合成グラファイトは、炭素豊富な材料を高純度のグラファイトに変える一連の複雑なプロセスを通じて製造されます。製造には通常、原料の選択、炭化、黒鉛化、精製のステップが含まれます。このプロセスは、石油コークスやコールタールピッチなどの炭素を豊富に含む前駆体から始まり、これらを高温に加熱して揮発性成分を除去し、炭素構造を形成します。この炭素構造はさらに極度の高温 (最高 3000°C) に加熱され、炭素原子がグラファイトの結晶構造に整列します。最後に、材料は精製されて不純物が除去され、高品質の人造黒鉛が得られます。この材料は、優れた導電性、熱安定性、耐薬品性により、電池、エレクトロニクス、冶金などの産業で広く使用されています。
重要なポイントの説明:
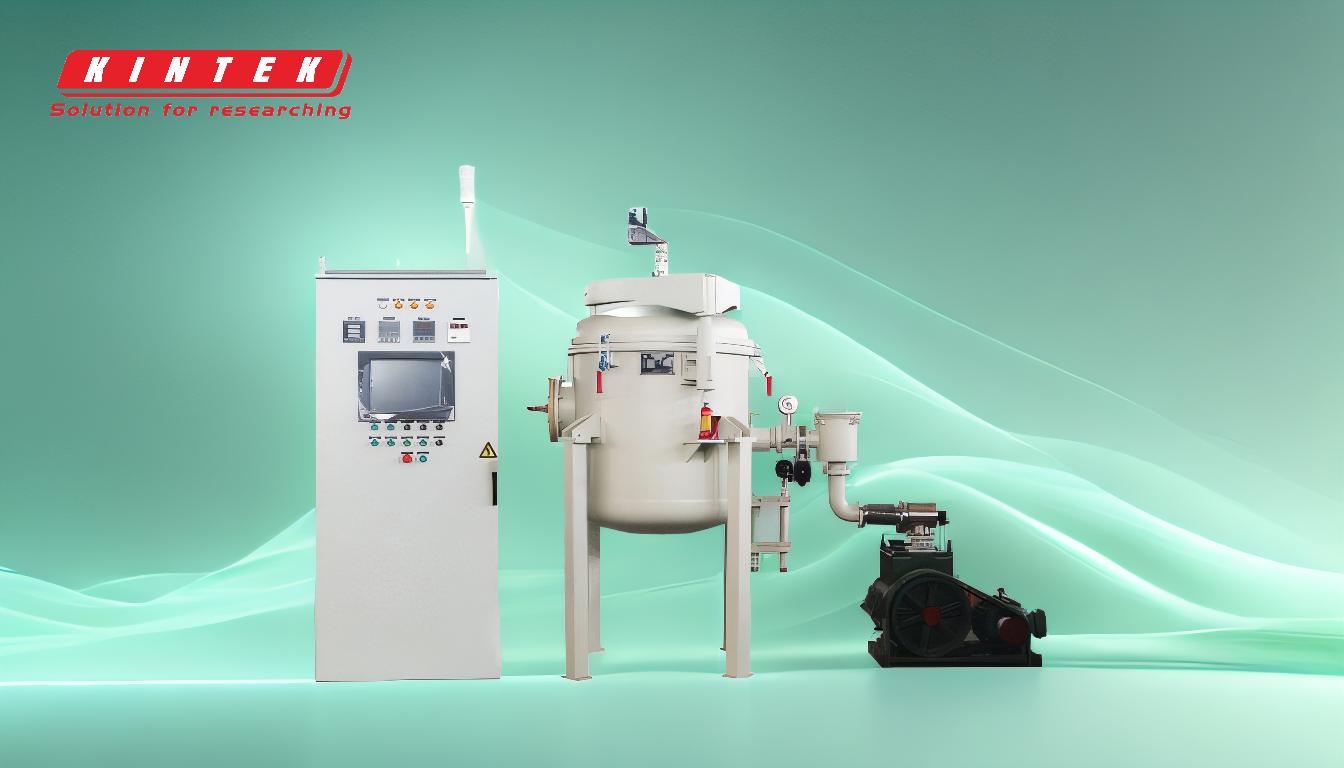
-
原材料の選択:
- 製造プロセスは、炭素を豊富に含む前駆体、通常は石油コークスまたはコールタールピッチを選択することから始まります。これらの材料は、炭素含有量が高く、加熱中に安定した炭素構造を形成する能力を考慮して選択されます。
- 石油コークスは石油精製の副産物であり、コールタールピッチは石炭の加工から得られます。どちらの材料もコスト効率が高く、人造黒鉛の製造に必要な炭素骨格を提供します。
-
炭化:
- 選択された原材料は炭化処理され、酸素のない環境で 500°C ~ 1500°C の温度に加熱されます。このステップでは、水素、酸素、窒素などの揮発性成分が除去され、固体の炭素構造が残ります。
- 炭化プロセスは、後にグラファイトに変換される最初の炭素骨格を形成するために重要です。
-
黒鉛化:
- 炭化後、材料は黒鉛化され、不活性雰囲気中で非常に高温 (最高 3000°C) に加熱されます。このステップにより、炭素原子が結晶性グラファイト構造に整列します。
- 黒鉛化は、高い導電性、熱安定性、機械的強度などの人造黒鉛の望ましい特性を達成するために不可欠です。
-
精製:
- 製造プロセスの最終ステップは精製であり、グラファイトを処理して残留不純物を除去します。これは通常、酸洗浄や塩素ガス環境での高温処理などの化学的または熱的方法を使用して行われます。
- 精製により、人造黒鉛がエレクトロニクスやバッテリーなどの業界の用途に必要な高純度基準を満たしていることが保証されます。
-
人造黒鉛の用途:
- 人造黒鉛はそのユニークな特性により、さまざまな産業で広く使用されています。電池業界では、リチウムイオン電池の重要なコンポーネントであり、負極材料として機能します。
- また、鉄鋼業界の電気アーク炉用の電極の製造や、るつぼや熱管理システムなどの高温用途にも使用されています。
-
人造黒鉛の利点:
- 合成グラファイトには、高純度、優れた一貫性、特定の用途に合わせて特性を調整できるなど、天然グラファイトに比べていくつかの利点があります。
- 優れた導電性、熱安定性、耐薬品性により、幅広い産業用途に多用途な材料となっています。
人造黒鉛の製造に関わる詳細な手順を理解することで、購入者は材料が特定のニーズに適合するかどうか情報に基づいた決定を下すことができます。このプロセスにより、最終製品が要求の厳しい用途に必要な高い基準を満たしていることが保証され、人造黒鉛が現代の産業において貴重な材料となっています。
概要表:
ステップ | 説明 | 主要な詳細 |
---|---|---|
原材料の選択 | 石油コークスやコールタールピッチなどの炭素が豊富な前駆体を選択します。 | 炭素含有量が高く、コスト効率が高く、安定した炭素構造の形成。 |
炭化 | 無酸素環境で 500°C ~ 1500°C に加熱して、揮発性成分を除去します。 | 固体の炭素構造を形成します。初期の炭素フレームワークにとって重要です。 |
黒鉛化 | 最高 3000°C まで加熱して炭素原子を結晶グラファイト構造に整列させます。 | 導電性、熱安定性、機械的強度を高めます。 |
精製 | 酸洗浄などの化学的または熱的方法により不純物を除去します。 | エレクトロニクスやバッテリーの用途向けに高純度を保証します。 |
人造黒鉛が産業上のニーズにどのように対応するかをご覧ください。 今すぐ専門家にお問い合わせください !