熱蒸着とマグネトロンスパッタリングは、どちらも広く使われている薄膜蒸着技術であり、それぞれに明確な利点と限界がある。熱蒸発法は、高い蒸着速度、簡便性、費用対効果で好まれ、光学、電子工学、太陽電池など、速度と材料利用効率が優先される用途に理想的である。特に融点の低い材料に適しており、均一性にも優れている。一方、マグネトロンスパッタリングは、密度、密着性、表面形状に優れた高品質膜の製造に優れており、精密な化学量論、低表面粗さ、膜特性の向上が求められる用途に適している。この2つの技術のどちらを選ぶかは、膜質、蒸着速度、材料適合性など、アプリケーションの具体的な要件によって決まります。
キーポイントの説明
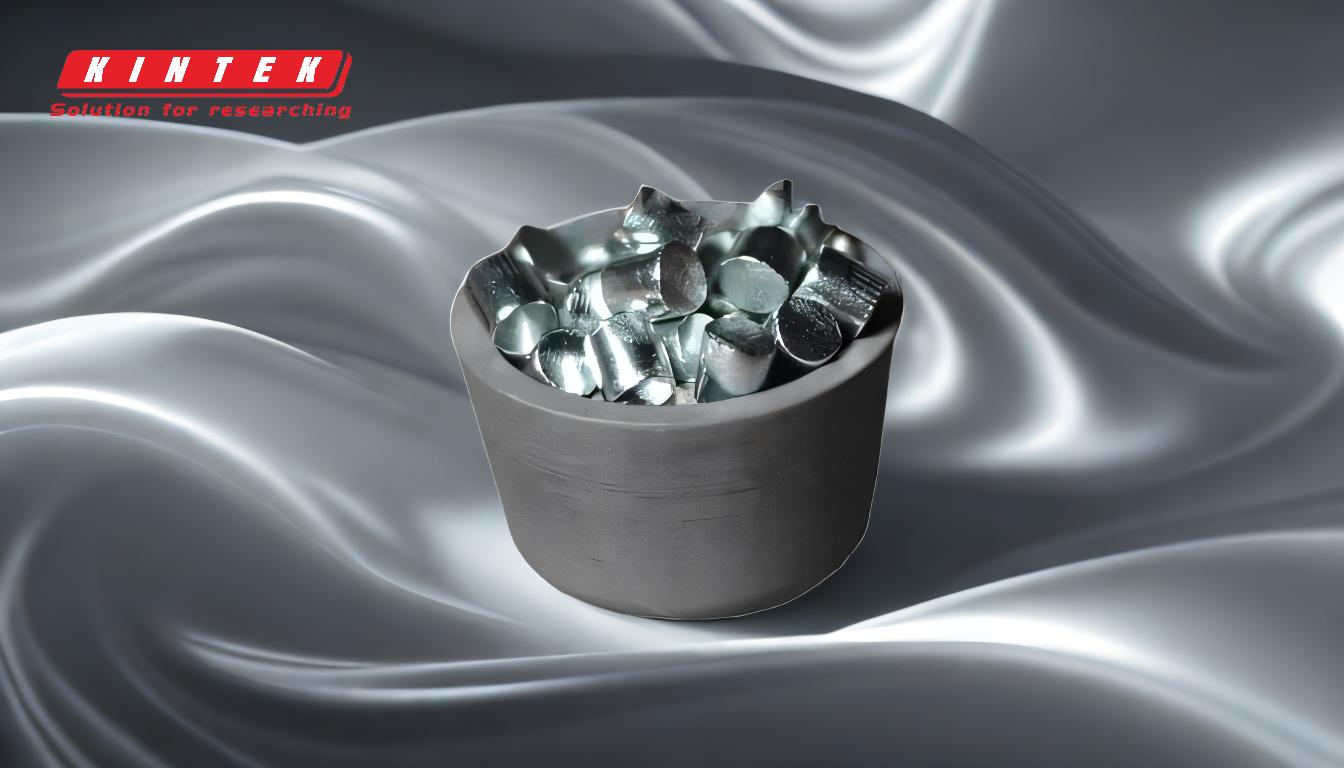
-
蒸着率と効率:
- 熱蒸発:マグネトロンスパッタリングに比べて成膜速度が格段に速いため、スピードが要求される用途でより速く、より効率的に成膜できる。これは、迅速な生産が要求されることの多い光学や電子工学のような産業で特に有利です。
- マグネトロンスパッタリング:速度が遅い反面、フィルムの特性をよりよくコントロールできるため、高い精度と品質が要求される用途には欠かせない。
-
フィルムの品質と特性:
- 熱蒸発:スパッタリング膜に比べ、密度が低く、粒径が大きい膜ができる。その結果、密着性や表面粗さが低下することがあり、高い膜質を要求される用途には適さない場合がある。
- マグネトロンスパッタリング:粒径が小さく、密着性に優れ、バルク材料に近い特性を持つ緻密な膜を生成する。そのため、膜質、密度、表面形状が重要な用途に最適です。
-
材料適合性:
- 熱蒸発:金属と非金属の両方に対応し、特に融点の低い材料に適している。合金の作成や連続コーティングも可能で、材料選択の柔軟性を提供する。
- マグネトロンスパッタリング:主に金属に使用されるが、色のオプションや変調の面でより多様性を提供し、特定の美的または機能的特性を必要とする用途に有益である。
-
コストと複雑さ:
- 熱蒸発:比較的シンプルで費用対効果が高く、必要な消費電力も少ない。低エネルギーの蒸発粒子を生成する穏やかな技術であり、繊細な用途に適している。
