで、幅広い温度範囲での運転が可能です。この広い温度範囲により、SPS炉はセラミック、金属、複合材料を含む様々な材料の焼結に多用途に使用できます。迅速かつ効率的に高温に到達する能力は、完全な緻密化と最適な特性を得るために高温処理を必要とする材料に特に有効です。
密度制御焼結
SPS 炉のもう一つの特筆すべき特徴は、焼結体の密度を制御できることです。多孔質体から完全高密度焼結体まで、SPS炉は柔軟な密度制御を提供します。これは印加力、ピストン移動量、電流などの焼結パラメータを調整することで達成される。密度を正確に制御することは、航空宇宙、自動車、医療産業など、特定の用途に合わせて材料の特性を調整するために不可欠です。
温度勾配焼結
SPS炉は金型内に温度勾配を作ることができ、融点の異なる材料の同時焼結を可能にします。この機能は、材料の異なる層や領域が異なる処理条件を必要とする機能的傾斜材料 (FGM) の調製に特に有用です。金型内に温度勾配(数百 °C/mm)を作り出す能力により、特性や機能性を調整した複雑な多層材料の製造が可能になります。
結論として、SPS炉は材料科学の分野で強力なツールとなる様々な先進機能を提供する。急速焼結、高純度化・活性化焼結、細粒化焼結、 広範囲温度焼結、密度制御焼結、温度勾配焼結を実現する能力により、 SPS炉は広範な用途に多用途かつ効率的に使用できる。この分野の研究開発が進むにつれ、SPS炉は高性能材料の生産においてますます重要な役割を果たすようになるでしょう。
SPSによる材料加工の多様性
スパークプラズマ焼結(SPS)は、金属、セラミックス、ナノ材料、複合材料など、幅広い材料の焼結に使用される高効率で汎用性の高い技術です。この方法は、直流パルスを利用して粒子間に火花プラズマを発生させ、急速加熱と緻密化プロセスを促進する。SPSは、従来の焼結法に比べて大きな利点があり、高品質の材料調製を実現できることで有名です。
SPSの幅広い適用範囲
ナノ材料
SPS技術は、ナノ材料の調製に特に効果的です。従来の焼結法では、ナノメータースケールの粒径を維持し、完全な密度を達成するのに苦労することがよくあります。急速加熱と短い合成時間を持つSPSは、効果的に結晶粒の粗大化を抑制します。また、この迅速なプロセスは、粉末中の欠陥や部分構造の保持を可能にし、準安定材料やナノ材料の合成に有益である。
勾配機能性材料
機能性勾配材料(FGM)は、ある方向に勾配分布を持つ複合材料であり、多くの場合、層ごとに異なる焼結温度を必要とする。化学的気相成長法(CVD)や物理的気相成長法(PVD)のような従来の方法は、コストが高く、工業生産には困難です。SPSは、耐熱性、耐摩耗性、硬度、導電性、気孔率に勾配を持つ材料の焼結を可能にし、多層を扱う能力を持つことで、これらの課題を克服しています。
電磁材料
SPSは、熱電変換素子や超電導材料、磁性材料、誘電体材料など、エレクトロニクス分野で使用される各種電磁材料の製造にも活用されています。これらの材料は、エネルギー貯蔵から生体医工学に至るまで、幅広い用途に欠かせないものです。
金属間化合物
金属間化合物は、その脆さと高融点で知られ、調製には特殊なプロセスが必要です。SPSは、粒子間の自己発熱と表面活性化を利用し、低温かつ迅速な焼結を可能にすることで、これらの化合物の効率的な調製方法を提供します。
高密度で微細なセラミックスとサーメット
SPSプロセスは、各粉末粒子内および粒子間の隙間で発生する熱を利用することで、焼結時間を大幅に短縮し、温度を下げます。このため、SPS法は、さまざまな産業用途に不可欠な高密度・微粒子のセラミックスやサーメットの作製に適した方法です。
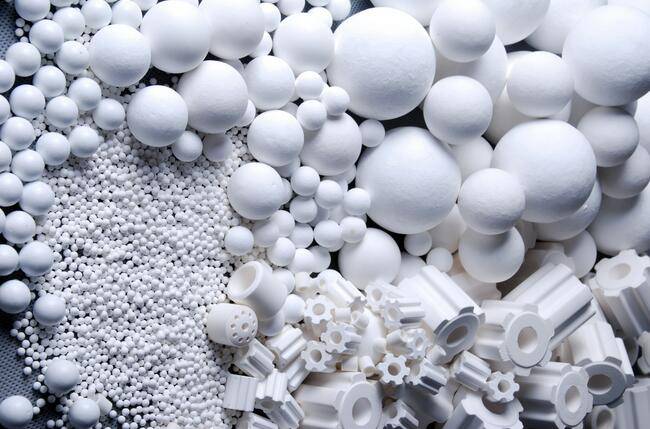
SPSの利点
- サイクルタイムの短縮 SPSは、焼結サイクルを数時間から数日に大幅に短縮し、生産性と迅速な材料開発能力を向上させます。
