浸炭プロセスは鋼部品の表面硬化に広く使用されていますが、使用する方法 (雰囲気浸炭または真空浸炭) に応じていくつかの欠点があります。これらには、高い初期資本コスト、経験的なプロセス制御の必要性、環境と安全性への懸念、機器のメンテナンスと後処理に関連する課題が含まれます。各方法には、真空浸炭におけるすすやタールの生成、雰囲気浸炭における浸炭深さの品質問題など、特有の欠点があります。機器や消耗品の購入者が情報に基づいた意思決定を行うには、これらの欠点を理解することが重要です。
重要なポイントの説明:
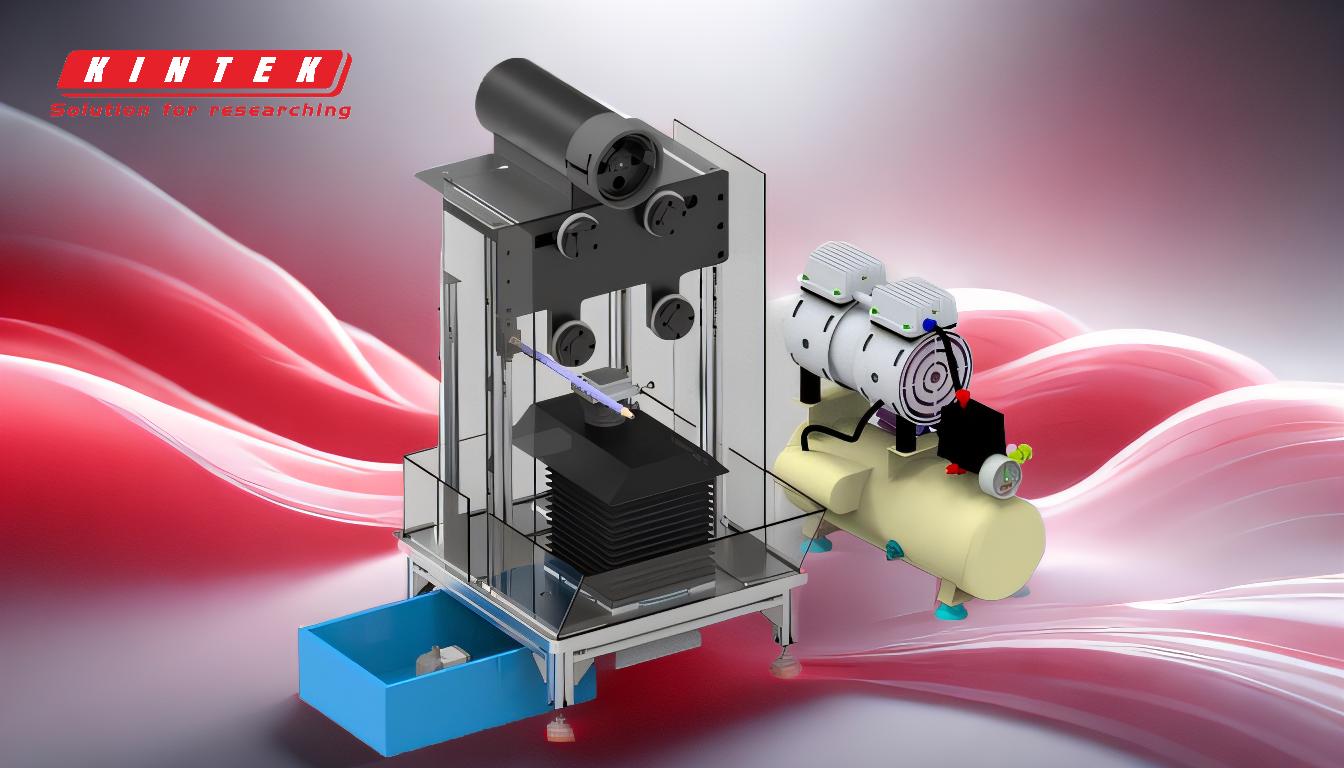
-
初期資本設備コストが高い:
- 説明: 真空浸炭には特殊な設備が必要であり、従来の雰囲気浸炭に比べて初期投資が高額になることがよくあります。これには、高度な真空チャンバー、ガス処理システム、正確な温度制御メカニズムが含まれます。
- インパクト :企業にとって、これは多額の資金を前払いすることを意味しますが、小規模な事業や予算が限られている事業では実現できない可能性があります。
-
経験的プロセス制御:
- 説明: 雰囲気浸炭と真空浸炭はどちらも、再現可能な結果を達成するために経験的データに大きく依存しています。これは、オペレーターが豊富な経験を持ち、特定の負荷ごとに最適な設定を決定するために多数の試運転を実施する必要があることを意味します。
- インパクト: この試行錯誤への依存は、熟練した人材の必要性とテスト中の材料の無駄の可能性により、非効率性、生産時間の増加、およびコストの増加につながる可能性があります。
-
ススとタールの生成(真空浸炭):
- 説明: 真空浸炭では、導入される炭化水素ガスの種類、圧力、量により、すすやタールが発生する可能性があります。これらの副産物は、処理中の機器や部品を汚染する可能性があります。
- インパクト :これにより、機器の頻繁な清掃とメンテナンスが必要となり、ダウンタイムと運用コストが増加します。さらに、すすやタールの存在は浸炭層の品質に影響を与える可能性があり、部品の手戻りや廃棄につながる可能性があります。
-
装置コンディショニング(雰囲気浸炭):
- 説明: 雰囲気浸炭装置は、一定期間アイドリングまたは停止した場合、適切に調整する必要があります。これには、システムをパージし、動作を再開する前に雰囲気が正しくバランスされていることを確認することが含まれます。
- インパクト: この要件は、特に装置が頻繁に停止および起動される場合、生産の遅延につながる可能性があります。また、運用が複雑になり、メンテナンスに追加のリソースが必要になります。
-
