スパークプラズマ焼結(SPS)の紹介
スパークプラズマ焼結(SPS) は、現代の材料加工技術における画期的なアプローチであり、材料の焼結方法に革命をもたらします。この革新的な方法は、従来の技術とは大きく異なり、直流パルスを使用して急速加熱と焼結を実現することで際立っています。SPSのユニークなプロセスでは、パルス電流によって火花プラズマを発生させ、優れた特性を持つ材料の創出を容易にしている。この総合ガイドでは、SPSの複雑さ、様々な産業における無数の応用例、そして従来の焼結法と比較した場合の大きな利点について掘り下げていきます。材料科学の未来を形作るSPSの変革の可能性を明らかにするために、ぜひご参加ください。
スパークプラズマ焼結炉の仕組み
スパークプラズマ焼結(SPS)は、パルス電流焼結(PECS)、プラズマ活性化焼結(PAS)、フィールドアシスト焼結技術(FAST)とも呼ばれ、ダイ/パンチセットアップ内で粉末成形体を加熱するために高パルス直流電流を活用する高度な焼結技術です。この方法では、最大250kNの圧縮力を加えることができ、変圧器の出力は10V、電流は最大10kAに達します。パルスDC電流パターンは、0~255msの範囲でONとOFFを調整でき、焼結プロセスを正確に制御できます。
SPSプロセスは、その急速な加熱と冷却速度が特徴で、工具のサイズと設計によっては、それぞれ1000℃/分と400℃/分を超えることがあります。この急速な熱サイクルにより、低温での粗大化プロセスが最小限に抑えられ、完全緻密化後も固有のナノ構造が維持されます。SPS炉内の温度は、上部パンチの穴底に焦点を合わせた中央高温計を使用してモニターされ、試料の特性やサイズに関係なく正確な温度測定が保証されます。外部パイロメーターと様々な場所に設置されたフレキシブル熱電対を使用することで、さらなる温度モニタリングが可能です。
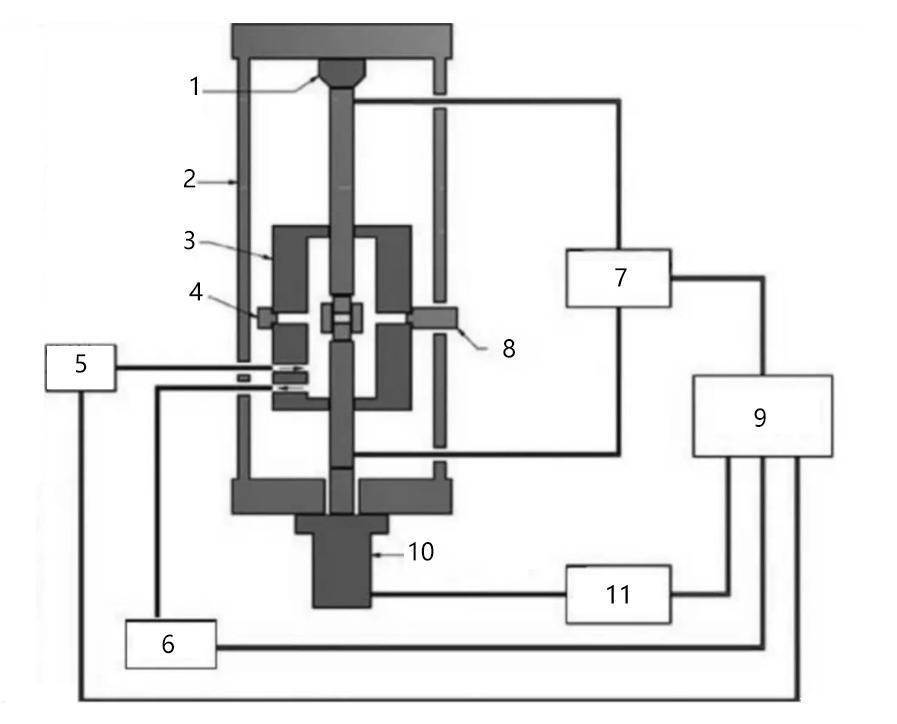
1.ローディングユニット 2.ローディングフレーム 3.真空チャンバー 4.観察窓 5.不活性ガス流路 6.真空ポンプ 7.パルススイッチ 8.温度計 9.制御システム 10.油圧シリンダー 11.油圧システム
SPS炉の主要コンポーネントには、軸圧装置、水冷パンチ電極、真空チャンバーが含まれます。軸圧装置は必要な圧縮力を加え、水冷パンチ電極はプロセス中に発生する熱を管理するのに役立ちます。真空チャンバーは、真空とアルゴン環境を切り替えられる雰囲気制御システムと相まって、最適な焼結条件を保証します。直流パルス電源と冷却水システム、変位測定、温度測定、安全制御ユニットがSPSのセットアップを完了し、ユーザーフレンドリーなタッチスクリーンインターフェースを通じて包括的なプロセス制御と焼結サイクルのプログラミングを容易にします。
SPS炉はセラミック、サーメット、金属を含む様々な材料の焼結に広く使用されています。その主な技術的利点は、処理時間を大幅に短縮する高い加熱・冷却速度にあります。高パルス電流は、導電性材料の緻密化を促進するだけでなく、表面酸化物の除去、エレクトロマイグレーション、電気塑性などの複数の焼結メカニズムを活性化する。この機械的圧力、電場、熱場の組み合わせは、粒子間の結合と緻密化を著しく改善し、SPSを高性能材料の調製に適した方法にしている。
要約すると、スパークプラズマ焼結プロセスは、材料の緻密化のための非常に効率的で制御された方法であり、迅速な処理時間と微細構造を維持する能力を提供します。その応用範囲は、先端セラミックスから金属複合材料まで、さまざまな分野に及んでおり、現代の材料科学と工学におけるその汎用性と重要性を浮き彫りにしている。
