標準的なメッキの厚さは 0.0005インチ~0.0015インチ(0.012mm~0.038mm)です。 の厚みがあります。この厚さ範囲は、耐久性、機能性、費用対効果のバランスを考慮して選択されることが多い。さらに、めっきの硬度は、以下の間で変化します。 48~52ロックウェルC で熱処理すると 約750°F(400℃)で で1時間加熱すると、硬度は 58 から 64 ロックウェルC .この熱処理工程は、めっきの機械的特性を向上させ、要求の厳しい用途に適しています。
主要ポイントの説明
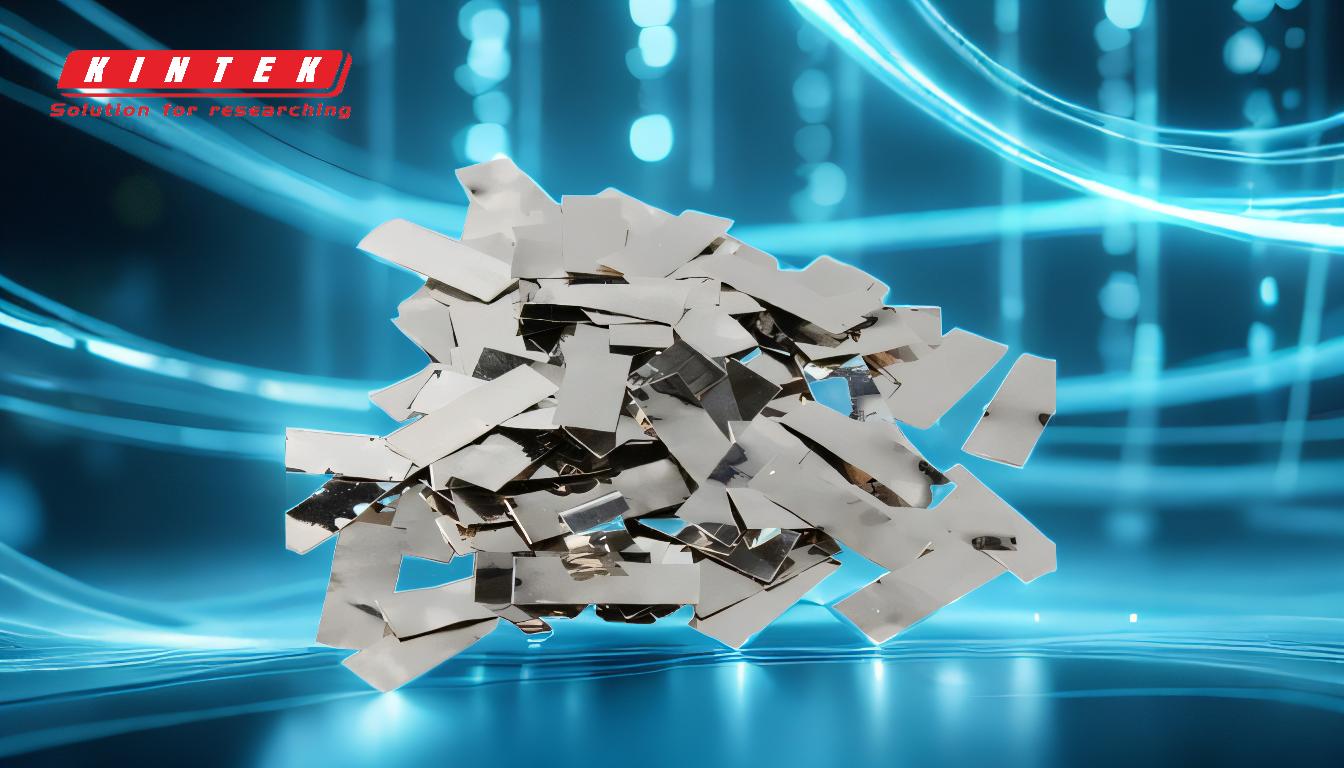
-
標準板厚範囲:
- エンジニアリング用途での一般的なめっき厚は 0.0005インチ~0.0015インチ(0.012mm~0.038mm) .この範囲は、ほとんどの工業用途に十分な保護と性能を提供するため、広く受け入れられている。
- より薄いコーティング(0.0005インチに近い)は、最小限の材料添加が必要な用途によく使用され、より厚いコーティング(0.0015インチまで)は、より要求の厳しい環境に選択されます。
-
メッキの硬度:
- メッキ材料の硬度は、通常、以下の範囲にある。 48から52ロックウェルC である。このレベルの硬度は、多くの汎用用途には十分である。
- 硬度は、機械的応力を受ける部品に不可欠な耐摩耗性、耐磨耗性、耐変形性を決定するため、非常に重要な要素です。
-
熱処理と硬度向上:
- で熱処理した場合。 750°F (400°C) で1時間加熱すると、その硬度は 58 から 64 ロックウェルC .
- 熱処理は、めっきの微細構造を変化させ、硬度、耐摩耗性、耐久性などの機械的特性を向上させる。このため、高応力や高温環境など、より厳しい使用条件に適している。
-
アプリケーション:
-
メッキの厚さと硬さの選択は、特定のアプリケーションの要件に依存します。例えば
- より薄いコーティング は、寸法精度が重要な電子機器や精密部品によく使用されます。
- より厚いコーティング は、過酷な条件にさらされる重機や自動車部品に適しています。
- 熱処理めっきは、切削工具や産業機器など、耐摩耗性の強化が必要な用途に最適です。
-
メッキの厚さと硬さの選択は、特定のアプリケーションの要件に依存します。例えば
-
コストと性能のトレードオフ:
- メッキと熱処理を厚くすると、材料費と加工費が増加する。従って、めっきの厚さと硬さの選択は、性能要件と予算制約のバランスをとる必要がある。
- コスト重視の用途では、標準的な厚さの無処理めっきで十分かもしれないが、高性能の用途では、熱処理による追加費用が正当化されるかもしれない。
これらの重要なポイントを理解することで、装置や消耗品の購入者は、特定のニーズを満たすめっき仕様について、十分な情報に基づいた決定を行うことができる。
要約表
パラメータ | 詳細 |
---|---|
標準厚さ | 0.0005インチ~0.0015インチ(0.012mm~0.038mm) |
未処理硬度 | 48~52ロックウェルC |
熱処理硬度 | 58~64ロックウェルC(750°F/400°C、1時間の熱処理後) |
用途 | 電子部品、精密部品、重機、自動車部品 |
コストに関する考察 | より厚いメッキと熱処理はコストを増加させますが、性能を向上させます。 |
お客様の用途に適したメッキの選択にお困りですか? 当社の専門家に今すぐご連絡ください オーダーメイドのソリューションを