- 低い焼結温度: 従来のプロセスと比較して低温での焼結が可能であり、特に熱に敏感な材料に有利です。
- 高精度プロセス制御: SPSは、温度や圧力などの焼結パラメーターを細かく制御できるため、最適な結果を保証し、従来の方法では実現不可能なユニークなケミストリーの創出を可能にします。
- 汎用性: 低融点金属から超高温セラミックスまで幅広い材料の緻密化が可能で、不均一な温度分布を必要とする異種材料の接合も可能です。
SPSの応用
SPS技術は、以下のような様々な分野で応用されている:
- エネルギー貯蔵: エネルギー貯蔵:高容量リチウムイオン電池やその他の高度なエネルギー貯蔵材料。
- 生物医学工学: 薬物送達用多孔質セラミックスや組織工学用足場材。
- 先端セラミックス 高温超伝導体、高性能圧電セラミックス
- 金属間化合物 機械的、熱的、電気的特性を改善した先端合金。
- 複合材料: 機械的特性を向上させた強化セラミックスと金属。
結論として、スパークプラズマ焼結は、多様な材料の焼結のための非常に汎用性が高く効率的な方法として際立っており、プロセス制御、エネルギー効率、幅広い用途向けの高品質材料の生産能力の面で大きな利点を提供しています。
SPS炉の操作性と安全性
スパークプラズマ焼結(SPS)炉は、その高度な操作性と堅牢な安全性で知られており、様々な産業用途で好んで使用されています。これらの炉はユーザーフレンドリーなインターフェースと包括的な安全機構に重点を置いて設計されており、効率的で安全な操業を保証します。
ユーザーフレンドリーな設計と制御システム
SPS炉は操作性を向上させる最先端の制御システムを装備しています。特筆すべき特徴は、タッチスクリーンインターフェースと中央制御用プログラマブルロジックコントローラ(PLC)の統合です。このセットアップにより、オペレーターは炉のパラメーターを簡単に監視・調整できるようになり、操作の複雑さが軽減され、ヒューマンエラーの可能性が最小限に抑えられます。例えばアレン・ブラドリーのPLCシステムは、プログラミングや変更が容易なことで知られており、炉の運転管理をさらに簡素化します。
これらの炉の制御盤は標準的なNEMA 12キャビネットにすべての電気制御装置を収納するよう設計されており、NFPA 70などの安全規格への準拠を保証しています。この集中制御は安全性を高めるだけでなく、メンテナンスやトラブルシューティングを容易にします。主電源スイッチのインターロックが内蔵されているため、無許可の操作や偶発的な操作を防ぐことができ、安全性がさらに高まります。
高度な安全メカニズム
SPS炉の運転において最も重要なのは安全性であり、このシステムには幾重もの保護機能が装備されています。主な安全機能には過昇温・過昇圧誤作動アラームがあり、オペレーターに潜在的な危険をリアルタイムで知らせます。さらに、機械式自動圧力保護装置が圧力関連の問題から保護し、炉と処理材料の完全性を保証します。
炉はまた、危険な状況下での操業を防止するインターロック機能も備えています。例えば、電気や水が不足した場合、圧力が不足した場合、または温度が上昇した場合には、インターロックによって炉の運転が停止されます。このようなインターロックは、事故を防止し、装置とオペレーターの両方を保護するために極めて重要である。
遠隔操作機能も重要な安全機能のひとつで、故障診断やプログラム更新を遠隔操作で行うことができます。これにより、メンテナンスの効率が向上するだけでなく、技術者が危険な状況にさらされるリスクも軽減されます。
熱電対の統合
焼結プロセスにおいて正確な温度制御は不可欠であり、SPS炉は精密な温度監視と制御のためにタイプ「S」やタイプ「K」のような高品質の熱電対を利用しています。これらの熱電対は作業監視と調査のために適切なジャックパネルと統合され、焼結プロセスが安全で最適な温度範囲内に維持されることを保証します。
結論