材料加工におけるSPS使用の利点
スパークプラズマ焼結(SPS)は、従来の焼結技術に対して大きな利点を提供することで、材料加工の分野に革命をもたらしました。SPSは、温度と圧力の両方を利用して材料の急速な緻密化を実現する電界支援焼結技術です。この方法は、セラミックス、金属、複合材料を含む幅広い材料の焼結に特に効果的で、その効率と精度は際立っています。
迅速な焼結率
SPSの最も顕著な利点のひとつは、迅速な焼結速度を達成できることです。ホットプレスや無加圧焼結といった従来の焼結方法では、所望の緻密化を達成するのに数時間かかることがあります。対照的に、SPSはわずか数分で材料を緻密化することができます。この迅速な焼結を可能にするのは、毎分500℃を超える高い加熱速度である。例えば、1200℃の温度に達するには、従来の方法では2~4時間かかるのに対し、SPSではわずか4分で達成できる。この速度は生産性を高めるだけでなく、エネルギー消費と操業コストを削減する。
微細粒焼結
SPSは、焼結材料の機械的・物理的特性を向上させるために重要な微粒焼結を促進します。加熱速度が速いため結晶粒の成長が抑制され、制御された微細構造を持つ材料を作ることができます。これは、特にナノ結晶材料の製造に有益であり、小さな粒径を維持することは、優れた特性を達成するために不可欠である。細粒焼結はまた、焼結製品の均質性を高め、より一貫した信頼性の高い性能につながります。
密度と温度勾配の制御能力
SPSは、焼結材料内の密度と温度勾配の優れた制御を提供します。この制御レベルは、温度と圧力の同時印加によって達成され、焼結プロセスの精密な調整を可能にします。密度制御は、特定の気孔率レベルの材料を作成したり、完全な高密度化を達成したりする場合に特に重要です。さらに、SPSは金型内に温度勾配を作ることができ、融点の異なる材料の同時焼結を可能にします。この機能は、組成や特性が空間的に変化する機能的傾斜材料(FGM)の製造に非常に有効です。
SPS炉の効率性とコンパクト性
SPS 炉は高効率でコンパクトに設計されているため、研究および工業用途の両方に最適です。SPS 炉のコンパクトな設計は必要な床面積を削減し、既存の生産ラインへの容易な統合を可能にします。さらに、SPS 炉の効率は急速な加熱・冷却が可能であることから向上し、省エネルギーと運転コストの削減に貢献します。黒鉛モールドと粉末ブリケットをジュール加熱する内部加熱機構により、均一な熱分布が確保され、熱損失が最小限に抑えられるため、焼結プロセスが最適化される。
精製と活性化焼結
SPSは、精製と活性化焼結の面でもユニークな利点を提供します。このプロセスでは、粒子表面から吸着ガスや酸化膜を除去できるため、界面が清浄になり、結合が改善されます。この浄化効果と粒子表面の活性化を組み合わせることで、他の方法では加工が困難な材料の焼結が可能になります。この機能により、高度なセラミックや複合材料など、SPSを使用して効果的に焼結できる材料の範囲が広がります。
結論として、スパークプラズマ焼結(SPS)には、材料加工に優れた選択肢となる多くの利点があります。その急速な焼結速度、微細粒焼結能力、密度と温度勾配の制御、効率性、コンパクト性により、研究用途と産業用途の両方において非常に貴重なツールとなっている。これらの利点を生かし、SPSは材料科学と工学の限界を押し広げ、革新的で高性能な材料の開発を可能にしています。
