真空成膜技術の歴史的発展
初期の課題とCVD技術
真空コーティング技術は、1960年代にCVD(Chemical Vapor Deposition:化学気相成長法)の登場によって、最初の大きな一歩を踏み出した。この先駆的な技術は当時画期的であったが、課題がないわけではなかった。最も大きなハードルのひとつは、高温を必要とすることで、効果的にコーティングできる基材の種類が限られていた。CVDプロセスの高い熱需要は、熱安定性の高い材料のみが成膜条件に耐えられることを意味し、潜在的な応用分野を大幅に狭めていた。
さらに、初期のCVD技術は、生産できるコーティングの種類が限られていた。CVDに関与する化学反応の複雑さと特異性から、確実に成膜できる材料は限られており、その有用性はさらに制限されていた。これらの限界は、真空コーティング技術の開発と普及に大きな課題をもたらし、これらの障壁を克服できる代替方法の探求を必要とした。
その後数十年で、こうした初期の課題は、1970年代に登場し、より適応性が高く環境に優しいソリューションを提供する物理蒸着(PVD)など、より汎用的で効率的なコーティング技術の開発への道を開くことになった。
PVD技術の出現
1970年代までに、物理蒸着(PVD)技術の登場により、真空コーティング技術の状況は大きく変化しました。この新しい方法は、その前身である化学気相成長法(CVD)に関連する環境問題のいくつかに対処するだけでなく、以前は実現できなかった無数の汎用性の高い表面特性を導入しました。CVDからPVDへの移行は、操作温度の低下と適用可能なコーティングの範囲の拡大によって顕著であり、それによってさまざまな産業分野での用途が広がった。
PVDの環境面での利点は特に注目に値する。高温と潜在的に危険な化学物質を必要とすることが多かったCVDとは異なり、PVDはより制御された条件下で作動するため、エネルギー消費量と排出量の削減につながった。この環境への優しさは、優れた硬度、耐摩耗性、耐食性を持つコーティングの製造能力と相まって、研究者と産業界の双方から急速に注目を集めるようになった。
この時期のPVD技術の急速な発展は、その適応性の高さと、コーティングの品質と耐久性の大幅な向上に起因している。自動車産業から航空宇宙産業まで幅広い産業が、工具や部品の性能を向上させるPVDを採用し始め、効率の向上と製品寿命の延長につながった。このような広範な採用は、PVD技術の進歩にさらに拍車をかけ、この技術を前進させ、近代的な工業プロセスの領域におけるPVDの地位を確固たるものにした。
現状と課題
不均衡な発展
装飾目的で真空コーティング技術が広く採用されているにもかかわらず、工業用金型製造におけるこれらのコーティングの適用には依然として課題が多い。主な障害は、工業用金型が要求する厳しい接着要件にあり、これにはコーティングと基材のより強固で耐久性のある接着が必要である。このような要求の高まりは、機能的な耐久性よりも美観を優先することの多い現在のコーティング技術では容易に満たすことができない。
さらに、工業用金型コーティングに特化した包括的なプロセス技術がないことが、こうした課題をさらに悪化させている。塗布方法がそれほど厳密でなくてもよい装飾用コーティングとは異なり、工業用モールドコーティングは、最適な性能と寿命を確保するために精密で管理されたプロセスを必要とする。このような技術開発の格差が、真空コーティング業界の不均衡な成長を招き、装飾用コーティングの進歩が工業用アプリケーションに十分に反映されていない。
