CVD(Chemical Vapor Deposition)とPVD(Physical Vapor Deposition)は、基板上に薄膜を成膜するために広く使われている2つの技術であり、それぞれに異なるプロセス、利点、限界がある。CVDは、ガス状の前駆物質と基板との化学反応に依存しており、複雑な形状に均一で高密度のコーティングを成膜することができます。高温で作動し、厚く高品質な膜を必要とする用途に最適である。一方、PVDは真空中で固体材料を物理的に気化させ、基板上に凝縮させる。PVDは低温で作動し、薄く滑らかで耐久性のあるコーティングの成膜に適している。CVDとPVDのどちらを選択するかは、希望する膜特性、基材、アプリケーションの要件などの要因によって決まります。
キーポイントの説明
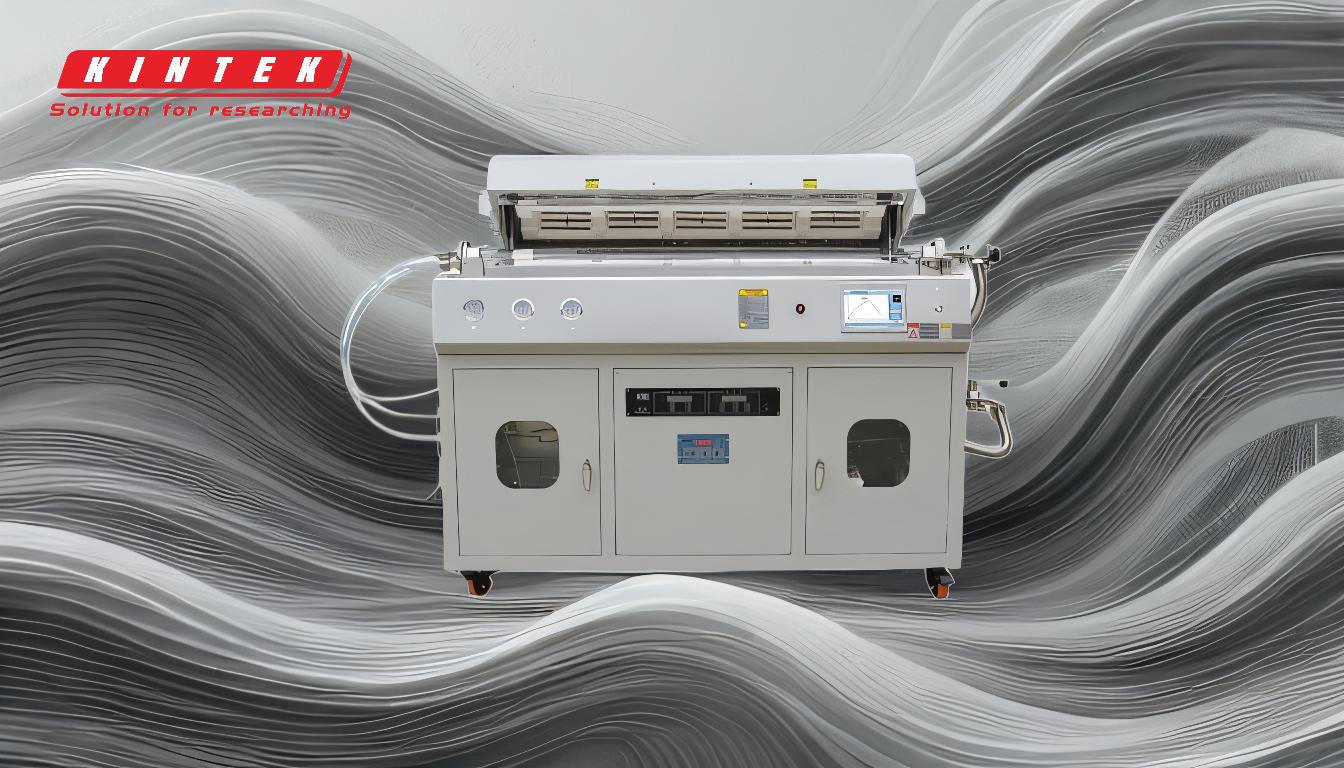
-
動作メカニズム:
- CVD:ガス状の前駆物質と基材との化学反応により、固体の皮膜を形成する。このプロセスは多方向性であるため、複雑な形状や深い凹部も均一に覆うことができる。
- PVD:固体材料を物理的に気化させ、基板上に輸送・凝縮させる。このプロセスはライン・オブ・サイトであり、露出した表面に直接材料を付着させる。
-
使用温度:
- CVD:一般的に高温(450℃~1050℃)で使用されるため、温度に敏感な基板での使用が制限されることがある。
- PVD:低温(250℃~450℃)で動作するため、高熱に耐えられない基材に適している。
-
コーティングの性質:
- CVD:主にセラミックやポリマーを成膜し、緻密で均一なコーティングが得られることが多い。
- PVD:金属、合金、セラミックスなど、より広範な材料を成膜できるが、一般的にCVDに比べ、コーティングの緻密さや均一性は劣る。
-
コーティング範囲:
- CVD:複雑な形状、穴、深い凹部へのコーティングが可能。
- PVD:視線方向の蒸着に限定されるため、複雑な形状や隠れた部分のコーティングにはあまり効果的でない。
-
膜厚と平滑性:
- CVD:化学反応により粗くなる可能性があるが、より厚い皮膜が得られる。
- PVD:より薄く、より滑らかで、より耐久性のある皮膜を形成し、精密さと表面仕上げを必要とする用途に最適。
-
蒸着速度:
- CVD:一般的に成膜速度が速く、厚膜の製造に経済的である。
- PVD:一般的に成膜速度は低いが、薄いコーティングの場合は塗布時間が早い。
-
用途:
- CVD:半導体製造、光学、耐摩耗用途など、高品質で均一なコーティングを必要とする産業で一般的に使用されている。
- PVD:装飾仕上げ、切削工具、医療機器など、平滑で耐久性があり、温度に敏感なコーティングを必要とする用途に適している。
-
材料利用効率:
- CVD:腐食性のガス状副生成物が発生し、膜中に不純物が残り、材料効率が低下する可能性がある。
- PVD:腐食性の副生成物を生成せず、特にEBPVD(電子ビーム物理蒸着)などの技術において高い材料利用効率を提供する。
これらの重要な違いを理解することで、装置や消耗品の購入者は、希望する膜特性、基板との互換性、運用上の制約など、アプリケーションの具体的な要件に基づいて、十分な情報に基づいた決定を下すことができる。
要約表
側面 | CVD | PVD |
---|---|---|
動作メカニズム | ガス状前駆体と基材との化学反応 | 真空中での固体材料の物理的気化 |
使用温度 | 高温(450°C~1050°C) | 低め(250℃~450) |
コーティング物質の性質 | 主にセラミックとポリマー;緻密で均一 | 金属、合金、セラミックス;緻密で均一ではない |
コーティング範囲 | 複雑な形状や深い凹部に最適 | 直視下蒸着に限定される |
膜厚/平滑性 | より厚く、より粗いコーティング | より薄く、より滑らかで、より耐久性のあるコーティング |
蒸着速度 | 厚膜には高い蒸着速度 | 薄いコーティングの場合、レートは低いが速度は速い |
用途 | 半導体製造、光学、耐摩耗用途 | 装飾仕上げ、切削工具、医療機器 |
材料効率 | 腐食性の副生成物が発生する可能性があり、効率が低い | 腐食性副生成物なし、高効率 |
CVDとPVDの選択でお困りですか? 今すぐ当社の専門家にお問い合わせください!