様々な産業におけるSPSの応用
スパークプラズマ焼結(SPS)技術は、様々な産業の製造プロセスに革命をもたらし、ユニークな特性を持つ先端材料の創出を可能にしました。SPSは、高密度で微細な材料を比較的低温で迅速に製造する能力で特に有名であり、ナノ材料、セラミックス、複合材料、医療用インプラントなどの合成に適した方法となっています。
ナノ材料
SPSの最も重要な用途の一つは、ナノ材料の調製である。ナノ材料は、粒径が小さいため強度や可塑性が向上し、卓越した機械的・物理的特性を示します。SPSは、焼結プロセス中の粒成長を抑制することで、これらの材料の合成を容易にします。SPS特有の急速加熱と短い焼結時間は、ナノ材料の性能にとって極めて重要なナノメートルスケールの粒径の維持に役立つ。この技術は、メカニカルアロイングなどの方法で得られた粉末の焼結に特に効果的で、従来の方法では圧密化が困難な場合が多い。
セラミックスとサーメット
SPSは、高密度で微細なセラミックスやサーメットの製造にも広く使用されています。各粉末粒子と粒子間の気孔が熱源となるSPSのユニークな加熱メカニズムは、迅速な緻密化と焼結時間と温度の大幅な低減を可能にします。この方法は、省エネルギーで生産効率が向上するため、工業生産に非常に有利です。高密度で微細な粒子構造を持つセラミックスを製造できるため、機械的強度と耐久性が向上し、さまざまなエンジニアリング用途に適している。
傾斜機能材料
特定の方向に勾配分布を持つ勾配機能材料も、SPSが大きく貢献している分野である。従来の焼結方法では、勾配材料の各層に必要な焼結温度の変化に苦労していた。しかし、SPSはこの勾配を効果的に管理できるため、このような複雑な材料を工業規模で生産することができる。SPSの制御された焼結プロセスは、構造全体の完全性を損なうことなく、各層が所望の特性を達成することを保証します。
医療用インプラント
医療分野では、SPSは機械的特性と生体適合性を調整したインプラントの製造に使用されています。焼結条件を精密に制御できるため、人骨に適合した特定の機械的特性を持つインプラントを作成することができ、機能性と寿命が向上します。さらに、SPSは骨の成長を促進する多孔質構造の製造にも利用でき、インプラントと周囲組織との一体化を向上させる。
複合材料とナノ構造材料
SPSは、磁気特性、圧電特性、熱電特性、光学特性などの特性を向上させた複合材料やナノ構造材料の製造に役立ちます。SPSの急速焼結プロセスは、材料のナノ構造を維持するのに役立ち、これは材料の性能にとって極めて重要です。例えば、SPSは、電界電子放出電極を開発するためにカーボンナノチューブの焼結に使用されており、様々な種類の材料を扱う際の汎用性を示している。
結論として、スパークプラズマ焼結は、様々な産業にまたがる用途を持つ、多用途で強力な技術として登場した。ユニークな特性を持つ高品質な先端材料を製造するその能力は、現代の製造業に不可欠なツールとなっている。この分野の研究開発が進むにつれて、SPSの潜在的な用途はさらに拡大し、材料科学と工学の革新を推進することが期待される。
ケーススタディSPSの成功事例
スパークプラズマ焼結(SPS)技術は、材料科学の分野に革命をもたらし、さまざまな材料の迅速な焼結と高密度化を可能にし、特性を向上させました。このセクションでは、SPSの多様性と有効性を実証するために、研究および産業環境の両方におけるSPSの成功事例を紹介します。
エネルギー貯蔵材料
