熱間成形と冷間成形は 2 つの異なる製造プロセスであり、それぞれに独自の長所と短所があります。熱間成形では材料を高温に加熱して展性を高めますが、冷間成形では材料を室温または室温付近で成形し、多くの場合、より強力で耐久性のある製品が得られます。これらの方法の選択は、材料特性、必要な製品特性、生産効率など、用途の特定の要件によって異なります。
重要なポイントの説明:
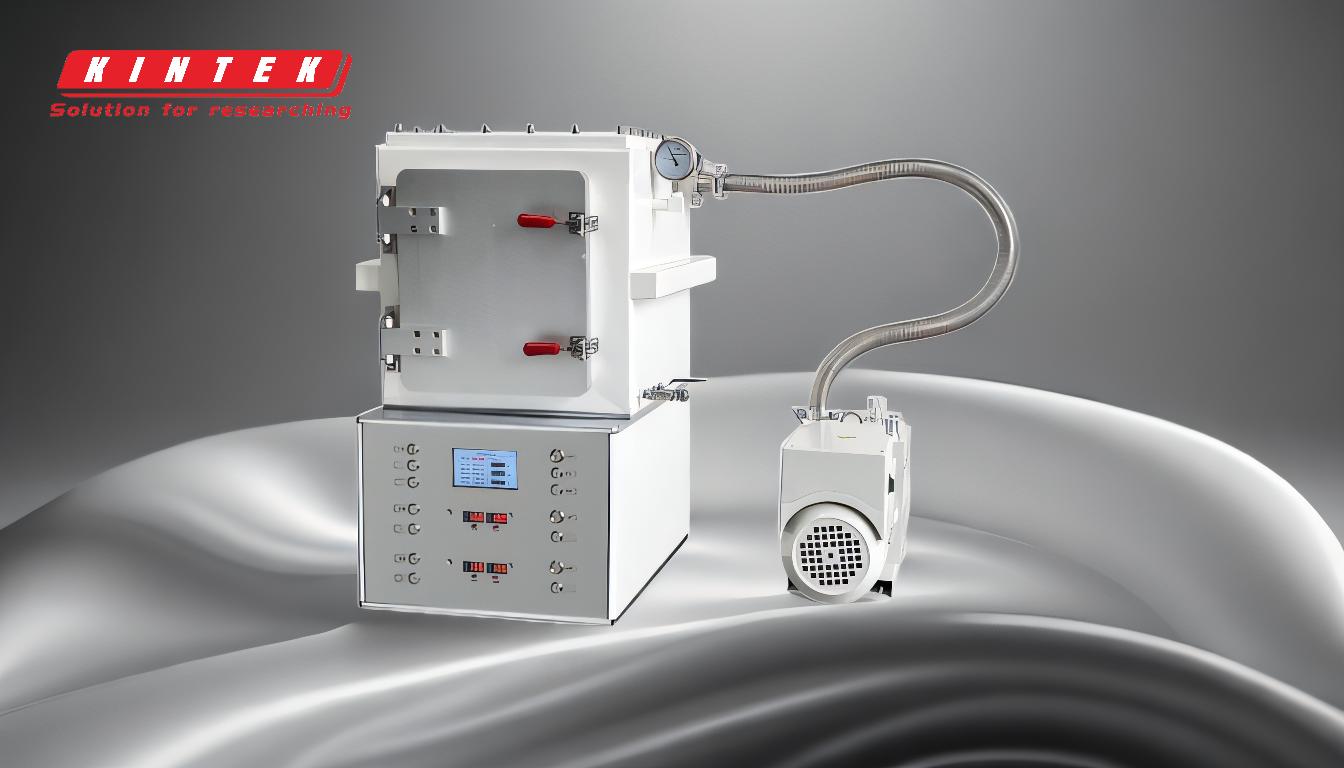
-
熱間成形の利点:
- 展性の向上: 材料を加熱すると降伏強度が低下し、割れることなく複雑な形状に成形しやすくなります。
- より低い力の要件: 加熱された材料の強度が低下するということは、成形プロセス中に必要な力が少なくなることを意味し、成形装置の寿命を延ばすことができます。
- 強化された焼結活動: ダイレクトホットプレスなどのプロセスでは、高温により微細な金属粉末がより効果的に焼結され、材料特性の向上につながります。
-
熱間成形の欠点:
- エネルギー消費量: 材料を高温に加熱する必要があると、大量のエネルギー消費が発生し、全体の生産コストが増加する可能性があります。
- 材料の制限: 一部の材料は高温で劣化したり、望ましくない相変化を起こしたりする可能性があるため、すべての材料が熱間成形に適しているわけではありません。
- 寸法管理: 高温により材料が膨張する可能性があり、正確な寸法公差を維持することがより困難になります。
-
冷間成形の利点:
- 強度と耐久性の向上: 冷間成形では加工硬化が起こり、最終製品の強度と耐久性が向上します。
- より良い表面仕上げ: 冷間成形では加熱が行われないため、製品の表面仕上げはより滑らかでより安定したものになることがよくあります。
- エネルギー効率: 冷間成形プロセスは、材料を加熱する必要がないため、通常、熱間成形に比べて必要なエネルギーが少なくなります。
-
冷間成形の欠点:
- より高い力の要件: 冷間成形では、材料を成形するためにより多くの力が必要となるため、成形装置の磨耗が増加する可能性があります。
- 限定された複雑さ: 冷間成形は、材料が低温では展性が低くなるため、一般に複雑な形状の作成にはあまり適していません。
- 材料の制限: 材料によっては、室温では脆くなりすぎたり、成形が困難になったりする場合があり、冷間成形の適用が制限されます。
-
アプリケーションと業界での使用:
- 熱間成形: 望ましい材料特性を達成するために高温が必要な、家具製造、木製ドア工場、木質パネル加工などの業界で一般的に使用されています。
- 冷間成形: 家具製造、木材産業、装飾、プラスチック、その他の産業において、強度と表面仕上げが重要な高品質部品の製造に使用されています。
要約すると、熱間成形と冷間成形のどちらを選択するかは、材料特性、必要な製品特性、生産効率など、用途の特定の要件によって異なります。各方法には独自の長所と短所があり、これらを理解することは、特定の用途に最適な成形プロセスを選択するのに役立ちます。
概要表:
側面 | 熱間成形 | 冷間成形 |
---|---|---|
展性 | 高 (複雑な形状の成形が容易) | 低い (複雑な形状にはあまり適さない) |
力の要件 | 必要な力が少なくなり、機器の摩耗が軽減されます | より大きな力が必要となり、機器の磨耗が増加します |
エネルギー効率 | 暖房によるエネルギー効率の低下 | よりエネルギー効率が高い(加熱が不要) |
材料の適合性 | 高温に耐えられる材質に限定される | 常温でも脆化しない材質に限る |
表面仕上げ | 滑らかにするために後処理が必要な場合があります | より滑らかでより一貫した表面仕上げ |
アプリケーション | 家具製造、木製ドア、木質パネル | 家具製造、木材産業、装飾、プラスチック |
用途に適した成形プロセスの選択にサポートが必要ですか? 今すぐ専門家にお問い合わせください !