物理的気相成長法(PVD)と化学的気相成長法(CVD)は、基板上に薄膜を堆積させるために広く使われている2つの技術である。PVDは、蒸発やスパッタリングなどの物理的プロセスによって固体材料を蒸気に変え、基板上に凝縮させる。これに対してCVDは、気体状の前駆物質を含む化学反応を利用して基板上に固体膜を形成する。PVDが低温で作動し、腐食性の副生成物を避けるのに対し、CVDは複雑な形状の均一なコーティングと高い成膜速度を可能にする。どちらの方法も、半導体、光学、コーティングなどの産業で不可欠であり、用途に応じて独自の利点を提供します。
キーポイントの説明
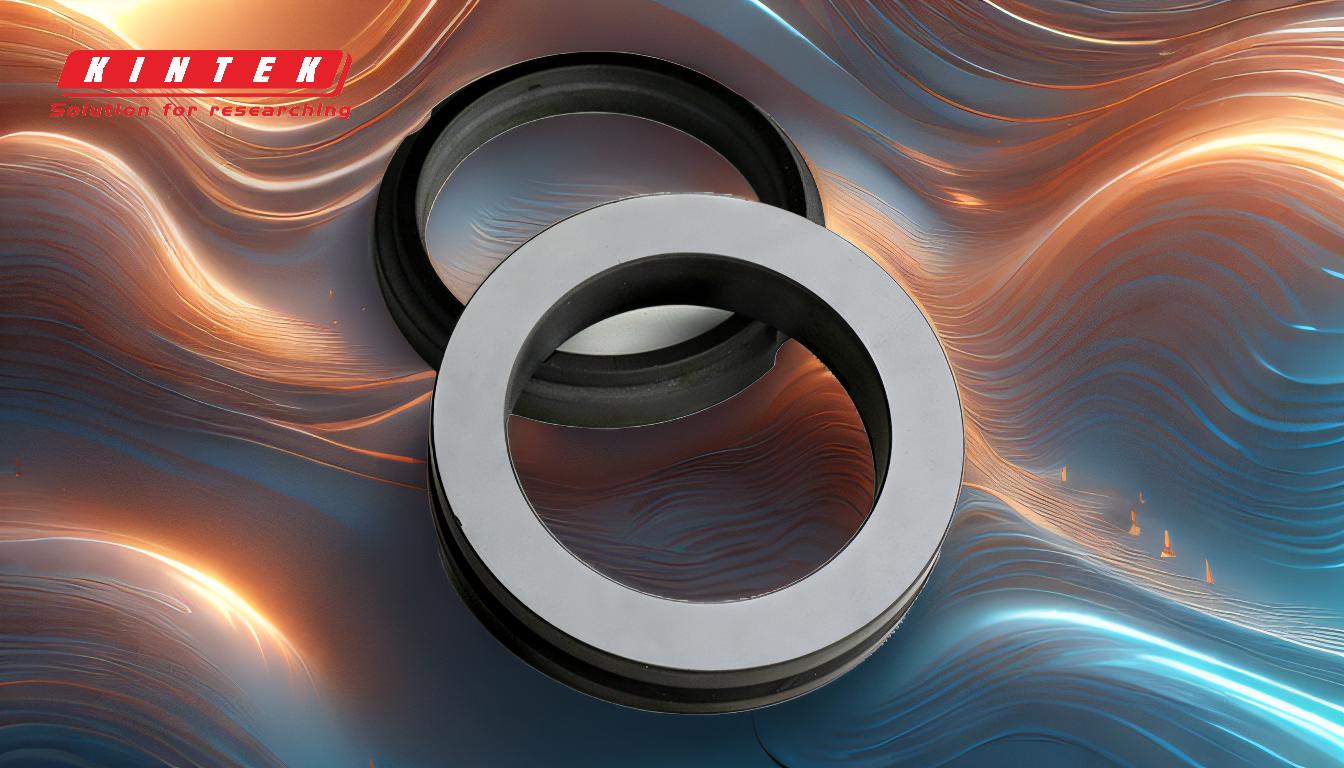
-
定義と基本原則:
- PVD:物理的気相成長法では、物理的手段(加熱、スパッタリングなど)によって固体材料を蒸気に変える。その後、蒸気が基板上に凝縮して薄膜を形成する。
- CVD:化学気相成長法では、ガス状の前駆物質が基板表面で化学的に反応または分解し、固体膜を形成する。このプロセスは、物理的な変換ではなく、化学反応に依存しています。
-
プロセスのメカニズム:
-
PVD:
- 固体材料を融点以上に加熱するか、イオンを衝突させて(スパッタリング)蒸気を発生させる。
- 気化した原子や分子は基板に移動し、薄膜として堆積する。
- 一般的なPVD法には、蒸着、スパッタリング、電子ビーム、ワイヤー爆発などがある。
-
CVD:
- ガス状の前駆体を反応室に導入。
- ガスは加熱された基板表面で化学反応または分解し、固体膜を形成する。
- CVDは、反応効率を向上させるために、熱的に活性化したり、プラズマで強化したりすることができる。
-
PVD:
-
主な違い:
-
材料状態:
- PVDは、物理的に気化する固体材料を使用する。
- CVDは、化学的に固体フィルムに変化する気体前駆体を使用します。
-
視線:
- PVDは、ターゲットとなる材料と基板との間に直接視線を通す必要があるため、複雑な形状を均一にコーティングする能力が制限されます。
- CVDは視線を必要としないため、複雑な形状や複数の部品を同時に均一にコーティングできる。
-
温度と副産物:
- PVDは低温で作動し、腐食性の副生成物を生成しない。
- CVDは高温を必要とすることが多く、腐食性のガス状副生成物や膜中の不純物の可能性がある。
-
材料状態:
-
利点と限界:
-
PVD:
- 利点蒸着温度が低い、腐食性の副生成物がない、材料利用効率が高い(例えば、EBPVDは蒸着速度が速い)。
- 制限事項CVDに比べて蒸着率が低い。
-
CVD:
- 利点複雑な形状の均一コーティング、高い成膜速度、1回の反応で複数の部品をコーティングできる。
- 制限事項高温と腐食性の副産物、フィルム中の不純物の可能性。
-
PVD:
-
用途:
-
PVD:
- 装飾用コーティング、耐摩耗性コーティング、半導体デバイスによく使用される。
- 例えば、切削工具の窒化チタン・コーティングや包装材料のアルミニウム・コーティングなどがある。
-
CVD:
- 半導体製造、光学コーティング、保護コーティングに広く使用されている。
- 例えば、マイクロエレクトロニクスの二酸化ケイ素膜や窒化ケイ素膜、ダイヤモンドライクカーボン膜などがある。
-
PVD:
-
材料の利用と効率:
- PVD:特にEBPVDのような成膜速度が0.1~100μm/分の方法では、高い材料利用効率が得られる。
- CVD:複雑な形状や複数の部品を同時にコーティングするのに有効だが、ガス状の前駆体を使用するため材料費が高くなる可能性がある。
-
環境と安全への配慮:
- PVD:一般に、低温で腐食性の副生成物がないため、より安全で環境に優しい。
- CVD法:反応性ガスの慎重な取り扱いと腐食性副生成物の管理が必要であり、安全面や環境面で問題が生じる可能性がある。
これらの重要なポイントを理解することで、装置や消耗品の購入者は、基板の形状、蒸着速度、温度感受性、環境への影響などの要因を考慮し、特定の用途にPVDとCVDのどちらが適しているかについて、十分な情報を得た上で決定することができる。
要約表
側面 | PVD | CVD |
---|---|---|
材料の状態 | 物理的に気化した固体材料 | ガス状の前駆物質が化学的に固体フィルムに変化 |
視線 | 直接目視する必要があるため、複雑な形状には限界がある。 | 視線が必要ないため、複雑な形状でも均一なコーティングが可能 |
温度 | 低温;腐食性副生成物なし | 高温;腐食性副生成物の可能性あり |
蒸着速度 | CVDに比べて低い | 高い成膜速度 |
用途 | 装飾コーティング、耐摩耗コーティング、半導体 | 半導体、光学コーティング、保護コーティング |
環境への影響 | より安全で環境に優しい | 反応ガスや副生成物の取り扱いに注意が必要 |
PVDとCVDの選択でお困りですか? 当社の専門家に今すぐご連絡ください をご利用ください!