SPSの最も重要な応用例の一つは、先進的なエネルギー貯蔵材料の開発である。例えば、SPSは性能を向上させた高容量リチウムイオン電池の製造に使用されている。焼結パラメーターを精密に制御することで、研究者たちは、より高いエネルギー密度とサイクル寿命の向上を実現した電池材料を作り出すことができた。研究によると、SPS処理されたリチウムイオン電池は、従来の方法と比較してエネルギー貯蔵容量が20%向上しており、電気自動車や携帯電子機器での使用に最適である。
生物医学工学
生体医工学の分野では、SPSは薬物送達用の多孔質セラミックや組織工学用の足場の作成に役立っている。これらの材料は、生体システムとの適合性を確保するために、微細構造を精密に制御する必要があります。SPSは、薬剤の効果的な送達や組織の成長に不可欠な、孔径を制御した高多孔質構造の作製を可能にする。例えば、SPS加工されたハイドロキシアパタイト・スカフォールドは骨組織工学に使用されており、従来の方法と比較して優れた生体適合性と機械的強度を示している。
先端セラミックス
SPSは、高温超伝導体や高性能圧電セラミックスなどの先端セラミックスの製造にも広く使用されています。これらの材料は、エネルギー伝送からセンサーやアクチュエーターに至るまで、幅広い用途に不可欠です。SPSは、これらのセラミックスのユニークな特性を維持したまま、より低温・短時間での緻密化を可能にする。例えば、イットリウム・バリウム・銅酸化物(YBCO)超電導体を理論密度に近い密度で製造するためにSPSが使用され、超電導転移温度が大幅に改善された。
金属間化合物と複合材料
SPSの多用途性は、金属間化合物や複合材料の加工においても実証されている。SPSは、機械的、熱的、電気的特性が改善された高度な合金を作るために使われてきた。例えば、SPSは、優れた高温強度と耐酸化性を示すチタンアルミナイド(TiAl)金属間合金の合成に採用されている。さらに、SPSは、セラミック粒子を埋め込んだチタンマトリックス複合材料のような、機械的特性を向上させた強化セラミックスや金属の製造を可能にし、高強度と耐摩耗性を持つ材料を生み出している。
工業用途
産業界では、磁性材料、硬質材料、傾斜機能材料など、さまざまな材料の製造にSPSが採用されている。例えば、太田精機のような日本の企業は、SPSを導入して100%WCの超硬材料の量産に成功し、国内外40社以上のメーカーに供給している。これらの材料は、切削工具から電子部品まで幅広い用途に使用されており、SPSの工業的拡張性を示している。
結論
ここで紹介したケーススタディは、エネルギー貯蔵から生体医工学、先端材料に至るまで、様々な分野におけるSPSの幅広い応用可能性を示している。SPSの低温での迅速な焼結と高密度化の能力は、精密なプロセス制御と相まって、材料科学者やエンジニアにとってかけがえのないツールとなっている。研究と開発が進むにつれて、SPSの潜在的な用途はさらに拡大し、材料加工をリードする技術としての地位が確固たるものになると期待されている。
SPSの課題と考察
スパークプラズマ焼結(SPS)技術の導入には、その利点を十分に活用するために組織が対処しなければならないいくつかの課題と考慮事項があります。例えば、設備コストの高さ、操作の複雑さ、専門的なトレーニングの必要性などである。SPS技術の統合と活用を成功させるには、これらの課題を理解し、克服するための戦略を立てることが重要です。
設備コスト
