熱蒸着は、基板上に薄膜を形成するために広く使用されている物理蒸着(PVD)技術である。このプロセスでは、真空チャンバー内でターゲット材料が蒸発するまで加熱し、蒸気を形成して真空中を移動させ、基板上に堆積させて薄膜を形成する。熱源は抵抗加熱(ボートやコイルを使用)または電子ビーム加熱である。この方法は、その簡便さ、高純度膜の製造能力、強力な接着特性から好まれている。エレクトロニクス、光学、コーティングなどの産業で、金属、合金、その他の安定した材料を蒸着するために一般的に使用されている。
キーポイントの説明
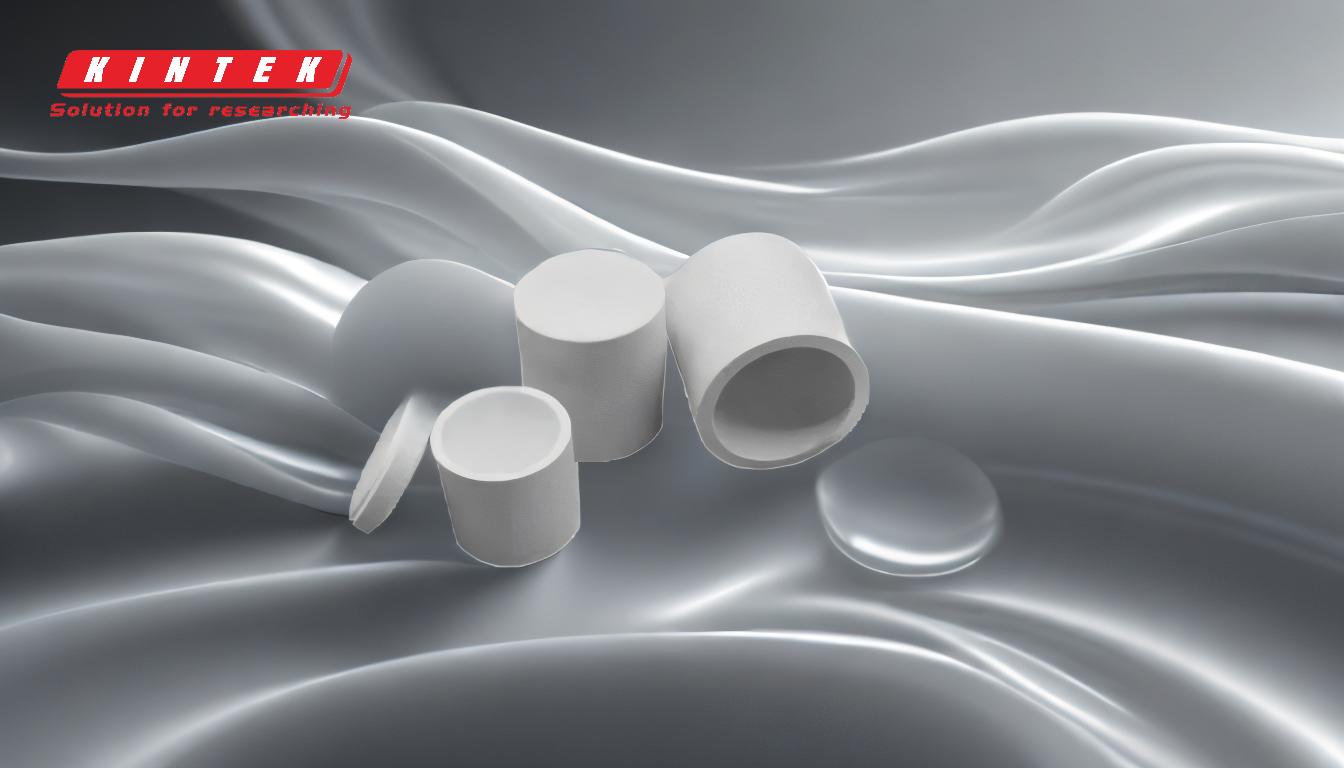
-
真空環境:
- 熱蒸発は高真空チャンバー内で行われ、コンタミネーションを最小限に抑え、効率的な蒸気の移動を保証します。
- 真空は、空気分子の存在を減少させ、不要な反応を防止し、気化した材料が基板に直接移動することを確実にします。
-
加熱メカニズム:
- 抵抗加熱(ボート、コイル、バスケット経由)または電子ビーム加熱のいずれかを使用してターゲット材料を加熱する。
- 抵抗加熱では、電流が耐火性金属エレメントを通過し、熱を発生させて材料を溶かし蒸発させる。
- 電子ビーム加熱では、集束した高エネルギー電子ビームを使用して、材料を直接加熱して蒸発させます。
-
蒸発プロセス:
- 材料は蒸発点まで加熱され、そこで固体または液体から蒸気に変化する。
- 真空チャンバー内で発生する蒸気圧により、材料は蒸気雲を形成する。
-
蒸気の移動と蒸着:
- 気化した材料は、空気抵抗がないため、真空チャンバー内を直線的に移動する。
- 蒸気は基板上に凝縮し、密着性と純度の高い薄膜を形成する。
-
基板コーティング:
- 均一なコーティングを確実にするため、基板は蒸発源の上または近くに配置される。
- 得られる膜厚と均一性は、材料特性、蒸発速度、基板の位置などの要因に依存します。
-
応用例:
- 熱蒸着は、エレクトロニクス(金属接点および相互接続用)、光学(反射および反射防止コーティング用)、装飾コーティングなどの産業で使用されている。
- 特に金属(アルミニウム、金、銀など)や合金の蒸着に適しています。
-
利点:
- 真空環境による成膜の高純度化。
- 基板への膜の強固な密着性。
- 他のPVD技術に比べてシンプルでコスト効率が高い。
-
制限事項:
- 分解せずに気化できる材料に限る。
- 融点が非常に高い材料や複雑な組成の材料には適さない場合がある。
これらの原則に従うことで、熱蒸発法は、厚さと組成を正確に制御しながら薄膜を蒸着するための、信頼性が高く効率的な方法を提供する。
要約表
主な側面 | 詳細 |
---|---|
真空環境 | 高真空はコンタミネーションを最小限に抑え、効率的な蒸気の移動を保証します。 |
加熱メカニズム | 抵抗加熱(ボート/コイル)または電子ビーム加熱。 |
蒸発プロセス | 加熱された材料が気化し、真空チャンバー内に蒸気雲が形成される。 |
蒸着 | 蒸気は直線的に移動し、基板上に凝縮する。 |
用途 | エレクトロニクス、光学、装飾コーティング(アルミニウム、金、銀など)。 |
利点 | 高純度、強力な接着力、コストパフォーマンス |
制限事項 | 分解せずに気化する材料に限定されます。 |
薄膜のニーズに対する熱蒸着にご興味がおありですか? 今すぐご連絡ください までご連絡ください!