蒸着成長は、気相から材料を堆積させることによって、基板上に薄膜やコーティングを作成するために使用されるプロセスである。この技術は、半導体、光学、保護膜などの産業で広く使用されている。このプロセスは大きく2つのタイプに分類できる:化学気相成長法(CVD)と物理気相成長法(PVD)である。CVDは化学反応によって気相を生成し、PVDは蒸発やスパッタリングなどの物理的プロセスに依存する。どちらの方法にも明確なステップとメカニズムがありますが、高品質で均一な密着性の高い薄膜を作るという共通の目標があります。CVDとPVDのどちらを選択するかは、具体的な用途、希望する膜特性、関係する材料によって異なります。
主なポイントの説明
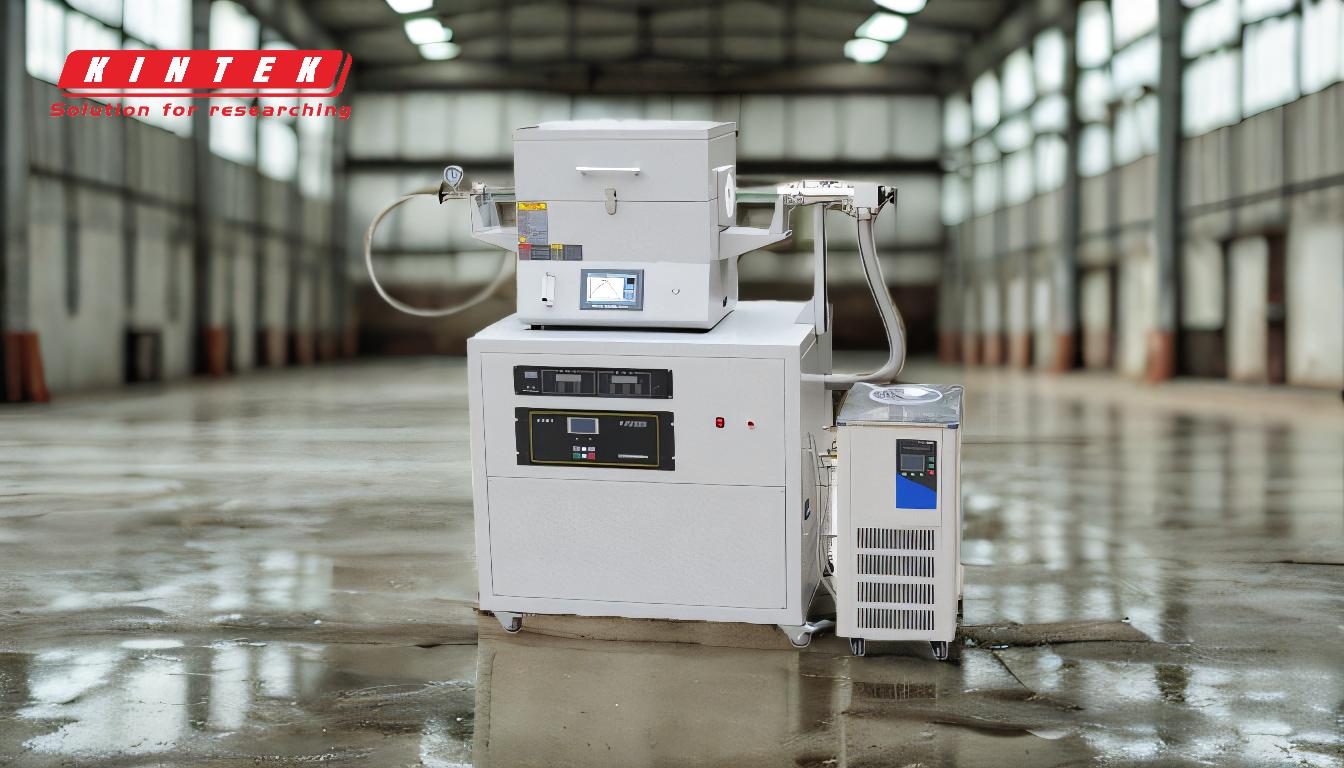
-
化学気相成長法(CVD):
- プロセスの概要: CVDでは、揮発性の前駆体を使用し、化学反応によって基板上に固体材料を形成する。このプロセスは通常、高温高圧の制御された環境で行われる。
-
関与するステップ
- 反応ガスの輸送: ガス種は基材表面に輸送される。
- 吸着: ガスが基材表面に吸着する。
- 表面反応: 熱やプラズマによって表面で化学反応が起こり、目的の膜が形成される。
- 核生成と成長: 反応生成物が基材上に蓄積するにつれて膜が核生成し、成長する。
- 脱着と除去: 反応の副生成物を脱着し、チャンバーから除去する。
- 利点 CVDは、化学量論的で高密度、高品質の膜を作ることができる。成膜時間と電力を調整することで、膜厚を精密に制御できる。
-
物理蒸着(PVD):
- プロセスの概要: PVDには、ソースから基板への材料の物理的な移動が含まれる。これは、蒸発やスパッタリングなどのプロセスによって達成される。
-
含まれるステップ
- 蒸発: 原料が加熱されるか、高エネルギーイオンが照射され、気化する。
- 輸送: 気化した原子は真空チャンバーを通って基板に移動する。
- 反応: 反応性PVDでは、気化した原子がチャンバー内に導入されたガスと反応して、酸化物、窒化物、炭化物などの化合物を形成することがある。
- 蒸着: 原子または化合物が基板上に堆積し、薄膜を形成する。
- 利点 PVDは、金属、合金、セラミックなど、幅広い材料の成膜を可能にする。このプロセスは真空下で行われるため、汚染が最小限に抑えられ、高純度の膜が得られます。
-
熱蒸着:
- プロセスの概要: PVDのサブセットで、原料を加熱して蒸気を発生させ、基板上で凝縮させる。
