冷間加工と熱間加工は2つの基本的な金属成形プロセスであり、それぞれに明確な利点と欠点がある。金属の再結晶温度以下で行われる冷間加工は、この温度以上で行われる熱間加工に比べ、いくつかの利点がある。これらの利点には、機械的特性の向上、表面仕上げの改善、寸法公差の厳格化、材料の無駄の削減などが含まれる。しかし、冷間加工には、変形抵抗性の向上や、場合によっては中間焼鈍の必要性などの限界もある。これらのプロセスの違いを理解することは、特定の用途に適した方法を選択するのに役立ちます。
主なポイントの説明
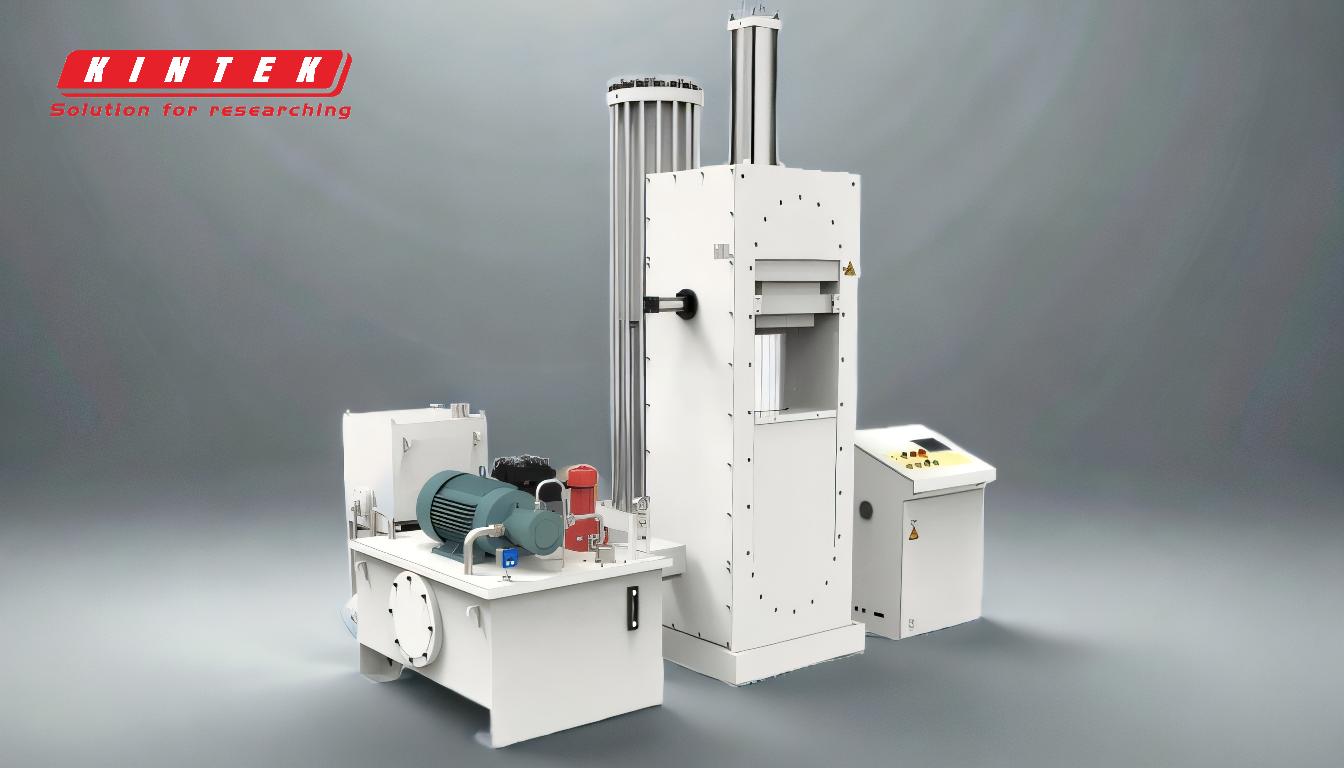
-
機械的特性の向上:
- 冷間加工は、ひずみ硬化によって強度や硬度といった金属の機械的特性を向上させる。この過程では金属原子が転位し、さらなる変形に対する抵抗力が増す。
- 一方、熱間加工は、金属が加工中に再結晶化し、ひずみ硬化の効果がなくなるため、機械的特性を著しく向上させることはない。
-
より良い表面仕上げ:
- 冷間加工は熱間加工に比べ、より滑らかで精密な表面仕上げが可能です。冷間加工では、熱間加工でよく見られる酸化やスケールの形成が避けられるからです。
- また、冷間加工では高温にならないため、表面欠陥のリスクも低減され、高品質な仕上げを必要とする用途に最適です。
-
より厳しい寸法公差:
- 冷間加工では、加工中に金属が大きく膨張したり収縮したりしないため、より厳密な寸法管理が可能になります。この精度は、寸法要求の厳しい部品の製造には極めて重要である。
- 熱間加工では、熱膨張や熱収縮のため、寸法精度が低くなることが多く、追加の機械加工や仕上げ工程が必要になります。
-
材料廃棄の削減:
- 冷間加工は、酸化やスケーリングの原因となる高温を伴わないため、材料の無駄を最小限に抑えることができる。この効率は、高価な材料や希少な材料に特に有益である。
- 熱間加工は、大きな変形を生じさせることができる反面、酸化やスケーリングによる材料ロスを生じることが多く、全体的な生産コストを増加させる。
-
冷間加工の限界:
- その利点にもかかわらず、冷間加工には、より強力な設備が必要となる高い変形抵抗などの限界がある。さらに、金属によっては、延性を回復させ、割れを防止するために、中間焼鈍を必要とする場合がある。
- 熱間加工は、精度は劣るが、大きな変形を 必要とする大型部品や複雑な部品の成形に適して いる。
まとめると、高強度、高精度、高表面品質を必要と する用途では、熱間加工よりも冷間加工の方が好まれ ることが多い。しかし、どちらの加工法を選択するかは、材 料特性、希望寸法、生産上の制約など、用途に特 有の要件によって決まる。
総括表
側面 | 冷間加工 | 熱間加工 |
---|---|---|
機械的性質 | ひずみ硬化により強度と硬度を高める。 | 再結晶による機械的性質の大幅な向上はない。 |
表面仕上げ | より滑らかで精度が高く、酸化やスケールを避けることができる。 | 酸化やスケールが発生しやすく、仕上がりが粗くなる。 |
寸法公差 | 伸縮を最小限に抑え、より厳密に管理。 | 熱膨張や熱収縮による精度の低下。 |
材料の無駄 | 酸化やスケールがなく、廃棄物が減少。 | 酸化やスケーリングによる廃棄物の増加。 |
制限事項 | 変形抵抗が高いが、中間焼鈍が必要な場合がある。 | 大きな変形を必要とする大型部品や複雑な部品に適しています。 |
お客様の用途に適した金属成形プロセスの選択にお困りですか? 今すぐ専門家にお問い合わせください !