このような問題に対処するため、工業用金型コーティング特有の要求を満たすことができる特殊な技術と方法論の開発が急務となっている。これには、コーティングの接着特性を向上させるだけでなく、前処理から塗布後の品質管理まで、プロセスチェーン全体を洗練させることも含まれる。これらの分野に注力することで、業界は装飾用コーティングと工業用コーティングのギャップを埋めることができ、よりバランスの取れた包括的な発展の軌道を促進することができる。
技術的格差
真空コーティング技術、特にPVD(Physical Vapor Deposition:物理的気相成長法)の分野では、国内の技術力が国際標準に遅れをとっていることが多い。この格差は単に装置の精巧さの問題ではなく、プロセスの最適化、材料科学の進歩、品質管理手法など、より広範な要素を含んでいる。
このギャップを埋めるためには、国内産業が先進設備を導入するだけでなく、最先端技術を吸収・統合することが急務である。これには、以下を含む多面的なアプローチが必要である:
- 設備のアップグレード:装置のアップグレード:複雑なPVDプロセスに正確に対応できる最新の真空チャンバー、電源、ガス投入システムに投資する。
- 技術の吸収:PVD技術のベストプラクティスを理解し導入するために、国際的なパートナーとの共同研究開発に取り組んでいます。
- プロセスの最適化:コーティング品質の均一性を確保するため、既存のプロセスを改良し、密着性や層の均一性などの問題に対処します。
側面 | 国内状況 | 国際標準 |
---|---|---|
設備 | 基本的または旧式 | 高度で高精度 |
プロセス制御 | 手動または半自動 | AIサポートによる完全自動化 |
材料科学 | 限定的な研究 | 広範な研究と革新 |
品質管理 | アドホック手法 | 体系的で厳格なFQC |
パリティに向けた道のりには、技術の獲得だけでなく、継続的なイノベーションと改善を支える強固なエコシステムの開発も含まれる。このような総合的なアプローチは、国内の能力を高め、世界規模で競争できるようにするために不可欠である。
PVDコーティングの基本概念と特徴
方法と技術
物理的気相成長法(PVD)にはいくつかの高度な手法があり、それぞれに独自の特徴と用途があります。PVDの中の2つの顕著な技術は、マルチアークめっきとマグネトロンスパッタリングです。
マルチアークめっきでは、電気アークを使用してターゲット材料を蒸発させ、材料をイオン化して基板に向かって推進します。この方法は、析出速度が速く、複雑な形状をコーティングできることで知られている。しかし、パーティクルの混入や不均一な膜厚といった問題がある。
一方、マグネトロンスパッタリングは、磁場を用いてターゲット原子のイオン化を促進し、これを基板に向かって加速する。この技術では、密度や均一性などのコーティング特性をよりよく制御できるため、精密なコーティングを必要とする用途に最適である。このような利点がある一方で、マグネトロンスパッタリングは、マルチアークメッキに比べ、時間がかかり、エネルギー消費量も多くなります。
方法 | 利点 | 短所 |
---|---|---|
マルチアークめっき | 成膜速度が速く、複雑な形状に適している。 | 粒子汚染、不均一な膜厚 |
マグネトロンスパッタリング | コーティング特性の優れた制御、高密度と均一性 | プロセスが遅く、エネルギー消費量が多い |
これらの方法とそれぞれの長所と短所を理解することは、特定の産業用途に最も適したPVD技術を選択する上で極めて重要である。
技術の組み合わせ
マルチアーク技術とマグネトロン技術の統合は、真空コーティングの分野での大きな進歩です。この組み合わせは、単なる技術の総和ではなく、両技術の利点を最大化する相乗的なアプローチであり、安定した高品質のコーティングの生産を保証します。