要約すると、SPS炉の操作性と安全機能はシームレスで安全な焼結体験を提供するように設計されています。ユーザーフレンドリーな制御システム、高度な安全機構、精密な温度制御を備えたSPS炉は、金属、セラミック、ナノ材料などの加工における広範な用途に理想的です。最新技術と堅牢な安全プロトコルの統合により、オペレーターはリスクを最小限に抑えながら効率的に作業することができます。
SPSにおける高度な制御・監視システム
高度な制御および監視システムは、スパークプラズマ焼結(SPS)プロセスに不可欠であり、温度、圧力、電流の正確な調節を可能にするとともに、焼結パラメーターを追跡および分析するための包括的なデータ取得を可能にします。これらのシステムは、焼結材料の品質と再現性を確保するために不可欠です。
自動プログラム制御
SPSプロセスは、乾燥・粉砕された既知量の粉末試料を、焼結体の除去を容易にするグラファイトシートが敷かれた円筒形のダイに装填することから始まります。その後、ダイをSPSチャンバー内に設置し、実験に必要な特定の時間-温度プロファイルを設定します。チャンバー内の雰囲気は、真空、アルゴン、その他の制御された環境など、必要に応じて維持される。パワーはAutoモードで最大に設定され、必要な負荷がダイに加えられる。Z軸位置はゼロに設定され、SINTERを押して焼結プロセスを開始する前にタイマーが作動します。
温度測定には、SPSは2種類の機器を使用します。1000℃以下の焼結温度には熱電対を、1000℃を超える温度には高温計を使用します。グラファイト電極間に高DCパルスを流し、焼結サイクルの最初から同時に軸圧を加える。試料はジュール熱と粒子間のスパークによって加熱され、熱と物質が瞬時に移動します。焼結後、電源を切り、試料を冷却します。
コンピューター制御システム
SPSの制御システムは通常コンピュータ化されており、自動モードへの手動切り替えが可能な自動PLCフラットパネル・タッチコンピュータ制御システムを特徴としている。制御システムのソフトウェアは自社開発で、炉の状態をリアルタイムでモニターできるユーザーフレンドリーなインターフェースを提供します。このシステムは安定性と信頼性が高く、高速応答と強力な干渉防止機能を備えています。ソフトウェアにはカラーシミュレーション画面が表示され、温度表示と真空バルブ制御が統合されているため、直感的な操作が可能です。
この装置は、温度、電力、真空度、水温、気圧、焼結時間曲線など、さまざまな曲線を分析に採用することができます。これらの曲線は、過去のデータに基づいて焼結プロセスを分析するユーザーフレンドリーな方法を提供します。このシステムはUSBインターフェースを通じてExcelファイルを自動生成し、さらなる分析を行うことができます。
温度制御方式は、1700°Cまでは熱電対を使用し、1700°C以上は赤外線を使用します。システムはRS232、RS422、CAN、LAN、USBなど様々な通信インターフェースをサポートし、他の機器とのネットワーク化を容易にします。ソフトウェアの制御インターフェースは視覚化されており、ワークフローを動的に表示するため、利便性と直感性に優れています。ソフトウェアのアップグレードも生涯無料です。
コントローラーとデータ収集
他の試験室と同様、SPSは完全マニュアルから完全自動システムまで、様々なコントローラーの選択肢を提供しています。自動コントローラーは、ユーザーがプロセスのパラメーターを設定し、手順が進むにつれて、システムが圧力、温度、その他のプログラムされたファクターを調整します。これらの制御システムは、カスタマイズ可能なソフトウェアと様々なデータ収集方法で構成可能である。コントローラーの選択は、アプリケーションの重要性と真空チャンバーのサイズによって決まります。小型のチャンバーでは、ポンピングと圧力をモニターするためのシンプルなゲージが必要なだけかもしれませんが、大型のチャンバーでは、より積極的で洗練されたシステムが要求されるかもしれません。
