浸炭は、延性のあるコアを維持しながら、低炭素鋼部品の表面硬度と耐摩耗性を向上させる、広く使用されている熱処理プロセスです。このプロセスには、高温で金属の表面に炭素を拡散させた後、急冷して硬い外層を作成することが含まれます。浸炭は、高い応力、摩擦、摩耗にさらされるコンポーネントの耐久性と性能を向上させるために、自動車、航空宇宙、製造、工具製造などのさまざまな業界に適用されています。このプロセスは多用途であり、特定の領域の選択的硬化や、高周波焼き入れなどのさらなる処理の準備が可能です。
重要なポイントの説明:
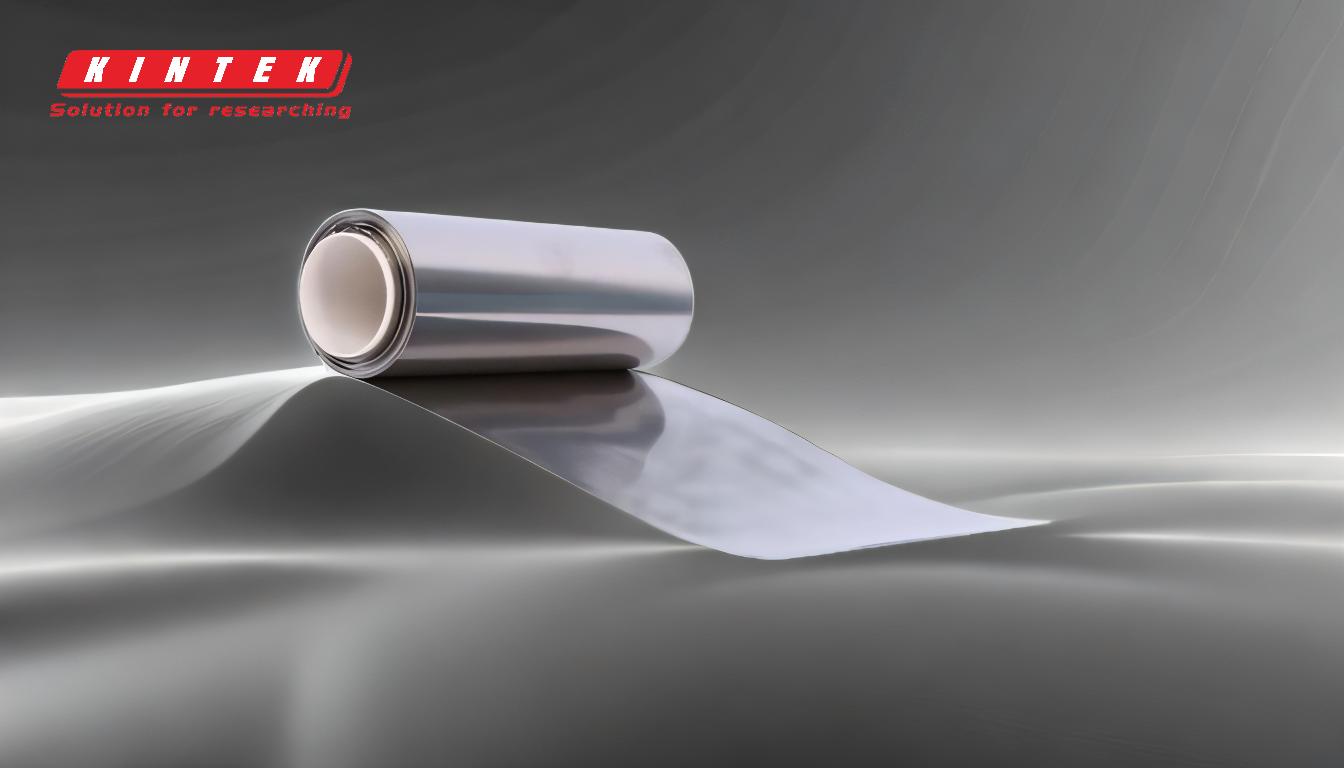
-
表面硬化による耐摩耗性
- 浸炭は主に、低炭素鋼部品に硬くて耐摩耗性の表面を作成するために使用されます。カーボンを表面に拡散させることにより、外層が大幅に硬くなり、摩擦、磨耗、衝撃にさらされるコンポーネントに最適です。
- 用途には、自動車や産業機械のギア、シャフト、ベアリング、その他の機械部品が含まれます。
-
靭性を高めるダクタイルコア
- 表面は硬くなりますが、部品の中心は柔らかく延性を保ちます。この組み合わせにより、コンポーネントは破損することなく高い応力に耐えることができるため、強度と柔軟性の両方が必要な部品に適しています。
- 例としては、車両のクランクシャフト、カムシャフト、トランスミッション部品などがあります。
-
選択的硬化
- 浸炭は、硬化していない領域を炭素停止塗料でマスキングすることで、部品の特定の領域に適用できます。これにより、メーカーはコンポーネントの硬さを特定の機能要件に合わせて調整することができます。
- この技術は、ギアの歯やベアリング レースなど、特定の表面のみを硬化する必要がある複雑な部品でよく使用されます。
-
高周波焼入れの準備
- 浸炭は、高周波焼き入れの前駆体として使用されることがあります。表面層の炭素含有量を増やすことにより、部品は後続の硬化プロセスに対する応答性が向上し、その結果、硬度と耐摩耗性がさらに向上します。
- これは、大型機械や航空宇宙部品などの高性能アプリケーションで特に役立ちます。
-
機械的特性の向上
- このプロセスにより、疲労強度や変形に対する耐性など、金属の微細構造と機械的特性が強化されます。これにより、浸炭部品の耐久性が向上し、厳しい環境でも長持ちします。
- アプリケーションには、発電コンポーネント、医療機器、工具機器などが含まれます。