- 温度範囲: 通常、原料は250~350℃に加熱される。
- 応用: この方法は、比較的低温で気化しやすい材料に特に有効である。
-
エアロゾルデポジション:
- プロセスの概要: この方法では、微細なセラミック粒子が高速で加速され、基材と衝突して緻密なコーティング層が形成されます。
- 利点 追加の熱処理を必要としないため、エネルギー効率が高く、温度に敏感な基板に適している。
-
スパッタリング
- プロセスの概要 スパッタリングでは、ターゲット材料に高エネルギーのイオンを照射し、原子を基板上に放出・堆積させる。
- 利点: この方法は汎用性が高く、金属、半導体、絶縁体など幅広い材料の成膜に使用できる。
-
CVDとPVDの比較
- CVD: 高品質で化学量論的な膜を、膜厚を正確に制御して製造するのに適している。ただし、より高温で複雑な装置を必要とすることが多い。
- PVD: 成膜可能な材料の点で汎用性が高く、一般的に低温で作動する。また、純金属や合金の蒸着にも適している。
結論として、蒸着成長プロセスは現代の製造および材料科学において重要な技術である。CVDであれPVDであれ、薄く均一で高品質な膜を作る能力は、エレクトロニクスから保護膜まで、幅広い用途に不可欠である。各手法の具体的な手順と利点を理解することで、用途に応じて最適な手法を選択することができる。
要約表
方法 | プロセスの概要 | 利点 |
---|---|---|
化学気相成長法(CVD) | 化学反応を利用して基板上に固体膜を形成する。高温・高圧が必要。 | 精密な膜厚制御により、化学量論的、高密度、高品質の膜が得られる。 |
物理蒸着(PVD) | 蒸発やスパッタリングのような物理的プロセスに頼って材料を基板に転写する。 | 金属、合金、セラミックを真空下で最小限のコンタミネーションで蒸着する。 |
熱蒸着 | 原料を加熱して蒸気を発生させ、基板上で凝縮させる。 | 低温(250~350℃)で気化する材料に最適。 |
エアロゾル蒸着 | 微細なセラミック粒子を加速し、熱処理なしで緻密なコーティングを形成。 | エネルギー効率が高く、温度に敏感な基板に適しています。 |
スパッタリング | ターゲット材料に高エネルギーのイオンをぶつけて原子を放出させ、成膜する。 | 汎用性が高く、金属、半導体、絶縁体の蒸着が可能。 |
お客様のアプリケーションに最適な蒸着方法を見つけてください。 今すぐ専門家にお問い合わせください !