セラミックスのホットプレス工程では、セラミック粉末に熱と圧力を同時に加えて緻密化と形状形成を行います。この方法は、機械的特性が向上した高密度で微細なセラミック材料を製造するのに特に効果的です。このプロセスには通常、粉末の準備、金型への充填、加熱、加圧、冷却、後処理といった複数の段階が含まれます。熱と圧力を組み合わせることで、熱間プレスは気孔率を減らし、セラミックの微細構造を改善し、高い強度と耐久性を必要とする用途に適しています。
キーポイントの説明
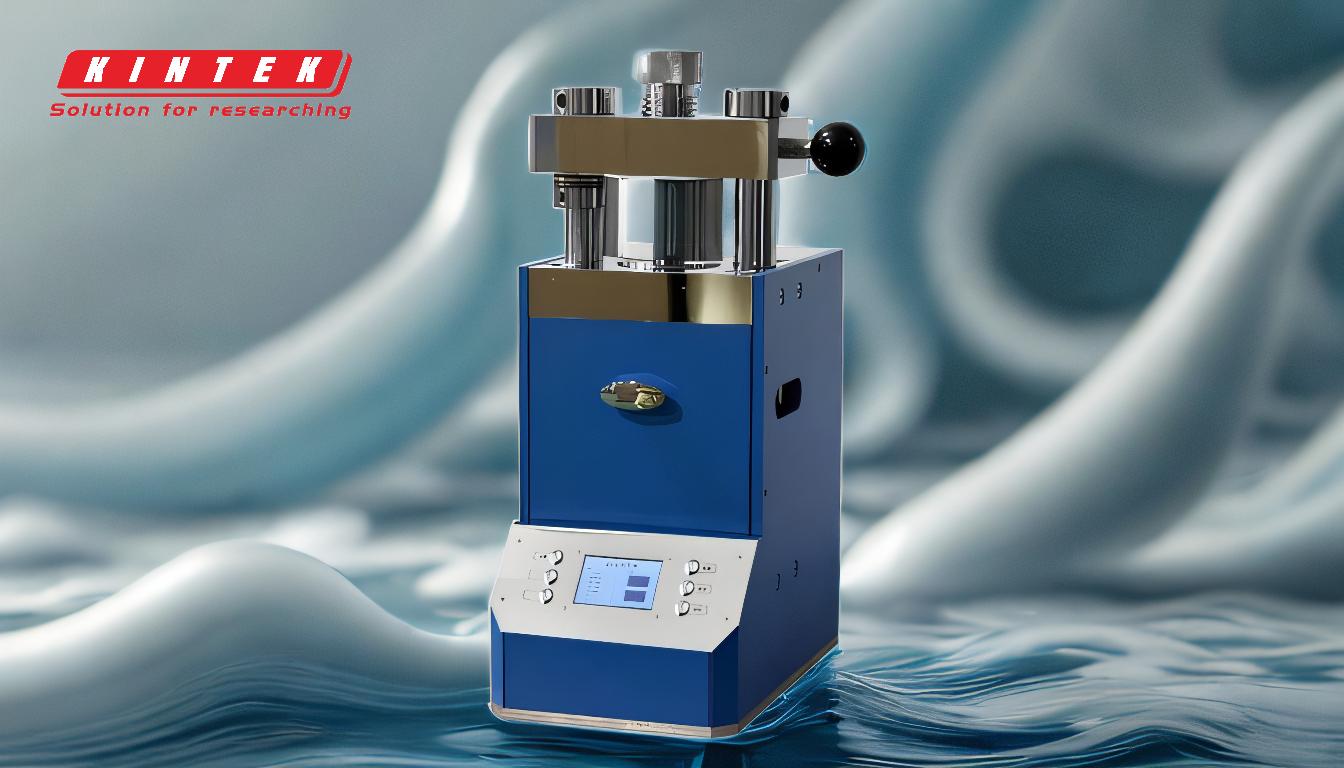
-
パウダーの準備:
- この工程はセラミック粉末の調製から始まり、この粉末は多くの場合、細粒で均質である。粉末は、流動性と圧縮性を向上させるために、結合剤や添加剤と混合されることがあります。
- 適切な粉体調製により、ホットプレス工程で均一な密度が得られます。
-
ダイフィリング:
- 準備されたセラミック粉末は、一般的にグラファイトなどの耐高温材料で作られた金型に装填される。ダイは、プロセスで使用される高温・高圧に耐えられるよう設計されています。
- ダイへの均一な充填は、一貫した高密度化を達成し、最終製品の欠陥を避けるために非常に重要です。
-
加熱:
- セラミック粉末を入れた金型はホットプレス炉に入れられ、セラミック材料にもよりますが、通常1000℃から2000℃の温度まで加熱されます。
- 均質な微細構造を実現するために不可欠な均一な温度分布を確保するため、加熱プロセスは慎重に制御されます。
-
プレス:
- 所望の温度に達したら、油圧または機械的手段を用いてセラミック粉末に圧力を加える。圧力は数MPaから数百MPaの範囲に及ぶ。
- 熱と圧力の組み合わせは、粒子の再配列、塑性変形、拡散を促進し、緻密化と空隙の除去につながる。
-
冷却:
- プレス工程の後、セラミックは室温までゆっくりと冷却されます。制御された冷却は、熱応力やクラックを防ぐために重要です。
- 冷却速度は、特定のセラミック材料とその熱特性に応じて調整することができます。
-
後処理:
- ホットプレスされたセラミックは、所望の最終寸法や表面仕上げを達成するために、機械加工、研磨、表面処理などの後処理工程が追加される場合があります。
- 後処理により、セラミック部品が意図された用途に必要な仕様を満たすことが保証されます。
-
ホットプレスの利点:
- ホットプレスは、高密度で微細な粒径を有し、強度、硬度、耐摩耗性などの機械的特性が改善されたセラミックスの製造を可能にする。
- このプロセスは、従来の焼結法では緻密化が困難な材料に特に有効です。
-
応用例:
- ホットプレスセラミックスは、切削工具、耐摩耗部品、電子基板、生体インプラントなど、幅広い用途に使用されています。
- ホットプレス・セラミックスの強化された特性は、高い性能と信頼性が要求される厳しい環境に適しています。
これらの手順を踏むことで、熱間プレス工程は優れた特性を持つ高品質のセラミック材料の製造を可能にし、先端セラミック製造における貴重な技術となっています。
総括表
ステージ | ステージ |
---|---|
粉末の調製 | 微粒子セラミックパウダーは、多くの場合、流動性を良くするためにバインダーを使用して調製されます。 |
ダイ充填 | 粉体を高温に耐える金型に充填し、均一な密度を得る。 |
加熱 | 金型を1000℃~2000℃に加熱し、均一な温度分布にする。 |
プレス | 圧力(MPa)をかけて空隙をなくし、緻密化する。 |
冷却 | 制御された冷却により、熱応力やひび割れを防ぎます。 |
後加工 | 機械加工、研磨、表面処理により、最終仕様を保証します。 |
利点 | 高密度、細粒度、優れた機械的特性。 |
用途 | 切削工具、耐摩耗部品、電子基板、インプラント。 |
熱間プレスによるセラミック製造の強化方法について、詳しくは以下をご覧ください。 今すぐ専門家にお問い合わせください !