トランスファー成形は、主に熱硬化性プラスチックやゴムに用いられる製造工程で、材料を予熱した後、加熱した金型キャビティに圧力をかけて押し込む。この方法は、エレクトロニクス、自動車、航空宇宙など、高精度で複雑な形状を必要とする産業で広く使われている。このプロセスには、高い生産速度、優れた表面仕上げ、複雑な部品の製造能力など、いくつかの利点がある。しかし、初期金型コストの上昇、材料選択の制限、材料廃棄の可能性などの欠点もあります。トランスファー成形の長所と短所を理解することは、メーカーが特定の用途への適合性について十分な情報を得た上で決定を下すために不可欠です。
主なポイントを説明します:
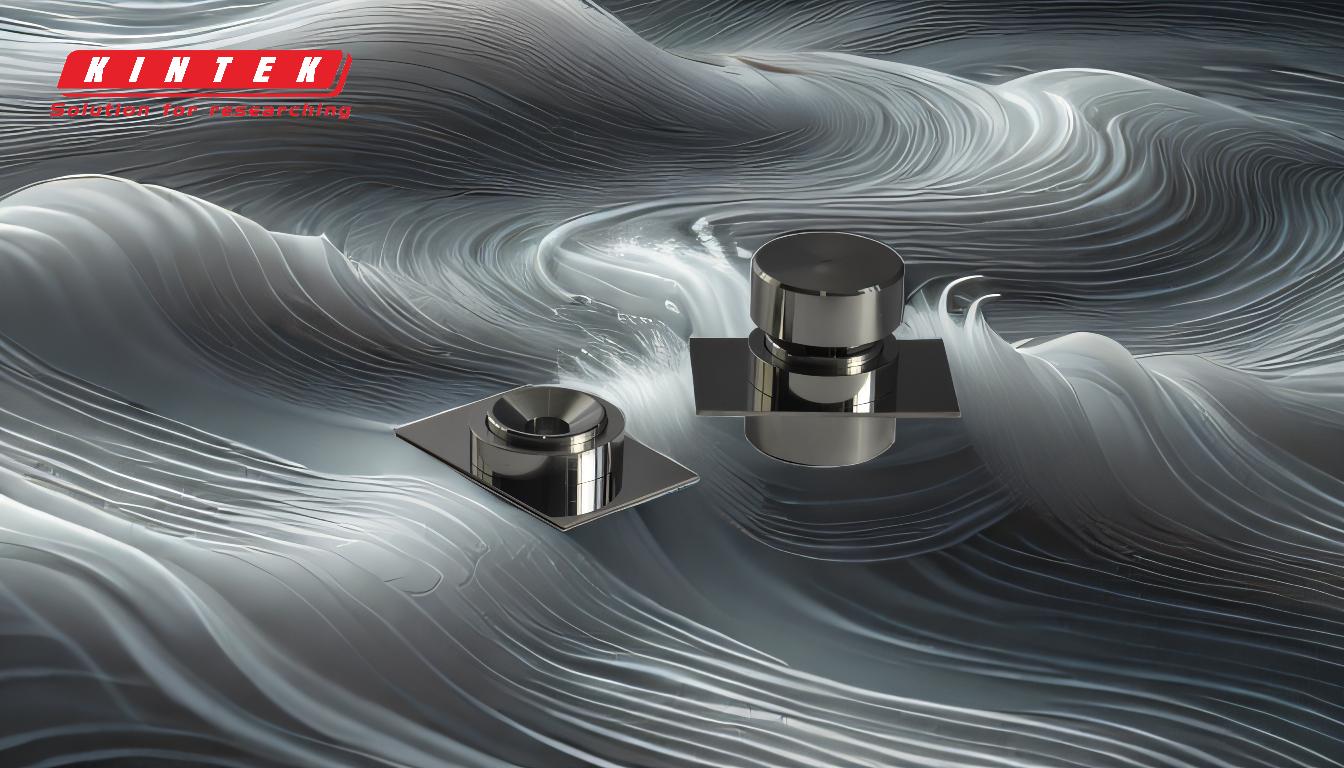
-
トランスファー成形の利点:
- 高い生産率:トランスファー成形は生産サイクルが速く、大量生産に適しています。予熱された材料は素早く金型に流れ込み、圧縮成形のような他の方法と比較してサイクルタイムを短縮します。
- 優れた表面仕上げ:このプロセスでは、滑らかな表面と微細なディテールを持つ部品が製造されるため、電気コネクターや自動車部品など、美観や精度が要求される用途に最適です。
- 複雑な形状の製造能力:トランスファー成形は、他の成形技術では困難な複雑な形状や薄肉の部品を作ることができます。
- フラッシュの削減:コントロールされた圧力と材料の流れにより、成形品のエッジ部の余分な材料(バリ)を最小限に抑え、後加工の必要性を低減します。
-
トランスファー成形の欠点:
- 高い初期金型コスト:トランスファー成形に使用される金型は、その複雑さと正確な位置合わせの必要性から、一般的に圧縮成形よりも高価である。
- 材料の制限:トランスファー成形は主に熱硬化性材料に適しており、硬化後に再溶融や再成形ができない。そのため、射出成形に比べて使用できる材料の範囲が限定される。
- 廃材:このプロセスでは、特にスプルーやランナーといった形で廃棄物が発生する可能性があり、これらは必ずしも再利用可能とは限らない。
- 長いセットアップ時間:トランスファー成形のための金型と材料の準備は、圧縮成形のような単純なプロセスに比べて時間がかかることがあります。
-
他の成形技術との比較:
- 圧縮成形:トランスファー成形は、圧縮成形よりも材料の流れやパーツの細部のコントロールがしやすいが、コストが高く、複雑である。
- 射出成形:射出成形は材料選択の面でより汎用性があり、より大きな生産量に対応できますが、トランスファー成形は熱硬化性材料やより小さく複雑な部品に適しています。
-
トランスファー成形の用途:
- エレクトロニクス:精密でデリケートな部品を保護できるため、集積回路やコネクターなどの電子部品の封止に使用される。
- 自動車:高い耐久性と耐熱性、耐薬品性を必要とするガスケット、シール、その他の部品の製造に最適。
- 航空宇宙:複雑な形状の軽量・高強度部品の製造に適しています。
-
トランスファー成形を選択する際に考慮すべき要素:
- 部品の複雑さ:トランスファー成形は、複雑なデザインや薄い壁の部品に最適です。
- 材料要件:材料が熱硬化プロセスに適合していることを確認する。
- 生産量:生産量が高い金型費用を正当化できるかどうかを評価する。
- 費用便益分析:精度と表面仕上げのメリットと、材料の無駄や段取り時間のデメリットを天秤にかける。
要約すると、トランスファー成形は、精度と表面仕上げにおいて明確な利点を持つ、多用途で効率的な製造プロセスである。しかし、その適性は、材料の適合性、部品の複雑さ、生産量などの要因によって異なります。これらの側面を慎重に評価することで、製造業者はトランスファー成形が特定のニーズに適した選択であるかどうかを判断することができます。
総括表
側面 | メリット | デメリット |
---|---|---|
生産率 | 大量生産に適した高い生産速度。 | シンプルな工程に比べ、セットアップ時間が長い。 |
表面仕上げ | 滑らかな表面と繊細なディテールを持つ優れた表面仕上げ。 | スプルーとランナーという形で材料が無駄になる。 |
複雑な形状 | 複雑な形状や薄肉部品の作成が可能。 | 複雑な金型のため、初期金型費用が高い。 |
材料適合性 | 熱硬化性材料に最適。 | 熱硬化性材料に限定されるため、材料の選択が制限される。 |
トランスファーモールディングがお客様のプロジェクトに適しているかどうかをお知りになりたいですか? 当社の専門家に今すぐご連絡ください ご相談ください!