PECVD (プラズマ化学蒸着) 装置で使用される熱処理プロセスなどの熱処理プロセスは、プラズマ生成の種類とプラズマと基板の間の相互作用に基づいて大きく異なります。 PECVD における熱処理の主なタイプは、直接 PECVD、誘導結合プラズマ リアクター、およびリモート プラズマ リアクターの 3 つです。各方法には、プラズマの生成方法、プラズマが基板とどのように相互作用するか、汚染リスクのレベルなど、独自の特徴があります。これらの違いを理解することは、太陽電池の反射防止コーティングなど、特定の用途に適切な機器を選択するために重要です。
重要なポイントの説明:
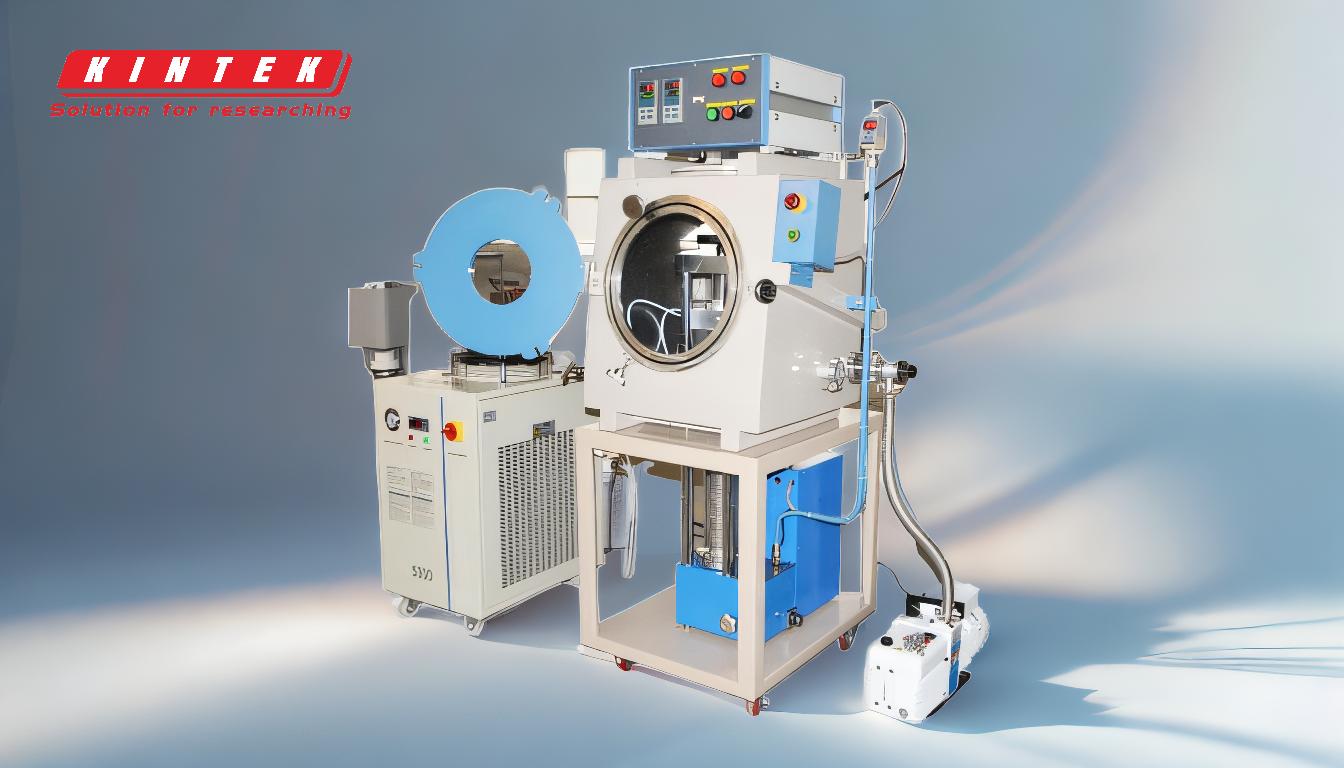
-
ダイレクト PECVD リアクター:
- プラズマ生成: 直接 PECVD リアクターは容量結合プラズマを使用し、プラズマは基板と直接接触します。
- 基材との相互作用 :直接接触により、効率的なエネルギー伝達と薄膜の堆積が可能になります。
- 汚染リスク: プラズマと基板間の直接相互作用により、汚染のリスクが高くなります。
- アプリケーション: 太陽電池の反射防止コーティングなど、正確かつ効率的な薄膜堆積が必要な用途で一般的に使用されます。
-
誘導結合プラズマリアクター:
- プラズマ生成: 誘導結合プラズマリアクターでは、電極が反応チャンバーの外側に配置され、誘導結合を通じてプラズマを生成します。
- 基板との相互作用: プラズマは基板と直接接触しないため、汚染のリスクが軽減されます。
- 汚染リスク: 直接 PECVD リアクターと比較して汚染リスクが低い。
- アプリケーション: 半導体製造など、汚染管理が重要な用途に適しています。
-
リモートプラズマリアクター:
- プラズマ生成: リモート プラズマ リアクターは、別のチャンバーでプラズマを生成し、それを基板チャンバーに輸送します。
- 基板との相互作用: 基板はプラズマ生成プロセスにさらされないため、汚染が最小限に抑えられます。
- 汚染リスク :3種類の中で最も汚染リスクが低い。
- アプリケーション: 高度なマイクロエレクトロニクスなど、汚染を最小限に抑える必要がある非常に敏感なプロセスに最適です。
