インジウム・スズ酸化物(ITO)の成膜には、化学的手法と物理的手法があり、それぞれ用途に応じて独自の利点があります。化学的手法には、化学気相成長法(CVD)、プラズマエンハンストCVD(PECVD)、原子層堆積法(ALD)などがあり、これらは膜特性の精度と制御で知られています。物理蒸着(PVD)を中心とする物理的手法には、スパッタリング、熱蒸着、電子ビーム蒸着、パルスレーザー蒸着(PLD)などがあり、高品質で均一な膜を作ることができるため、広く利用されている。これらの方法は、基板の種類、希望する膜の特性、特定のアプリケーションのニーズなどの要因に基づいて選択される。
キーポイントの説明
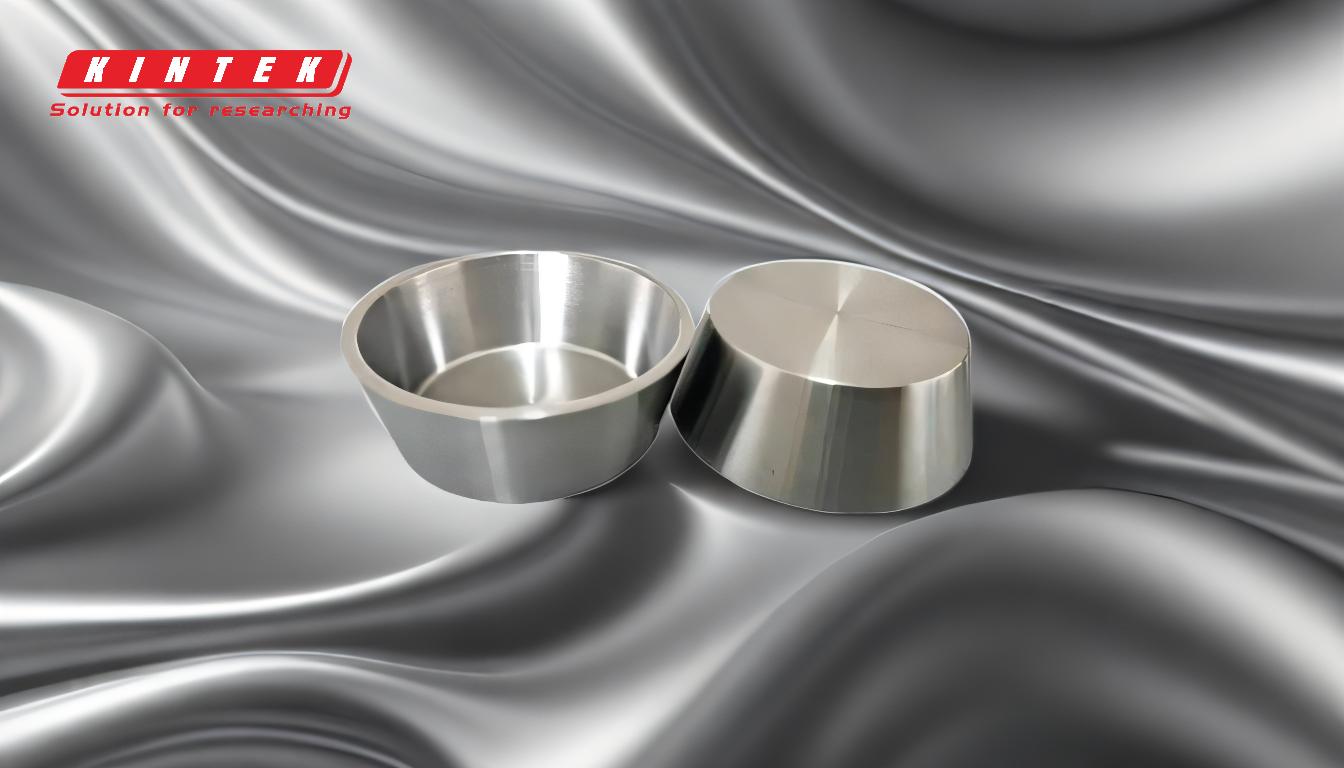
-
化学蒸着法:
- 化学気相成長法 (CVD):気体状の前駆体を化学反応させ、基板上に固体膜を形成する方法。優れた電気的・光学的特性を持つ、高純度で均一なITO膜の製造に高い効果を発揮する。
- プラズマエンハンスドCVD(PECVD):PECVDはプラズマを使って化学反応速度を高め、低温での成膜を可能にする。これは特に温度に敏感な基板に有効である。
- 原子層蒸着 (ALD):ALDは膜厚と組成を原子レベルで制御できるため、超薄膜でコンフォーマルなITOコーティングを必要とする用途に最適です。
-
物理蒸着法:
- スパッタリング:ITO成膜の最も一般的な方法のひとつ。ターゲット材料にイオンをぶつけて原子を放出させ、基板上に堆積させる。スパッタリングは、密着性に優れた緻密で均一な膜を作ることができるため好まれている。
- 熱蒸着:この方法では、ITO材料を真空中で蒸発点まで加熱し、蒸気を基板上に凝縮させる。シンプルでコスト効率が高いが、スパッタリングと同レベルの均一性が得られない場合がある。
- 電子ビーム蒸着:この技術では、電子ビームを使用してITO材料を加熱・蒸発させるため、蒸着速度が速く、膜厚を正確に制御できる。
