プラズマ蒸着、特にプラズマエンハンスト化学気相成長法(PECVD)のようなプロセスは、従来の化学気相成長法(CVD)に比べてかなり低い温度で作動する。CVDは通常1000℃前後の温度を必要とするが、プラズマ蒸着は200~400℃とはるかに低い温度で同様の結果を得ることができる。これは、熱エネルギーだけに頼ることなく、プラズマが化学反応を活性化するのに必要なエネルギーを提供するためである。低温域は、ポリマーや特定の金属など、高温に耐えられない基材にとって有益である。さらに、プラズマを使用することで、フィルム特性の制御が容易になり、CVDのような高温プロセスで一般的な問題である熱応力が軽減される。
キーポイントの説明
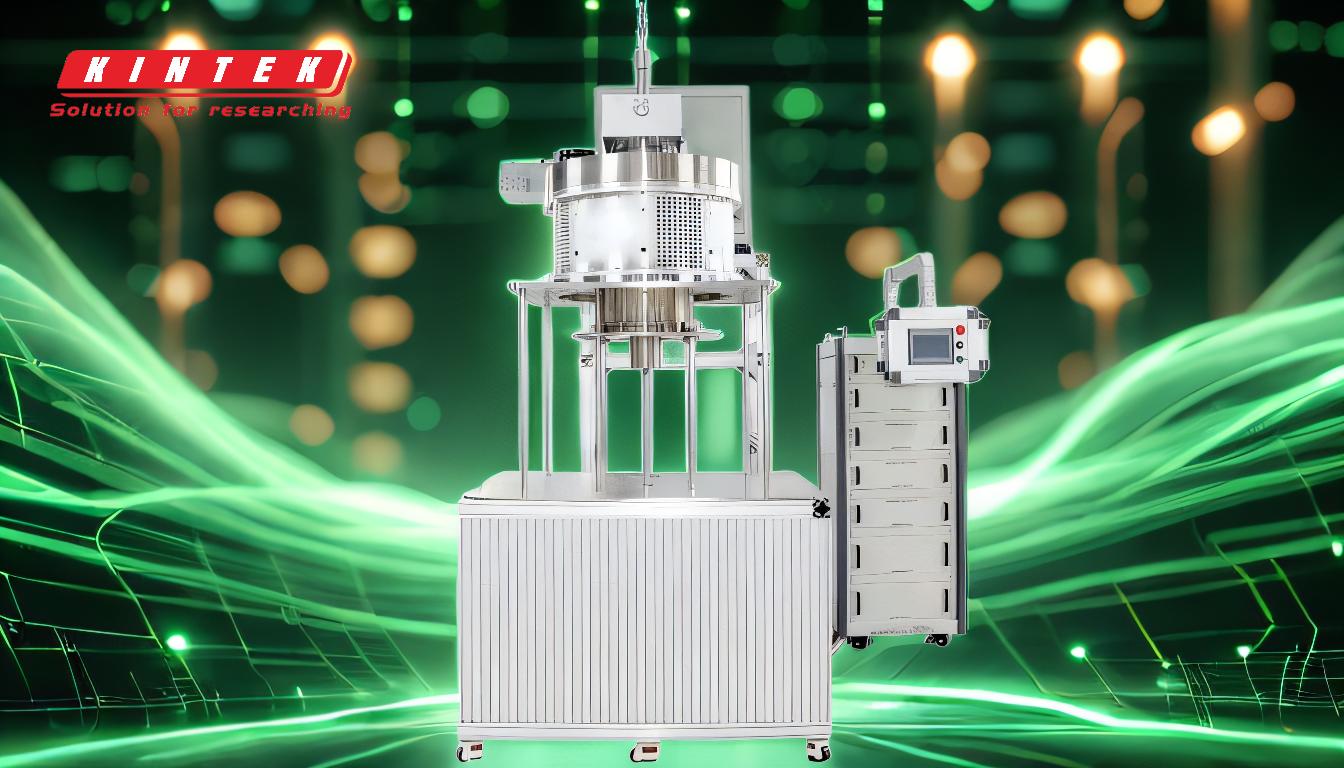
-
プラズマ蒸着における温度範囲:
- PECVDを含むプラズマ蒸着は、通常200~400℃の温度で作動する。これは、従来の化学蒸着に必要な1000℃よりもかなり低い温度である。 化学気相成長 (CVD)である。
- 低温化は、熱エネルギーだけに頼るのではなく、化学反応に必要なエネルギーをプラズマで供給することで達成される。
-
低温の利点:
- 基板適合性:ポリマーや特定の金属など、多くの基材はCVDに必要な高温に耐えられない。プラズマ蒸着は、これらの材料にダメージを与えることなくコーティングすることを可能にします。
- 熱応力の低減:高温は、基板と蒸着膜の熱膨張率の違いにより、熱応力を引き起こす可能性があります。プラズマ蒸着では温度が低いため、この問題が最小限に抑えられ、膜の密着性が向上し、欠陥が少なくなる。
-
CVDとの比較:
- 温度:CVDプロセスは通常1000℃前後の温度を必要とし、これはプラズマ蒸着の200~400℃の範囲よりはるかに高い。
- エネルギー源:CVDでは、熱エネルギーが化学反応の原動力となるが、プラズマ蒸着では、エネルギーがプラズマから供給されるため、低温化が可能となる。
- 応用例:プラズマ蒸着の温度範囲が低いため、温度に敏感な材料を含む幅広い用途に適している。
-
熱応力の考慮:
- CVDでは、特に成膜後の冷却段階において、熱応力が大きな問題となる。基板と膜の熱膨張係数の差は、クラックや剥離につながる可能性がある。
- プラズマ蒸着は、より低い温度で操作することで熱応力のリスクを低減し、熱膨張のミスマッチを最小限に抑え、より安定した膜を得ることができます。
-
プロセス制御と膜特性:
- 成膜プロセスにプラズマを使用することで、膜厚、均一性、組成などの膜特性をよりよく制御することができる。
- また、温度が低いため、成膜プロセスをより正確に制御することができ、不要な副反応や基板の劣化の可能性を減らすことができる。
まとめると、プラズマ成膜は従来のCVDに代わる低温成膜法であり、より幅広い材料や用途に適している。エネルギー源としてプラズマを使用することで、成膜プロセスを正確に制御することができ、その結果、熱応力を最小限に抑えた高品質の膜が得られる。このため、温度に敏感な基材へのコーティングを必要とする産業にとって、プラズマ蒸着は魅力的な選択肢となっている。
総括表
側面 | プラズマ蒸着 | 従来のCVD |
---|---|---|
温度範囲 | 200-400°C | ~1000°C |
エネルギー源 | プラズマ | 熱エネルギー |
基板適合性 | ポリマー、金属 | 高温による制限 |
熱応力 | 最小 | ハイリスク |
アプリケーション | 広範で敏感な材料 | 高温材料 |
プラズマ蒸着がお客様の材料コーティングプロセスをどのように強化できるかをご覧ください。 今すぐお問い合わせください !