焼結機コンポーネント
SPS装置は、一軸プレス、パンチ電極、真空チャンバー、制御された雰囲気、DCパルス発生器、位置、温度、圧力測定ユニットなど、いくつかのコンポーネントによって支援されます。焼結温度の制御は、保持時間、ランプ速度、パルス持続時間、パルス電流と電圧などのパラメーターを設定することによって達成される。直流パルス放電は、火花プラズマ、火花衝撃圧力、ジュール加熱、電界拡散効果を発生させる。SPSでは、従来のホットプレスとは異なり、直流パルス電圧のオン・オフによって焼結が補助される。圧力の印加は材料の塑性流動を助け、粒子を通る直流パルス電流の流れは詳細な図に示されている。
結論として、SPSにおける高度な制御および監視システムは、正確で再現性のある焼結結果を達成するために不可欠である。これらのシステムは、リアルタイムの調整と包括的なデータ取得を可能にし、焼結材料の品質と一貫性を保証します。コンピュータ制御、カスタマイズ可能なソフトウェア、高度なデータ収集方法の統合により、SPS技術は材料科学と工学の限界を押し広げ続けています。
材料科学におけるスパークプラズマ焼結の応用
スパークプラズマ焼結(SPS)は、材料科学の分野に革命をもたらした多用途で高度な焼結技術です。一軸圧力、パルス直流電流、急速加熱を組み合わせることで、SPSはユニークな特性と構造を持つさまざまな材料の合成を可能にします。このセクションでは、焼結、接合、成形、表面改質、固体電解質や電熱材料などの合成など、SPSの多面的な応用について掘り下げます。
先端材料の焼結
SPSは、高融点材料やナノ材料を効率的に焼結できることで特に有名です。SPS特有の急速な加熱速度(最高1000℃/分)と短い処理時間は、粉末のナノ構造を維持し、粒成長を防ぎ、ナノサイズの粒子固有の特性を維持するのに役立ちます。このため、SPSは高密度で微細なセラミックスやサーメットを製造するための理想的な方法となっている。例えば、焼結性が悪く脆いことで知られる窒化チタンは、SPSを用いることで高密度化することができ、1~5GPaの圧力下で理論値に近い密度を達成することができます。
接合と成形
焼結だけでなく、SPSは異種材料の接合や複雑な形状の成形にも使用されます。プロセス中に印加される直流電流は、材料を加熱するだけでなく、粒子間の拡散結合を促進するため、セラミックスと金属など、従来は接合が困難であった材料の接合が容易になります。この能力は、軽量で高強度な複合材料の需要が高い航空宇宙産業や自動車産業で特に有用である。
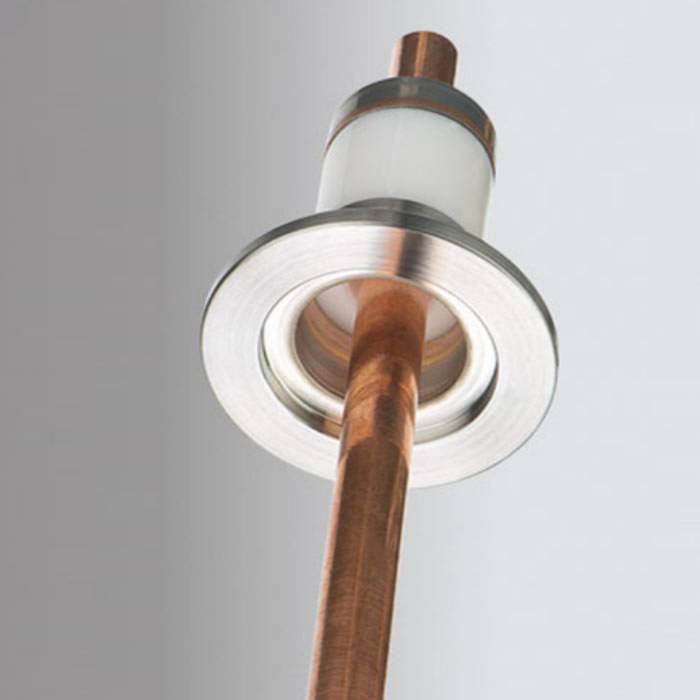
表面改質
SPSは表面改質にも利用でき、バルク特性に影響を与えることなく材料の表面特性を向上させることができます。電流密度と圧力を制御することで、特定の表面層を調整し、硬度、耐摩耗性、耐腐食性の向上などの所望の特性を得ることができます。この応用は、過酷な環境にさらされる工具材料や部品に特に有益である。
機能性材料の合成
SPSの最も重要な用途の一つは、固体電解質や電熱材料などの機能性材料の合成である。固体電解質は、固体電池や燃料電池への応用に不可欠であり、高密度化と純度が要求される。SPSは、粒界偏析が少なくイオン伝導性に優れたこれらの材料の合成を容易にします。同様に、様々な加熱用途に使用される電熱材料も、精密なSPS処理パラメータにより、熱伝導率や電気抵抗率を制御して合成することができる。
産業的意義と将来展望
SPSの産業的意義は、エネルギー消費を抑え、処理時間を短縮して高性能材料を製造できる点にある。この技術は、従来の方法では合成が困難なナノ材料、バルクアモルファス合金、傾斜機能性材料の製造に特に適している。新たな用途の発見と処理パラメーターの最適化の研究が進むにつれて、SPSは材料科学の将来において重要な役割を果たすようになり、さまざまなハイテク産業の進歩を牽引している。