SPS技術導入の主な障壁の一つは、設備に必要な初期投資の高さである。SPSシステムは洗練されており、精密な温度・圧力制御、真空システム、特殊電源などの高度な機能を含んでいる。これらのコンポーネントは、初期費用を増加させるだけでなく、最適な性能を確保するために定期的なメンテナンスとキャリブレーションを必要とする。
操作の複雑さ
SPSの操作には、真空生成、圧力印加、抵抗加熱、制御された冷却など、複数の段階が含まれます。各段階では、欠陥を防ぎ、望ましい材料特性を確保するために、注意深い監視と調整が必要です。これらの操作は複雑であるため、高度な技術的専門知識と細部への細心の注意が必要となり、高度な焼結技術の経験がない組織にとっては困難な場合があります。
専門トレーニング
SPSの技術的性質を考慮すると、装置の操作と保守に携わる人員は、専門的な訓練を受けなければならない。このトレーニングは、SPSシステムの基本操作だけでなく、プロセスの最適化、トラブルシューティング、安全プロトコルなどの高度なトピックもカバーする必要がある。このトレーニングに必要なコストと時間は莫大なものとなり、SPS技術の導入を遅らせる可能性がある。
課題克服のための戦略
これらの課題を克服するために、組織はいくつかの戦略を採用することができる:
-
高品質設備への投資:高品質機器への投資:初期コストは高いが、信頼性が高く高品質なSPS機器に投資することで、長期的な保守・運用コストを削減することができる。また、強力なサポートとサービスネットワークを持つ信頼できるメーカーの機器を選択することで、運用中に発生する問題を軽減することができる。
-
コラボレーションとパートナーシップ:SPSの経験を持つ研究機関や他の企業と提携することで、貴重な見識やサポートを得ることができる。共同プロジェクトにより、導入の成功に必要なコストや専門知識を共有することができる。
-
継続的なトレーニングと開発:スタッフに対する継続的なトレーニングに投資することで、SPSの最新技術やベストプラクティスを常に把握することができる。これは、ワークショップ、オンラインコース、ハンズオントレーニングセッションを通じて達成することができる。
-
プロセスの最適化:十分に文書化され、標準化された強固なプロセスを開発することは、ばらつきを減らし、結果の一貫性を向上させるのに役立つ。これには、各素材や用途に最適な条件を特定するための入念な実験と検証が必要である。
-
研究開発の重視:継続的な研究開発に取り組むことは、組織がSPS技術の最前線に立ち続けるのに役立つ。これには、新素材の探求、既存プロセスの最適化、SPS製造部品の革新的用途の開発などが含まれる。
結論
SPS技術の導入にはいくつかの課題があるが、適切な戦略と投資によって、これらを効果的に管理することができる。高いコスト、操作の複雑さ、トレーニングの必要性などに対処することで、組織はSPSの潜在能力を最大限に引き出し、材料科学と製造の大幅な進歩につなげることができる。
スパークプラズマ焼結の将来動向
比較的低温での迅速な焼結で知られるスパークプラズマ焼結(SPS)技術は、効率性、拡張性、アプリケーションの多様性において大きな進歩を遂げ、進化し続けています。新素材や効率的な製造プロセスへの需要が高まる中、SPSは材料科学における技術革新の最前線に立っています。
効率の改善
SPS技術の主要な焦点のひとつは、効率の向上です。従来の焼結法では時間とエネルギーがかかるのに対し、SPSでは処理時間とエネルギー消費の両方が大幅に削減されます。今後の開発では、パルス電流技術を改良し、SPS装置の制御システムを改善することで、これらの点をさらに最適化することを目指している。例えば、電源と制御システムの進歩により、より精密な温度と圧力の制御が可能になり、より効率的な焼結プロセスにつながる可能性がある。