- マグネトロンスパッタリング:より複雑で、特殊な装置と高い消費電力が必要なため、一般的に高価。しかし、精密な特性を持つ高品質のフィルムを必要とする用途では、その投資は正当化される。
-
均一性と指向性:
- 熱蒸発:プラネタリー基板固定具とユニフォミティマスクを使用することにより、優れた均一性を提供する。また、複雑な形状のコーティングに有利な優れた指向性を提供します。
- マグネトロンスパッタリング:高い均一性を実現できる反面、熱蒸発と同レベルの指向性を実現するには、より高度なセットアップと制御が必要になる場合がある。
-
用途と産業利用:
- 熱蒸発:光学コーティング、電子部品、太陽電池の製造など、高い成膜速度と材料効率が優先される産業で広く使用されている。
- マグネトロンスパッタリング:半導体デバイスの製造、保護コーティング、装飾仕上げなど、精密な特性を持つ高品質のフィルムを必要とする産業に適している。
要約すると、熱蒸着とマグネトロンスパッタリングのどちらを選択するかは、アプリケーションの具体的な要件によって決まる。サーマルエバポレーションは高速でコスト効率の良い生産に適しており、マグネトロンスパッタリングは高品質で精密な成膜に適した方法である。どちらの手法にも独自の利点と限界があり、膜質、成膜速度、材料適合性、コストなどを考慮して決定する必要がある。
総括表:
側面 | 熱蒸着 | マグネトロンスパッタリング |
---|---|---|
蒸着速度 | 高い | 中程度 |
フィルムの質 | 密度が低く、粒径が大きい | 密度が高く、粒径が小さい |
材料適合性 | 金属、非金属、低融点 | 主に金属、多彩なカラーオプション |
コスト | 低コスト、シンプルなセットアップ | 高コスト、複雑なセットアップ |
均一性 | プラネタリー治具で優れている | 高いが高度な制御が必要 |
用途 | 光学、エレクトロニクス、太陽電池 | 半導体、保護膜 |
どの薄膜蒸着技術がお客様のプロジェクトに適しているか、まだご不明ですか? 当社の専門家に今すぐご連絡ください をご利用ください!