結論として、スパークプラズマ焼結は、焼結や接合から表面改質、先端機能材料の合成に至るまで幅広い応用を提供する、材料科学における変革的技術として際立っている。高い効率と精度で材料を処理するその能力は、研究者にとっても産業界にとっても不可欠なツールとなっている。
SPS技術利用の課題と考察
スパークプラズマ焼結(SPS)技術は、ユニークな特性を持つ先端材料の合成を可能にすることで、材料科学の分野に革命をもたらしました。しかし、SPSの導入には、最適な焼結結果を得るために対処しなければならない独自の課題と考慮事項が伴います。このセクションでは、金型の選択とメンテナンスの重要な側面、およびSPSの効果的な運用のための広範な考慮事項について掘り下げます。
金型の選択とメンテナンス
金型材料の選択は、SPS技術において極めて重要な要素である。伝統的には、高温耐性、優れた電気・熱伝導性、化学的安定性から黒鉛が好まれてきた。しかし、グラファイト金型には、機械的強度が低い、寿命が短い、焼結材料が汚染される可能性があるなどの限界がある。これらの問題から、代替金型材料の探求が必要となっている。
最近の進歩により、超硬合金、導電性セラミックス、炭素繊維黒鉛などの代替金型材料が開発されている。これらの材料はそれぞれ独自の利点を備えているが、同時に課題も抱えている。例えば、超硬合金製の金型は強度が高いが、高温で変形しやすい。導電性セラミックは特性のバランスが取れているが、高価であることが多い。炭素繊維グラファイト金型は、グラファイトの利点と強化された機械的特性を兼ね備えていますが、損傷を防ぐために慎重な取り扱いが必要です。
金型の完全性を維持することは、安定した焼結結果を得るために極めて重要である。定期的な点検と劣化した金型の交換は、焼結プロセスにおけるばらつきを防ぐために不可欠です。さらに、金型の使用と使用の間に適切な洗浄とコンディショニングを行うことで、金型の寿命を延ばし、焼結材料の品質を維持することができます。
最適な焼結結果の達成
最適な焼結結果を得るためには、いくつかの点を考慮する必要があります。これには、適切な焼結パラメータの選択、焼結環境の制御、焼結メカニズムの理解などが含まれます。
焼結パラメーター
温度、圧力、滞留時間などの焼結パラメータは、焼結材料の最終的な特性を決定する上で重要な役割を果たします。SPSで達成可能な急速な加熱・冷却速度は、非平衡な微細構造をもたらす可能性があり、これはユニークな材料特性を得る上で有利となる。しかし、これらの速度は、過度の粒成長やその他の欠陥を防ぐために注意深く制御されなければならない。
焼結環境
雰囲気や温度勾配を含む焼結環境は、焼結プロセスに大きな影響を与える。雰囲気を制御することで、材料を劣化させる酸化やその他の化学反応を防ぐことができる。金型内の温度勾配は不均一な緻密化につながるため、焼結セットアップの慎重な設計と最適化が必要となります。
焼結メカニズムの理解
SPSの焼結メカニズムは、粒子間に火花プラズマを発生させ、急速な加熱と緻密化を促進します。しかし、このプロセスを支配する正確なメカニズムはまだ完全には解明されておらず、現在も研究が続けられています。有限要素シミュレーションは、焼結プロセスを研究するための貴重なツールとして登場し、材料内の温度分布と電場分布に関する洞察を提供している。
今後の方向性
SPS技術の継続的な改善には、継続的な研究開発が必要である。今後の主な研究分野としては、特性を向上させた新しい金型材料の開発、高度なシミュレーション技術による焼結パラメータの最適化、焼結メカニズムのより深い理解などが挙げられる。
結論として、SPS技術は先端材料の合成に大きな利点を提供する一方で、最適な結果を得るために対処しなければならないいくつかの課題や考慮事項も存在する。金型を注意深く選択・維持し、焼結パラメータを制御し、焼結メカニズムの理解を進めることで、SPS技術で可能なことの限界を押し広げ続けることができる。
SPS技術の今後の動向と革新