スケーラビリティの向上
スケーラビリティは、SPS技術のもう一つの重要な側面である。現在、SPSは実験室や小規模生産で主に使用されている。しかし、工業的な需要に応えるためには、将来のSPSシステムは、より大量の、より複雑な形状に対応する必要がある。研究者たちは、より高い圧力と温度に耐え、金型の完全性と再利用性を確保できる新しい金型材料と設計を模索している。さらに、SPS装置に高度なロボット工学と自動化を統合することで、より大型で複雑な部品の生産が容易になり、SPSが大量生産のための実行可能な選択肢となる可能性がある。
新しい材料と産業への拡大
SPS技術は従来、金属やセラミックの焼結に使用されてきた。しかし、そのユニークな能力は、新しい材料タイプや産業への拡大の可能性を提供する。今後の研究では、ポリマー、複合材料、ナノ材料など、より広範な材料へのSPSの適用に焦点が当てられると思われる。この拡大により、材料特性の精密な制御が重要なエレクトロニクス、航空宇宙、生物医学工学などの分野で、新たな用途が開かれる可能性がある。
環境および経済的メリット
SPSの環境的・経済的な利点も、今後の発展の原動力となっている。SPSのエネルギー効率に優れ、廃棄物の少ない製造工程は、世界的な持続可能性目標に合致している。産業界がますます環境に優しい製造ソリューションを求めるようになる中、SPSは高性能材料の製造方法として好まれるようになる可能性がある。さらに、SPSに関連する処理時間の短縮とエネルギーコストの低減は、大幅な経済的節約につながり、製造業者にとって魅力的な選択肢となる。
技術統合とコラボレーション
最後に、SPS 技術の将来は、他の先端製造技術との統合や、異分野間の協力的な取り組みが進むと思われる。例えば、SPSと積層造形技術を組み合わせることで、両技術の長所を活用したハイブリッド製造プロセスの創出につながる可能性がある。さらに、材料科学、電気工学、機械工学を含む学際的研究は、SPSプロセスの理解と最適化におけるブレークスルーをもたらす可能性がある。
結論として、スパークプラズマ焼結の将来は有望であり、より効率的でスケーラブルかつ汎用性の高い技術へと進化する可能性がある。研究と開発が進めば、SPSは先端材料の製造方法に革命をもたらし、さまざまな産業分野のイノベーションに貢献し、持続可能な製造方法を促進する可能性がある。
結論材料科学の形成におけるSPSの役割
結論としてスパークプラズマ焼結(SPS) 技術は、材料科学の分野で変革をもたらす技術として際立っている。微細粒レベルの材料を迅速に焼結するその能力は、効率性と汎用性と相まって、SPSを現代の材料加工における礎石として位置づけている。将来に向けて、SPSは重要なイノベーションを推進し、様々な産業への応用を拡大し、高度で高性能な材料開発への道を切り開く態勢が整っている。SPS技術の継続的な進化と採用は、間違いなく材料科学の未来を形成し、複雑な材料課題に対する新たな可能性と解決策を提供するでしょう。
無料相談はお問い合わせください
KINTEK LAB SOLUTION の製品とサービスは、世界中のお客様に認められています。弊社スタッフがどんなご質問にも喜んで対応させていただきます。無料相談にお問い合わせいただき、製品スペシャリストにご相談いただき、アプリケーションのニーズに最適なソリューションを見つけてください。