後処理のための材料許容量が大きい:
- 説明: どちらの方法でも、研削や機械加工などの後処理操作に対応するために、多くの場合、大幅な材料許容値が必要になります。これは浸炭後の最終寸法と表面仕上げを達成するために必要です。
- インパクト :これにより材料費が増加し、廃棄物の発生量が増加する可能性があり、長期的には持続可能でなく、費用対効果も高くない可能性があります。
-
ケースの深さの品質の問題:
- 説明: 大気浸炭では、大気中の炭素ポテンシャルやその他のプロセス変数が変化するため、一貫した浸炭深さを達成することが困難になる場合があります。
- インパクト: ケース深さが一貫していない場合、部品が仕様を満たさず、再加工、廃棄、さらにはサービスの失敗につながる可能性があります。この変動により、品質管理プロセスが複雑になる場合もあります。
-
環境汚染と安全性への懸念:
- 説明: 雰囲気浸炭には潜在的に有害なガスが使用されるため、環境汚染を防止し、職場の安全を確保するために常に監視する必要があります。
- インパクト :これにより、運用上の負担が増大し、安全装置への投資、トレーニング、環境規制への準拠が必要になります。これらの側面を適切に管理しないと、罰金、法的問題が発生し、会社の評判が損なわれる可能性があります。
要約すると、浸炭は鋼部品の表面特性を向上させる効果的な方法ですが、慎重に考慮する必要があるいくつかの欠点があります。これらには、高い初期コスト、経験的なプロセス制御の必要性、環境と安全性への懸念、装置のメンテナンスと後処理に関連する課題が含まれます。これらの欠点を理解することは、浸炭プロセスを選択して実装する際に情報に基づいた意思決定を行うために不可欠です。
概要表:
短所 | 方法 | インパクト |
---|---|---|
初期資本設備コストが高い | 真空浸炭 | 多額の先行投資が必要で、小規模な運用には困難 |
経験的プロセス制御 | 両方の方法 | 熟練した人材、試行錯誤、生産時間の増加が必要 |
煤とタールの生成 | 真空浸炭 | 頻繁な洗浄、機器の汚染、部品の手直しの可能性 |
機器のコンディショニング | 雰囲気浸炭 | 生産の遅延と運用の複雑さの増加 |
多額の材料費手当 | 両方の方法 | 材料費の増加と廃棄物の発生量の増加 |
ケースの深さの品質の問題 | 雰囲気浸炭 | 一貫性のない結果、部品のやり直し、または廃棄 |
環境汚染 | 雰囲気浸炭 | 安全上の懸念、規制遵守、罰金の可能性 |
適切な表面硬化プロセスの選択にサポートが必要ですか? 今すぐ専門家にお問い合わせください カスタマイズされたソリューションを実現します。