化学的気相成長法(CVD)と物理的気相成長法(PVD)は、半導体、光学、コーティングなど、さまざまな産業で使用されている2つの著名な薄膜蒸着技術である。どちらの手法も基板上に薄膜を堆積させることを目的としているが、そのメカニズム、操作条件、結果において根本的に異なっている。CVDは、ガス状の前駆物質と基板との化学反応によって固体皮膜を形成するため、多方向への成膜が可能で、複雑な形状にも対応できる。一方、PVDは、固体材料を物理的に気化させ、基板上にライン・オブ・サイト方式で凝縮させるため、精密で薄く、耐久性のあるコーティングを必要とする用途に適している。CVDとPVDのどちらを選択するかは、基材の材質、希望するコーティング特性、運用上の制約などの要因によって決まる。
キーポイントの説明
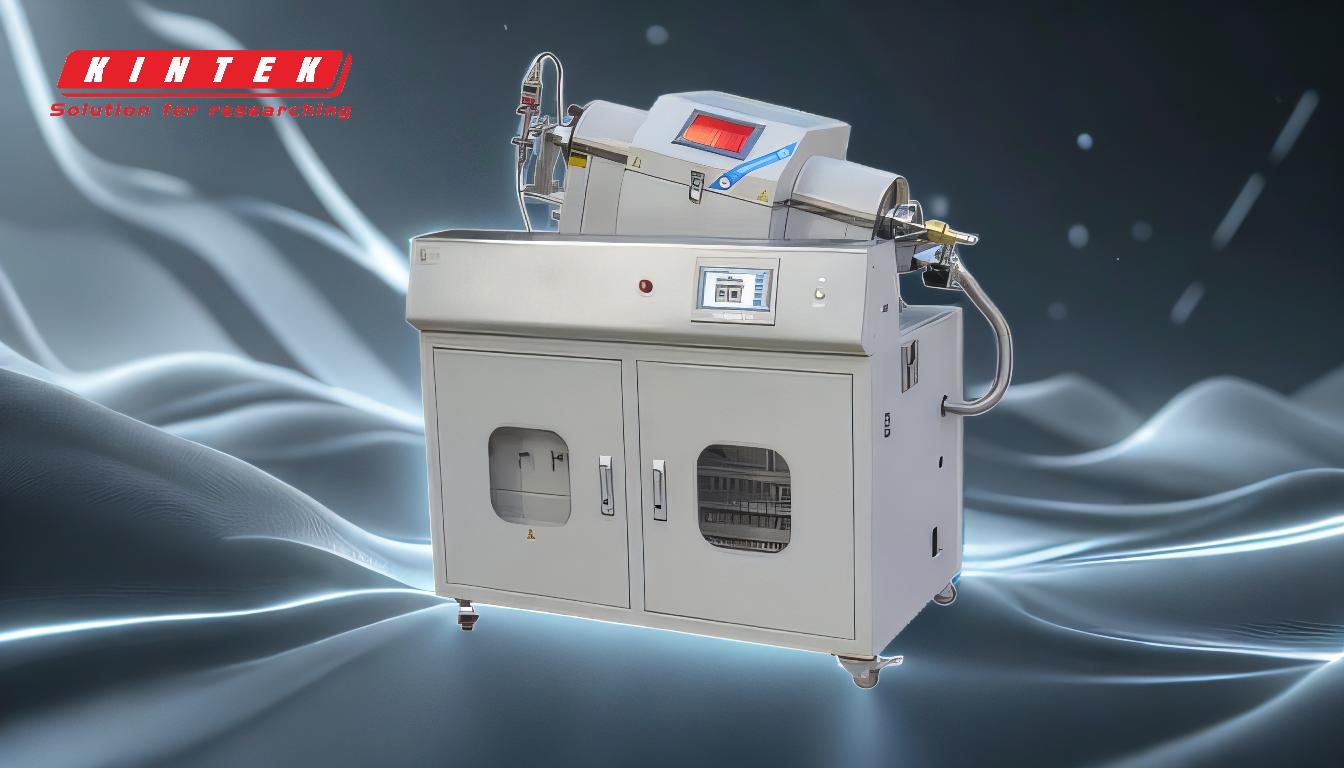
-
成膜メカニズム:
- CVD:ガス状前駆体と基材表面の化学反応を伴う。このプロセスは多方向性であり、複雑な形状、深い凹部、穴の均一なコーティングを可能にする。
- PVD:スパッタリングや蒸発などの物理的プロセスによって固体材料を気化させ、基板上に凝縮させる。このプロセスは視線方向のプロセスであるため、視線方向以外の領域へのコーティングには限界がある。
-
使用温度:
- CVD:一般的に高温(450℃~1050℃)で使用されるため、温度に敏感な基材への使用が制限されることがある。また、高温は化学反応を促進するが、不純物が混入する可能性がある。
- PVD:より低い温度(250℃~450℃)で動作するため、温度に敏感な素材に適している。また、基材への熱損傷のリスクも低減します。
-
コーティング材料:
- CVD:主にセラミックやポリマーの成膜に用いられる。プロセスの化学的性質により、幅広い材料組成に対応できる。
- PVD:金属、合金、セラミックスなど、より幅広い材料を成膜できる。この汎用性により、PVDは多様な用途に適しています。
-
コーティング特性:
- CVD:密着性に優れ、緻密で均一な高品質のコーティングができる。ただし、プロセスが遅くなり、表面が粗くなることがある。
- PVD:高精度で、薄く、滑らかで、耐久性のあるコーティングが得られる。CVDに比べ、コーティングの緻密さや均一性は劣るが、多くの場合、短時間で塗布できる。
-
用途:
- CVD:半導体製造や工具コーティングなど、厚膜で複雑な形状のコーティングが必要な用途に最適。
- PVD:光学コーティング、装飾仕上げ、耐摩耗層など、精密で薄く、耐久性のあるコーティングが必要な用途に最適。
-
利点と限界:
- CVDの利点:高い投射力、複雑な形状のコーティングが可能、厚膜コーティングが可能で経済的。超高真空は不要。
- CVDの限界:動作温度が高い、腐食性副生成物の可能性がある、場合によっては成膜速度が遅い。
- PVDの利点:動作温度が低く、腐食性の副生成物がなく、材料の利用効率が高い。
- PVDの限界:また、成膜速度は一般にCVDよりも低い。
まとめると、CVDとPVDのどちらを選択するかは、基材の材質、希望するコーティング特性、運用上の制約など、アプリケーションの具体的な要件によって決まる。CVDは複雑な形状のコーティングや厚く均一な膜を作るのに優れており、PVDは温度に敏感な素材への精密で薄く耐久性のあるコーティングに適している。
総括表
側面 | CVD | PVD |
---|---|---|
成膜メカニズム | ガス状前駆体と基板との化学反応 | 固体材料の物理的気化、基板上への凝縮 |
使用温度 | 高温 (450°C~1050°C) | 低~中温 (250°C~450°C) |
コーティング材料 | セラミックス、ポリマー | 金属、合金、セラミックス |
コーティング特性 | 緻密、均一、高品質 | 薄い、滑らか、耐久性 |
用途 | 半導体製造、工具コーティング | 光学コーティング、装飾仕上げ、耐摩耗層 |
利点 | 複雑な形状のコーティングが可能。 | 低温、腐食性の副生成物なし |
制限事項 | 高温、蒸着速度低下、不純物の可能性 | 直視蒸着、複雑な形状での均一性の低下 |
どの蒸着プロセスがお客様の用途に適しているか、まだご不明ですか? 当社の専門家にご連絡ください。 にお問い合わせください!