-
業界を超えた多用途性
- 浸炭は、自動車、航空宇宙、製造、医療機器の製造など、幅広い業界で使用されています。表面硬度と耐摩耗性を向上させるその能力は、信頼性の高い高性能コンポーネントの作成に不可欠です。
- たとえば、航空機の着陸装置、手術器具、工業用切削工具は、厳しい性能基準を満たすために浸炭処理を受けることがよくあります。
-
典型的なケース深さ
- 硬化層の深さ (硬化深さ) は、用途に応じて通常 0.020 インチから 0.050 インチの範囲です。これにより、コアの延性を維持しながら、十分な表面硬度が確保されます。
- 硬化層の深さは、耐荷重能力や耐摩耗性など、各コンポーネントの特定の要件を満たすために慎重に制御されます。
-
プロセスのバリエーション
- 浸炭にはガス浸炭、液体浸炭、パック浸炭など、用途や材質に応じたさまざまな方法があります。
- たとえば、ガス浸炭は一般に大量生産に使用されますが、パック浸炭は小規模なバッチまたは特殊な部品に好まれます。
これらの重要なポイントを理解することで、機器や消耗品の購入者は、特定のニーズを満たすために浸炭をいつどのように使用するかについて情報に基づいた決定を下すことができます。このプロセスの多用途性と、表面硬度と中心部の靭性の両方を強化する能力により、このプロセスは現代の製造およびエンジニアリングにおいて重要な技術となっています。
概要表:
重要な側面 | 説明 |
---|---|
表面硬化 | 摩擦にさらされるコンポーネントに硬くて耐摩耗性の外層を作成します。 |
ダクタイルコア | 破損することなく高い応力に耐えられるように、柔らかく柔軟なコアを維持します。 |
選択的硬化 | カーボンストップペイントを使用して、特定の領域をターゲットに硬化させることができます。 |
高周波焼入れの準備 | その後の硬化プロセスに対する応答性が向上します。 |
機械的性質 | 疲労強度、耐変形性、耐久性が向上します。 |
多用途性 | 自動車、航空宇宙、製造、医療機器業界で使用されています。 |
典型的なケース深さ | アプリケーションのニーズに合わせて調整できる範囲は 0.020 インチから 0.050 インチです。 |
プロセスのバリエーション | さまざまな用途に応じたガス浸炭、液体浸炭、パック浸炭が含まれます。 |
浸炭がどのようにコンポーネントを最適化できるかを発見してください。 今すぐ専門家にお問い合わせください !