- パルスレーザー蒸着(PLD):PLDは、高出力レーザーパルスを使用してターゲットから材料をアブレーションし、基板上に堆積させる。PLDは、複雑な組成を持つ高品質の膜を製造することで知られている。
-
成膜方法の選択基準:
- 基板適合性:どの方法を選択するかは、基板材料(シリコン、ガラスなど)とその熱的・化学的安定性に依存する。
- フィルム特性:厚さ、均一性、導電性、光学的透明性などの望ましい特性は、成膜技術の選択に影響する。
- 適用要件:タッチスクリーン、太陽電池、ディスプレイなどの特定の用途では、成膜方法の選択を導くような特定の膜特性が要求されることがある。
-
利点と限界:
- 化学的方法:フィルムの組成や特性のコントロールに優れているが、より高い温度と複雑な装置を必要とする場合がある。
- 物理的方法:一般的にシンプルで汎用性が高いが、均一な膜厚の達成や原子レベルでの膜組成の制御が難しい場合がある。
これらの方法とそれぞれの利点を理解することで、装置や消耗品の購入者は、それぞれのニーズや用途に合わせた、十分な情報に基づいた決定を下すことができる。
要約表
蒸着方法 | 主な特徴 | 用途 |
---|---|---|
化学蒸着(CVD) | 高純度で均一な膜、優れた電気・光学特性 | 精密用途向け高品質ITO膜 |
プラズマエンハンスドCVD (PECVD) | 低温成膜、高感度基板に最適 | 温度に敏感なアプリケーション |
原子層蒸着 (ALD) | 原子レベルの制御、超薄膜、コンフォーマルコーティング | 先端用途向け超薄膜ITO層 |
スパッタリング | 緻密で均一な膜、良好な密着性 | ディスプレイ・タッチパネル用高性能ITO膜 |
熱蒸着 | シンプルでコスト効率に優れ、適度な均一性 | 予算に優しいITO蒸着 |
電子ビーム蒸着 | 高い蒸着速度、精密な膜厚制御 | 高精度で迅速なITO蒸着 |
パルスレーザー堆積法(PLD) | 高品質膜、複雑な組成 | 特殊用途向け高性能ITO膜 |
お客様のアプリケーションに最適なITO成膜方法の選択にお困りですか? 当社の専門家に今すぐご連絡ください オーダーメイドのソリューションを