-
プロセスガスとプラズマの相互作用:
- 使用ガス: 一般的なプロセス ガスにはシランとアンモニアが含まれており、これらはリアクター内でイオン化されてプラズマになります。
- プラズマの特性: プラズマは化学反応性があり、シリコン チップなどの基板上への薄膜の堆積を促進します。
- アプリケーションにおける役割: 太陽電池チップに反射防止膜を形成し、効率を高めるために不可欠です。
-
機器の選択に関する考慮事項:
- 汚染管理: 低汚染性が要求される用途には、誘導結合プラズマ リアクターまたはリモート プラズマ リアクターを選択してください。
- 効率と精度: 直接 PECVD リアクターは、高精度で効率的な薄膜堆積が必要な用途に適しています。
- アプリケーション固有のニーズ: 反射防止コーティングや高度な半導体機能の必要性など、アプリケーションの特定の要件を考慮してください。
これらの違いを理解すると、適切なものを選択するのに役立ちます PECVD装置 特定の熱処理ニーズに対応し、最適なパフォーマンスと最小限の汚染リスクを保証します。
概要表:
タイプ | プラズマ生成 | 基板との相互作用 | 汚染リスク | アプリケーション |
---|---|---|---|---|
ダイレクト PECVD リアクター | 基板と直接接触する容量結合プラズマ。 | 効率的なエネルギー伝達と薄膜の堆積。 | 直接的な相互作用により汚染リスクが高くなります。 | 太陽電池の反射防止コーティング。 |
誘導結合プラズマリアクター | チャンバーの外側の電極は、誘導結合を通じてプラズマを生成します。 | プラズマが基板に直接接触しないため、汚染が軽減されます。 | 直接PECVDと比較して汚染リスクが低い。 | 半導体製造。 |
リモートプラズマリアクター | プラズマは別のチャンバーで生成され、基板チャンバーに輸送されます。 | 基板がプラズマ生成にさらされないため、汚染が最小限に抑えられます。 | 3種類の中で最も汚染リスクが低い。 | 先進的なマイクロエレクトロニクス。 |
ニーズに合った適切な PECVD 装置の選択にサポートが必要ですか? 今すぐ当社の専門家にご連絡ください。