スパークプラズマ焼結(SPS)技術は、その迅速な焼結能力で知られ、ユニークな特性を持つ高品質の材料を製造する能力により、材料科学の分野で注目されてきました。研究が進化を続ける中、いくつかのトレンドとイノベーションが生まれつつあり、SPS技術の効率向上、応用範囲の拡大、安全性の向上が期待されている。
工業化と大量生産
SPS技術の最も重要なトレンドの一つは、工業化への移行である。従来の焼結法と比較して、SPSはエネルギーと時間の節約、生産効率の向上、製品性能の優れた制御という点で大きな利点を提供する。日本のような国々は、主に磁性材料、硬質合金、傾斜機能材料の生産において、すでにSPSの工業的応用を達成している。例えば、日本の太田精機は、SPSを用いて100%WCの超硬材料の大量生産に成功し、世界40社以上のメーカーに供給している。対照的に、中国など他地域のSPS技術は、新素材の調製とプロセス研究に重点を置いた実験室での研究段階にとどまっている。
焼結形状の多様化
現在、SPSは、焼結機構と黒鉛鋳型の制約から、単純な円筒形サンプルの製造に限られている。しかし、より複雑な形状や構造を作り出すために、SPS技術を開発する傾向が高まっている。この進歩は、様々なエンジニアリング分野におけるSPSの適用性を大幅に拡大し、現在では実現不可能な複雑な部品の製造を可能にするだろう。
材料合成と接続
SPS技術はバルク材料の焼結だけでなく、特に従来の方法では入手が困難な粉末の合成にも利用されている。例えば、SPSは超高温ZrC材料粉末の合成に利用され、高純度と約100nmの微細粒径を達成している。さらにSPSは、セラミック-セラミック接合やセラミック-金属接合などの材料接合(溶接)にも応用が検討されている。SPSの電場によって強化された自己拡散により、中間層を介さずに材料を接続することができるため、堅牢で耐久性のある複合構造を作るための新たな可能性が開かれる。
焼結金型の性能最適化
黒鉛は、その高温耐性と優れた電気・熱伝導性によりSPSで一般的に使用されているが、強度が低く、焼結材料が汚染される可能性があるなどの制約がある。より高い強度、再利用性、汚染の低減を提供する新しい金型材料を開発する傾向がある。超硬金型、導電性セラミック金型、炭素繊維グラファイト金型などの材料が研究されていますが、高温での変形や高コストなどの課題が残っています。
シミュレーションとモデリングの進歩
SPSの複雑な焼結プロセスを理解することは、そのパラメータを最適化し、結果を予測する上で極めて重要である。有限要素シミュレーションはこの点で貴重なツールとして登場し、研究者は焼結中の温度分布や電場分布を解析できるようになった。ABAQUS、MATLAB、MSC.MARCのようなソフトウェアが焼結プロセスのシミュレーションに使用され、様々なパラメータの影響に関する洞察を提供し、製造の理論的指導に役立っています。
強化された安全機能
SPS技術が進化し続けるにつれ、その安全機能の強化にますます焦点が当てられている。これには、より安全な操作プロトコルの開発、SPS装置の信頼性の向上、安全性を損なうことなく技術をより幅広い環境で使用できるようにすることなどが含まれる。
結論としてSPS技術の将来は、効率の改善、材料用途の拡大、安全機能の強化を目指した研究開発が進行中であり、有望である。これらの進歩は、材料科学の分野に革命をもたらし、以前は実現不可能であった高性能材料や部品の製造を可能にする。SPS技術が成熟し続けるにつれ、製造と材料革新の未来を形作る上で極めて重要な役割を果たすことは間違いない。
無料相談はお問い合わせください
KINTEK LAB SOLUTION の製品とサービスは、世界中のお客様に認められています。弊社スタッフがどんなご質問にも喜んで対応させていただきます。無料相談にお問い合わせいただき、製品スペシャリストにご相談いただき、アプリケーションのニーズに最適なソリューションを見つけてください。