高い成膜速度と高密度コーティングの生産能力で知られるマルチアークめっきは、最小限の基板加熱で均一かつコンフォーマルなコーティングの生産に優れたマグネトロンスパッタリングを補完する。これらの方法を組み合わせることで、メーカーは成膜速度とコーティングの均一性のバランスをとることができる。
さらに、これらの技術をハイブリッド化することで、コーティング特性を最適化することができる。例えば、マルチアークイオンをマグネトロンスパッタリングプロセスに組み込むことで、コーティングの密着性と硬度を高めることができ、高い密着性と耐久性が最も重要な工業用金型コーティングにおける一般的な課題に対処することができる。
この統合はまた、材料選択とプロセス制御に新たな道を開く。両技術の長所を活用することで、硬い耐摩耗性コーティングからより複雑な多層構造まで、特性を調整した幅広い材料の成膜が可能になります。その結果、さまざまな産業用途の多様な要求を満たす、より汎用性の高い堅牢なコーティングソリューションが実現します。
まとめると、マルチアークとマグネトロン技術の組み合わせは、コーティングの品質と安定性を高めるだけでなく、達成可能な材料特性とプロセス効率の範囲を広げる。この進歩は、真空コーティング技術が達成できる限界を押し広げる極めて重要なものであり、工業用コーティングの進化の礎石となっています。
最新のコーティング装置とプロセス
コンポーネントとシステム
最新のコーティング装置は、それぞれが真空蒸着プロセスにおいて重要な役割を果たす重要なコンポーネントの洗練された集合体です。このシステムの中心は真空チャンバー真空チャンバーは、基板を大気条件から隔離する密閉された環境で、コーティングのための原始的な表面を確保します。真空チャンバーは通常、耐久性と耐腐食性で知られるステンレス鋼などの材料で作られている。
必要な真空レベルを達成する、真空部品 が使用される。これには、ロータリーベーンポンプやターボ分子ポンプなどの真空ポンプが含まれ、これらは連動してチャンバーの圧力をPVDプロセスに必要な超低レベルまで下げます。これらのポンプの効率は、コーティングの品質と均一性に直接影響するため、非常に重要です。
電源もまた、コーティング材料を気化させるのに必要な電気エネルギーを供給する重要なコンポーネントです。最新のシステムでは、多くの場合中間周波電源 またはパルス技術を使用することが多く、蒸着プロセスを正確に制御することで、より高品質なコーティングを実現します。これらの高度な電源は、従来のPVDセットアップで一般的な課題であったアーク放電や不均一な蒸着などの問題を軽減するのに役立つ。
最後にプロセスガス投入システム は操作に不可欠です。これらのシステムは、真空チャンバー内に反応性ガスを導入し、特性に合わせた複雑なコーティングの形成を可能にします。ガスの流量と組成を正確に制御することで、特定の機械的、化学的、光学的特性を持つコーティングが可能になり、この技術の汎用性と応用性が高まります。
まとめると、最新のコーティング装置は、真空チャンバー、真空取得部品、電源、プロセスガス入力システムが複雑に絡み合っており、それぞれがPVDプロセスの精度と品質に貢献している。
高度な技術
真空コーティング技術の領域では、いくつかの高度な技術が登場し、コーティングの品質と適用性を大幅に向上させている。そのひとつが非平衡磁場.これらの磁場は、成膜プロセスをより正確に制御し、均一性と密着性に優れたコーティングを可能にします。これは、コーティングの耐久性と性能が重要な産業用途で特に有益である。
もうひとつの重要な進歩は中間周波電源.従来の電源とは異なり、これらの中間周波数システムは、より高い安定性と効率を提供する。これにより、下地材料の完全性を損なうことなく、より厚く堅牢なコーティングの成膜が容易になります。この技術革新は、金型や工具に高性能コーティングを必要とする産業で特に有用である。
