プラズマ アーク炉は、材料、特に金属や合金の溶解および加工に使用される高温装置です。プラズマ アーク炉内の温度は非常に高いレベルに達することがあり、多くの場合 15,000 ケルビン (K) を超えます。これは従来の電気アーク炉よりも大幅に高くなります。この高温はプラズマ アーク トーチを使用することで達成され、プラズマ アーク トーチは、最も耐火性の高い材料でも溶解できる集中した強力な熱源を生成します。
重要なポイントの説明:
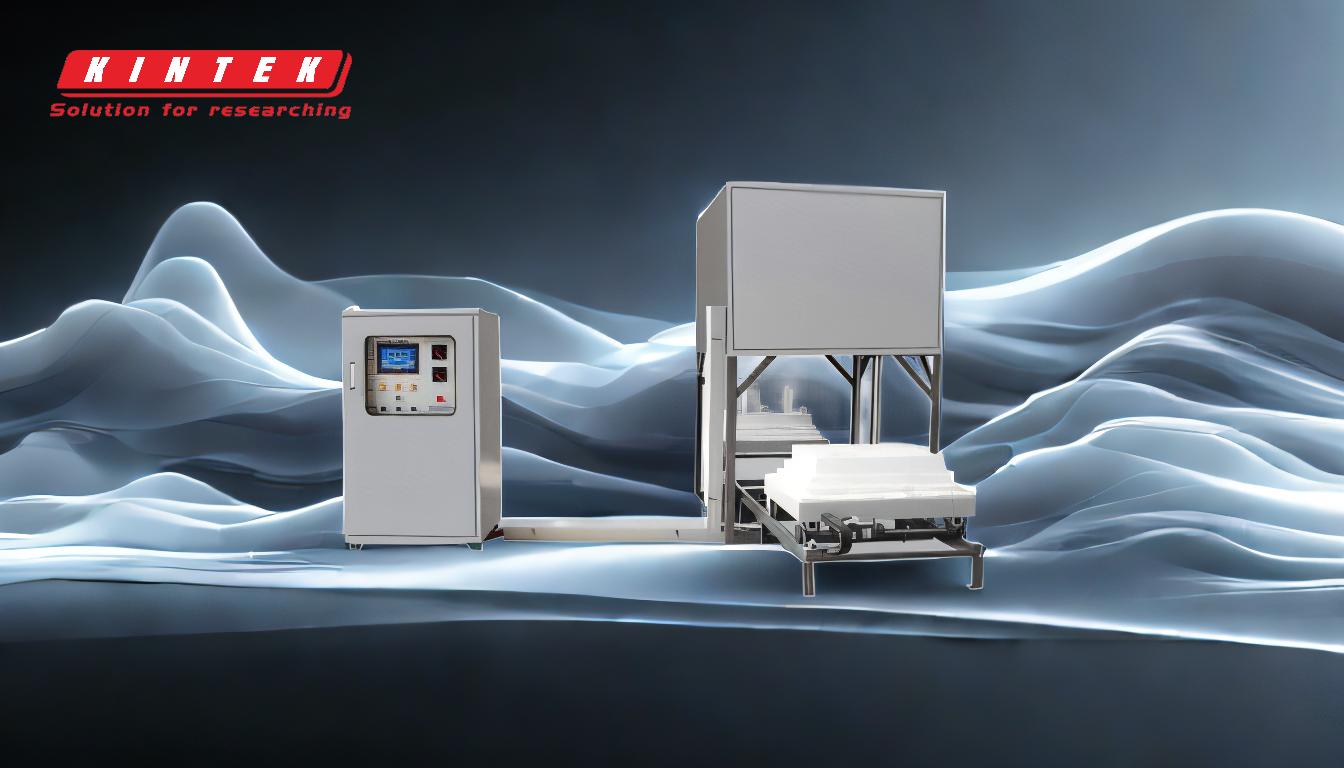
-
プラズマアーク炉の温度範囲:
- プラズマ アーク炉内の温度は、 15,000K 、参考文献に記載されているように。これは、ガスをイオン化してプラズマを形成することによって生成されるプラズマ アークのエネルギーが非常に集中しているためです。プラズマ アーク溶解炉 (PAM) のプラズマ アーク トーチは、これらの極端な温度を達成するように特別に設計されており、非常に高い熱を必要とする材料の溶解および処理に適しています。
-
電気炉との比較:
- 対照的に、従来の電気炉は通常、100℃を超える温度で動作します。 3000℃ (約3273K)。これは依然として非常に高いですが、プラズマ アーク炉で達成可能な温度よりも大幅に低いです。違いはエネルギー密度と熱の発生方法にあります。電気アーク炉は電極間の放電に依存しますが、プラズマ アーク炉はイオン化ガスを使用してより強力で集中した熱源を生成します。
-
プラズマアーク炉の応用例:
-
プラズマ アーク炉は極めて高温であるため、次のような特殊な用途に最適です。
- 高融点金属 (タングステン、モリブデン、チタンなど) の溶解。
- セラミックや複合材料などの先端材料の加工。
- 高価値金属のリサイクルと精製。
- これらの用途では、従来の炉では達成できない温度が必要になることがよくあります。
-
プラズマ アーク炉は極めて高温であるため、次のような特殊な用途に最適です。
-
プラズマアーク炉の利点:
- 高精度: 集中した熱源により、溶解プロセスを正確に制御し、材料の無駄を削減します。
- 多用途性 :非常に高融点の材料を含む幅広い材料の処理が可能です。
- 効率: プラズマ アークのエネルギー密度が高いため、他のタイプの炉と比較して溶解時間が短縮されます。
-
課題と考慮事項:
- エネルギー消費量: プラズマ アーク炉は高温を維持するために大量のエネルギー投入を必要とし、これが一部の用途では制限要因となる可能性があります。
- 設備費: プラズマ アーク炉には高度な技術と材料が必要とされるため、従来の炉よりも高価になります。
- 運用の複雑さ: 高温と特殊なプロセスには、熟練したオペレーターと慎重なメンテナンスが必要です。
-
今後の動向:
- プラズマ アーク技術の進歩により、エネルギー効率が向上し、運用コストが削減されることが期待されています。さらに、新しい材料や用途の開発により、航空宇宙、エレクトロニクス、再生可能エネルギーなどの業界でプラズマ アーク炉の使用が拡大すると考えられます。
プラズマ アーク炉の詳細については、次のトピック ページを参照してください。 プラズマアーク炉 。
概要表:
特徴 | プラズマアーク炉 | 電気炉 |
---|---|---|
温度範囲 | 15,000Kを超える | 3000℃以上 (~3273 K) |
熱源 | プラズマアークトーチ | 放電 |
アプリケーション | 高融点金属、セラミックス | 金属溶解全般 |
利点 | 高精度、多用途性 | 費用対効果の高い |
課題 | 高いエネルギー消費 | より低い温度範囲 |
材料の極度の熱の可能性を解き放ちます— 今すぐ専門家にお問い合わせください !