さらにパルス技術 はコーティング・プロセスに革命をもたらした。短く制御されたバーストでエネルギーを供給することで、パルス技術は基材への熱応力を最小限に抑え、反りや劣化を防ぎます。この方法は、デリケートな素材や複雑な表面処理が必要な素材に特に有利です。また、正確なエネルギー供給により、コーティングがより効果的に密着し、より長持ちする信頼性の高い結果が得られます。
これらの高度な技術は、真空コーティング技術の進化に貢献し、さまざまな産業用途において、より汎用的で効果的なものとなっている。非平衡磁場、中間周波電源、パルス技術の統合は、コーティングの品質を向上させるだけでなく、その適用範囲を広げ、現代産業のますます厳しくなる要求に応えています。
金型用PVDの応用と品質管理
前処理とコーティングプロセス
前処理法は、物理蒸着(PVD)コーティング用の表面を準備するための重要なステップです。これらの方法には高温スチーム洗浄が含まれ、汚染物質を効果的に除去し、清浄な基材を確保します。サンドブラストも重要な技術で、コーティングの密着性を高める粗面を作ります。PVDコーティングプロセス自体は、最適な結果を得るために、正確な温度制御と均一な加熱に大きく依存しています。
均一な加熱は、基材を均一に加熱し、コーティング材を均一に蒸着させるために不可欠です。温度制御も同様に重要であり、その偏差はコーティングの厚みや品質にばらつきを生じさせるからである。安定した一貫した加熱条件を維持し、PVDコーティングの全体的な品質を高めるために、中間周波数電源やパルス技術などの高度な技術がしばしば採用されます。
これらの前処理とコーティング工程は、工業用金型へのPVDコーティングの成功に不可欠です。金型の耐久性と性能を向上させるだけでなく、金型の稼動寿命も延ばし、高精度な製造環境には欠かせないものとなっている。
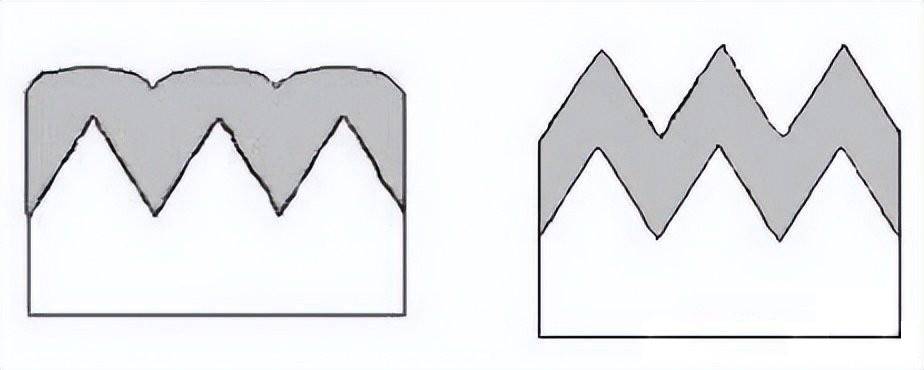
品質管理対策
機能品質管理(FQC)は、コーティングされた金型の信頼性と性能を確保するために重要な側面です。このプロセスでは、コーティングが要求される基準を満たしていることを保証するために、いくつかの入念な検査が行われます。
FQCの主要な手法のひとつが外観検査.これは、傷、くぼみ、変色などの表面の欠陥を検出するための徹底的な目視検査を含みます。これらの欠陥は金型の機能や寿命に大きな影響を与える可能性があるため、このステップは不可欠です。
もう一つの重要な方法は層深さ検査.この技術では、コーティング層の厚さを測定し、指定されたパラメータに準拠していることを確認します。塗膜の深さと均一性を正確に測定するために、プロフィロメーターや走査型電子顕微鏡など、さまざまな機器が使用されます。
塗膜の密着検査 も重要である。この工程では、コーティングと金型基材との接着強度を評価します。一般的な方法としては、スクラッチテスト、プルテスト、クロスカットテストなどがある。これらの検査は、潜在的な層間剥離や剥離の問題を特定するのに役立ち、コーティングの耐久性と有効性を保証します。
これらのFQC手法を統合することで、メーカーはコーティングされた金型が業界標準を満たすだけでなく、それを上回ることを保証し、さまざまな産業用途に信頼性の高い高性能ツールを提供することができます。
無料相談はお問い合わせください
KINTEK LAB SOLUTION の製品とサービスは、世界中のお客様に認められています。弊社スタッフがどんなご質問にも喜んで対応させていただきます。無料相談にお問い合わせいただき、製品スペシャリストにご相談いただき、アプリケーションのニーズに最適なソリューションを見つけてください。